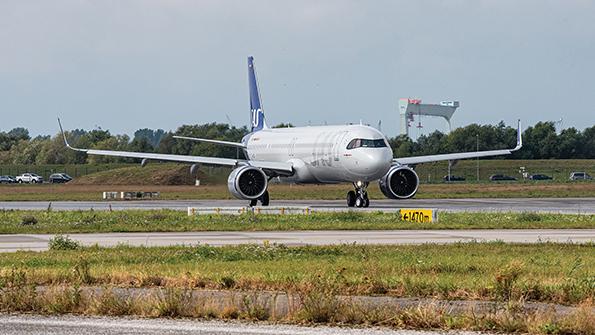
Several years ago, as part of periodic changes to the maintenance annex guidance (MAG) that underpins the Bilateral Aviation Safety Agreement (BASA) between the European Union and the U.S., Europe introduced new documentation requirements for certain parts. Specifically, new parts subject to a dual release for export from the U.S. to Europe—as are parts installed by a U.S. shop on European-registered aircraft—needed to be traceable to the relevant production approval holder (PAH). Typically, that means an 8130-3 airworthiness approval form.
For repair stations with both FAA and European Union Aviation Safety Agency (EASA) certifications, this presented a problem. While the FAA encourages PAHs to ship parts with 8130-3s, the regulations do not require it. Repair stations often ask for the forms, but they are not always included.
But repair stations’ authority to inspect and tests parts to determine whether they are airworthy presented a solution. The Aeronautical Repair Station Association (ARSA) led an effort to find it—and came up with the E100 New Article Inspection Form.
The FAA, in a September 2016 letter to ARSA, said the E100 is an acceptable means of compliance for a repair station’s parts-documentation needs and the relevant “special conditions” in the new guidance, which went into effect days later. EASA, which was consulted by ARSA during the E100 development process, took the position that while it prefers an 8130-3 from the PAH, the E100’s validity as an acceptable means of compliance is a U.S. regulatory issue.
The issue seemed settled—until recently.
ARSA has heard that some U.S.-based repair stations with EASA certificates are getting pushback from both the FAA and its European counterpart on E100 usage. In some cases, both FAA inspections and EASA representatives conducting visits to U.S. shops have been rejecting E100s.
The news prompted ARSA to write Acting FAA Administrator Billy Nolen and ask that the agency reiterate its position on E100s—one that some shops have used to refute inspectors’ objections.
“In one case, an E100 form-related finding was subsequently withdrawn after the repair station provided the [September 2016] letter and additional explanation of why the practice was appropriate” under FAA regulations, ARSA wrote in the April 7 letter.
Completing an E100 “requires a comprehensive inspection by knowledgeable maintenance personnel; it documents a process to determine if an article is traceable to a PAH and suitable for installation,” the letter explains. “Completing the form requires a thorough assessment of all aspects of the part, its packaging, records, physical condition, identifying information, conformity with manufacturer data, etc. When completed properly, the E100 form results in the safety outcome required by the U.S. and E.U. regulations—the installation of an airworthy part.”
ARSA acknowledged that getting 8130-3s from the PAH is preferable, and has long urged repair stations to request them. But absent a mandate, paperwork gaps will persist.
“It is clear EASA would prefer that the FAA Form 8130-3 originate from the PAH; however, the U.S. regulations, the [bilateral’s] special conditions and the plain language in the MAG do not require that result,” ARSA wrote. Given the FAA’s failure to enforce requirements that PAHs provide an FAA Form 8130-3 when exporting a new article to an EASA- approved repair station, the E100 form is fully in line with the U.S. aviation safety system and is necessarily in widespread use.”
ARSA also pointed out that the FAA’s job is to enforce its own regulations, preferably with consistency. Rejecting E100s fails on both counts.
“It seems that some FAA personnel are more committed to enforcing EASA preferences than the FAA regulations and the bilateral agreement’s special conditions,” the letter says. “We are also concerned that FAA personnel below the level of division manager have apparently ignored FAA policy . . . issued six years ago.”
ARSA’s specific request to Nolen is “confirmation of ARSA’s position that the E100 form is still an acceptable method of compliance with the U.S. aviation safety regulations . . . and the MAG when inspecting new parts received without an FAA Form 8130-3 from the PAH.”