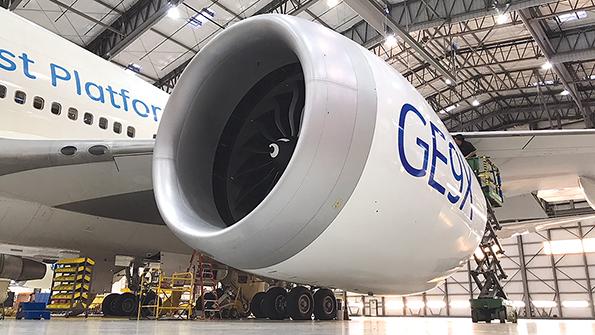
Providing graphic proof of aviation’s never-ending drive for higher bypass ratios and greater propulsive efficiency, General Electric’s gargantuan GE9X, the largest turbofan ever to fly, is poised to return to the skies in November for a final evaluation campaign on the company’s Boeing 747-400...
Subscription Required
This content requires a subscription to one of the Aviation Week Intelligence Network (AWIN) bundles.
Schedule a demo today to find out how you can access this content and similar content related to your area of the global aviation industry.
Already an AWIN subscriber? Login
Did you know? Aviation Week has won top honors multiple times in the Jesse H. Neal National Business Journalism Awards, the business-to-business media equivalent of the Pulitzer Prizes.