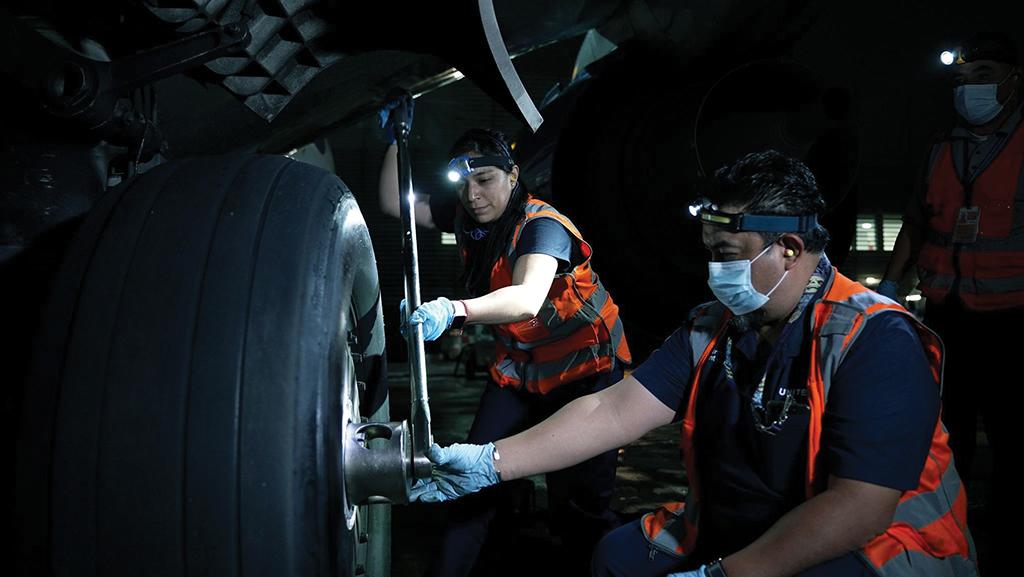
United recently launched its Calibrate apprenticeship program to help increase its staff. The airline hopes to hire up to 7,000 technicians over the next four years.
Industry forecasts all stress the growing need for aviation maintenance technicians, and if headcount goals at airlines and MROs are any indication, these positions could become increasingly harder to fill. However, as companies seek to connect with younger generations and recruit them to the MRO industry, some employers are finding that new graduates from airframe and powerplant schools are lacking in crucial skills.
At the Aviation Technician Education Council’s (ATEC) recent annual conference, many companies were actively looking to recruit new aviation maintenance technicians (AMT). AAR Corp. is trying to fill 250 technician positions across its 10 MRO sites, and it will need about 1,000 new technicians over the next five years. Republic Airways expects to need around 2,000 certificated AMTs over the next decade. And United Airlines, which is set to take delivery of some 700 new aircraft by the end of 2032, will have sky-rocketing workforce needs due to its growing fleet.
“What that means for us is a lot of technicians,” says Rodney Luetzen, vice president of line maintenance at United Airlines. “We’re on pace to hire about 175 technicians a month and up to 7,000 technicians over the next four years.”
One way United is trying to fill these positions is through its recently launched Calibrate program, a three-year apprenticeship pathway through which participants receive technician pay and benefits while training to earn airframe and powerplant (A&P) certification. The program is offered internally to International Brotherhood of Teamsters-represented employees through its first apprenticeship class offered in Houston, although the airline hopes to open this up to more locations and external candidates eventually.
“Ironically, as we offer these positions, the average seniority for apprentices is about 10-25 years, so we’re getting people that are toolroom mechanics, [ground support equipment] mechanics and facility mechanics that want that A&P,” Luetzen says.
The airline also hopes to improve the diversity of its workforce. “We’re pretty weak when it comes to female technicians,” Luetzen says, noting that women comprise only about 3% of its technician workforce. “We definitely want to grow that. We have aspirations of 10% female technicians, and we are aggressively recruiting and trying to retain our female technicians,” he adds.
Other companies highlighted the various ways in which the industry is trying to recruit and retain workforce. Efforts range from internship and apprenticeship programs such as Calibrate to partnerships with schools, youth outreach initiatives and nonprofit Choose Aerospace’s growing program to bring Part 147 curricula to high schools.
Ryan Goertzen, president of Choose Aerospace and vice president of workforce development at AAR, says the nonprofit enrolled 188 students across 16 schools during its inaugural year, 2021-22. The program has developed around 500 hr. of computer-based curriculum covering general subject areas in the FAA Mechanic Airman Certification Standards. The program’s learning management system includes various multimedia formats such as videos, digital whiteboards and virtual reality simulations to engage young students and enable interaction.
Choose Aerospace is working with ATEC to build an industry credential that would support matriculation from high school to A&P school. It also is seeking a change to the FAA’s Part 65 certification standards that would allow for early testing. Goertzen says the nonprofit’s goal is to have enrolled 10,000 students by 2027. “We have to meet this goal if we’re going to meet the demands of the industry,” Goertzen stresses.
Courting Gen Z
Several stakeholders at the conference discussed adjustments the industry will need to make to meet the shifting values of Gen Z, such as sustainability and work flexibility.
“There’s a big generational shift that’s already happening,” notes Livia Hayes, director of Oliver Wyman CAVOK. “How does the workplace continue to evolve to accommodate the things that are important to them? Gen Z is very climate conscious, and we’re in an industry that is not known for that, but there is a lot of work to be green, so how can we help them see that we are caring about the environment and that we are trying to do things in an environmentally conscious way to attract that younger talent?”
Hayes also points out the importance of showing young people various career paths within MRO. “If you don’t want to turn a wrench forever, you don’t have to—you can lead, you can manage, and you can teach. It’s about showing everybody how many opportunities there are,” she says.
Although the pandemic shifted many attitudes about remote work, this could be more difficult for the MRO industry to address. “From a carrier perspective, maintenance has to get done at certain times,” notes Justin Madden, managing director of engineering and maintenance at Airlines for America. “It has to get done outside, and you might be in a cherry picker in the middle of winter doing something on the horizontal stab. That’s not going to go away. But I think there are ways that [this can be addressed],” he adds, citing examples such as establishing child care at a company’s facilities.
At Boeing, Chief Mechanic Jennifer Radtke says remote work for more experienced technical staff is sometimes possible using augmented reality (AR) technology. For instance, a mechanic who is not certified to perform an inspection could wear an AR headset and have a remote expert follow along, witnessing the inspection virtually and collaborating from home. To compete with newer tech startups, the OEM also has begun allowing employees at some facilities to bring pets to work, and it has hired chefs to provide meals to workers on site.
Skills Shortfalls
In addition to the industry’s scramble to hire technicians, several stakeholders point out that new graduates are lacking certain skills, leading to increased training time or issues with retention.
Radtke says she thinks some A&P schools may be spending too much time focusing on new technologies instead of basics, such as safety wiring. “We still have to maintain the fleet that is currently in service, and that means please stick to basics and balance that to the importance on [new technology],” she says. “If you come out of A&P school and you don’t know how to safety wire, that’s a challenge.” Radtke notes that despite some new employees coming onboard with impressive credentials, Boeing is “spending a lot more time training them individually on basic skills before we can even get into building airplanes.”
Radtke also mentions soft skills as an area where the new technical workforce falls short, which reflects results from a recent ATEC survey in which 78.57% of respondents highlighted this area as a shortfall for entry-level candidates. She suggests A&P schools work with students on skills such as professional vernacular to help bridge this gap.
In this same vein, several companies highlighted recurring challenges with younger workforce, such as attendance issues and being respectful and inclusive toward coworkers. Brennen Horton, manager of maintenance and ground operations recruitment at Republic Airways, suggests many of these issues can be traced back to not teaching students enough critical-thinking skills.
“Critical thinking encompasses not only the soft skill shortfalls that we see, but also some of the technical skill shortfalls that we see as well,” Horton says. “How can we as employers better partner with the educators to understand and show students that every cause has an effect or every decision has a consequence?”
Simone Drakes, managing director of United’s Calibrate program, says the airline requires both soft skill and practical interviews to ensure it hires the right candidates. However, it continues to see a shortage of candidates with enough experience in basic skills or areas such as avionics, which she notes has “been a gap for many years and is getting worse as aircraft technology advances.”
While A&P schools with limited resources simply cannot teach everything in a short period of time, Drakes suggests instilling in students the importance of seeking information in documentation and manuals, which should be an ongoing process over the course of an AMT’s career. “We don’t expect you to remember this stuff. We expect you to know where to go find it,” Drakes says.