Sustainable Alternatives For Aircraft Handling Tackle Adoption Hurdles
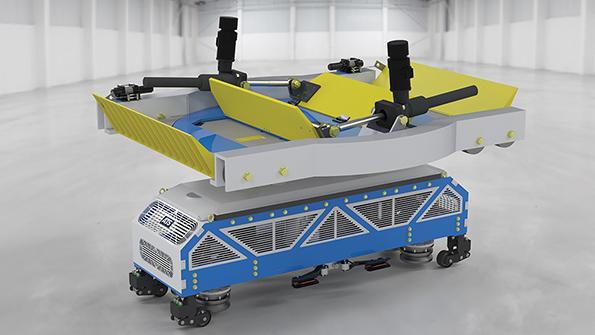
Late in 2020, ground handler Dnata completed the first “green” aircraft turnaround in the U.S., servicing a Viva-Aerobus Airbus A320 at New York’s John F. Kennedy International Airport using only zero-emissions ground support equipment.
- Electric and autonomous tow vehicles could improve efficiency
- Other options range from electric taxiing to rail-based towing
The milestone emphasizes that efforts to improve the sustainability of aviation extend to the ground. In addition to all-electric ramp equipment, trials are underway of technologies that range from electric taxiing to autonomous tugs designed to save time and fuel when handling aircraft on the ground. But changing age-old practices is not easy, and all these technologies face challenges with adoption.
The JFK trial took place in November. The exercise involved turning around the A320 using electric baggage tractors and conveyor belts to offload then load the aircraft. A Mototok remote-controlled electric pushback tractor was then used to position the aircraft for taxi and departure.
In September, meanwhile, WheelTug conducted the first demonstration of its preproduction electric taxiing system on an AlbaStar Boeing 737NG at Memphis International Airport. The system, comprising a modified nosegear incorporating an electric motor powered by the aircraft’s auxiliary power unit, is planned for supplemental type certification by the end of 2021.
And in August, Amsterdam Schipol Airport completed a five-month trial of TaxiBot’s semi-robotic towing tractor that assessed how the system could help reduce emissions and improve operations. Data from these tests have been used to simulate the effect of multiple TaxiBots operating at Schipol as part of a feasibility study completed at the end of 2020.
And these are not the only options. Startup Aircraft Towing Systems World Wide (ATS) is developing a towing system that would be built into the taxiways and ramps of airports to move aircraft between gate and runway under electric power. A prototype is taking shape at Ardmore Industrial Airpark in Oklahoma, and testing is planned to begin in March.
Another startup, Moonware, is developing a family of electric-powered tow tugs capable of navigating autonomously between predetermined waypoints provided by air traffic control, receiving dynamic route updates via cloud network. The initial use is towing general-aviation and business aircraft as well as urban air mobility vehicles, scaling later to airliners.
While the developers of these different approaches claim substantial time and fuel savings over established ground-handling procedures, to sell their systems they must navigate a complex web of interrelationships between manufacturers, airlines and airports, as well as air traffic control providers and aviation regulators, to secure adoption of their solutions.
Moonware and TaxiBot are sticking with the practice of towing aircraft using ground vehicles, but they augment the approach by bringing in automation or electrification or both, to make the process more efficient and sustainable. ATS and WheelTug are seeking, in different ways, to change the established procedure significantly. That brings complexities into the equation of who pays and who benefits.
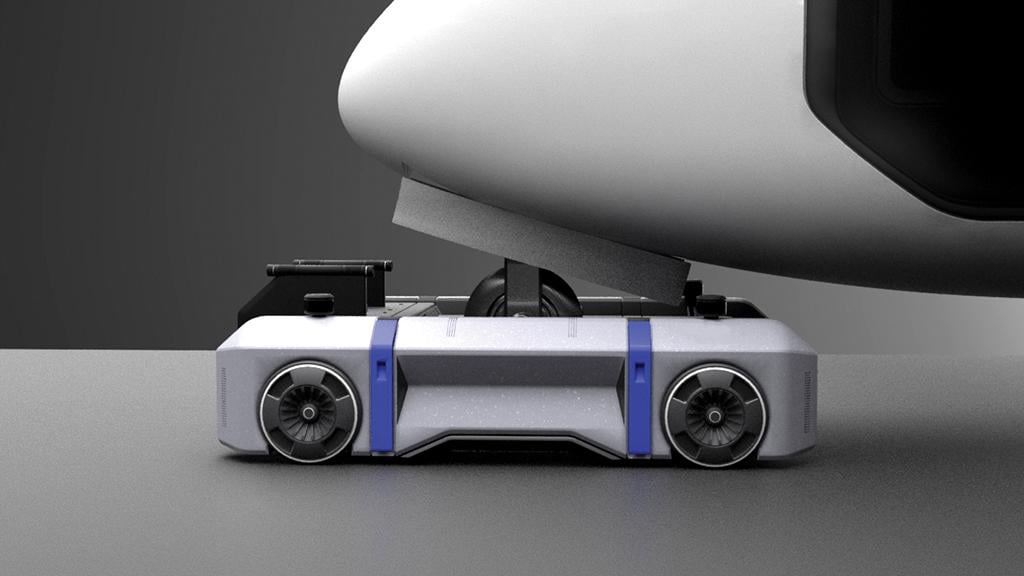
“Typically, the airlines own and operate the tug equipment, but they can request airports pay for the equipment to entice them to use the airport. It is kind of an unwritten practice,” says ATS CEO Vince Howie. “Normally, some airports have backup equipment. But it depends on the arrangement between the airline and airport. The FAA does not certify or purchase tug equipment, but it must meet the aircraft manufacturers’ specs.”
The system being developed by Edmond, Oklahoma-based ATS comprises a below-ground channel that houses an electric-powered pull car. This connects to an above-ground turntable called the tow dolly. The aircraft’s nosegear is taxied onto the tow dolly, the wheels chocked and engines shut down. The pull car below the pavement then tows the aircraft along a track. The pilot maintains control of the aircraft and can disconnect from the dolly using brakes.
While the system would be expensive to install at airports, potential benefits of the ATS concept include fuel savings, emissions reductions, improved air quality and reduced noise from taxiing with the engines shut down, as well as increased engine life and higher airport throughput.
The pull car houses a 200-hp electric car motor, which powers two hydraulic pumps driving four hydraulic motors. These hydraulic drives grip a monorail that the pull car rides along while moving through its channel. The electric motor is powered via conductor rails.
The tow track, a concrete channel under the taxiway, is covered with steel plates that can be lifted for maintenance access. The 1.75-in.-wide gap between the plates is protected by brushes to keep out dirt. The channel has drainage and can be heated.
The Ardmore test site will have a 358-ft.-long channel and a prototype pull car built by Production Machine & Tool. ATS expects to begin testing by March, towing an engineless Boeing 727 acquired at auction. The ex--freighter can be ballasted with water to simulate aircraft of different weights.
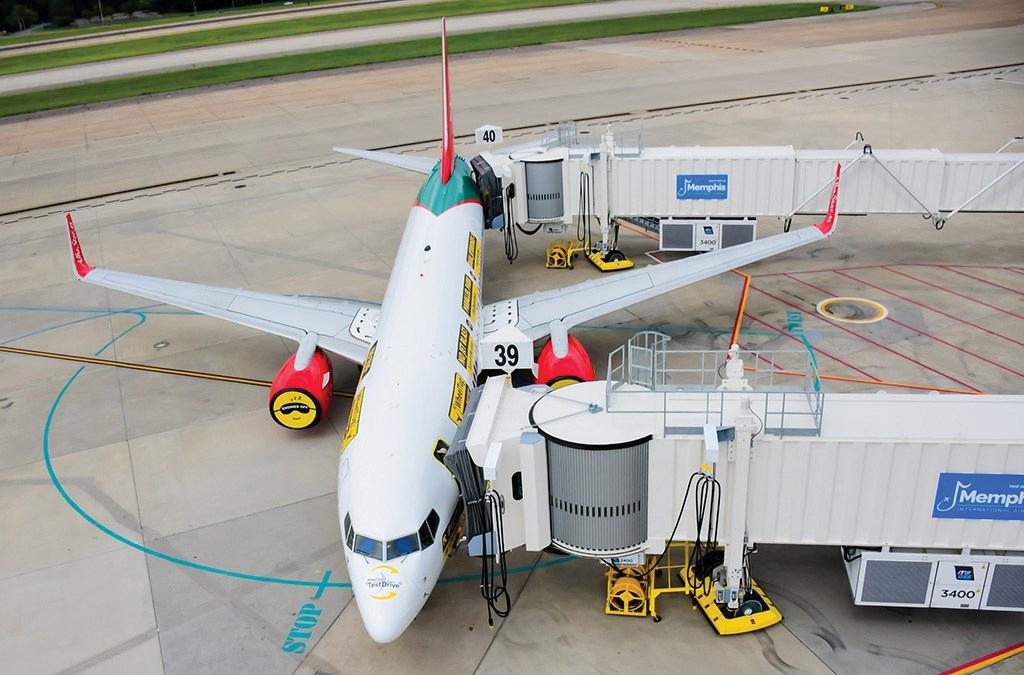
The prototype has been designed to demonstrate the system’s ability to tow airliners weighing up to 1 million lb. Howie says ATS wanted to bring in an Airbus A380 for the demo, but the company is now hoping American Airlines will provide a Boeing 787.
The Ardmore test channel will be 2 m deep by 2 m wide (6.6 X 6.6 ft.) to accommodate the prototype pull car with its 24-in.-dia. electric motor. The production system will use two 12-in.-dia. BorgWarner motors to reduce the size of the pull car. ATS’ goal is a 1 X 1-m channel to minimize installation costs.
Howie acknowledges the full runway-to-gate system will be expensive to install at a major airport. A benefits analysis conducted for ATS by architectural consultants Jviation estimates the cost at $950 per linear foot, putting the construction cost at $240 million for Chicago O’Hare International Airport and almost $255 million for Dallas-Fort Worth International Airport.
On the benefit side, Jviation identified avoidable annual taxi fuel costs of almost $72 million at Dallas-Forth Worth and $105 million at O’Hare. The study suggests installation costs could be borne by a public/private partnership including the airlines, airport, local government or the FAA. The return on investment would come from a per-use fee for airlines of about half the per-taxi fuel cost saving.
Cost will depend on the size of the channel, and ATS is planning three sizes, for regional jets, narrowbodies and widebodies, respectively. “Not all airports have A380s,” Howie says. “The pull car is designed to tow 80% of aircraft by weight, and we can couple two together like a train for heavier aircraft.”
ATS also sees a market for a smaller system that would only be used to push aircraft back from the gate, replacing diesel tugs. “We’ve targeted 34 airports, major hubs, for the entire system, but there are over 200 candidates for just pushback,” he says. ATS says it has received expressions of interest from several major airports across the U.S. and Europe including London Heathrow.
“We have always touted this as a modular system, and smaller airports have asked if we can just do pushback,” Howie says. “The [Environmental Protection Agency (EPA)] is after them over fuel spills and emissions. There are a couple of airports in the U.S. where EPA savings far outweigh any costs.”
While the full system is intended to be automated and operated centrally by the airport tower ground controller—the tow dolly is equipped with sensors to detect any local obstacles—the pushback-only version is designed to be remotely controlled by a ground marshal at the gate.
A pushback-only system would be 300 ft. long, reducing installation cost, and built with a specific curve designed to ensure the aircraft is turned in the same direction every time. This will be demonstrated using a curved section of the Ardmore test track. “We think we can take the pushback section alone to market soon, possibly [in 2021], and the entire system in another year,” Howie says.
San Francisco-based Moonware, meanwhile, has been formed by a team with experience in self-driving vehicle development at Aptiv, Tesla and Uber. At the core of its product offering is cloud-based software that uses machine learning and sensor fusion to integrate real-time position and status data from autonomous vehicles to enable dynamic, optimized routing.
“Moonware is developing a software platform that delivers real-time fleet situational awareness and vehicle routing for ground-handling vehicles,” says co-founder and CEO Javier Vidal. “Ground crew, pilots and ramp managers are all able to visualize airside movements and the state transitions of the vehicles.” This fleet management software can be integrated with existing ground service vehicles.
The startup’s electric tow tugs will be capable of navigating autonomously between predetermined waypoints designated by airport traffic control, such as gates, taxiways and runways. The cloud-based traffic management network will provide over-the-air updates to dynamically change the vehicle’s route, to tow a new aircraft, avoid a potential hazard or recharge its batteries.
“Our software platform runs on a core optimizer that dispatches vehicles to service gates/aircraft, taking into account the multiple variables surrounding an airfield’s flight throughput requirements,” he says. “The autonomous vehicle is capable of classifying and mapping its local environment to perform dynamic path planning and obstacle detection to avoid potential accidents such as wing strikes.”
The vehicles are fully autonomous, with multiple lidar sensors for obstacle detection and the option for remote override in the event of an emergency. “Our interim step will be to commence with autonomous operations in nonmovement areas of an airfield, such as gates and ramps, performing pushback and marshaling, and slowly extend to movement areas such as taxiways to perform taxiing,” Vidal says.
Moonware’s first vehicle, which could be ready for service by 2023, is designed to tow smaller aircraft up to weights exceeding 10,000 lb., including air taxis on vertiports. “We are developing a scaled-up version that can tow commercial aircraft exceeding 600,000 lb.,” Vidal says. Compared to diesel-powered, manually driven tugs, the vehicles “are cheaper and safer and can save airlines and airports more than 50% in operating costs,” he adds.
ATS and Moonware are entering a market that so far has been slow to adopt new technology. Originally developed by Israel Aerospace Industries, the TaxiBot was first approved for airport towing in 2014 but is in regular use only at two airports in India. The system is controlled by the pilot as it tows the aircraft to the runway and requires a driver onboard for the return trip. The developers are now looking at making the vehicle fully electric and autonomous, to eliminate emissions and reduce costs.
WheelTug has been developing its electric taxiing system since the mid-2000s. Over time, its marketing has focused on the on-ground time savings made possible by using in-wheel electric taxiing versus towing by a ground vehicle. “The total ground-time savings are worth far more than the fuel savings. The 2,200-plus aircraft reserved were signed up for that reason,” says CEO Isaiah Cox. “The driver for the business model is [that] time is worth considerably more than fuel.”
The Memphis demo showcased two time-saving maneuvers enabled by the electric taxiing system. The WheelTug “twirl” cuts pushback delays by allowing the aircraft to turn at the gate using nosewheel power. The “twist” speeds the turnaround by enabling the aircraft to maneuver engines-off to park parallel with the terminal and allow boarding via both doors.
Although faced with lack of interest from the aircraft manufacturers, WheelTug has accumulated slot reservations from more than 25 airlines for both 737s and A320s. “Airlines are increasingly supportive of electric taxiing, and it benefits older aircraft more than new ones,” says Cox. This may indicate growing interest in sustainability solutions that go beyond the efficiency improvements that come with each new generation of aircraft.