Startup Tackles Infrastructure Barrier To Decarbonizing With Hydrogen
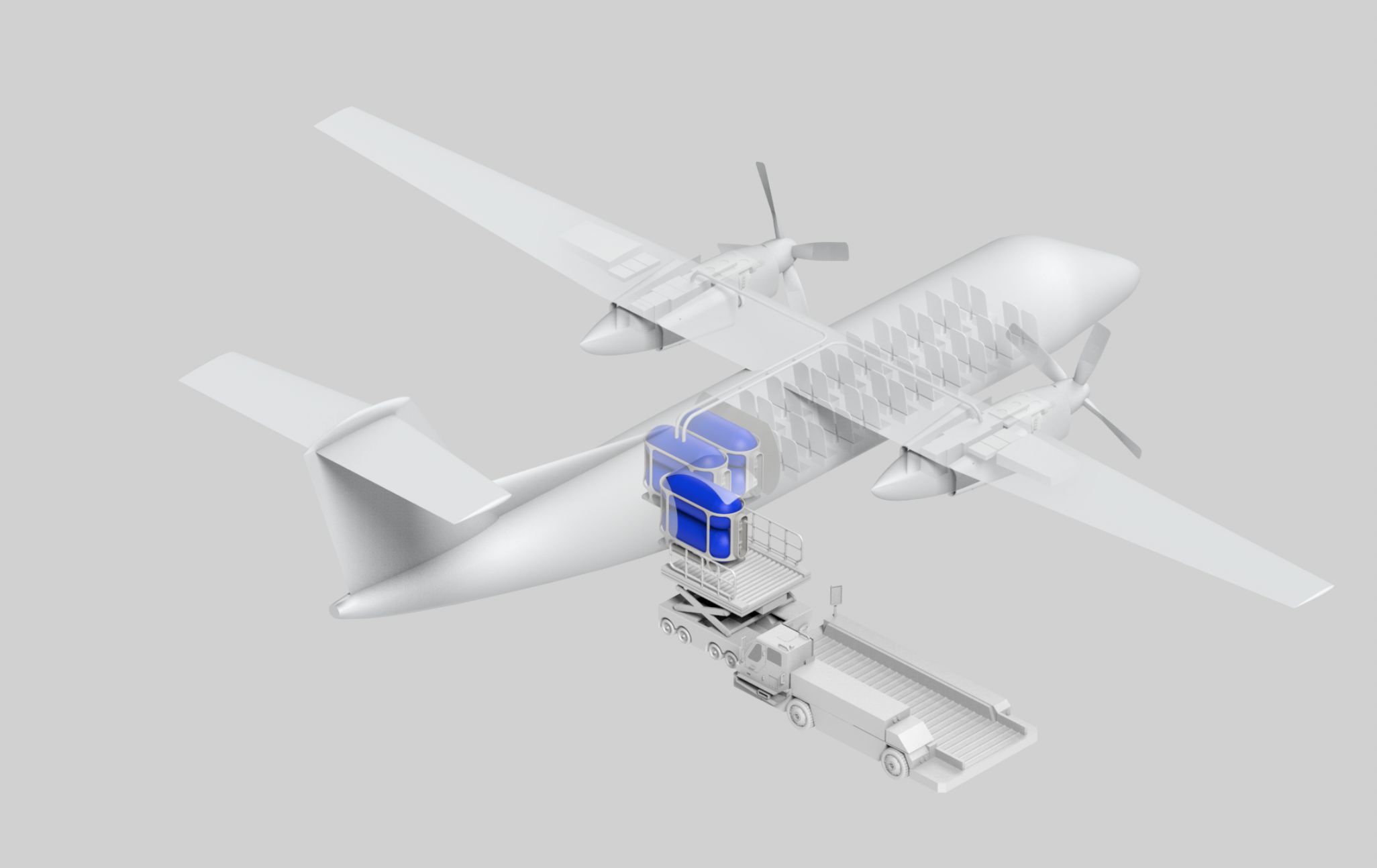
Hydrogen is gaining attention as a means to deeply decarbonize aviation, with Airbus looking at the fuel as one way to meet its stated commitment to bring an aircraft with net-zero carbon emissions to market by 2035. But previous efforts to bring hydrogen to aviation have stumbled over the high cost barrier of the infrastructure required for production and distribution.
- Universal Hydrogen infrastructure designed to be scalable globally
- Two-capsule fuel-cell modules would be easily transportable
- ATR and Dash 8 conversions first with sights set on single-aisles
Former Airbus and United Technologies chief technology officer Paul Eremenko has launched a venture to build the infrastructure for hydrogen-powered commercial aviation.
To kick-start the market, startup Universal Hydrogen plans to convert ATR 42 and De Havilland Canada Dash 8-300 regional aircraft to hydrogen fuel-cell propulsion to pump-prime demand. But Eremenko’s goal is to prove out the company’s hydrogen infrastructure before Airbus and Boeing make technical decisions on the next generation of single-aisles in the latter half of the 2020s.
“If we want hydrogen aviation to happen, we need a much more capital-light approach,” Eremenko says. “Our goal is to produce a minimally capital-intensive approach to building a hydrogen infrastructure that is scalable to global scale.”
Universal Hydrogen is developing a lightweight, modular capsules—“think of them as batteries,” Eremenko says—that can be transported via the existing global intermodal container network and loaded with existing airport equipment into aircraft that have been minimally modified to operate on hydrogen.
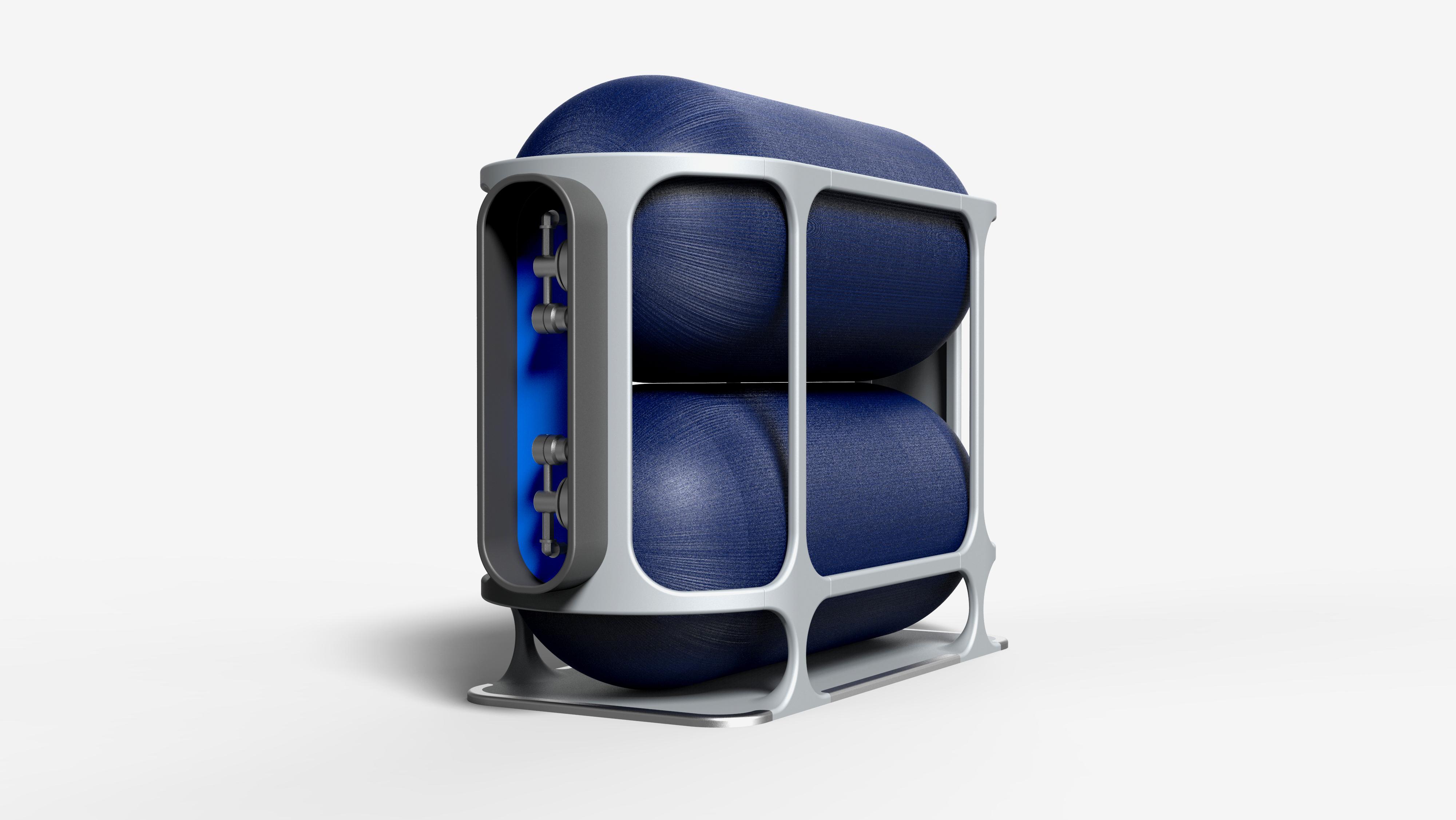
“What we are trying to do is connect production to consumption, and allow them to take place in geographically disparate areas at temporally disparate times,” Eremenko says. “We are not especially keen to do either production or play long-term in the consumption business, but we may have to do a little bit of both in order to get the aviation hydrogen market going.”
Universal Hydrogen is developing both 850-bar high-pressure gas and liquid hydrogen capsules in the same interchangeable form factor so an airline can choose between them for each flight. “For the Dash 8-300 with the gaseous capsules, we get 400 nm range. With the liquid capsules, we get 550 nm,” Eremenko says. “The fleet-wide average stage length for these aircraft is about 300 nm. So even with the gaseous solution you’re going to be able to perform 75-80% of all missions flown.”
The capsule is a cylinder with rounded ends, for more efficient packaging during transport and storage in the aircraft, Universal Hydrogen chief technology officer JP Clarke says. One pair of capsules is mounted in a frame that provides structural support, plumbing and other systems. These two-capsule modules are then transported as dry freight in cargo containers by road, rail or sea. At the airport, they are loaded onto the aircraft using existing ground handling equipment—or a forklift at more austere locations, Eremenko says.
Insulated but uncooled, the liquid capsule has a maximum 40-hr. dwell time between production and consumption because overpressure builds up as the hydrogen evaporates. “As a result of that, and because liquefaction is a more energy-intensive process than compression, an airline would pay more for the liquid capsule. But they’d get a slightly better range,” Eremenko says.
In the case of the Dash-300 retrofit, up to three modules—or six capsules—are slotted into the rear fuselage forward of the cargo area, which would be untouched. The service door is widened slightly as part of the supplemental type certificate modification. The hydrogen is plumbed through the dorsal fin, external to the fuselage pressure vessel, into the nacelles.
In each nacelle is a 2-megawatt hydrogen fuel-cell stack powering an electric motor—either a single motor of about 2 megawatts or around 1.6 megawatts, plus a smaller motor for auxiliary power. The existing propeller and controller are retained. A small lithium-ion battery handles throttle transients.
A fuel-cell’s only emissions are warm air and water vapor. A thermal-management system including a P-51 Mustang-style zero-drag radiator on the nacelle cools the fuel-cell and motor. The water is collected in the outer-wing fuel tanks and dumped at flight conditions when no contrails are produced.
“We’ve designed the retrofit so that it meets or exceeds the nominal aircraft performance, other than the change in range capability,” Eremenko says. “We lose two rows of seats in the back. And we relocate the rear galley to the front, which causes us to lose two rear-facing seats in the front. So we lose a total of 10 seats and the Q300 goes from a 50-passenger to a 40-passenger airplane.”
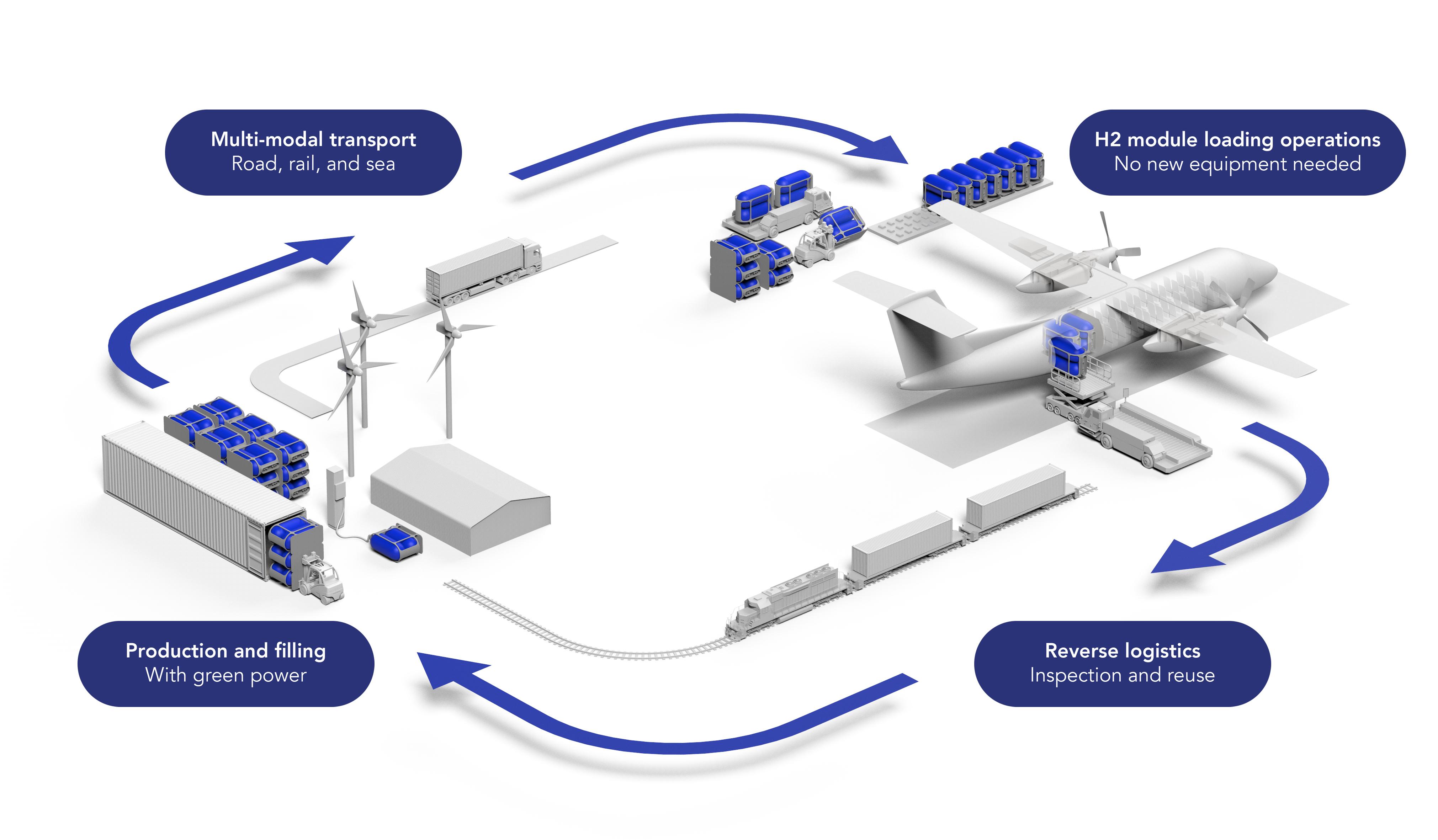
Despite the loss of seats, operating economics in 2025—in terms cost per available seat mile—are estimated to be roughly equal between the modified and unmodified Dash 8. Hydrogen is projected to be more expensive than jet fuel in 2025, but that cost is expected to come down over time, he says.
“There will be a growing cost advantage to hydrogen. On top of that, the maintenance and overhaul costs for a fuel-cell-electric powertrain are quite a bit lower than for a turboprop engine. Our estimates for maintenance and overhaul costs suggest at least a 25% improvement,” Eremenko says.
Universal Hydrogen is working with partners to lighten a proven terrestrial fuel-cell and develop the motor. “These are fundamentally off-the-shelf technologies. I don’t want to understate the challenge, but we think our plan is attainable on a three-year timescale,” he says. “We’re allowing some margin with a 2024 entry into service.”
The startup has also engaged the regional airframers. De Havilland Canada has been “an exceptional partner to us thus far,” Eremenko says. “ATR, which is starting to think about hydrogen, has also been positive toward the effort.”
What would regional carriers have to pay in exchange for going green? “The value proposition that we offer is that we would subsidize the conversion to hydrogen for them, up to offering it as a no-cost conversion in exchange for a long-term hydrogen fuel contract,” he says. The established renewable-energy project finance market would then be tapped to pay for the conversions.
“The regional aircraft fuel market is about $2 billion/year. So we might create a billion-dollar business by supplying the regional market if we get really good penetration,” Eremenko says. “The huge opportunity in the 2030s is the single-aisle. And both Airbus and Boeing seem likely to make decisions on the technology base for the single-aisle in the mid- to late-2020s, for an entry into service in the early 2030s. And we would like to de-risk the decision for them, as much as we can, to go with hydrogen.”
Universal Hydrogen is six months into the initial design phase, self-funded to the tune of about $3-5 million if partner efforts are included, he says. “We’re going into detailed design in the next month or two. And, by this time next year, we would expect to have an iron bird of the powertrain as well as an end-to-end demonstration of the full-scale capsule technology.”
Experimental flight testing will follow, with one side of the aircraft converted to fuel-cell propulsion and the other left unmodified for safety of flight. “After experimental flight, we would go into certification flight test. And alongside that, we would mature the hydrogen logistics network and develop a low-rate initial production system for the capsules and the modules,” he says. “To get us to market, we need an equity raise of about $300 million.”
After kick-starting demand with its ATR and Dash 8 conversions, the startup plans to release its modification as an open-source reference design that can be customized by developers of commuter aircraft, single-engine turboprops or urban air mobility vehicles—Eremenko’s eyes are firmly on decarbonizing the single-aisle sector.
Universal Hydrogen is already in discussions with both Airbus and Boeing. “They’re both receptive and learning more about our approach and technology,” he says. “But the proof will be when we are actually in operation at scale from 2024 onwards showing that we have solved the infrastructure and logistics problem for hydrogen for them.”
Comments
Where will all that energy be sourced? Fossil fuels of course, because there is no viable technology to replace them. And how will these fuel cell modules be delivered? By fossil fuel burning vehicles on land and sea.
Decarbonizing one industry simply carbonizes another with the present state of technology.
And the "value proposition"? How will H2 ever compete economically with the several hundred years supply of fossil fuels that exist on earth?