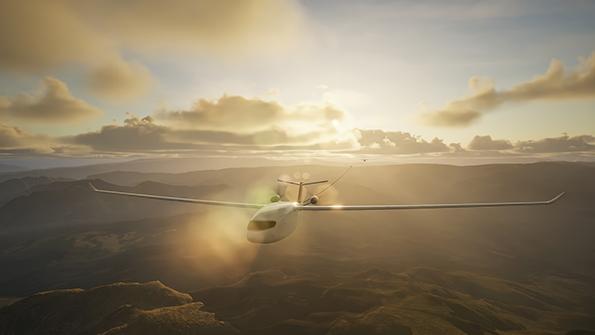
Purpose-designed electric aircraft would tow the main aircraft in climb and cruise to extend the range of zero-emission flights.
In the race for sustainable aviation, developers of both electric- and hydrogen-powered aircraft face the same problem: how to provide enough range without over-penalizing payload.
California-based startup Magpie Aviation is developing a system to provide a zero-emission solution to the challenge using current battery technology. The company is flight-testing the first elements of an aero tow concept in which electric and other aircraft will be tethered to an all-electric tow aircraft to extend their range by hundreds of miles.
- Inflight towing would extend range
- Active hook for tether tested in flight
- Dedicated electric tow aircraft in design
From a small proof-of-concept demonstration, Magpie plans to scale up the aero tow system gradually to the point at which, by 2030, regional turboprop-size aircraft could be pulled in everyday commercial service by electric tow aircraft. Beyond this, the company expects that advances in battery technology will enable the tow concept to be expanded to transports the size of single-aisle airliners.
Magpie envisages an initial phase in which electric passenger and cargo aircraft automatically connect to an electric tow aircraft after takeoff and are assisted in their climb to cruise altitude. Later phases would expand the capability of the system to enable a tow vehicle to pull aircraft at high speed for up to 300 mi. per charge. Eventually, the startup foresees a network of electric tow aircraft that would be pre-positioned to enable multiple aero tow stages covering flights extending more than 1,000 mi.
“It sounds kind of crazy, but we kept coming back to it because we couldn’t find any reason why we couldn’t do it,” Magpie CEO Damon Vander Lind says. Although targeted at electric-powered aircraft, Magpie says the tow concept could be adapted to hybrid- and hydrogen-powered designs as well as any conventional aircraft capable of being operated in a low-power mode.
“If we have this goal of zero emissions by 2050, there’s this big question mark—particularly over truly long-distance flights with high payload and zero emissions,” Vander Lind says. “The reason we chose to work with battery-electric [aircraft] is it’s hard to hit the economics when you have a 20-something-percent efficiency level [for hydrogen and electrofuels],” he says, referring to other propulsion options to decarbonize aviation.
Under Magpie’s concept of operations, the towed aircraft will have power reserves adequate to take off and land as well as to fly to an alternative airport. Vander Lind says the towing aircraft will be “all batteries” and optimized for its role with electric pusher propellers, a fast climb rate and high-aspect-ratio wing. Because electric-powered aircraft do not suffer the same lapse-rate performance reduction with increasing altitude as turbine aircraft, “we can stay at highly efficient indicated airspeeds while still going quite fast, with a relatively small platform,” he notes. “That’s one of the non-intuitive things about battery-electric aircraft that we see as enabling our technology.
“While our modeling shows that there is an advantage to doing a custom tow aircraft like this,” Vander Lind continues, “we get a big advantage because the more expensive and critical passenger- and cargo-carrying ‘main aircraft’ has similar requirements to today’s aircraft and so adapts well to existing in-operation and already-in-development platforms. Remember that if we want to hit a zero-carbon 2050 goal, an airliner has a 30-year life, so we’re already at the point where airlines have to think hard about the operating life of the assets that they are buying today.”
Vander Lind adds that “you get towed until you’ve depleted down to your reserve in the lead aircraft, and then you swap in another tow aircraft.” By stringing together multiple tows “you start to get flights like San Francisco to Seattle with today’s battery technology,” he notes. “It starts to fit within the realm of the feasible.”
Before founding Magpie, Vander Lind established the Heaviside electric vertical-takeoff-and-landing aircraft division of startup Kitty Hawk. And prior to that he ran Makani Power, a company that was developing huge tethered airborne wind turbines before being acquired by Google.
After better-than-expected results from studies of the concept by airline economic consultancy firms, Magpie approached the FAA with the idea. “We thought there’d be more regulatory hurdles. There are some challenges, but they were mostly building on what exists today for towing or refueling,” Vander Lind says. The next major technical issue was development of a safe and reliable automated “active hook” connection device for the tether.
A prototype system recently was flight-tested in Nevada with a glider and Pipistrel tow aircraft flown by test pilots Jim Payne and Tim Gardner. “I took off being towed by the Pipistrel Virus with the active hook on the nose of the PIK-20D sailplane,” Payne says. “We towed to 10,000 ft. [above mean sea level], where I released. Tim Gardner then started about a 500-fpm descent in the Virus while I flew formation on the hook. When he was stable, I moved forward and made a connection. After each connection, he would tow me up about 1,000 ft., where I released and repeated the process. We did this three times on the first flight and five times on the second flight.”
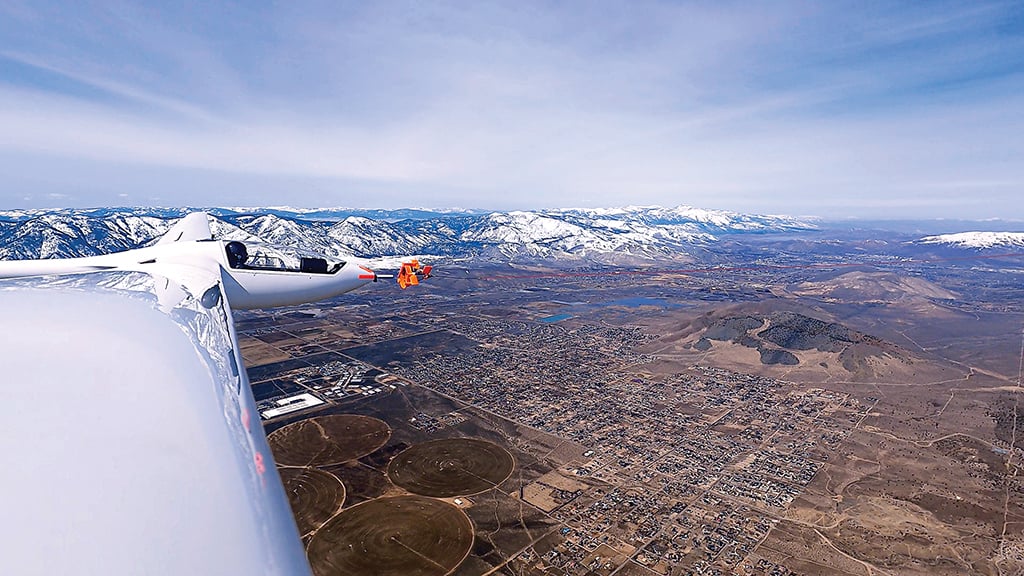
The tests, thought to be the first time a glider has reconnected with a tow in flight, proved the ability of the hook to steer automatically toward the glider’s nose probe. The tracking system in the device uses real-time kinematic (RTK) GPS, a technique that increases the accuracy of satellite-based positioning signals by using a fixed base-station that sends corrections to a moving receiver wirelessly. Using these corrections, the RTK GPS receiver can fix the position of the antenna to within 1-2 cm (0.4-0.8 in.).
“We’ve also used a vision system as well, because we think that there will have to be a fusion of different sensor sources for the final version, because you can’t always rely on GPS,” Magpie Chief Technology Officer Andrew Goessling says. “The glider moved around behind the tow plane, and the active hook was autonomously tracking it wherever it went. The pilot is just responsible for closing speed; everything else lateral and vertical is taken care of by the device.”
The automated technology makes connecting to the stabilized active hook easier than probe-and-drogue aerial refueling used in the military, which “requires a considerable amount of pilot skill,” Payne says.
The tether used in tests so far is a synthetic fiber rope only 1/10 in. (2.5 mm) in diameter, like that used in marine and construction applications. It reflects the relatively low forces involved in towing an aircraft while in cruise, Vander Lind says. “That 2.5-mm tether, moving at the speed of a jetliner [Mach 0.85], would convey about 500 hp,” he points out. “That’s with a standard safety factor for a high-performance fiber that you’d see in other safety-critical applications such as cranes.”
For simplicity, safety and certification reasons, the tether will not be used to transfer electricity to recharge the aircraft on tow in flight.
Although the tether used in current flight tests is some 100 m (330 ft.) long, the planned in-service line would extend upward of 500 m to 1.5 km (0.9 mi.), Vander Lind says. The longer length will effectively “de-couple” the two aircraft from any turbulence-induced interaction and provide opportunities for harvesting wake energy, he says.
Magpie is using a glider receiver in initial tests for cost reasons and is modifying another aircraft with an electric propulsion system for future work. “Obviously, [using a glider] makes it a harder problem because you don’t have a throttle lever to control back-and-forth positioning,” Goessling says. “But to do it successfully in that situation means that it should be easy to do when you’re just doing a level flight.”
“There’s a lot of work to go from initial proof-of-concept to a product,” Vander Lind says. Further tests planned for the hook include night and simulated instrument flight rules engagements. “We are going to look at the edges of the envelope so we can really understand any corner case that can go wrong with the device,” he says. “What you really need is for this to be a product with a lot of robustness.”
The future electric tow aircraft will have a second seat for carrying observers. “We will be able to bring people up to experience it,” he adds. “We think that for this type of problem, public perception and building consensus around this being a potential solution is a really important part of what we have to do.”
Editor's note: This article was updated to clarify Magpie CEO Damon Vander Lind's statement about the choice of working with battery-electric aircraft.
Comments