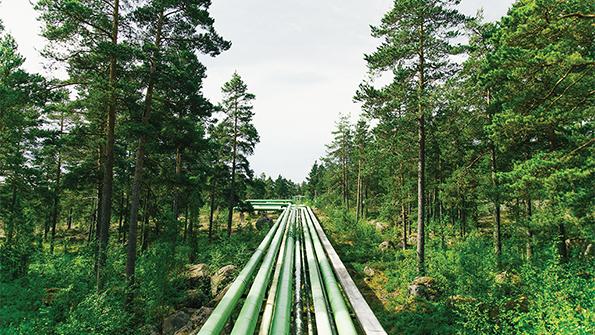
Echoing the Ancient Mariner, the world’s airlines are lamenting the woeful lack of sustainable fuel in a sea of fossil kerosene. And with US airlines joining those in the UK and elsewhere in committing to achieve net-zero carbon emissions by 2050, the need for alternative aviation fuels is becoming acute.
Every scenario developed by the industry shows that scaling up production of jet fuel from sustainable sources is critical to reducing aviation emissions in the near term. This holds true even as fleets are renewed with more fuel-efficient aircraft, airspace operations are improved and new propulsion technologies are developed.
But the scale-up challenge is enormous. Barely 60 million gal. of sustainable aviation fuel (SAF) was produced in 2020, a tiny fraction of the record 96 billion gal. of jet fuel consumed by the world’s airlines in 2019—a number that, before COVID-19, was projected to reach 215 billion gal. by 2050.
Announcing its members’ commitment to be net-zero by 2050, Airlines for America (A4A) at the end of March also pledged to work with the government and other stakeholders to make 2 billion gal. of SAF available to US aircraft operators in 2030. Scale that globally and the size of the task ahead is clear.
Since 2009, civil aviation has had the aspirational goal of halving its carbon emissions by 2050 from 2005 levels. The new commitments to net zero by 2050 represent a significant acceleration by those nations with the resources to do so. A global long-term goal to be agreed by ICAO in 2022 may be more achievable by all, but is certain also to rely heavily on SAF.
That some airlines have set even more aggressive net-zero deadlines will only increase the pressure. Cargo carrier Deutsche Post DHL wants to meet 30% of fuel needs with SAF by 2030. It consumed 480 million gal. in 2019. Delta Air Lines wants to reach 10% SAF by 2030 and consumed 4.2 billion gal. in 2019. Add JetBlue Airways, which plans to be net-zero by 2040, and demand could outstrip supply.
Scaling up is essential also to bringing down the cost of SAF, which is now between three and five times as expensive as Jet A fuel. IATA sees the scale of production at which SAF becomes cost-competitive with jet fuel as 2% of 2019 consumption, or 1.9 billion gal. a year. IATA believes that tipping point could be reached in 2025, but it means a 30-fold increase in production.
With the emergence of new propulsion options, there is debate over the long-term need for SAF. EasyJet CEO Johan Lundgren argues that short-haul carriers should invest in carbon offsets rather than SAF because zero-emission technologies like electric and hydrogen are on the horizon.
But electric- and hydrogen-powered aircraft will have short ranges for the first few decades—500-1,000 nm—so for existing short/medium-range fleets during the transition and for long-haul fleets in the long term, SAF looks to be the only viable decarbonization option.
Why Use SAF?
Global commercial aviation accounted for just over 1 billion tons (907 million metric tons) of CO2 emissions in 2019. Excluding any improvements in technology and operations, and even allowing for the pandemic impact on traffic, this is projected to nearly double to almost 2 billion tons by 2050.
Whether the goal is a 50% reduction or net zero by 2050, more fuel-efficient aircraft, improvements in air traffic management, and new electric and hydrogen propulsion technologies will only get the industry part of the way. SAF and carbon offsets will be essential, to a greater or lesser extent.
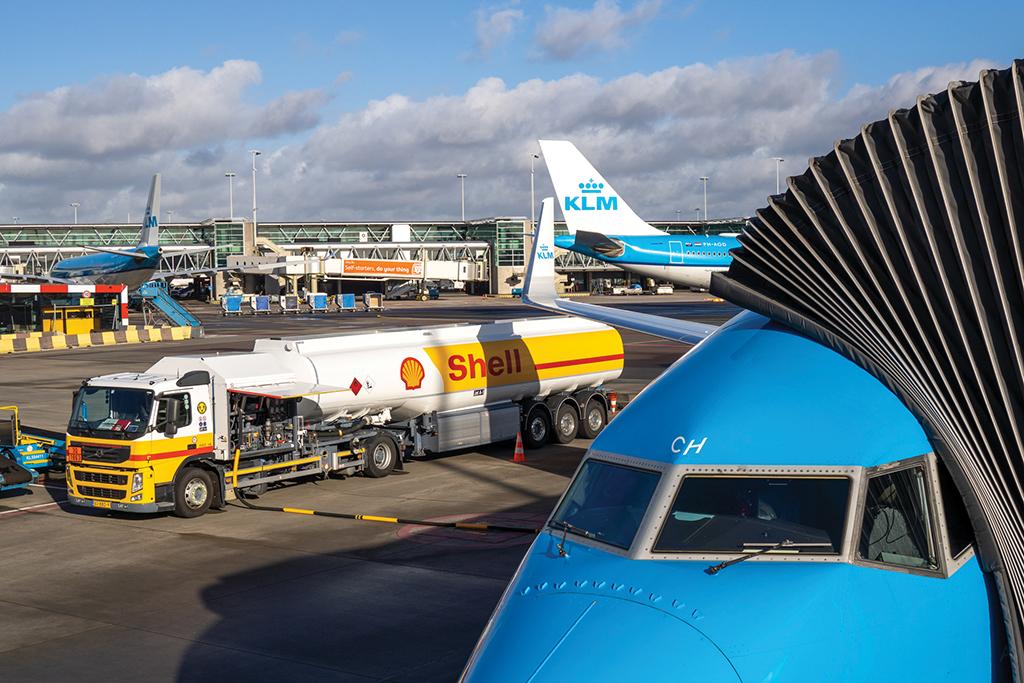
SAF does not reduce the “tailpipe” emissions from burning fuel in flight. The calculated reductions in greenhouse-gas emissions come from the life cycle of carbon. Consuming conventional jet fuel releases fossil CO2, pulling it from the ground and adding it to the total carbon in the biosphere. Burning SAF returns to the atmosphere carbon that had been absorbed by plants or that would have been released as industrial waste gases or by incinerating household garbage.
The result is a net “well-to-wake” reduction in life-cycle CO2 emissions. This can be as high as 80% for SAF produced from biomass such as used cooking oil. Higher reductions can be achieved using woody feedstocks such as forestry residues. Synthetic fuels produced from captured CO2 and renewable electricity can reach well-to-wake reductions of 100% relative to fossil jet fuel.
Some feedstocks even promise to be carbon negative. Researchers at the US National Renewable Energy Laboratory reported in March that SAF made from food waste has the potential to reduce net carbon emissions by up to 165%. The large reduction claimed is based on preventing food waste rotting in landfills from releasing methane, a greenhouse gas 20 times more potent than CO2.
How Much SAF?
Released in September 2020 by the cross-industry Air Transport Action Group (ATAG), the Waypoint 2050 sustainability blueprint laid out three scenarios for how the aviation industry could meet its stated goal of reducing CO2 emissions by 50% by 2050. In all of them, SAF is essential.
The most aggressive scenario for deployment of SAF would need 116 billion-151 billion gal. (440 billion-570 billion liters) per year of production by 2050. Even with the most aggressive fielding of electric and hydrogen propulsion technologies, 62 billion-90 billion gal. a year of SAF would still be needed.
And that is just to halve net CO2 emissions by 2050. While that target is in line with the Paris Agreement goal to limit global temperature rise to well below 2 C, ATAG says, aviation will have to make even more aggressive cuts in carbon emissions if it is to help achieve the preferred climate target of 1.5 C.
Getting onto the path to limit the global temperature rise to 1.5 C could require all of global aviation to reach net-zero emissions by 2050, ATAG notes, which could demand another 38 billion gal. a year of SAF production capacity.
Identifying the rapid and global scaling up of SAF as “perhaps the single largest opportunity to meet and go beyond the industry’s 2050 goal,” Waypoint 2050 concludes aviation will likely need 150 billion-170 billion gal. a year by 2050.
Against this background, ATAG is analyzing what needs to be done over the next 10 years to achieve whatever the industry ultimately sets as its target. The deep dive is looking at how many SAF production facilities are needed, and where.
With hundreds of SAF plants required globally, each costing hundreds of millions of dollars to build, the scale-up task is daunting. In the UK alone, 14 plants are required to produce 1.3 billion gal. a year by 2035 and just one of those—Velocys’s Altalto waste-to-fuel plant—will cost almost $700 million.
How Usable Is SAF?
Scaling up production is one issue; scaling up consumption is another. Currently, the use of SAF in aircraft is limited to blends of up to 50% with conventional jet fuel. This limit is imposed so that SAF blends can be treated as “drop-in” fuels and mixed with conventional Jet A in airport supply systems then used in all aircraft without modification.
The blend limit is required because most of the feedstock-to-fuel pathways so far approved produce a synthetic paraffinic kerosene that does not contain all of the hydrocarbons found in fossil jet fuel. The lack of aromatic hydrocarbons could cause problems with fuel systems and seals in aircraft and engines.
While availability of SAF keeps blends to single-figure percentages, such limits are academic. But as airlines look ahead to increasing use of SAF, these become a drawback. As a result, the engine makers, with Airbus, Boeing and other aircraft manufacturers, are working to make their products compatible with 100% SAF. Boeing’s goal is to certify all its commercial aircraft to operate on 100% SAF by 2030.
One of the seven already-approved feedstock-to-fuel pathways for SAF, catalytic hydrothermolysis jet, or CHJ, contains aromatics so the blend limit could be increased from 50% to 100% and it would still be a fleetwide drop-in fuel. Other pathways with the potential for 100% use are undergoing approval. But increasing the blend limit on most SAFs will require more testing and a revision to the fuel specification.
The first SAF to become commercially available at any scale, hydroprocessed esters and fatty acids, or HEFA, is limited to a 50% blend because it lacks aromatics. However, engine testing with 100% HEFA by Rolls-Royce and flight tests by Airbus and Boeing indicate that newer design aircraft could operate safely on this purely paraffinic fuel, allowing airlines to fully benefit from the life-cycle CO2 reduction.
But unblended HEFA is not a drop-in fuel. A manufacturer could approve the use of 100% HEFA in specific aircraft, if the data supports it, but it would need to be handled separately from the fungible jet fuel supply because only certain aircraft could use it, the FAA says. So 100% HEFA would be a SAF that is a “limited or targeted drop-in” and not suitable for the entire fleet.
Who Makes SAF?
In 2020, there were just two main producers of SAF: World Energy in California and Neste in Finland. That will change dramatically over the coming months as more production facilities are brought on line and more feedstocks and regions are brought into play, all the result of investments years in the making.
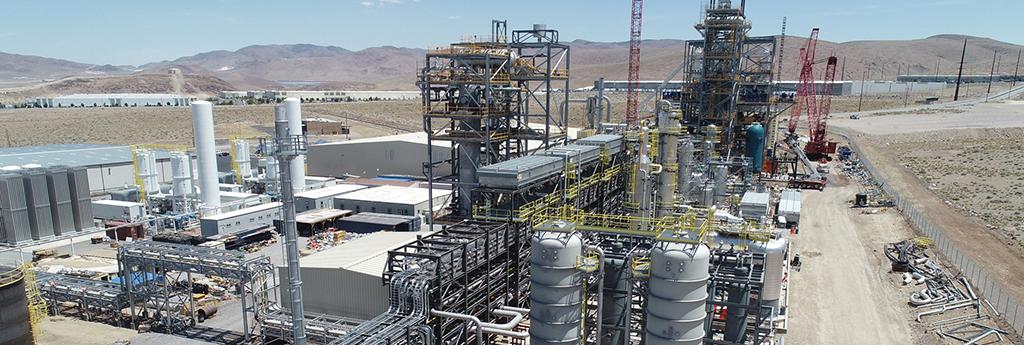
In addition to Neste and World Energy scaling up their existing production capacity, key first-of-kind SAF plants are scheduled to come on line between now and 2024. For 2021, these include Fulcrum BioEnergy’s 10.5 million gal./year plant in Reno, Nevada, producing SAF from municipal solid waste (MSW). Red Rock Biofuels’ 16 million gal./year facility in Lakeview, Oregon, is also planned to begin operating this year, producing fuel from woody biomass.
In 2022, LanzaJet’s first ethanol-to-fuel plant is scheduled to be operational in Soperton, Georgia, with the capability to devote 90% of its 10 million gal./year capacity to SAF. LanzaJet has aggressive plans to have four plants operational by 2025 producing 100 million gal./year of sustainable fuels.
SkyNRG, co-founded by KLM in 2010 to develop the supply chain for sustainable aviation fuel, plans to have Europe’s first dedicated SAF plant operational in 2023. The DSL-01 facility in Delfzijl, Netherlands, is designed to produce 36 million gal./year of HEFA SAF and other products from waste oils.
Also by 2023, World Energy plans to have completed the expansion of its Paramount, California, HEFA plant to 150 million gal./year of capacity, while Neste is aiming to reach 480 million gal./year of HEFA output from plants in Finland, Singapore and the Netherlands.
According to the FAA-led Commercial Aviation Alternative Fuels Initiative (CAAFI), 2023-24 could see almost another 600 million gal./year of SAF capacity added. Projects planned to become operational include Gevo’s first plant to convert inedible corn to sustainable fuel, in Luverne, Minnesota.
The SAF scale-up will also become more global. Petroleum refiners Total in France and Preem in Sweden plan to commission their first HEFA plants in 2024 and Omega Green, a 300 million gal./year facility in Paraguay, is planned to be operational by 2024 producing HEFA SAF and green diesel.
Is There Enough Feedstock?
A key feature of the SAF scale-up over the coming years is the shift to waste streams as the feedstocks for fuel production. Some of the early efforts to produce renewable fuels drew criticism for using sources such as palm oil, which drove changes in land use and diverted resources from producing food.
Initial commercial production of SAF is largely using waste vegetable oils and animal fats such as tallow and used cooking oil. But availability of such feedstocks is finite. As more production pathways are approved and production facilities constructed, the range of usable feedstocks is broadening.
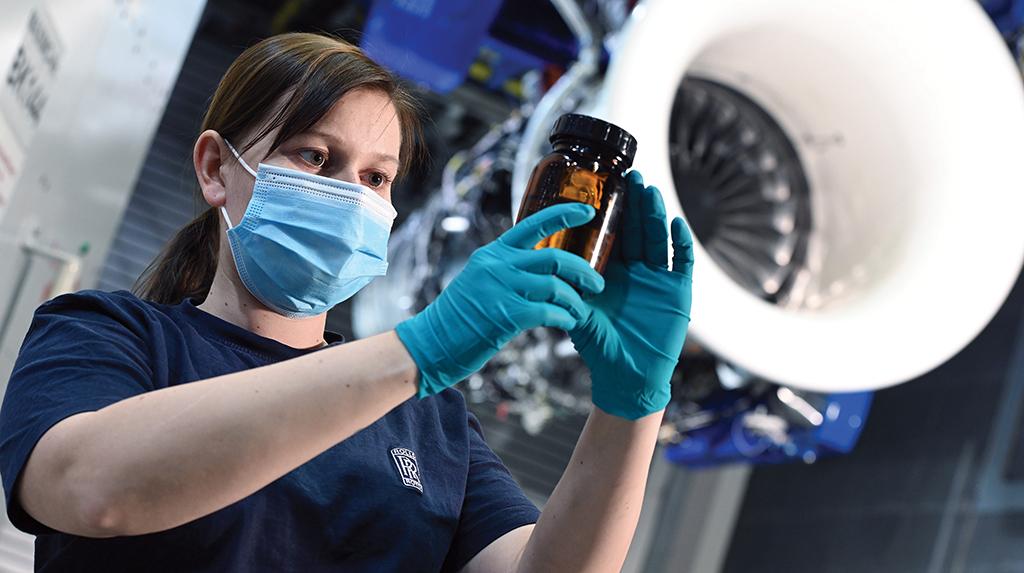
The aviation industry favors a shift toward waste streams that do not compete with food production. Sources are expanding to include municipal solid waste that would otherwise go to landfills or be incinerated, waste gases from industrial processes, and residues from agriculture and forestry.
There is also growing interest in power-to-liquid (PtL) synthetic fuels, also known as electro-fuels or e-fuels, produced from captured atmospheric CO2 and renewable electricity. This is particularly true in Europe, which has limited capacity to produce biomass as feedstock for sustainable fuels. PtL technology is still immature and expensive, and will require massive scale-up in renewable energy generation.
In February, KLM completed the first commercial flight on a partial blend of synthetic PtL kerosene produced by Shell from CO2, water and renewable energy. At the same time, two e-fuel projects were announced in the Netherlands: Zenid in Rotterdam and Synkero in Amsterdam. Other e-fuel production projects are planned in Denmark, Germany and Norway.
An analysis of SAF production potential by the World Economic Forum (WEF) suggests sufficient capacity exists across different feedstocks to meet even ATAG’s most aggressive scenario for the deployment of SAF to meet aviation 2050 targets. The analysis indicates the potential to produce almost 38 billion gal. from MSW, 57 billion gal. from agricultural and forestry residues and 15 billion gal. from waste gases.
In WEF’s analysis, oil and cellulosic crops meeting strict sustainability criteria to avoid competition with food or land-use change could provide another 62 billion gal. in SAF production potential by 2050—enough to ensure aviation could meet its needs. PtL fuels, meanwhile, have theoretically unlimited production potential, but will have to compete with other users for access to renewable energy.
Who Is Buying SAF?
So far, a handful of airlines and fuel suppliers have played a key role in advancing SAF. These include United Airlines, which placed the first long-term offtake contract for SAF, with World Energy, and began taking delivery of HEFA fuel in 2016 for regular flights from Los Angeles International Airport.
Other airlines have followed suit. Fulcrum’s Reno plant is anchored by offtake agreements from United, Cathay Pacific Airways and aviation fuel supplier World Fuel Services. SAF produced at Red Rock’s Lakeview plant will go to FedEx Express, Southwest Airlines and Shell.
As it scales up capacity, early producer Neste has secured a growing list of customers for its HEFA SAF, including All Nippon Airlines (ANA), Finnair, KLM, several US airlines operating from San Francisco International Airport, and aviation fuel suppliers Air bp, Avfuel and Shell.
With the kickoff of ICAO’s CORSIA carbon offsetting scheme for international flights and the ability to use SAF to reduce an airline’s offsetting obligation, there has been an uptick in agreements. Delta in 2019 signed a 10 million gal./year contract with Gevo, with deliveries to begin by 2023. Delta has also signed a conditional offtake agreement with Northwest Advanced Bio-Fuels, which plans to build a wood-waste-to-fuel plant in Washington state.
After plans to build an MSW-to-SAF plant in London fell through for lack of financing, British Airways (BA) partnered with Velocys on the Altalto project to build a 13 million gal./year MWS-to-SAF plant in Immingham, England. The partners are still seeking financing for the plant, planned to come online after 2025.
In March, BA extended for another year its option for equal equity ownership of Altalto Immingham. But the UK airline has also invested in LanzaJet’s Soperton plant, along with ANA, in a deal that includes a fuel offtake agreement and a study of the potential to build an alcohol-to-jet plant in the UK.
Across the industry, the number of offtake and investment agreements is slowly but steadily growing. These range from Gevo selling SAF to Scandinavian Airlines (SAS), to United taking another pioneering step by making a multimillion-dollar investment in 1PointFive, a startup that plans to capture and permanently sequester atmospheric CO2. United CEO Scott Kirby describes carbon capture and sequestration as the ultimate offset for aviation emissions because it will permanently remove the CO2 that aircraft will emit.
What Needs To Be Done?
As the urgency behind scaling up SAF production intensifies, airlines and other aviation stakeholders are calling on governments to put in place policies and incentives that will encourage feedstock and fuel producers, airlines and other operators to make long-term commitments and investments.
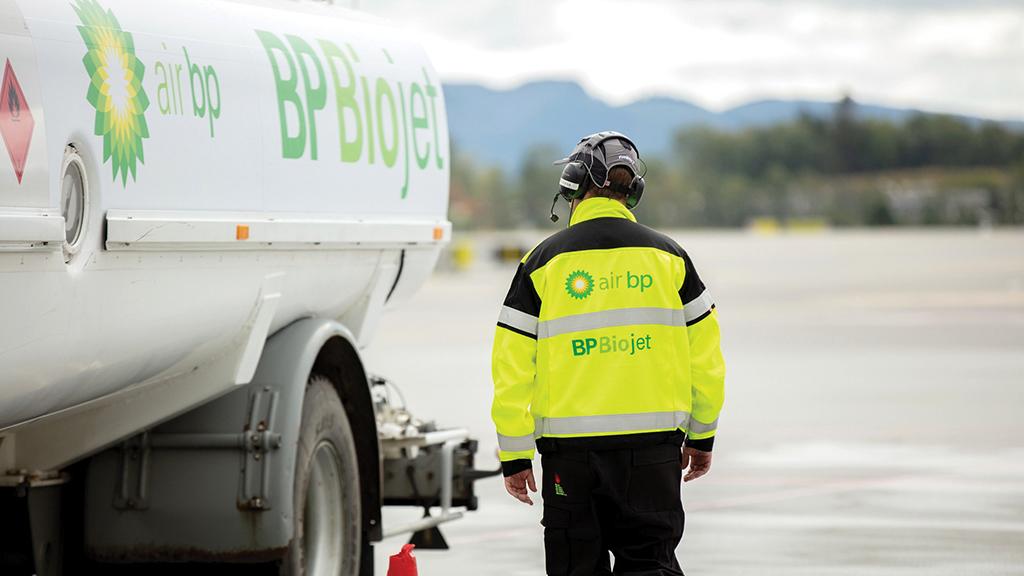
In the US, A4A is pushing for a $2 per gal. SAF blender’s tax credit (BTC) to incentivize production. This is because SAF plants can also produce green diesel, and with higher margins because of the less-stringent requirements. So even where capacity is available it will be directed toward more-profitable ground transportation fuel unless there is an incentive, in the form of a BTC, for blenders to produce SAF.
In Europe, the impending ReFuelEU Aviation legislation is expected to propose a blending mandate to stimulate growth in SAF availability. Already being introduced in Scandinavia, the mandate would stipulate percentages of SAF to be blended with conventional jet fuel that would increase over time.
Reports suggest the proposed European Union (EU) mandate would start at 2% in 2025, increasing to 5% in 2030, 20% in 2035, 32% in 2040 and 63% in 2050. A sub-mandate for Europe’s favored carbon-neutral PtL e-fuels would begin at 0.7% in 2030 and increase to 25% by 2050, the unconfirmed reports suggest.
The proposal for a mandate has the potential to divide the aviation industry even as it comes together to lobby for government action to support the scaling up of SAF. In the US, A4A argues it is too early for a blending mandate because there are still too few SAF producers. In the EU, LCCs are urging that SAF quotas are applied to long-haul international as well as short-haul domestic European flights.
Where the Ancient Mariner saw “water, water everywhere, nor any drop to drink,” the aviation industry can at least see the first tantalizing trickles of sustainable aviation fuel. But to turn the tap and increase that flow will take coordinated action this year by airlines, governments and other stakeholders to avoid being blown into the doldrums.
Comments
This would provide a growing market for producers and would avoid the problem of "free riders" in the airline industry who will currently benefit from lower fuel costs by using conventional fuels. It would also provide an incentive for airlines to convert to SAF in short order.