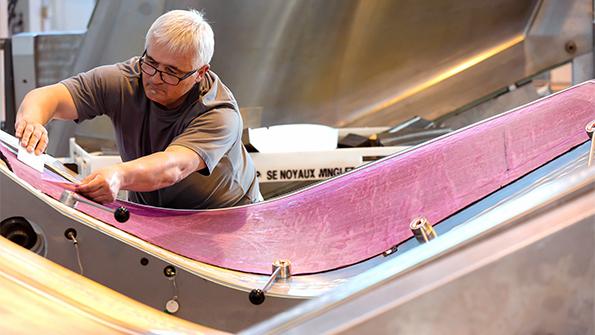
Ask the Editors: The Aviation Week Network invites our readers to submit questions to our editors and analysts. We’ll answer them, and if we can’t we’ll reach out to our wide network of experts for advice.
Do you feel that composite intensive designs like the Boeing 787 and Airbus A350 have set the bar moving forward?
France Bureau Chief Thierry Dubois responds:
Use of composites in aircraft will continue to grow. These materials, especially carbon-fiber reinforced plastic (CFRP), enable designers to create more efficient aircraft. They are not only light, but also enable external shapes to be more aerodynamic. And they make it possible to manufacture complex components as single pieces, reducing the part count.
In-service experience with CFRP-intensive aircraft, such as the Airbus A350 and Boeing 787, has not revealed any particular problems in operations or maintenance. Airframers have been both innovative and conservative, as they have gradually increased the share of composites in a design. For Airbus, composite usage increased significantly from the A380, at 25% composites by weight, to the A350, at 53%.
The trend is continuing. Compared to the A350-900, the latest A350-1000 has more CFRP parts, such as door surrounds.
Progress in two areas—manufacturability and recyclability—may further boost the use of composites. Thermoplastics, compared to conventional thermosets, are easier to manufacture. While the reinforcing fibers are the same, the resin matrix in a thermoplastic composite melts when heated. When cooled down, it resolidifies without losing any mechanical properties. Curing is more straightforward.
Thermoplastics lend themselves more easily to production automation. They are weldable, repairable and recyclable. Their mechanical properties mean they can be used in smaller quantities, allowing lighter structures. Further weight saving, around 15%, is expected thanks to induction welding of thermoplastic parts, which will cut the number of fasteners needed to assemble fuselage structures.
But the trend is relatively slow. The aerospace sector’s investments in thermoset production tooling are recent, and some have yet to be recouped. Boeing introduced thermoplastics in 2018 in “elementary structural parts” on the 787’s fuselage and wing, replacing metal and thermoset composites. Daher, which is supplying these parts, predicts the industry use of thermoplastics will grow from 300 metric tons in 2019 to 1,000 metric tons in 2029.
In two other segments of civil aviation, helicopters and business jets, large structural parts such as tail components are already made of thermoplastics.
Improvements in recyclability of composites are also expected. Until now, high-performance aerospace carbon fiber has been recycled into lower-value products. New efforts aim at recycling more fiber while retaining its features. Keeping the fiber’s length, rather than chopping it up, is key.
Airframe application requires fibers on the order of several dozen centimeters in length. For high mechanical performance, the fibers must be oriented consistently. Orienting short fibers is impractical, but the recycling processes developed so far involve chopping up the fibers. Tarmac Aerosave, a specialist in aircraft dismantling and recycling, says the technology for producing long fibers from recycled CFRP is now mature. But it has yet to name companies offering such processes.
Another company, Xcrusher, has been developing a technology to recover uncured composite offcuts from a factory. The process can yield kilometers of fiber with constant section length and constant specific weight, according to the company.
ELG Carbon Fiber is developing techniques to use recycled carbon fiber in structural applications. Last December, it unveiled the world’s first train bogie made of such material. Recycled carbon fiber is thus making its way to higher-value applications.
Meanwhile, progress in aluminum alloys, which have long been the most used materials for aircraft construction, should not be overlooked. Metal producers are developing lighter alloys. They are offering more integrated solutions, such as pre-machining. And they arguably lead in recycling.