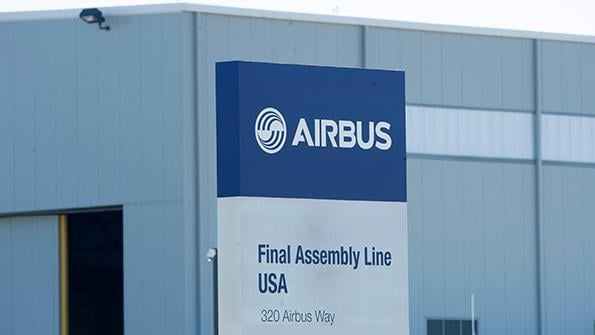
Airbus is in a historic position of strength, with the opportunity to become the world’s most important aerospace OEM. It is breaking out of its duopoly with Boeing, pursuing a production rate of 75 A320s per month, operating final assembly facilities in five countries (including two in North America) and seeking to position itself as the leader in sustainability. This raises the question: Why is it operating an antiquated supply chain for aircraft produced in North America?
Consider the Airbus wing supply chain for A320 wings assembled in Mobile, Alabama. Raw material, mostly aluminum, comes from mills in Europe and North America. It is shipped to component manufacturers for skins, ribs, stringers, winglets and control surfaces in Austria, France, Germany, Italy, South Korea, the UK and other countries. These components are then shipped to its wing fabrication facility in Broughton, England. Fully completed wings are shipped via a Beluga aircraft to Germany. There, they are loaded onto a specialized ship for a multiweek journey to Mobile, Alabama. These wings are then mated at the final assembly facility to other major assemblies, which also come from Europe.
Really?
This is closer to a 19th century mercantilist supply chain than a leading aerospace OEM 30 years after the Toyota Production System—which emphasizes speed and proximity of major Tier 1 suppliers to final assembly—became the global benchmark for manufacturing productivity.
It is time for Airbus to create a North American supply chain to match its soaring ambitions. The logic is compelling. First, it creates additional manufacturing capacity when the company needs it most. It is no secret that Airbus is at loggerheads with key suppliers as it pursues ever higher production rates for the A220, A320neo and other aircraft. The updated supply chain also would tap into North America’s low energy costs and relatively flexible labor compared to Europe. Importantly, this would provide a currency hedge for a company that sells its jetliners in U.S. dollars yet sources 74% of its spending from Europe. Just 19% is sourced from North America (principally engines and components), where it employs just 5.5% of its workforce.
From a financial perspective, a North American supply chain would speed up Airbus’ cash conversion cycle. Owning enormously expensive subassemblies stuck on ships for weeks is hardly a recipe for financial success or asset productivity. The revised supply chain also would expand Airbus’s defense opportunities in the lucrative and vast U.S. defense sector. Placing production facilities in strategic states would expand its U.S. political influence and improve its odds of winning a future defense program—such as the KC-Y next-generation tanker.
Resilience is another reason to diversify. If the COVID-19 crisis taught manufacturers anything, it is that redundant and more regional and local supply chains offer critical defense against black swan events and soaring shipping costs.
Finally, a North American supply chain would help Airbus meet one of its hallmark goals: sustainability. Its dispersed global supply chain, which supports seven final assembly facilities in five countries, consumes a lot of energy. Nearly 20% of the 3,774 GWh that Airbus consumes annually to produce aircraft is spent on operating its Beluga and maritime fleet as well as ground transportation. Local supply chains are greener.
Airbus should set up wing, fuselage and perhaps empennage production facilities in North America, supported by local subtier suppliers. Airbus need not own all these facilities; it could encourage its current suppliers to invest. Or it could tap into the rich aerostructures capability in the region—from suppliers such as Spirit AeroSystems (the world’s largest aerostructures supplier) or Mitsubishi Heavy Industries Aerospace Canada, a wing specialist in Ontario. Local subtier suppliers, coping with Boeing’s struggles and the aftermath of the COVID-19 crisis, would welcome the additional work.
The timing for supply chain modernization is perfect. It would relieve the pressure on Airbus’ European suppliers to invest in additional capacity, and it would position Airbus to be a more diversified aerospace OEM at a time when global defense budgets are surging.
This idea is not without risk. Aerostructures manufacturing is a notoriously low-profit endeavor, and some business cases for new capacity could be difficult to close. Airbus also would have to cope with the inevitable learning curve and quality escapes associated with new facilities and suppliers. And the OEM would have to deal with political blowback from European governments and labor unions.
Market leadership, however, entails taking risks and updated business models. It is time for Airbus to “think globally and produce locally” and update its supply chain model in North America.
Comments