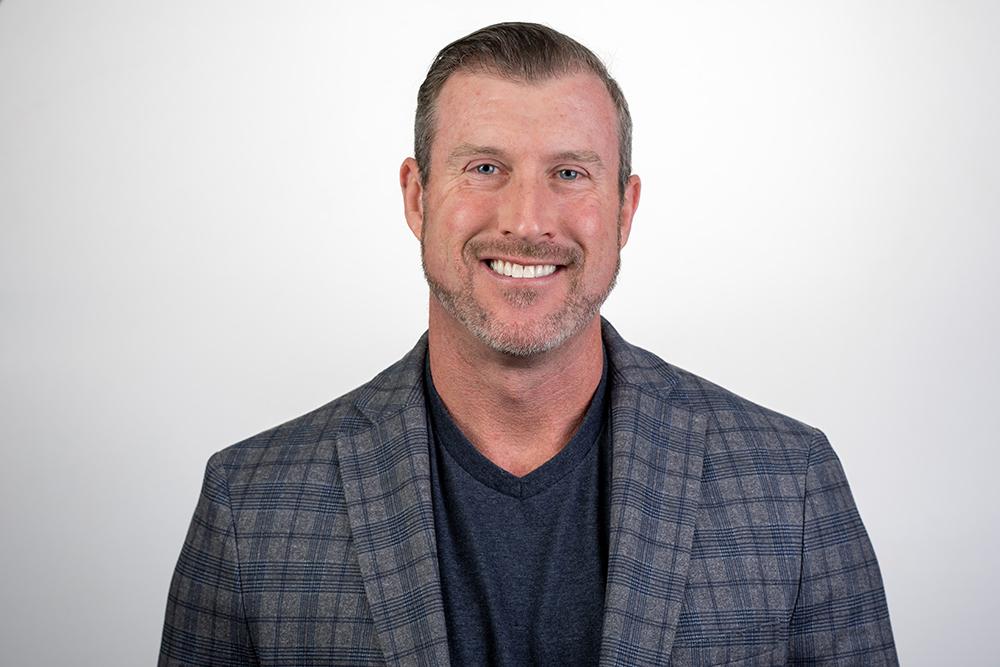
Jason Lewandowski, chief operations officer at TAT Technologies
Jason Lewandowski, chief operations officer at TAT Technologies, talks to Aviation Week Network about the unsung hero of aircraft components: heat exchangers. He also shares perspectives on OEM supplier issues, overcoming post-pandemic challenges and the increasing demand for MRO services.
What services does TAT Technologies provide in the heat exchanger component segment?
TAT Technologies has a long history in the design and manufacturing of thermal components. We operate in both the OEM and MRO space and provide end-to-end solutions starting from design, production and aftermarket services for both commercial and defense customers. We have in-house R&D capabilities, so we are on the cutting edge of aircraft environmental and cooling technology. TAT products are found on many commercial airliners and business jets currently in production, either as a direct supplier or a component supplier to the tier-one system partner of the airframer. We understand that the efficiency and reliability of these components are critical to the overall performance of the systems they support.
Why are heat exchangers so important?
Heat exchangers and the associated components in the ATA21/36 may not be the most sophisticated components in aerospace and defense systems, but their importance cannot be overstated. They are critical to ensure passengers, the aircraft and its crew are all keeping their cool during a fight. Whether to pre-cool the engine bleed-air entering the system or to control the cabin temperature itself, optimal functioning of these components is very important for safe and comfortable flight. Our Tulsa subsidiary, TAT Limco, works on restoring serviceability on a broad range of components like heat exchangers, but also condensers, reheaters, ozone converters, oil coolers, pre-coolers, etc.
As the OEM parts manufacturer, are you exposed to the ongoing supplier issues some of the OEMs are facing?
Throughout the COVID years and the war in Ukraine, we were mostly impacted by disruptions in supplies of raw and specialty material used in the manufacturing of our new cores. We’ve seen a strong recovery trend in materials availability over the last 18 months, and we expect this trend to continue. Nevertheless, longer and less reliable supplier lead times forced us to increase our inventories and work even harder with our customers on forecasting. Having two fully operational global manufacturing sites that produce the fins, plates and bars required in-house and braze them in one of our 12 operational on-premises vacuum braze furnaces helped immensely.
Restrictions on the availability of Inconel [a nickel-chromium-based superalloy], for example, caused us difficulties in producing sufficient new components for our business jet clients. Additionally, the impact of price fluctuations and limitations in freight capacity was challenging in the recovery phase from the pandemic. Our MRO activity relies to a lesser extent on OEM proprietary parts, and we have been successful in finding ways to overcome significant issues as they appeared.
How are things on the MRO side?
At the MRO end of the business, TAT Limco and the partnership with Lufthansa Technik Shenzhen in China continue to drive the industry forward with FAA designated engineering representative-approved core replacement solutions, using in-house manufactured core matrixes. This MRO activity is not limited to products manufactured by TAT Technologies. We have seen increased demand for our MRO services, both due to long repair turnaround times and also older airframes flying longer. We had to reverse plans to wind down production for aircraft such as the Boeing 747-400 and the Airbus A300 to serve our very important freight customer base.
How is TAT Technologies addressing the needs of future thermal components?
Our R&D center of excellence is pioneering in the development of compact, lightweight and robust thermal management systems for electrified and hybrid aircraft. Leveraging cutting-edge technologies, including multiphysics simulations, new materials and advanced manufacturing techniques like additive manufacturing, we want to ensure our products meet the highest standards of quality, safety and reliability. Our future product portfolio aligns with customer needs and sets new industry benchmarks.