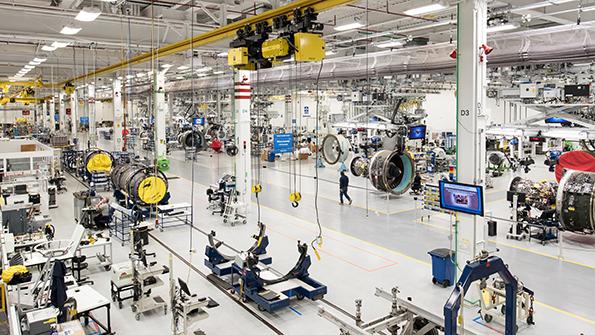
There is no shortage of ironies in the aerospace and defense sector, one of which is the race to automate and digitalize business while also struggling to hire enough workers to profit from the expected ramp-up of commercial aviation manufacturing in the post-pandemic era.
Digitalizing business operations is about cutting costs, boosting reliability—by removing the human worker, no less—and reaping the benefits of how one plus one can equal three in the technological sense. Hiring, however, is about having enough warm bodies on the factory floor to put together new products during a demand uptick that OEMs assert could surpass pre-pandemic production rates of airliners.
The two trends ultimately are in opposition, but because the timelines involved are so long—major aerospace advances are measured in decades, not years—there can be progress on both fronts for a long time. Still, some recent events outline how the dichotomy between the two trends likely will be a key theme of the 2020s.
Take a recent announcement by U.S. prosecutors. The U.S. Justice Department has unveiled an ongoing antitrust investigation into labor allocation in the aerospace engineering market and has revealed indictments against six executives who are alleged to have established an anti-poaching regime among their companies.
A federal grand jury in Bridgeport, Connecticut, returned an indictment on Dec. 15, 2021, charging Mahesh Patel of Connecticut, Robert Harvey of South Carolina, Harpreet Wasan of Connecticut, Steven Houghtaling of Connecticut, Tom Edwards of Connecticut and Gary Prus of Florida. Due to a LinkedIn profile, Patel, the alleged ringleader, was identified as an employee with Pratt & Whitney, the aero-engine division of Raytheon Technologies.
Besides the six who have been charged, “unnamed others” were involved in the eight-year plot that started in 2011. The conspiracy affected thousands of engineers and other skilled workers in the aerospace industry, the Justice Department says. The indictment alleges the executives knew that not recruiting and hiring each other’s employees would restrain their overall labor costs. “Patel and certain other co-conspirators explicitly appealed to this financial benefit when communicating with each other about the agreement,” the Justice Department says.
As Aviation Week workforce studies have noted for years: A&D companies have relied on poaching employees from each other as a primary means of meeting talent needs—rather than hiring and training graduates out of college or recruiting from outside the industry. Intra-industry recruitment became more dominant as industry downsized after the Cold War.
Yet large and midmarket aerospace companies cut roughly 19% of their workforce during the height of the COVID-19 pandemic, according to financial analysts. Even more aerospace workers are leaving on their own (AW&ST July 26-Aug. 8, 2021).
Many companies still will likely need thousands more workers to meet Airbus, Boeing and Embraer production forecasts through much of this decade. Approximately 65% of suppliers indicated labor and hiring comprise the primary risk to the cycle, according to a survey of 60 suppliers released Dec. 13 by RBC Capital Markets analyst Ken Herbert.
But as Patel’s alleged plot illustrates, keeping labor costs down was a key executive desire long before the pandemic, and leaders indicate it is even more important now. Digital technologies, which were once more of a vision than a business plan, are increasingly the solution of choice.
“As we continue to advance our focus on automation and digital and how we operate the business, we’re obviously going to look to . . . drive the margins and therefore not necessarily just automatically bring the direct part of the workforce back,” then-Raytheon Chief Financial Officer Toby O’Brien said in January 2021.
On that note, Pratt in October 2020 announced plans to invest at least $650 million through 2027 in a turbine airfoil production facility in Asheville, North Carolina. The plant, scheduled to open by the end of 2022, eventually may employ 800 workers, but it also will be a showcase of Industry 4.0 technologies. This is a trend that is likely to be repeated across the aerospace industry in coming years.
Are more aerospace workers needed? Yes. Do aerospace companies want to keep costs as low as possible? Yes. Is the industry accelerating adoption of automation, robotics and Industry 4.0? Yes. Will the 2020s be the decade of expanded aerospace hiring? Maybe.