GSE Market Expects Quicker Recovery Than Other Aviation Segments
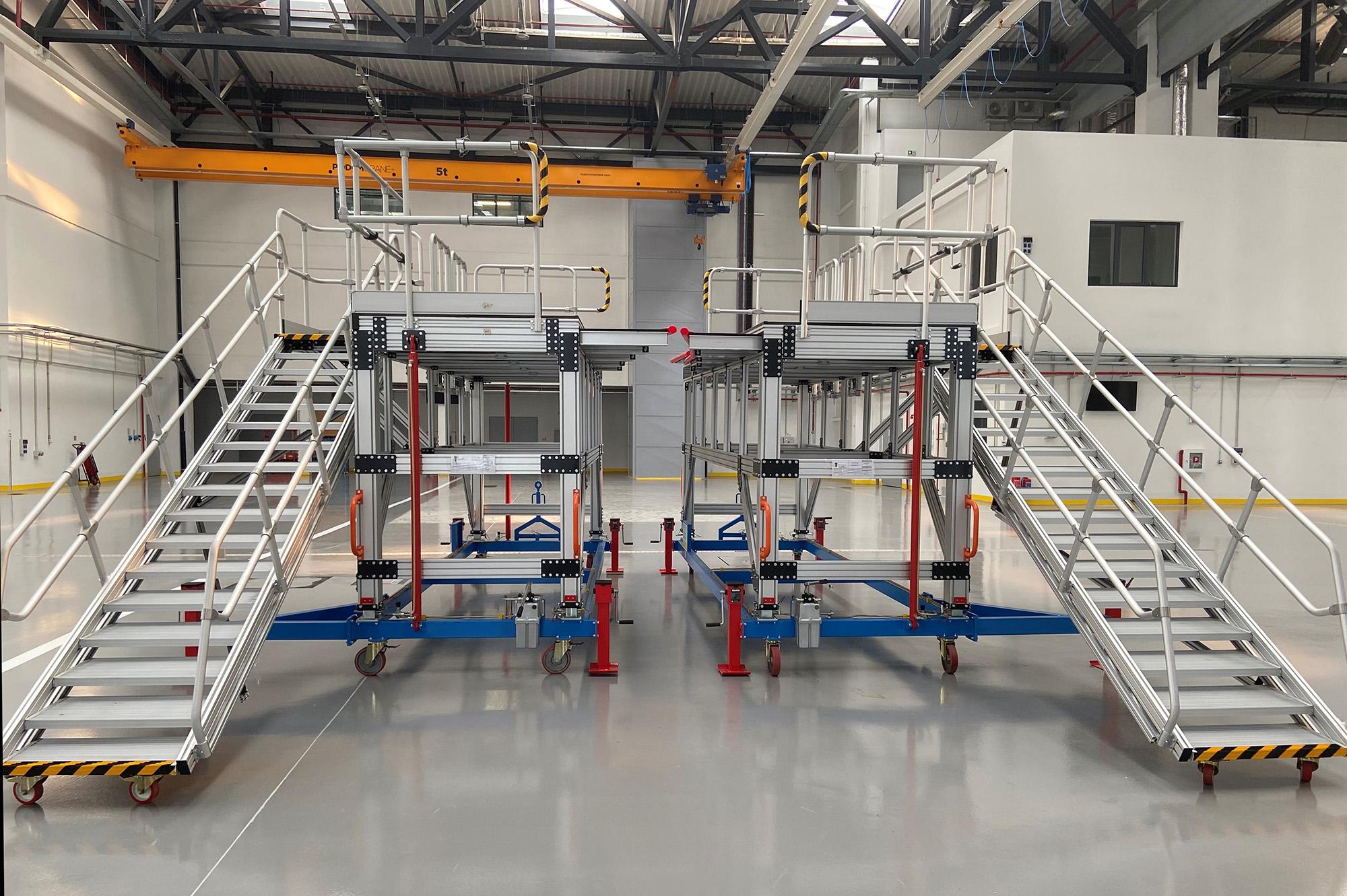
Turkish ground support equipment (GSE) specialist Makro Aero remains confident about the market’s recovery, despite the COVID-19 pandemic causing airlines and MROs to tighten their purse strings. It has continued to win contracts from major customers this year and is investing in initiatives to broaden its product portfolios.
Makro Aero recently won a contract from a large Middle Eastern airline to replace a couple hundred existing aircraft access stands in its maintenance hangars. Additionally, it has won a contract with what it says is the biggest airline in Germany for a tail docking platform and a contract with a Spanish airline for various aircraft maintenance stands for its new maintenance hangar in Spain.
In June, it delivered a nose docking platform for a customer in Bulgaria and Makro Aero says it will soon finish manufacturing a wing docking platform for this customer. The equipment, which will enable the customer to perform heavy maintenance for Airbus and Boeing narrowbodies, is part of its efforts to develop base maintenance capabilities.
Meanwhile, Makro Aero has signed a contract with TUBITAK (The Scientific and Technological Research Council of Turkey) to develop an engine positioner, which it says will improve the efficiency of engine mounting and dismounting processes during maintenance activities. It has also established a subsidiary called PORTECH in Singapore to broaden its footprint in Asia.
According to Makro Aero’s business development manager, Tanju Taskiran, the continued orders during the pandemic have given the company confidence in the industry, but it has still been an uphill battle.
“The COVID-19 pandemic hit aviation hard. We immediately experienced it from the activities of our customers,” says Taskiran. “The aviation industry is used to cyclical patterns where the demand fluctuates, but this was not something anyone would expect and thus the companies acted very conservatively for their capital expenditures. Investing in new GSE or replacing the old ones were deferred.”
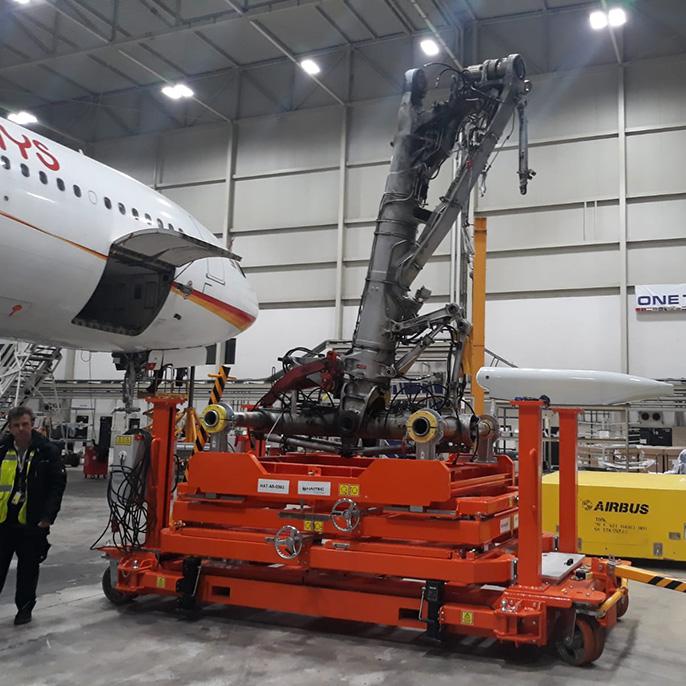
He notes that while Makro Aero did not experience any order cancellations, some prospective projects were canceled or put on hold during the early stages of the pandemic. “Right now airlines and the MRO companies are trying to adjust and almost everyone is in a consensus that it will take three to four years to reach the pre-pandemic levels in aviation. Yet we are optimistic the GSE market will bounce back slightly earlier than that,” says Taskiran, noting that he expects the GSE market to be in better shape at the end of 2022.
“We believe that once the airlines start to see more clearly, they will start investing in their equipment and will kick off their on-hold projects,” he says. “We believe the biggest challenge will be the revised aircraft orders from airlines. We strongly believe that orders for narrowbody aircrafts will be robust even if it takes some time, but the orders for widebody aircrafts may not recover as expected. This means demand for widebody aircraft GSE may shrink even further.”
Another challenge, says Taskiran, is deferred new hangar construction. Since construction itself is a large contributor in the economy, he believes governments will “not turn a blind eye to the construction industry and incentives will kick in here. On the other hand, cash infusion by the central banks will ease the financing and will reduce the cost of money,” he says. “Hopefully this will have a positive effect in investing in new equipment.”
Although many companies in the aviation industry were forced to halt operations during the pandemic, Makro Aero kept its manufacturing capabilities and capacity intact through social distancing on premises and remote work for design engineers. Online meetings were used to meet with customers abroad.
Aside from orders for GSE equipment, Makro Aero was involved in manufacturing equipment related to efforts against COVID-19. It designed a laryngoscope mounted on a stand and equipped with a camera for a hospital. It also designed and manufactured 40 machines for medical face mask earloop welding, which it says have been used to manufacture millions of masks.