Supply Chain And Hiring Woes Mar Demand Recovery
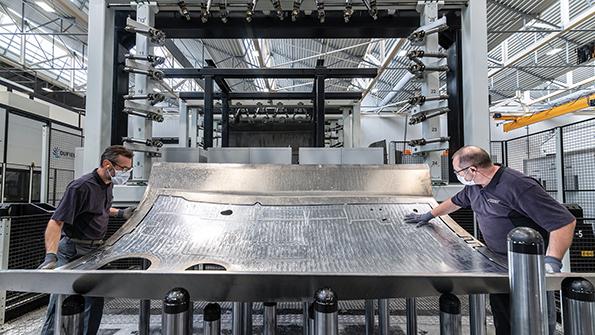
As OEMs strive to ramp up production and meet renewed demand for commercial, business and military aircraft, the global aerospace industry has to solve pressing issues. Tensions in the supply chain and a widespread skill shortage are combining to make every delivery a challenge.
A few positive indications are emerging, according to some major suppliers who are spending time reviewing processes with their subcontractors. Technical solutions are ready, such as raising the level of automation in factories and bringing microchip manufacturing in-house. Nevertheless, the overall recovery of the supply chain may take a long time to materialize, and customers may continue to face delays.
- Engine-makers’ problems are rippling through industry
- Automation has to be better understood
Causes can be found in raw material availability and prices, work organization and the impact the COVID-19 pandemic has had on employment.
“The impact of [COVID-19 and the war in Ukraine] has led to uncertainty over the supply of energy, electronic components and materials,” says Dassault Aviation Chairman and CEO Eric Trappier. “This has stoked an increase in inflation due to actual or potential shortages and weakened the supply chain, which is now at acute risk, given the increase in our production rate.” The fighter and business jet manufacturer shares part of its supply chain with Airbus.
Delayed engine deliveries have held back production increases at Airbus, Boeing and Embraer. “We are behind where we would have liked to be with Boeing and Airbus,” General Electric Chairman and CEO Larry Culp says. The bottlenecks also affect airlines waiting for spare engines and slower-than-usual heavy maintenance turnaround times.
“It may take 18 months for everyone to catch up,” Culp says. The issues are “not going to be solved overnight.” He blames the supply chain bottlenecks on “a wide range of underlying dynamics,” including shortages of materials and workers.
CFM International, the GE-Safran joint venture, is maximizing efforts to ease supply chain problems that have slowed deliveries of Leap engines to Airbus and Boeing. It is starting to see “signs of improvement,” says CFM President and CEO Gael Meheust.
CFM is the exclusive engine provider to Boeing with the Leap 1B and offers the Leap 1A in competition with Pratt & Whitney’s PW1100G geared turbofan on the Airbus A320neo.
“It’s a fact that the global supply chain is challenged,” Meheust says. The issues range from a shortage of labor and raw materials to longer production lead times. To address the problems, Meheust says the joint venture’s parent companies have deployed teams “with our suppliers to review their schedules to assist in any form we can and to help them if there is anything we can do to make sure they have a robust plan.” The goal is to improve the accuracy of data flowing through the chain to enable better planning.
The French aerospace industry’s lobbying association, GIFAS, has created so-called “watch towers.” Those teams are tasked with detecting financial problems at small suppliers. A dedicated investment fund may then go to that company’s rescue.
To solve the microchip shortage issue, California-based Cadence Design Systems offers aerospace OEMs the opportunity to avoid reliance on third-party microelectronics suppliers by helping them design and build their own chips.
“We provide the software, hardware and intellectual property,” says Frank Schirrmeister, Cadence’s senior director for the solutions and ecosystem group. “Think of it as the Lego blocks for chip design.”
James Chew, senior global director for aerospace and defense, describes Cadence Design as “the Home Depot of electronics development.”
“But the thing is, we have to train you,” Chew says. “Home Depot’s slogan is: ‘You can do it—we can help.’ . . . We’ll show you how to do it, and then you do it yourself.”
The skill shortage was already a concern before COVID-19, as production was ramping up, but it has become even more serious since then. “After two years of the ‘whatever it takes’ policy [to save the economy], returning to intense work is difficult,” Trappier says. Additionally, France has been confronted with a trend where employees are reconsidering the approach to work.
Further automating factories may be one answer. In the UK, industrial robotics specialist FANUC has struggled to explain what reasonable expectations for return on investment should be in factory automation.
The sector lags behind the automotive industry by more than a decade’s worth of robotics take-up, and over-ambitious amortization aspirations are holding aerospace back, says Oliver Selby, head of UK sales for FANUC. Industrial manufacturers in Europe and elsewhere tend to view 4-5 years as a reasonable timescale to see a return on capital investment, Selby says, whereas British companies expect to see a return within two years.
Moreover, automation may offer aerospace companies a chance to tackle their ongoing skills shortages and contribute to their environmental commitments. Some of FANUC’s products are fully electric, and Selby says that automated processes, when properly implemented, will often use up to 30% less energy than nonautomated ones.
Comments