Middle East Market Seeks Remedy To MRO Capacity And Labor Challenges
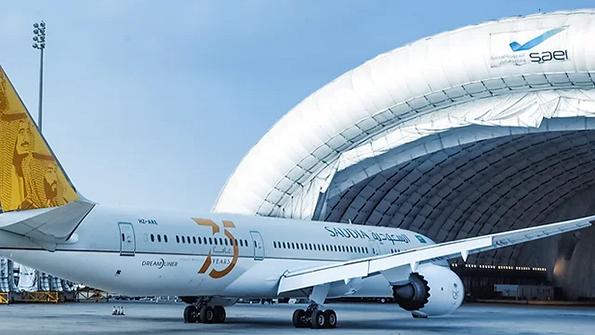
Saudia’s MRO business is looking to enhance its component maintenance repair capability.
Aftermarket Capacity and Capability Boosts Sought
MRO providers are looking to add capacity in the Middle East to meet aftermarket demand increases following a sizable passenger traffic increase in 2022. The region’s capabilities, particularly in component and engine repairs, remain underserved.
Etihad Airways Engineering plans to grow capacity at its Abu Dhabi maintenance facility to about 540,000 ft.2. It is set to build three new widebody bays dedicated to Boeing 777-300ER passenger-to-freighter(P2F) conversions in partnership with Israel Aerospace Industries, with which it signed an agreement for the P2F services in 2021.
Another company aiming to expand its capacity in the region is Amman, Jordan-based maintenance provider Joramco. The MRO outlined plans to increase its presence in Jordan’s capital, with the potential to construct two new hangars. The first will conduct line maintenance with capacity for P2F conversion services and a large volume able to handle one Airbus A380 or four narrowbody aircraft. Joramco estimates that the hangar will be operational by the third quarter. A second proposed hangar is planned to focus on aircraft painting services, with volume for one Boeing 777 aircraft or two narrowbody aircraft.
Both Etihad and Joramco entered newly announced partnerships, continuing the trend of Middle East-based companies teaming up with OEMs to add regional capability. Etihad Airways Engineering’s facilities are to become the new base for Collins Aerospace’s Nacelle Systems MRO business, located in Dubai’s Jebel Ali Free Zone.
Driven by a desire to relocate the shop to a customer facility, the move is to be completed by year-end, with all staff set to move to Etihad’s Abu Dhabi facility. In another capability addition, Etihad announced it would become an authorized service center for manufacturer Acme to grow its own specialties in battery and avionic instruments repair and overhaul.
Meanwhile, Joramco joined the aftermarket repair network of Spirit AeroSystems. Following an initial memorandum of understanding signed last year, Joramco will become an authorized service center for Spirit, initially to conduct nacelle repair services for V2500, CFM56-5B and CFM56-7B engines. Eventually, both parties expect to expand the capabilities to other platforms, including Boeing 777 aerostructures.
Other notable partnerships announced at Aviation Week’s MRO Middle East in March include a major cross-regional collaboration. Saudia Aerospace Engineering Industries (SAEI), set to play a key role in Saudi Arabia’s ambitious aviation industry plans, signed an agreement related to component repair services with German MRO giant Lufthansa Technik.
The agreement will see Lufthansa Technik provide its total component support package to the fleet of SAEI airline affiliate Saudia’s 57 777 and 787 aircraft. The contract covers 39 777s and 18 787s, for which SAEI will gain 24/7 access to Lufthansa Technik’s components pool. The MRO is to also support SAEI’s ramp-up of its in-house component capabilities, including the digitalization of MRO processes and associated supply chains.
Constrained Labor Markets
Addressing supply chain-related issues such as labor shortfalls is expected to be among the key challenges in the region over the mid- to long-term.
The Middle East has felt the negative impacts of these challenges, with the welcome rise in passenger traffic last year and resulting MRO activity hampered by a lack of readiness to meet the ramp-ups.
David Doherty, Etihad Engineering’s acting vice president for commercial, said that despite employing more than 2,000 people, the company has not been immune to the global shortage of engineers and mechanics.
He identifies access to skilled labor outside of the Gulf region as the business’ primary challenge. “We have a finite pool of labor available in the Gulf Cooperation Council [(GCC)] and most of that labor comes from countries outside of the GCC, and therefore some of our airline colleagues and competitors are also drawing from that same pool,” Doherty told a panel at MRO Middle East.
This has led to Etihad reviewing its training functions beyond the typical Part 147 training. “We need to make sure that as well as benefiting from the market, we’re not consuming more labor without adding to it,” Doherty said.
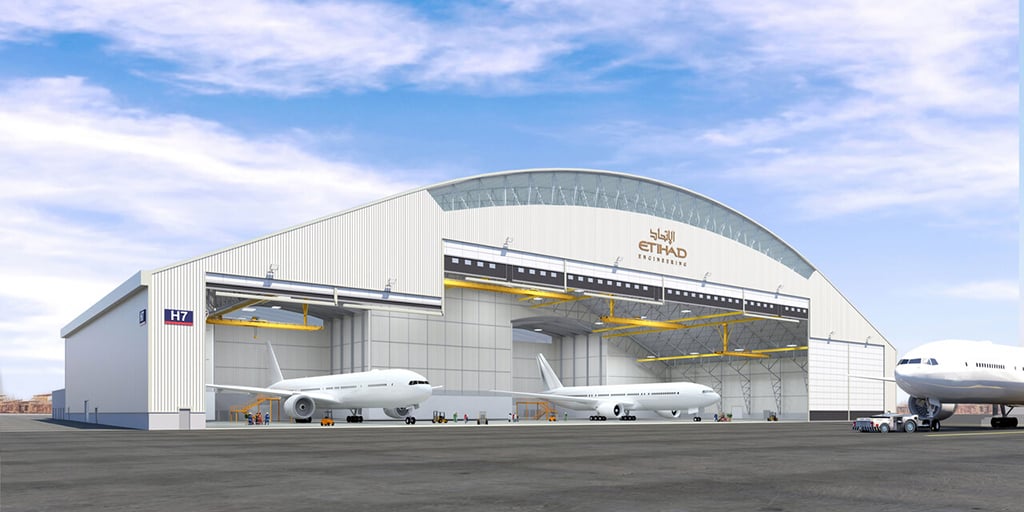
The company specializes in heavy maintenance and component overhaul services, with an estimated 70/30% split between third-party and Etihad Airways-related work, respectively. Doherty said the company is considering several strategic joint ventures, with announcements expected shortly, while also adding to capacity with three new hangars being built in Abu Dhabi this year.
Recruiting for these new facilities through attractive financial offers will benefit the company in the short term. Longer-term solutions such as apprenticeship schemes and upskilling existing mechanical labor are also potential remedies. Doherty estimated that in the next year alone, Etihad will need an extra 300-350 mechanics to aid its growth aspirations.
Derk Nieuwenhuijze, head of strategy, marketing and communications at Air France-KLM, speaking at MRO Middle East, noted the overall challenges presented by the MRO supply chain and ways these have affected the company. He said Air France-KLM, which employs around 12,000 workers across the group, is exploring ways to get people into its global network of maintenance shops and has faith in traditional methods, such as apprenticeship programs, to accomplish this.
However, the nature of disrupted supply chains means the company is not looking at workforce numbers alone. “When tackling these supply chain crunches, we’ve not only thought about bringing more people in, but ultimately thinking about how we can make the people that we have more productive,” he said.
Nieuwenhuijze said the airline group’s MRO business has looked to utilize more automation and invest in standardizing visual inspection methods to save time on manual inspection tasks carried out by technicians. “We use a lot of artificial intelligence and image recognition tools, but also make sure these programs can really work with people and help them be more productive,” he said.
MROs and OEMs Plan Sustainability Initiatives
As the industry continues to grapple with the effects of climate change and aims at sustainability targets, the Middle East’s MRO players are considering how to implement sustainability initiatives across their business and the wider industry. During a panel on sustainability at MRO Middle East, panelists offered insights into the different approaches taken by OEMs and MROs to support the sustainability targets.
Loay Al-Maddah, facilities director at SAEI, pointed to climate change as the biggest challenge faced by the MRO division of flag carrier Saudia Airlines. He highlighted that, in order to reduce its environmental footprint, SAEI is building a renewable energy plant at its new MRO village and intends to use electric ground equipment to lessen its dependence on fossil fuels.
Al-Maddah also emphasized the need for aircraft manufacturers to look for weight optimization by using lighter materials and even designing aircraft with less friction. “At the new MRO village, we are installing solar panels and are trying to limit printouts by signing letters digitally,” he said.. “We are using recyclable materials within the facilities and utilizing equipment that can save energy,” he said.
“We have also set up a recycling program for all types of waste, [including] regular waste, fuel oil and food waste,” he added. “We are planning to have [sustainability] representatives who will monitor and take care of [CO2 emissions].”
Gregoire Desmasures, head of upgrade marketing and sustainability solutions at Airbus, said at the conference that the OEM is committed to reducing its industrial emissions by 63% by 2050 to align with the industry’s goal of net zero emissions at that point.
To achieve this, Airbus has set out several pillars. The first is advancing technologies with new-generation aircraft, which Desmasures said emit 25% less CO2 than previous-generation aircraft. Another is optimizing flight operations with initiatives such as Descent Profile Optimization to reduce fuel consumption. Additionally, he noted that Airbus is aiming to reach 100% renewable energy in all its European facilities by 2024.
Desmasures mentions that Airbus is collaborating with its customers to define and implement their road maps. “We are also collaborating with some research and development programs around aircraft management,” he says. “We have partnered with [the Single European Sky Air Traffic Management Research program], a European initiative, to modernize the air traffic management system.”
Furthermore, he points out that Airbus and Tarmac Aerosave have collaborated to develop a proven method for decommissioning, dismantling and recycling Airbus aircraft in an environmentally responsible way.
“We are able to recycle 92% of an aircraft’s total weight, and where there are parts that we cannot recycle, we try to dispose of [them] safely,” he adds.