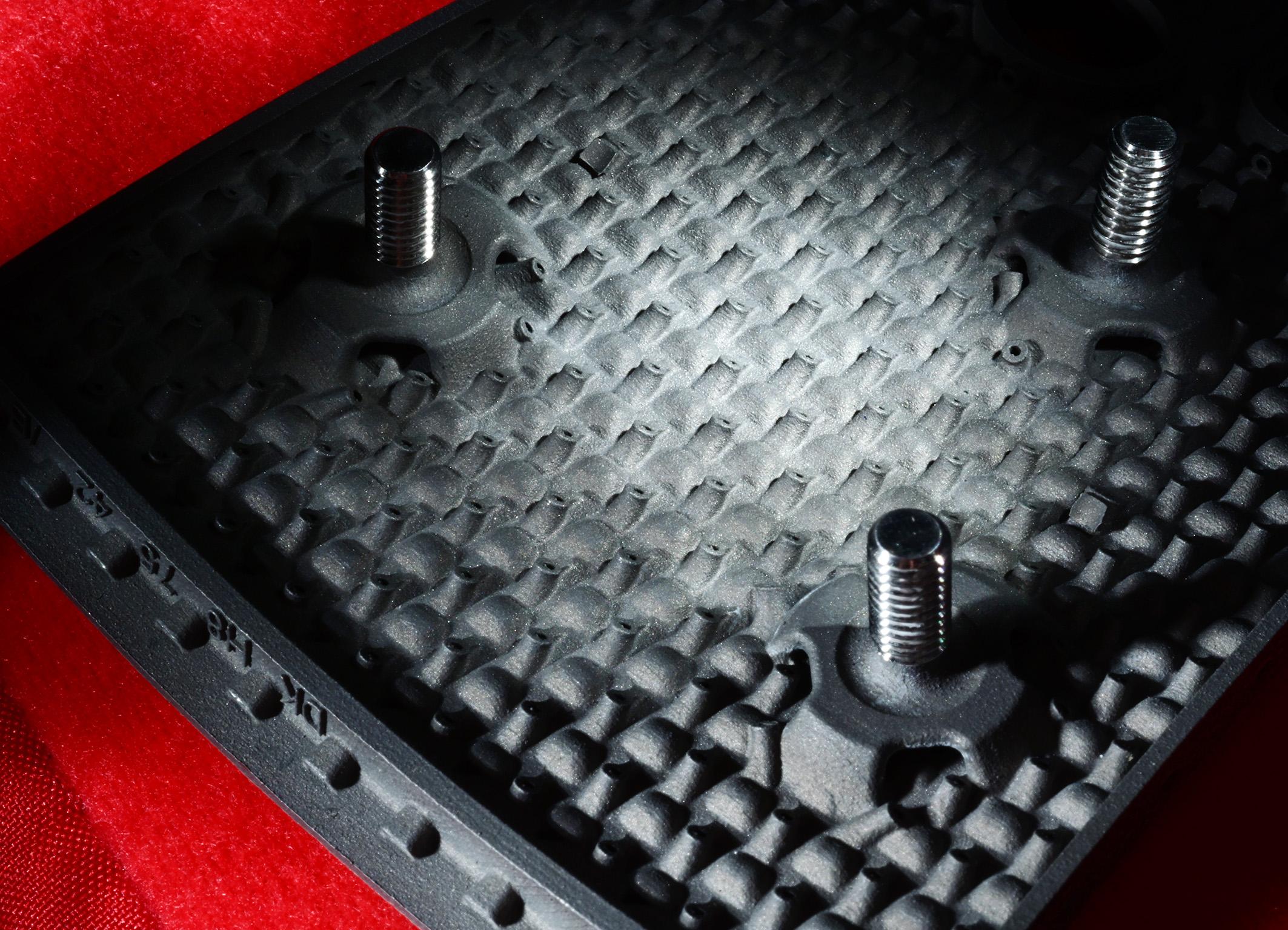
GE has looked to edge forward its additive manufacturing capabilities in the commercial aviation industry. But other engine OEMs are moving to exploit the new techniques for their new engines.
Among these is Rolls-Royce, which is working on additive manufacturing for a new business-jet engine and will look to apply its expanded additive experience to the Ultrafan or to novel electric powerplants further in the future. Pratt & Whitney is much earlier in its additive journey, but has ambitious plans.
And it is future plans that really count. For the opportunities to design new additive parts expand dramatically when clean-sheet engine concepts are considered. That may be where aviation is headed under climate pressures.
Why all the interest in additive? For Rolls, the main advantage is clear. “It creates novel geometries, and we can design parts that we could not make by other means," says Neil Mantle, director of manufacturing at Rolls’s innovation hub who led the company's additive efforts for eight years as it developed both additive repairs and new part-printing capabilities.
In 2015, Rolls used the new technique to make the largest additive structure in civil aviation, a 1.5-meter titanium front bearing housing for a demonstrator of the Trent XWB-97. “We have moved on considerably since then,” he says.
Rolls has now built a dedicated additive manufacturing facility in Rotherham, which will print combustor tiles and other parts for its new Pearl 10X engine that will power Dassault Falcons.
The combustor tiles are complexly shaped structures with multiple perforations that could not have been made without additive manufacturing. The alternative, casting plus laser drilling, would have made tiles with much less cooling ability.
Phillip Zeller, SVP of the Pearl 10X program, explains the additive tiles optimize cooling flows, thus using less air for cooling the engine and enabling more air to flow through to the combustor.
The printed tiles also control nitrogen oxide, which can come from engines hot spots, enable better control of the combustor’s outlet, protect blades and vanes and improve the turbine’s life. Overall, Zeller estimates the engine’s cooling will be 20% more efficient with the complex geometry enabled by additive.
The Pearl program has also expanded Rolls’s experience with additive, which started with electron beam melting used in XWB development and now includes laser powder bed fusion techniques used for Pearl. To increase productivity, each Rotherham machine now has four lasers which will enable four sets of tiles to be melted simultaneously. Zeller says another advantage of additive is at the program level.
Changes in design based on prototype tests can now be incorporated in the next prototype much more quickly, saving about 75% of the time required by traditional manufacturing processes.
The complexity and efficiency additive enables will be crucial as Rolls moves into new markets. “It will be important in electric flight, where power density, weight and cooling matter,” Mantle stresses. Rolls is now applying additive across its portfolio of aviation and non-aviation engines.
Rolls has worked with EASA and FAA for six years on certifying additive techniques, and now understands certain processes thoroughly. “Additive is no harder to certify than other difficult production methods on gas turbines,” Mantle notes. “You have to understand design, materials and fabrication.”
And that’s the barrier to entry for other companies that might seek to print replacement parts. They would have to obtain all the data on design, material and fabrication. Mantle says eight years ago, some worried that there would be many third parties that could additively manufacture engine components.
Today, both regulators and aftermarket companies understand the tough requirements necessary to ensure the integrity of printed parts.
In any case, Rolls is now looking forward to applying its additive skills lessons to the Ultrafan and any other future commercial jet engines.
Pratt & Whitney is working hard to catch up with GE and Rolls. The OEM is making a dedicated effort to modernize and transform its operations, in line with Raytheon Technologies’ Industry 4.0 strategy, according to additive manufacturing fellow Jesse Boyer. “Additive manufacturing is a key element of this strategy, improving performance, cutting lead times and driving efficiency,” Boyer says.
Pratt actually printed 30,000 plastic face shields to protect first responders during the pandemic, “much more than we initially thought possible in a short timeframe,” Boyer observes.
The Pratt fellow says his company’s merger with Raytheon in 2020 helps exploit synergies with its partner, including the Additive Manufacturing Process Capability Center at Raytheon Technologies’ Research Center.
The OEM’s small teams frequently use additive for prototyping, for example a single-piece static hot section, including combustor, for a small turbojet engine. “Additive manufacturing allowed the engine to develop from initial concept to test within 6-8 months, a process that usually takes 12-24 months.”
For the future, Pratt is focusing on additive advanced heat exchangers, acoustic panels, bearing supports, actuation system components and combustor components. And it is renewing an emphasis on additive repairs and production tooling. In terms of additive technologies, it is looking at powder bed fusion, directed energy deposition and binder jetting.
“We continue to develop powder bed fusion processes that result in more robust process control and process efficiency,” Boyer says. But the renewed focus on repairs and sustainment means Pratt is widening its interest to include directed energy deposition and binder jetting.
Pratt engines do not have many parts that have either the low maximum temperature, minimal fatigue or tensile requirements that would allow use of non-metallic components. Nevertheless, the OEM is monitoring the capability of newer composite-like materials that could be additively manufactured.
Boyer divides the potential of Pratt’s additive efforts into four use cases. First, additive may be used for part substitution or adaption. Here an existing part or component might be made additively because casting, forging or conventional manufacturing is encountering problems, and additive can reduce cost or lead time. There would be minimal changes in design and material.
Second, additive could be used for sustainment in the aftermarket. This is basically about replacement or repair of a fielded part. Lead times can be reduced with no design change.
Third, several parts may be combined into one additive component. Significant design and some material changes would help optimize supply chains and reduce material use, lead time and costs.
Fourth, additive could be used to optimize new part design the way GE and Rolls are doing, with a clean- sheet design for a specific engine-making purpose.