随着武器测试的临近,研究人员面临更严峻的高超声速屏障 | Researchers Face Tougher Hypersonic Barriers As Weapon Tests Loom

经过几十年的发展,高超声速飞行器的时代即将来临,曾经被认为是科幻小说或异想天开的军事计划的概念即将成为现实。
After decades of promise the age of operational hypersonic vehicles is dawning, and concepts once considered the stuff of science fiction or the fanciful prediction of military planners are about to become reality.
美国第一代火箭助推滑翔和吸气式战术打击武器正在研制中,将在几年内投入使用。然而支持者表示还有更多的工作要做。下一代更大的设计能够利用5马赫以上的飞行速度优势来发挥更广泛的作用,包括打击和侦察、高速民用和军用运输,甚至多级入轨。
The first generation of U.S. tactical boost-glide and air-breathing strike weapons are in development and will be fielded within a few years. But proponents say much more work still needs to be done before larger, next-generation designs can harness the advantages of flight speeds of Mach 5-plus for broader roles including strike and reconnaissance, high-speed civil and military transport and even multistage access to space.
除了诸如推进器类型选择以及推进器和机身的复杂耦合优化等最优先问题之外,设计人员还必须应对随马赫数变化而引起的流体力学方面的挑战性变化。再加上人们对满足如此高要求的耐高温特种材料的不断探索尚未取得成功。这一系列问题仍然和以往一样令人生畏。
Ranging from first order issues such as propulsion type selection and the complex coupled optimization of propulsion and airframes, designers must also contend with challenging changes in flow physics with varying Mach numbers. Added to the continuing quest for exotic materials with such high-temperature resistance that they have yet to be invented, the list of hurdles remains as daunting as ever.
不过,早期高超声速火箭助推滑翔飞行器和吸气式超燃冲压发动机的演示验证为今天的开发人员在高速空气动力学和推进技术方面奠定了坚实的基础。美国国防部国防研究与工程现代化局局长马克·刘易斯(Mark Lewis)说:“好消息是,现在毫无疑问,超燃冲压发动机可以制造并且能够产生正推力,这很了不起。我们非常了解燃料特性以及如何有效地喷注燃料。”
Tests of rocket-boosted hypersonic glide vehicles and early air-breathing scramjet-powered demonstrators have, however, given today’s developers a solid foundation of the basic high-speed aerodynamics and propulsion requirements. “The good news is there is now zero doubt that a scramjet can be built and can produce net positive thrust,” says Mark Lewis, director of defense research and engineering for modernization at the U.S. Defense Department. “That’s all pretty remarkable. We have a keen understanding what the properties of the fuel should be and how to inject it effectively.”
但是,刘易斯也提到,要超越一次性使用的火箭助推滑翔飞行器和导弹,实现开发可重复使用的高超声速飞行器的最终愿景,需要付出巨大的努力。他说:“在机体与发动机一体化方面,特别是推进模态转换方面,还有很多工作要做。我们需要一种推进系统,能够从0马赫一直加速到5或6马赫,然后再减速到0马赫。这是我们现在正开展的研究。最大的问题是,它应该是一台联合循环发动机还是多台发动机的组合?我可以直接从涡轮发动机转到亚燃/超燃冲压发动机,还是需要一些中间过渡措施?”
But to go beyond rocket-boosted single-use gliders and missiles to fulfill the ultimate vision of developing reusable hypersonic aircraft will require a huge effort, says Lewis. “There’s a lot to do there in terms of the engine-airframe integration, particularly the propulsion transition,” he says. “We need a propulsion system that gets us all the way from Mach 0 all the way up to Mach 5 or 6 and then back down to Mach 0. That’s one we’re still working on. The big question is, should it be a combined cycle engine or multiple engines? Can I go direct from a turbine to a ramjet/scramjet, or do I need something intermediate?”
由于涡轮发动机的工作上限约为3马赫或4马赫,吸气式系统开发人员的重点一直放在高速涡轮喷气发动机、亚燃和超燃冲压发动机的组合上,统称为涡轮基联合循环(TBCC),以加速至马赫数5及以上。然而,尽管以超燃冲压发动机为动力的美国航天局X-43A和美国空军主导的X-51A飞行器取得了开创性的成功,并于2019年对美国空军委托诺斯罗普·格鲁门公司制造的5900kg推力超燃冲压发动机进行了试验,但是对于组合式高速动力的最佳技术路径还没有达成明确的共识。
As the upper operating limit for turbine engines is around Mach 3 or 4, the focus for developers of air-breathing systems has been on a combination of high-speed turbojets, ramjets and scramjets—collectively dubbed the turbine-based combined cycle (TBCC)—to accelerate to Mach 5 and beyond. However, despite the pioneering success of the scramjet-powered NASA X-43A and U.S. Air Force-led X-51A vehicles, and tests in 2019 of a 13,000 lb.-thrust Northrop Grumman-built scramjet by the Air Force, there is no definitive consensus on the best path forward for integrated high-speed propulsion.
部分原因是超燃冲压发动机虽然概念简单,没有运动部件,但在工作的物理环境方面却很复杂。喷气发动机的机械压缩被冲击压缩取代,冲击压缩以冲击波的形式进入发动机,必须有效地压缩进气道和隔离段内的空气,然后形成湍流和化学混合,并在1毫秒内使燃料和空气产生反应。
Part of the reason is that scramjets, while conceptually simple with no moving parts, are complex in terms of operational physics. The mechanical compression of jet engines is replaced by shock compression which, in the form of shockwaves entering the engine, must efficiently compress air within the inlet and isolator before turbulence and chemistry mix and react fuel and air in under 1 millisec.
即使以20世纪60年代普惠公司J58涡喷发动机上1.3m长度燃烧室的性能为标准,超燃冲压发动机的任务也要困难几个数量级。J58在洛克希德SR-71上以980m/s(3.3马赫)的速度在8万英尺(24km)的高度上飞行,而X-43A上的 0.8m长度燃烧室要以2900m/s(9.7马赫)的速度在33km的高度上飞行。
Even by the performance standards achieved by the 50-in.-long combustor in Pratt & Whitney’s J58 turbojet of the 1960s, the fastest air breathing engine ever to seeoperational use, the task of the scramjet is orders of magnitude more difficult. The J58 traveled at 3,200 ft/sec at Mach 3.3 and 80,000 ft. in the Lockheed SR-71, while the X-43A’s 30-in.-long combustor traveled at around 9,600 ft./sec. as it flew at Mach 9.7 and 110,000 ft.
波音公司主持X-51A概念设计的首席高超声速科学家凯文·鲍库特(Kevin Bowcutt)说:“挑战在于设计具有最佳气动外形(面积分布和形状)、喷注器和火焰稳定器外形、喷注器空间布置以及其他燃油喷注参数的燃烧室。”。他认为这些问题虽然重要,但可以通过多学科设计优化(MDO)方法解决,该方法同时结合了空气动力学、控制、推进和结构方面的考虑,以获得高度集成的解决方案。
“The challenge is designing combustors with optimal overall geometries (area distribution and shape), injector and flameholder geometries, and the spatial distribution of fuel injectors, plus values of other fuel injection parameters,” says Kevin Bowcutt, the chief hypersonics scientist at Boeing who led the X-51A conceptual design. He thinks the hurdles, while significant, can be tackled using a multidisciplinary design optimization (MDO) approach that simultaneously combines aerodynamics, control, propulsion and structural considerations to produce a highly integrated solution.
鲍库特补充说:“快速、高精度流体仿真分析(CFD)软件、专门用于高超声速发动机试验的良好地面试验设施,以及用于试验测量的精密流量检测仪器将有助于这个设计优化过程。”X-51A是第一款使用MDO(多学科优化方法)进行改进的高超声速飞行器。
“This design optimization process will be aided by fast, high-fidelity flow simulation [computational fluid dynamics] tools, good ground test facilities specializing in hypersonic engine testing, and sophisticated flow diagnostic instrumentation for test measurements,” adds Bowcutt, who has previously noted the X-51A was the first hypersonic vehicle to be refined using MDO.
尽管超燃冲压发动机的开发已进行了数十年,但具有竞争力的推进方案仍在不断涌现。那么,超燃冲压发动机是否仍然是正确的答案呢?刘易斯说:“我认为盖棺定论还为时过早。我们面对的一个挑战就是要开放思想,我们要充分考虑在高速推进上是否还有其他技术路线可以推动我们进步。我不想限制我们的技术选择范围。”
However, despite decades of scramjet development work, competing propulsion concepts continue to emerge. So, are scramjets necessarily still the right answer? “I would say the jury’s still out,” says Lewis. “One of our challenges is to be open-minded enough to think maybe there are other ways to propel ourselves at high speed. I wouldn’t want to narrow down our technology options.”
推进方案
Propulsion Options
同时还在研究TBCC以外的各种可能的替代动力循环。这些推进方案可以使飞行器从静止加速到6马赫以上,其中大多数利用液氢的热力学特性作为冷却剂和燃料。例如,日本宇宙航空研究开发机构(JAXA)研究的ATREX吸气式涡轮冲压膨胀循环发动机;俄罗斯开发的ATRDC深度预冷空气涡轮火箭发动机;美国MSE公司的集成了深度预冷涡轮与液体火箭的KLIN发动机;以及吸气式火箭发动机。
A potential wide variety of alternative power cycles beyond the TBCC have also been studied that could speed a vehicle from a standing start to Mach 6-plus, most of which take advantage of the thermodynamic properties of liquid hydrogen as a working fluid for cooling and power. Examples include the ATREX expander air turbo-ramjet studied by JAXA, the Japan Aerospace Research Agency; the Russian-developed ATRDC deeply-cooled, air turbo rocket; the KLIN cycle thermally integrated deeply-cooled turbojet and liquid rocket engine; and the aspirating rocket engine.
其他有希望的吸气式方案包括压力增益循环,例如旋转和脉冲爆震发动机,以及更奇特的磁流体/磁-等离子体发动机。这两种循环都在做高超声速应用研究,前者作为脉冲爆震火箭联合循环的一部分,与引射冲压发动机、亚燃冲压发动机、超燃冲压发动机和火箭模式组合,可实现太空入轨。
Other air-breathing concepts showing promise include pressure-gain cycles such as rotating and pulse detonation engines and, potentially, even more exotic magnetohydrodynamic/magneto-plasmadynamic engines. Both cycles are being investigated for hypersonic application, the former for potential access to space as part of a pulse detonation rocket-based combined cycle with ejector ramjet, ramjet, scramjet and rocket modes.
另一个替代方案是反作用发动机公司的“佩刀”(SABRE,协同吸气式火箭发动机),研发团队在英国和美国,设计目标是在吸气模式下为高达5.4马赫的飞行器提供动力,并在火箭模式下一直达到入轨速度。这台发动机的预冷器在2019年10月通过了一个关键的里程碑测试,在相当于5马赫的进气温度下成功运行。
Another alternative is the Reaction Engines SABRE (synergetic air-breathing rocket engine), which is in development at sites in the UK and U.S. Designed to power vehicles up to Mach 5.4 in air-breathing mode and all the way to orbital velocity in rocket mode, the engine’s precooler passed a critical milestone test in October when it operated successfully at temperature inlet conditions equivalent to Mach 5.
刘易斯说:“液体空气循环发动机和深度预冷循环发动机的整个构想都极有发展前景。我不知道最终是否会成功,但是对于某些类型的飞行器来说,它们似乎具有明显的优势。我认为有必要保持足够多样化的研究组合和开发组合,以便有足够的空间来容纳各种聪明的想法。”
“The whole idea of a liquid air cycle engine and the deeply-cooled cycle is extremely promising,” says Lewis. “I don’t know if at the end, they’ll pan out, but they seem to have some significant advantages for certain classes of vehicles. I do worry that we [must] maintain a sufficiently diverse research portfolio and development portfolio that there is room for a full range of clever ideas.”
机体-推进一体化
Airframe-Propulsion Integration
随着速度和高度的增加,吸气式飞行器必须在相对狭窄的飞行包线中航行。碳氢燃料超燃冲压发动机在大约3马赫速度开始启动,燃料热值的极限约为7.5马赫,而氢动力飞行器的性能极限约为14马赫。在高度方面,大多数双模态超燃冲压发动机的理论飞行包线上边界是24kPa的动压。这意味着工作范围限定在从30km高度的5马赫到45km高度的15马赫。
Air-breathers must navigate a relatively tight flight trajectory propulsion corridor as speed and altitude increase. Commencing with a takeover speed of around Mach 3, hydrocarbon-powered scramjets hit a fuel thermal limit around Mach 7.5, while hydrogen-powered vehicles reach a performance limit around Mach 14. In terms of altitude, most dual-mode scramjets are theoretically bounded by upper operability limits at a dynamic pressure of 500 psf—a level that runs from Mach 5 at 100,000-ft. to Mach 15 at 150,000 ft.
在较低的高度,稠密的大气层构成了另一个界线。飞行器设计者通常以平流层中的高超声速飞行为目标,将动压限制在96kPa以下。受结构强度设计限制,飞行包线从大约12km高度的2.5马赫到大约33km高度的14马赫。
At lower altitudes, the denser atmosphere presents another barrier. Vehicle designers usually target hypersonic flight in the stratosphere to limit the dynamic pressure to below 2,000 psf. The line representing the resulting structural design limit extends from around 40,000 ft. at Mach 2.5 to around 110,000-ft. at Mach 14.
除了这些挑战之外,不同马赫数带来的气动特性变化也使设计考虑因素变得复杂。寻找适合不同飞行模态的最佳机翼尺寸;高载油系数飞行器的总体布局;并定义合适的进气道和尾喷管尺寸,这两个部件的尺寸要随马赫数而改变。
To add to these challenges, design considerations are also complicated by changing aerodynamic behavior with Mach number; finding the optimum wing size to suit varying flight modes; configuring the vehicle for a high propellant fraction; and defining the correct inlet and nozzle size, both of which vary extensively with Mach.
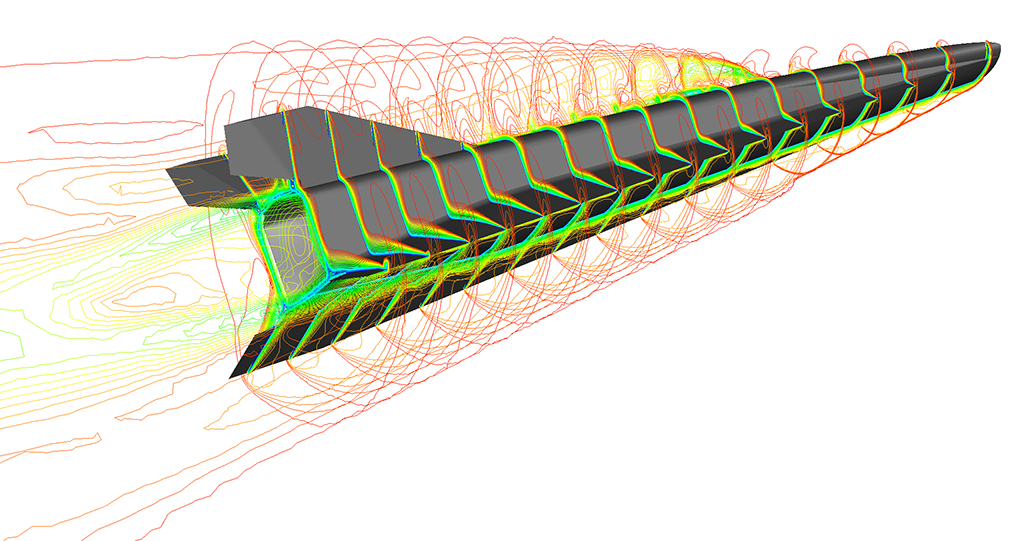
刘易斯说:“我们知道如何制造好的进气道,但是一直有个问题:什么是最好的进气道设计?有句话叫“尽善尽美是足够好的敌人”,我们制造的进气道能够正常工作。然而,显然还有一些领域需要继续发展、研究和提高。”
“We also know how to build good inlets,” says Lewis. “But there is still an ongoing question: What is the best inlet design? Under the general heading of ‘perfection is the enemy of good enough,’ we know how to build inlets that work. However, there are clearly areas for continued development, research and advancement.”
由于高推阻比对于快速加速到5马赫以上至关重要,因而推进一体化必不可少,并且推动了在不同马赫数下的进气量需求。设计人员发现,总的进气量和发动机推力系数必须足够高,以保证在所有速度下推阻比都能大于2。另一方面,尽管进气道尺寸和进气量必须足够大才能实现高超声速性能,但是当飞行器通过马赫数1左右的跨音速区域时,必须减小进气道和尾喷管的尺寸以降低跨音速阻力。
As achieving a high thrust-to-drag ratio is critical for efficient acceleration to Mach 5-plus, propulsion integration is vital and drives the need for increasing air capture with Mach number. Designers have discovered that overall air capture and engine thrust coefficient must be sufficiently high enough to give a thrust/drag ratio of greater than 2 at all speeds. But, at the same time, although inlet size and air capture must be relatively large for hypersonic performance, drag from inlets and nozzles must be reduced as the vehicle passes through the transonic region around Mach 1.
鲍库特表示:“设计进气道要兼容非常大速度范围的空气流量捕获要求(通常以捕获面积计算)和收缩比要求,实现高压缩比和流动稳定性,还要确保大范围内的低进气畸变和低附加阻力(包括溢流阻力)。在大跨度的马赫数、高度和攻角范围内,这非常具有挑战性。”
“It is very challenging to design inlets that accommodate a very large range of air mass capture (measured as capture area) and contraction ratio with high compression efficiency and flow stability, and low flow distortion and additive (including spillage) drag, across a large range of Mach number, altitude, and angle of attack” says Bowcutt.
刘易斯回忆说:“多年来,我一直在研究许多高超声速飞行器的概念设计,其最终形状不是取决于高超声速性能要求,而是由跨音速性能决定的。你可以设计出高超声速的外形,你知道它们在马赫数5、6、7、8时表现出色,但它们没有希望突破马赫数1,在这里有点跟不上。对于武器应用,我们可以轻松搞定,例如我们通常会用火箭帮助突破马赫数1。但是如今,(对于水平起降的高超声速飞行器)低马赫数下的性能变得至关重要。”
“Over the years I’ve been involved in looking at conceptual design for a number of hypersonic vehicles where the final shape was dictated not by its hypersonic performance, but by the transonic performance,” Lewis recalls. “You can design hypersonic shapes that you know do great at Mach 5, 6, 7, 8, but they have no hope of punching through Mach 1. There’s a slight disconnect there. With the weapons applications we have an easier task because we are usually punching through Mach 1 with a rocket, for example. But this shows that low Mach number performance becomes critical.”
机体和推进系统紧密耦合给设计带来极端挑战,而将飞行器内部子系统的重量、功率和尺寸降到最低,进一步加剧了挑战的难度。刘易斯认为,通过类似MDO(多学科优化)的方法实现高度一体化的飞行器架构“绝对是一个关键技术领域”。他说:“35年前我们就知道,高超声速飞行器必须是一个高度一体化的系统,而今天我们所学到的一切都强调了这一点。”
The extreme challenges of bringing together a closely coupled airframe and propulsion system are further magnified by the need to then minimize the weight, power and size requirements of the subsystems inside the vehicle. The need for a highly integrated flight architecture, made possible through MDO-type approaches, is “absolutely a key area,” says Lewis. “We knew 35 years ago that a hypersonic vehicle would have to be a fully integrated system, and today everything that we’ve learned has reinforced that,” he says.
尺度与流体物理学
Scaling and Flow Physics
不同的尺度带来不同的挑战。马里兰州约翰霍普金斯大学应用物理实验室的防空和导弹防御部门负责人大卫•范•维(David Van Wie)说:“对于大型飞行器,有另一个非常重要的耦合,因为其结构可以弯曲和扭转。你不能把它设计成刚性体。飞行载荷会深入影响到发动机和推进系统中。随着尺寸加大,这种耦合影响会变得更具挑战性。”
Challenges also differ, depending on size. “Going to the bigger vehicles there’s another coupling that’s really important, in that structures can bend and flex,” says David Van Wie, head of the Air and Missile Defense Sector at Johns Hopkins Applied Physics Laboratory, Maryland. “You just can’t make it rigid enough,” he says. “Flight loads can couple back into the engine and the propulsion systems, and the degree of coupling gets more challenging as you go to larger scales.”
小型飞行器虽然结构刚性较好,但仍面临容量和热管理方面的挑战。范•维说:“NASA很久以前的研究表明,细长飞行器的高超声速升阻比要比短粗的飞行器高得多。但当你尝试缩小尺寸时,它不可能又长又细,那样就没有内部空间了。最终要从理想升阻比的气动设计妥协为一个可以实现的目标。”
Smaller scale vehicles, though structurally stiffer, face challenges related to packaging and thermal management. “NASA studies long ago said long slender vehicles had much higher hypersonic lift-to-drag ratios than shorter, stubbier vehicles,” says Van Wie. “And when you go try to make something small, it can’t be long and slender, there’s just no internal volume. It ends up setting what is achievable from an aerodynamic efficiency from a lift-to-drag ratio.”
刘易斯补充道:“在内部进行所有气动和推进的集成是一个挑战。你必须确保内部有足够的空间放置所需的所有部件,如用于引导、导航和控制的传感器和系统。”
“There is a challenge there doing all the aerodynamics and propulsion integration with the internal packaging, Lewis adds. “You must make sure you have room for all the parts inside that you need such as sensors and systems for guidance, navigation and control.”
另一个尺度问题,也是高超声速飞行器设计的核心问题,涉及边界层的特性。边界层是靠近机身表面的薄薄一层空气,设计者努力将层流状态维持尽可能长的时间,以尽量减少发热量,从而降低热防护要求。在高超声速下,边界层趋于变厚,通常对激波扰动的抵抗力更强。但当它转变为湍流时,它会影响加热、阻力和稳定性。激波上的压力升高也会与边界层产生相互作用。
Another scaling issue, and one that goes to the heart of hypersonic vehicle design, concerns the behavior of the boundary layer, a thin layer near the surface that designers strive to keep laminar for as long as possible to minimize heating and thus reduce thermal protection requirements. At hypersonic speeds, the boundary layer tends to thicken and, in general, become more resistant to disturbances. But when it transitions to turbulent flow it can affect heating, drag and stability. Pressure rises across shockwaves can also interact with the boundary layer.
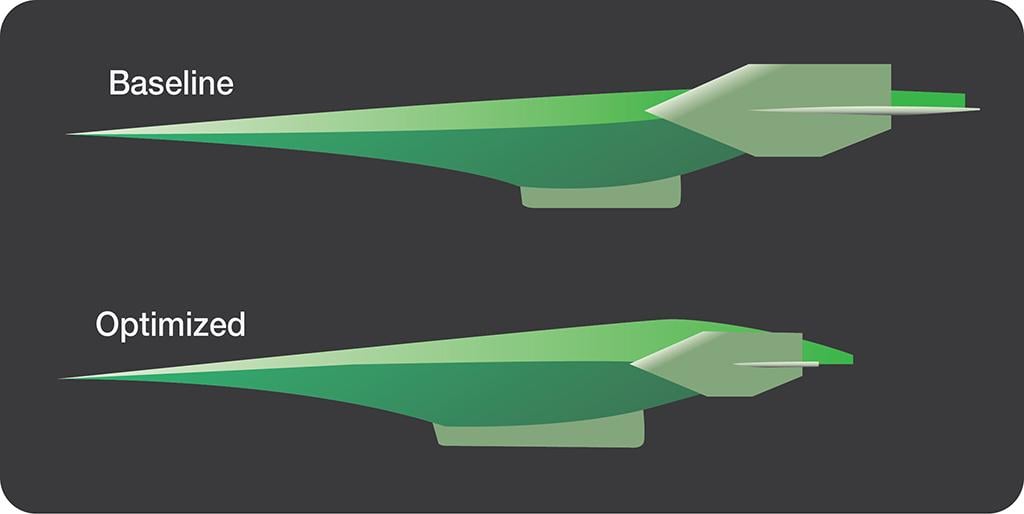
刘易斯认为,虽然最近计算软件的进步使流体物理学的预测更加准确,但缩小边界层过渡区范围的进一步改进将有助于增强高超声速飞行器设计的稳健性。他说:“我们已经学会了围绕我们不知道的东西进行设计。我们意识到,我们永远无法确切知道边界层何时从层流过渡到湍流,所以我们必须围绕它进行设计。”
Although advances in computational codes have recently enabled more accurate predictions of flow physics, further improvements in narrowing down boundary layer transition zones will help build robustness into hypersonic vehicle design, says Lewis. “We’ve learned to design around what we know we don’t know,” he says. “We realized we’re never going to know exactly when the boundary layer transitions from laminar to turbulent, so we have to design around that.”
相反,超燃冲压发动机的开发人员面临这样一个挑战,即在进气道中引入湍流而非层流边界层条件,以获得更好的可操作性。鲍库特说:“在激波与边界层相互作用的情况下,湍流不太容易受到边界层分离的影响。”
Conversely, scramjet engine developers face the challenge of encouraging turbulent, rather than laminar, boundary layer conditions in inlets for better operability. “A turbulent flow is less susceptible to boundary layer separation where shocks interact with the boundary layer,” says Bowcutt.
刘易斯回忆起上世纪80年代在美国国家空天飞机项目(NASP)上学习到的经验教训,他说,一位非常资深的讲师警告说,如果飞行器的边界层是湍流而不是层流,那么它将永远飞不起来。他说:“我学到的就是,如果我们的飞行器设计如此敏感,那么它肯定飞不起来,我们需要设计足够稳健的气动布局。这是最困难的部分。”
Recalling lessons learned from working as a student on the National AeroSpace Plane (NASP) program of the 1980s, Lewis says a very senior lecturer warned that if the vehicle’s boundary layer was turbulent instead of laminar, then it would never fly. “Among the things I’ve learned is, if our vehicle designs are that sensitive, then they’re not going to fly and we need to be designing robust configurations,” he says. “That’s the hard part.”
范•维同意这个观点,高超声速飞行器还远未成熟到实际可用阶段。他说:“我认为,提高我们对如何实际制造飞行器并使其在飞行环境中稳健运行的知识,是目前更大的挑战领域之一。你肯定不希望这个飞行器只能按照特定剖面飞行。我想它应该像其他飞行器一样自由飞行。”
Maturing hypersonic vehicles into operational systems remains a major hurdle, agrees Van Wie. “Improving our knowledge on how to actually build vehicles and get them to operate robustly in the environment is, I think, one of the bigger challenge areas right now,” he says. “You want to be able to fly it in a way where you don’t have to thread the needle and follow, for example, a given experimental flight profile. I want to fly it like any other aerospace vehicle.”
飞行器前缘周围的激波与边界层的耦合作用是另一个挑战,尤其是对于高空中细长的助推滑翔飞行器和尖头的再入体而言。雷诺数(Re)是流体惯性力与黏性力比值的无量纲度量标准,它体现了流体相互作用或前缘粘性影响的程度。在雷诺数较低的高层大气中,边界层厚度增加,并与邻近气流相互作用。即使在高超声速飞行器的非常锋利的前缘,在非常低的雷诺数下,边界层的增长也会有效地改变前缘的形状,使其面对边界层外的迎面气流时显得钝化。
Interaction of the shockwave around the leading edges of the vehicle with the boundary layer is another challenge, particularly for slender-shaped boost-glide vehicles at higher altitudes and sharp-nosed reentry bodies. The degree to which flow interaction effects, or leading-edge viscous interaction, can occur is influenced by the Reynolds (Re) number, a nondimensional scaling metric that is the ratio of inertial forces to viscous forces. In the upper atmosphere with lower Re, the thickness of the boundary layer increases and interacts with the adjacent flow. At even the very sharp leading edges of a hypersonic vehicle, in very low Re, the growth of the boundary layer effectively changes the shape of the leading edge, making it seem blunter to the oncoming flow outside of the boundary layer.
这种效应改变了前缘的气流分布,进而影响了边界层的特性,并产生粘性相互作用,对升阻比有潜在的破坏性影响。其他的激波-边界层耦合会引起类似的麻烦,例如进气道和进气道上的斜坡。刘易斯指出:“这是影响前缘特性的一个重要因素,但它引入了一个尺度。因此,如果我采用给定的形状,可以高超声速飞行并具有一定的性能,然后我等比缩小它。我会突然发现截然不同的物理特性,就来自于尺度变化的影响。”
The effect changes the air distribution at the leading edge, which in turn affects the behavior of the boundary layer and creates viscous interactions with potentially damaging impacts on lift/drag. Similar effects can cause trouble in other shock/boundary layer interactions such as inlets and on inlet ramps. “That’s a significant factor in the behavior of leading edges, but it introduces a scale,” says Lewis. “So, if I take a given shape that flies hypersonically with a certain performance, and I photographically reduce it. I could suddenly pick up entirely different physical behavior because of the way these interactions scale.”
高温材料
Higher-Temperature Materials
另一个重大挑战是在材料方面。尽管经过70年的研究,航天器、弹道武器和超声速飞机的热防护系统(TPS)和其他防热技术都得到了发展,但这些材料体系都不能完全解决在大气层内高超声速飞行面临的独特加热问题。
Another significant challenge is in materials. Despite the seven decades of research that led to the development of thermal protection systems (TPS) and other heat-resistant treatments for spacecraft, ballistic weapons and supersonic aircraft, none of these material systems specifically meet the unique heating challenge of extended hypersonic flight through the atmosphere.
在6马赫或更高的持续速度下,高超声速飞行器前缘的温度可达到1600~2200℃,温度上限比钛的熔点高300℃,比钢的熔点高600℃。极高的热量像喷灯一样,被聚集覆盖到一个很小的区域,导致非常大的热冲击和极端温度梯度。在飞行中,材料性能在如此高温下会发生变化,同时还可能产生氧化和催化反应。
At sustained speeds of Mach 6 and above, the temperatures at the leading edges of hypersonic vehicles can run from 1,600-2,200C (2,900-4,000F), the upper range of which is more than 300C higher than the melting point of titanium and 600C hotter than the melting point of steel. The highest heat flux is focused, blowtorch-like, over a relatively small area, leading to high thermal shock and extreme temperature gradients. At such high temperatures, material properties can change during the flight, while oxidation and catalysis effects are also possible.
范•维说:“在这个领域内有很多发明机会。随着前缘越来越尖锐,它们会变得更热,这是当前一个主要的材料问题。你需要前缘多尖锐?这个问题实质上可以转换成材料的最高工作温度。答案取决于它是可重复使用飞行器还是一次性武器系统。这是一个活跃的研究领域。”
“It is an area where there’s a lot of opportunity for invention,” says Van Wie. “As the leading edges become sharper, they want to get hotter. That’s one of the main materials issues out there: How sharp do you want to go, and that fundamentally translates into the highest temperatures they can be operated at. The answers are influenced by whether it’s a reusable vehicle or a one-use weapon system. But this is an active area of research.”
范•维说:“(更高的耐温材料)将允许您设计具有更锐利前缘的飞行器,从而获得更高的升阻比,更好的性能。或者,它可以让飞机以更高的速度和高度飞行,从而获得更多的利润。这是一个有很大提升空间的挑战领域。”
“[Higher-temperature-resistant materials] would allow you to design vehicles with sharper leading edges, which would give you a higher lift-to-drag ratio for better performance. Or it would give more margin by allowing flight at higher speeds and altitudes,” says Van Wie. “It is a one of the challenge areas where there’s a lot of room for improvement.”
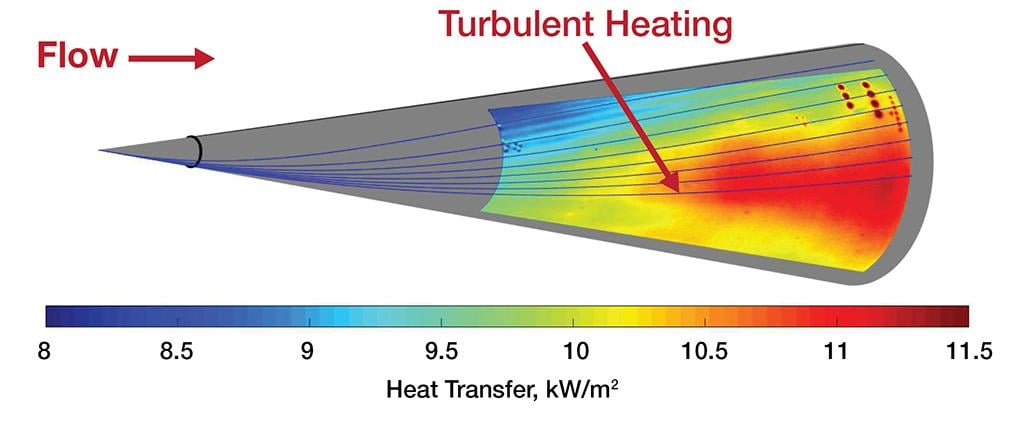
另一个重要的相关问题是,随着飞行器尺寸变化而不断变化的热环境。刘易斯说:“人们仍然不了解材料问题如何随尺寸而变化。这是另一条需要持续投资和发展的技术路径。例如,我将特定的高超声速飞行器外形等比例缩小,那么我会得到更锐利的前缘。然后它会变得更热。因此,我经过权衡采用更钝的前缘,它会造成更大的阻力,空气动力学性能会降低。”
Another significant, related, hurdle is the changing thermal environment with varying vehicle size. “People still don’t understand how the material challenges scale with size,” says Lewis. “It’s another avenue that requires continued investment and development. For example, if I take to make a given hypersonic configuration smaller by just photographically reducing it, then I wind up with much sharper leading edges. And then those get much hotter. So, I end up with this trade-off going on for blunt leading edges that create more drag and have less aerodynamic performance.
“所以这是一个非常活跃的领域,尤其是在我们讨论高超声速飞行器的尺度时。”他补充说:“经过大量类似工作之后,我们意识到,我们必须非常谨慎地对待尺度问题。如果一个特定尺寸的飞行器能正常运行,并不意味着我们可以把相同的设计直接缩放,应用到我们正在开发的系统中。”
“So that’s a pretty active area, especially as we’re talking about delivering hypersonics at scale. And for doing it in large numbers, we realized we had to be very careful extrapolating that if something works on a certain scale, it doesn’t mean that we can take that same configuration and apply it across the range of systems that we’re looking to develop,” he adds.
当飞行器以5马赫以上的速度通过大气层时,空气本身会发生变化。刘易斯说:“你的温度变得如此之高,以至于飞行器周围气流的化学成分开始发生变化。你开始分解氧气。在更高的温度下,最终你可以开始分解氮气。这种化学离解会影响飞行器上的流场特性。”双原子氧在1700℃左右分解成氧自由基,而氮的分解在3700℃左右发生。
As a vehicle passes through the atmosphere at Mach 5-plus, the air itself can change. “Your temperatures become such that the chemical composition of the air flowing around the vehicle begins to change,” says Lewis. “You start to disassociate oxygen. Then at even higher temperatures eventually you can start disassociating nitrogen. This chemical dissociation affects the behavior of the flow over the vehicle.” The dissociation of diatomic oxygen into oxygen radicals takes place at temperatures around 1,700C, while that of nitrogen is at around 3,700C.
离解、更高马赫数下的等离子体形成和气动加热效应还会对高超声速飞行器的通信、制导导航与控制(GNC)提出了重大挑战。“这增加了高超声速计算的难度。你把你的传感器放在哪里,你如何放进某个孔或者窗口里,并与飞行器上其他部分融合为一体?”刘易斯问。
Disassociation, plasma formation at higher Mach numbers and aeroheating effects pose a major challenge for communicating with hypersonic vehicles, as well as for guidance, navigation and control (GNC). “It makes the hypersonic calculation somewhat challenging. Where do you put your sensor, and how do you put in an aperture or window of some sort that you can blend with the rest of the vehicle?” asks Lewis.
针对GNC问题的研发工作在所有高超声速企业都很活跃,目前的研究工作从导弹和跨大气层飞行器的新型传感器和航电设备到半自主/自主导弹制导系统的先进设计,以及为高超声速飞行器轨迹优化开发新的制导律。其他研究领域包括将数据融合应用于目标识别和跟踪算法,以及开发新的自适应控制算法和新型驱动系统等。
Research and development into tackling the GNC hurdles is active across the hypersonic enterprise, with current study work ranging from new sensors and avionics for missiles and transatmospheric vehicles to advanced designs for semiautonomous/autonomous missile guidance systems and development of new guidance laws for high-speed vehicle trajectory optimization. Other areas of study include the application of data fusion for target discrimination and tracking algorithms, as well as development of new adaptive control algorithms and novel actuation systems.
洛克希德·马丁公司的技术总监大卫·汉恩(David Hunn)表示,材料是成功研制高超声速飞行器的“首要”问题。“我不得不根据现有材料体系的局限性来调整我的飞行轨迹和性能。”汉恩在2019年11月伦敦举行的皇家航空学会高超声速会议上这样说。
Materials represents the “first and foremost” challenge to successful hypersonic vehicle development said David Hunn, director of technology at Lockheed Martin Missiles and Fire Control. “I’m having to adjust my trajectory and performance based on the limitations of materials systems that are available now.” Hunn was speaking at a Royal Aeronautical Society hypersonics conference in London in November.
“我们过去在这个领域的探索很少。那么我们该如何解决呢?”他问道。选择范围从带有循环冷却剂的内部冷却结构到各种被动、烧蚀或半主动TPS的隔热结构。但是总的来说,辐射冷却/热结构方法是首选。他说:“(它)简单,没有诸如泵类的活动部件,而且是可预测的和稳定的。可以说,它有最小的空间、重量和功率要求。”
“We are in regimes that have rarely been explored in the past. So how do we handle that?” he asked. The options range from internally cooled structures with circulating coolant to insulated structures with passive, ablative or semiactive TPS. But overall, the radiation cooled/hot structure approach is preferred. “[It] is simple, there are no moving parts such as pumps, and it is predictable and stable,” he said. “Arguably it also offers the minimum space, weight and power.”
涂层挑战
Coating Challenges
由于金属无法承受所需的热流密度,因此目前的材料选择主要集中在碳纤维和碳基复合材料以及陶瓷基复合材料上。
With metals incapable of withstanding the required heat flux, material choices are currently focused mainly on carbon-fiber and carbon-matrix composites as well as ceramic composites.
汉恩说:“我们希望能够有材料解决方案,但还是有一个问题。我们必须明白,这些碳基材料会氧化。所以在空气中,我不得不担心化学催化反应会把空气分解为基本元素,然后与机身重新结合,这将是一个吸热反应,给机体带来更多的热量。我还得担心其散热率。如果太低,它会变得很热。从根本上讲,不管机身材料是什么,我们都要开发在这些环境下工作的热防护涂层。”
“We have a hope here that there are material solutions out there but—and there is always a but—we have to understand that these carbon-based materials oxidize,” said Hunn. “So in the air I have to worry about chemical catalytic reactions breaking the air down into its base elements and recombining that with the airframe—and that would be an endothermic reaction adding more heat to it. I also have to worry about heat emissivity. If it is too low it gets really hot. Fundamentally, no matter what the airframe materials, the chances are we will have to develop protective coatings to work in these atmospheres.”
工作温度超过1700℃的新型涂层研究主要集中在新型陶瓷材料上,例如碳化钽和碳化铪,以及硼化锆和硼化铪。汉恩说:“有些是陶瓷基材料,它们具有很好的抗氧化性能,因此有很多研究将这些新型涂层应用于某些先进复合材料上,作为当前高超声速飞行器机体的近期解决方案。”
Work on new coatings for temperatures in excess of 1,700C are focused on novel ceramic materials such as tantalum and hafnium carbide, and zirconium and hafnium borides. “Some are ceramic-based materials, which are pretty good oxygen barriers, so there’s a lot of research looking at some of these novel coatings on some of these advanced composite materials as near-term solutions for current hypersonic airframes,” said Hunn.
但是,为了将高超声速飞行器的发展推进到新的阶段,他说:“答案是我们必须超越大自然,发明我们自己的材料。”大学和研究实验室正在开展一项基础性的工作,其重点是利用计算能力和周期表中的路线图,“提出一些新颖的材料,这些材料具有高超声速飞行所需的特性。”他说。
However, to advance hypersonic vehicle development to the next level, he said, “The answer really is that we are going to have to sidestep Mother Nature and invent our own materials.” Work at a fundamental level is underway at universities and research labs that is focused on using computational power and a road map from the periodic table to “come up with some novel new materials that have the characteristics needed to roll into hypersonics,” he said.
汉恩指出,对中国和俄罗斯研究工作的评价表明,“他们在设计新材料并针对高超声速环境进行定制方面,确实在提高技术水平。”例如,莫斯科国立科技大学的科学家最近透露了对一种新的陶瓷化合物的测试,他们声称这种陶瓷化合物能够承受高超声速飞行器尖锐前缘或鼻锥的典型2000℃热负荷。科学家们说,这种被称为碳化铪的新材料的熔点还不清楚,但已经被证明超过了4000℃,他们补充说,计划在高超声速条件下做进一步测试。
Reviews of Chinese and Russian research work indicates “that they are really advancing the state of the art in designing new materials and tailoring them for the hypersonic environment,” said Hunn. Scientists from Moscow’s National University of Science and Technology, for example, recently revealed tests of a new ceramic compound they claim will withstand the typical 2,000C thermal loads of a sharp leading edge or nosecone of a hypersonic vehicle. The melting point of the new material, called hafnium carbonitride, is not yet known but has already been demonstrated to be beyond 4,000C, say the scientists, who add that further tests are planned at hypersonic conditions.
外部加热问题造成的后果是,为高超声速飞行器(包括滑翔和有动力)的高密度设备布置带来了工程和设计上的挑战。“你有一个变热的外表面,而你的内部是不允许变热的电子系统。”范·维说。
The corollary of the external heating issue creates an engineering and design challenge for the densely packed interiors of hypersonic vehicles—both gliders and powered. “You have an outside surface that wants to be hot and you have electronic systems inside that you can’t allow to get hot,” says Van Wie.
置于飞行器内部,防止热量从外部传递进来的隔热层使问题更加复杂。“那么,如何处理内部产生的热量?范维问。“这个问题没什么神奇的,这只是对工程系统的挑战。解决它的方法有很多种,但你必须从系统角度来研究它,要思考对于特定的飞行器类型和特定的任务来说,什么才是有意义的。”
The problem is compounded by the insulation built into the vehicle to prevent heat transfer from the exterior. “So, what do I do with the internally generated heat flux?” asks Van Wie. “There’s nothing magical about that problem—it’s just an engineering system challenge. There’s a whole variety of different ways of attacking it, but you have got to take a look at it from a system perspective and what makes sense for a particular vehicle type and a particular mission.”
准备升级
Readying the Ramp-Up
最后也是最紧迫的挑战,尤其是对美国第一代武器系统开发商而言,是建立工业基础能力,以支持计划中的生产增长。今年早些时候,美国国防部的采购部门在五角大楼设立了一个“作战室”,以评估工业供应链中的强势和弱势领域。
A final and more urgent challenge, particularly for the first-generation U.S. weapon systems developers, is establishing the industrial base to support the planned production ramp-up. Earlier this year the U.S. Defense Department’s acquisition leadership established a “war room” in the Pentagon to assess the areas of strength and vulnerability in the industrial supply chain.
Aerojet Rocketdyne公司为X-51A提供超燃冲压发动机的推进专家,积极参与了一系列进攻性和防御性高超声速飞行器的工作,从DARPA的滑翔破坏者和作战火力计划到先进的全尺寸发动机TBCC推进系统和洛克希德·马丁公司的吸气式高超声速武器方案(HAWC)。
Propulsion specialist Aerojet Rocketdyne, which provided the scramjet for the X-51A, is actively engaged on a series of offensive and defensive hypersonic efforts, ranging from DARPA’s Glide Breaker and Operational Fires programs to the Advanced Full Range Engine TBCC propulsion system and the hypersonic air-breathing weapon concept (HAWC) with Lockheed Martin.
Aerojet Rocketdyne公司防务板块高级副总裁泰勒·埃文斯(Tyler Evans)说:“我们专注于执行现有的项目,并有能力在时机成熟时完成(客户)所需的工作。”。“X-51是一个推进技术验证机,它证明我们掌握了超声速燃烧的科学机理。因此,今后十年,我们将专注于使超燃冲压发动机实用化,使其可重复使用,并在经济上负担得起。”
“We’re focused on executing the programs we’ve got and then having the capability and capacity to do what’s needed when the time comes,” says Tyler Evans, senior vice president of Aerojet Rocketdyne’s defense business. “The X-51 was a propulsion demonstrator that demonstrated that we could tame the science of supersonic combustion, and it did that. And so, 10 years later, we’re focused on making scramjets practical, making them repeatable, making them affordable.”
作为准备工作的一部分,该公司还收购了佛罗里达州的增材制造专家,3D材料技术公司(3D Material Technologies)。此举旨在降低其固体和液体火箭以及超燃冲压发动机的生产成本。埃文斯说,增材制造是“我们解决方案不可或缺的一部分”。
As part of the readiness ramp-up the company also acquired Florida-based additive manufacturing specialists 3D Material Technologies, in a move designed to support lower production costs across its range of solid and liquid rockets as well as scramjets. Additive manufacturing is “integral to our solution,” says Evans.
这条消息是Guy Norris在 Aviation Week & Space Technology 发表的文章。您可以点击此处查看更多关于高超音速的文章。