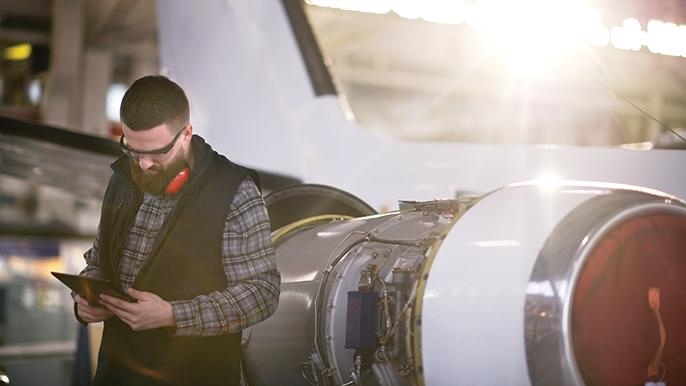
Severe turbulence is an ongoing reality and problem. According to “Turbulence Related Accidents & Incidents” by Donald Eick, senior meteorologist in the NTSB’s Office of Aviation Safety, airline pilots report 5,500 severe or greater turbulence encounters annually — that’s 15 per day — and they are tough on crews, their passengers and the airframe. In addition, flight control system failures, upsets and pilot-induced maneuvers also can produce excessive stress.
These inflight events should be followed by a logbook entry by the captain and a proper inspection by a maintenance technician. Nevertheless, the NTSB has discovered the resulting structural aircraft damage can be substantial and yet evade post-flight visual inspections by pilots and maintenance technicians, thus allowing unairworthy aircraft to fly again.
On Nov. 17, 2002, a Canadair CL-600---2B19 operated by Comair from Atlanta to Washington, encountered severe turbulence during its descent near Rockville, Virginia. About 3 hr. before takeoff, the dispatcher approved the flight release, which contained SIGMET Whiskey 8 for occasional severe turbulence from 14,000 ft. to FL 280. The turbulence box overlaid the departure airport and planned en route climb to altitude; however, the top of descent (TOD) and destination airport were clear of the turbulence.
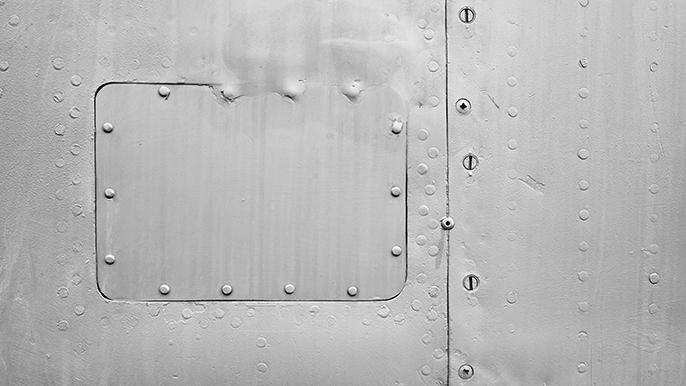
When the pilot later printed the flight release, SIGMET Whiskey 8 had been replaced with SIGMET Whiskey 9. The turbulence box had moved east of the departure airport, and the TOD and destination airport remained clear of the turbulence box. The flight release also contained a single pilot report of severe turbulence from a Boeing 737 at FL 240, within the defined area of turbulence. Prior to departure, but after the flight release was signed by the pilot, the release was updated again, this time with SIGMET Whiskey 10. The turbulence box moved farther east to cover the TOD and destination airport. Nearing his destination, the pilot descended into the turbulence box.
The airplane was not equipped with an aircraft communications addressing and reporting system (ACARS). Rather, weather updates were accomplished by direct radio contact between the dispatcher and pilots, or by the pilots accessing FAA facilities while en route. Although the operator had about 100 flights operating in the turbulence box, none were canceled due to forecast turbulence, or reported to have encountered severe turbulence.
The pilot turned on the seat belt sign, asked the flight attendant to be seated, and made an announcement for the passengers to remain seated as they were within 30 min. of the destination airport. While descending through 17,800 ft., the flight encountered heavy turbulence. Fortunately, there were no injuries to the crew or passengers. Upon landing, the jet was visually inspected for damage in accordance with the Canadair Regional Jet (CRJ) Aircraft Maintenance Manual (AMM) and returned to service.
One of the certification criteria for transport aircraft dealing with structural integrity is 14 CFR 25.301(a), which states, “The structure is required to be designed to sustain the highest loads expected in service [‘limit load’] without detrimental permanent deformation and any deformation may not interfere with safe operation.”
Subsequent evaluation of the flight data recorder by Canadair revealed large vertical accelerations ranging from +4.3 to -1.9 negative during the turbulence encounter. These load factors were outside the certificated design envelopes for the wing, pylon and horizontal stabilizer attachment to the vertical stabilizer. The inspection procedures in the CRJ AMM define a minimum positive G threshold depending on the airplane’s weight (+2.5g in this event), above which a visual inspection for damage is required. No inspection criteria were provided for negative-G or lateral-G excursions. Canadair subsequently performed an engineering assessment and determined inspections in addition to those already specified in the CRJ AMM were required to ensure the airplane’s structural integrity.
On May 12, 1997, an Airbus A300-600 operated by American Airlines as Flight 903 experienced a stall warning system activation followed by extreme bank angles left and right, and a rapid loss of more than 3,000 ft. One passenger sustained serious injuries. Upon landing, the aircraft was inspected visually for damage in accordance with the Airbus A300-600 AMM, which specifies threshold criteria for positive and negative accelerations in the vertical axis, but does not specify lateral-G excursions. Damage to the engine pylons and engines was noted and repaired before the airplane was returned to service.
Subsequent analysis of Flight 903’s FDR revealed lateral accelerations in excess of 0.4g, resulting in internal loads well in excess of the certificated ultimate loads for the vertical stabilizer attachment structure. The stabilizer was removed, and the composite attachment lugs were subjected to ultrasonic nondestructive inspection. The results of the right-hand aft attachment lug inspection indicated a delamination. Delamination of a composite structure can severely compromise its strength. The NTSB wrote that this type of damage can be caused by extreme loading conditions such as those associated with the upset. The vertical stabilizer was removed permanently.
In both of these events, the operators performed the required inspections as specified in the applicable AMM. However, at the time neither the CRJ nor the A300 AMM included inspections for damage caused by high loads due to extreme lateral accelerations, such as those encountered by American Flight 903, and the Canadair AMM did not include inspections for damage caused by extreme negative vertical accelerations, such as those encountered by Comair Flight 5109.
Pilot Control Inputs
Inappropriate control actions by pilots can exacerbate an upset recovery or turbulence encounter, putting additional loads on the aircraft. Remember that flight at high speed and high altitude produces considerable changes on an aircraft’s stability and handling qualities. Since air density decreases at higher altitudes, an aircraft’s aerodynamic damping decreases and it becomes more responsive to control inputs. Flight in the high-speed regime creates high control power, which if used improperly, can over-stress aircraft components.
Over-controlling is a distinct threat at high altitude. For the same control surface movement at constant airspeed, an airplane at 40,000 ft. experiences a higher pitch rate than one at 5,000 ft. because there is less aerodynamic damping. Therefore, the change in angle of attack (AOA) is greater, creating more lift and a higher load factor. It takes less force to generate the same load factor as altitude increases. Erratic and large pitch inputs, possibly from a startle/surprise effect, can quickly bring the aircraft into an upset. It is imperative that pilots refrain from overreacting with large and drastic inputs. Rather, they should smoothly adjust pitch and power to keep the aircraft within the center of its maneuvering envelope.
Aircraft are not built to endure an infinite number of combinations of control inputs. The structural integrity of an aircraft is intended to withstand a pre-defined stress load induced by “normal” control inputs. At speeds higher than maneuver speed (Va), a single large deflection in pitch or roll has the potential to generate structural damage or even failure. At any speed, large aggressive control deflection reversals can exceed structural design limits. Also, certification flight tests involve control input in a single axis and single direction. Control reversals will amplify the loads on the aircraft’s structures.
The Airbus document “Managing Severe Turbulence” provides additional guidance to flight crews of fly-by-wire (FBW) aircraft based upon in-depth analysis of severe turbulence events. Airbus engineers discovered that pilots who followed the prescribed recommendations for FBW aircraft to keep the autopilot and autothrottles engaged were able to minimize the loads on aircraft, as opposed to flight crews who took over manually.
The manufacturer’s Flight Crew Operating Manual recommendations are to follow the target speed (which depends on altitude) when turbulence is encountered and keep autothrottles engaged except if thrust changes become excessive and keep the autopilot on. Detailed studies found the autopilot, when combined with the turbulence-induced motions, limits the aircraft to smaller reactions. In contrast, they also found that pilot pitch-down reaction to an initial updraft will accentuate the pitch-down effect as the aircraft flies into the downdraft section. This increases the negative load factor and increases the risk and number of injuries.
A severe turbulence encounter may lead to excessive high-speed or low-speed excursions. This will induce autopilot disconnections and activation of the appropriate flight control law in an FBW aircraft. In the case of a Vmo/Mmo exceedance, a pitch-up would be commanded to reduce the excursion. If excessive low speed occurs, the alpha protection law would activate and produce a nose-down movement. In order to keep the autopilot engaged as long as possible, flight control software modifications have been developed on FBW aircraft.
Severe turbulence can induce significant altitude excursions because of the turbulence or as a consequence of triggering the Vmo/Mmo protection or the AOA protection. Without the pilot in the loop these protections will place a priority on protecting the target speed rather than maintaining the trajectory. When either protection law is activated, the autopilot is disconnected automatically. The pilot should apply smooth corrections to manage the aircraft trajectory and avoid sudden corrections fighting the turbulence.
According to the industry’s Upset Recovery Manual, if during recovery the application of full lateral control (ailerons and spoilers) is insufficient, it may be necessary to apply rudder in the direction of the desired roll. The manual warns, “only a small amount of rudder input is needed. Too much rudder applied too quickly or held too long may result in loss of lateral and directional control and cause structural damage.” After recovering the aircraft, flight crews must assess any damage that may have occurred.
Severe atmospheric turbulence and inappropriate flight-crew control inputs can induce significant “multi-axial” loads on aircraft structures. A prime example of this occurred when a Boeing 747 nearing Anchorage, Alaska, on March 31, 1993, was in the vicinity of strong mountain wave turbulence. The jumbo experienced a rapid 50-deg. roll to the left followed by a significant yaw. Then came several pitch and roll oscillations. The severe turbulence created dynamic multi-axis loadings that so exceeded the structural capability of the No. 2 engine pylon that it separated from the airplane, taking the engine with it.
What is “multi-axial” loading and why is it important to this discussion? Its impact on an engine pylon illustrates this phenomenon perfectly. Under normal circumstances in flight, the engine is producing a significant amount of forward thrust, thus its pylon endures a direct tensile (pulling) force along its primary axis and is designed accordingly. Now, consider an abrupt rolling input to the aircraft. Suddenly, in addition to the tensile force from the thrust-production, the pylon experiences a sideways shearing force. This places the pylon into a condition of “multi-axial” force . . . tensile stress in one direction and shear stress in another. The combination of stresses acts in a direction that the structural element was not designed to withstand originally, and can lead to failure.
Summary
Due to the risk of reduced structural integrity of an airplane, the NTSB is concerned about deficiencies in inspection procedures. Implicit in the high-load and inspection formulation was the presumption that the specified inspections would be adequate to identify and address damage caused by any such event. Canadair and Airbus determined their published inspection criteria were inadequate to ensure safety after the high-load events encountered by their airplanes, and that additional broader and more-detailed inspections were required to ensure safety.
The NTSB wants to prevent inspected but still unairworthy aircraft from returning to service after events that exceeded the manufacturer’s threshold. Furthermore, the board is troubled that aircraft may be exceeding design and certification standards more frequently than was known or expected, and recommends all such events be tracked and evaluated.
After encountering significant turbulence or any other event that may have exceeded the aircraft’s structural limitations, a captain is responsible for annotating the fact in the aircraft’s logbook after the flight, triggering a mandatory inspection for structural damage. According to Airbus, turbulence can be considered as excessive when passengers and crew are moved violently against their seat belts and objects move around the aircraft. Inspections that are mandated after flight in excessive turbulence are described in the AMM. In case of severe turbulence, it is recommended the manufacturer be informed as well. Note that in some cases the manufacturers have determined that limit loads have been exceeded in portions of the aircraft, thus requiring additional inspections.