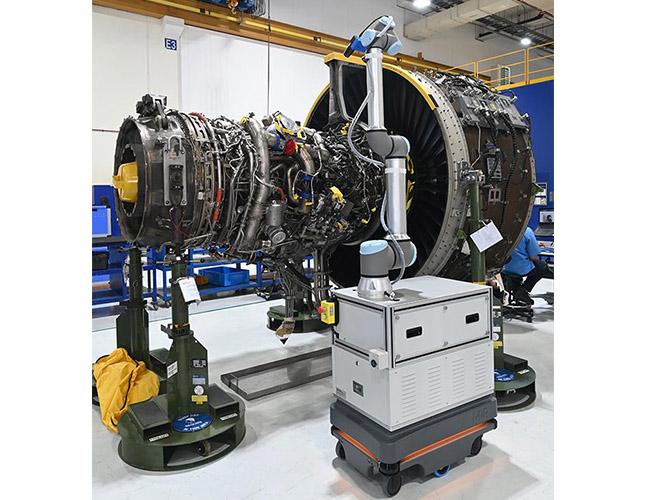
The early pivot to digitalization has helped Collins Aerospace Singapore operations remain relatively unaffected during the disruptive 2020 pandemic period. This comes as its Singapore-based Innovation Hub continues to hire more engineers with the target to develop at least 40 proofs of concept for future MRO technologies and solutions.
Rodney Hua, regional operations management director at Collins Aerospace, says the company was “ahead of the curve” and focused on non-traffic revenues, embarking on the digitalization process at an early stage. Collins introduced a digital operating system for the Singapore shop floor in 2018, which digitalizes all engine nacelle overhaul processes into a central system. All relevant stakeholders, including the management, buyers and cell lead, have a clear view from their own computer of who is working on which component, as well as the status of the overhaul.
“With the exception of the person holding the spanner, all work can be carried out off-site at home, and our business remains undisrupted during the lockdown period,” says Cheam Hing Gee, general manager aerostructures MRO, Collins Aerospace.
Collins’ non-traffic revenue includes lease returns maintenance works. Cheam says the Singapore and Tianjin MRO sites managed to meet or exceed the targets set in 2020 to account for the effects of the pandemic, and adds that Collins is “not very far behind” if factoring the pre-pandemic targets set in 2019 for 2020.
In late 2020, Collins introduced a robotic machine vision system that will automatically conduct inventory inspections for the Pratt & Whitney PW1000G Geared Turbofan (GTF) engine build-up quick engine change (QEC) kit. Known as “Spot,” the robot is a combination of high-resolution cameras, a cobot arm and an autonomous mobile robot which enables the robot to move around the GTF engine without human intervention.
Spot is able to inspect 159 different items on the QEC Kit by taking 56 standardized photos for a four-page inventory list of components in 20 min., cutting down man-hours spent by 70% compared to 15 hr. if done manually—although Collins says there are still some areas which have to be carried out manually due to blind spots and difficult angles.
Wee Chong Yaw, engineering manager, aerostructures MRO, says Spot is currently programmed for the GTF engine—the most common type on the Singapore shop floor—and could be easily programmed for other engine types, depending on demand requirements.
In parallel, the Singapore Innovation Hub is planning to hire 15 more engineers by 2022, increasing its strength to 40 engineers hired from various fields, including banking, gaming and data sciences. The lab, led by Tina Lake, is rolling out two proofs of concept that will be gradually rolled out in the next 12-18 months. These include RFID technology for parts tracking and an online customer portal, which aims to provide all customers with real-time updates of the MRO process 24/7.
Lake says the Innovation Hub and the Collins aerostructure team regularly discuss which projects to pursue, and her team usually tackles the “more futuristic” programs for which the aerostructure team lacks the resources or expertise.
According to Cheam, Collins has a digitalization roadmap that lasts until 2026, which is reviewed every six months.