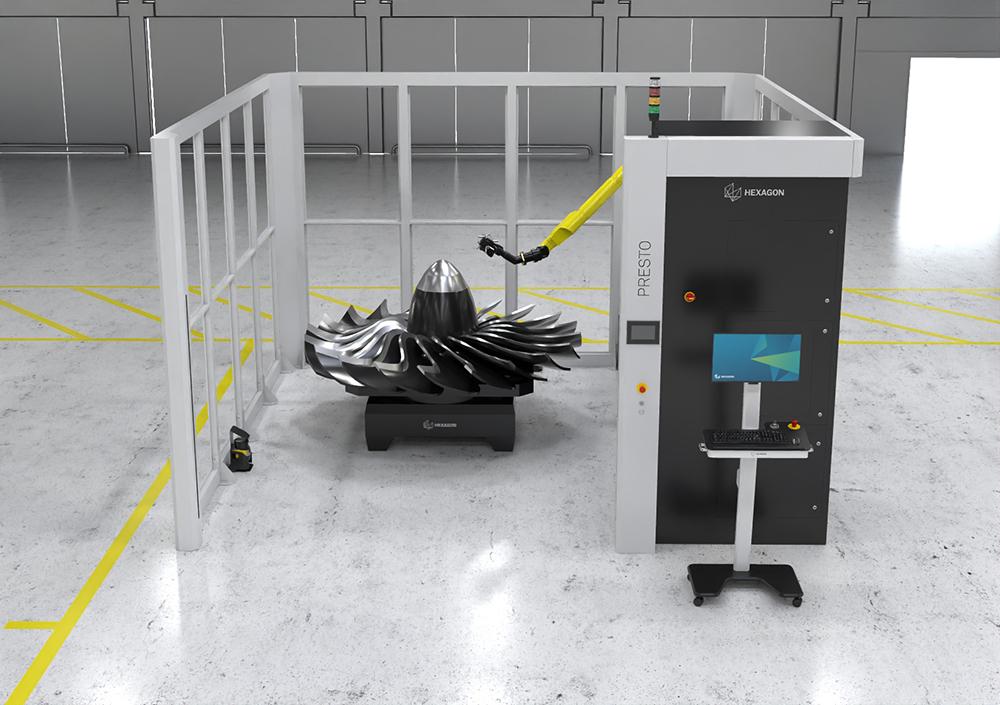
A new automated system expects to accelerate aerospace component inspections by at least 50%, claim the developers at Hexagon Manufacturing Intelligence.
The company says its Presto XL inspection cell is a non-destructive testing (NDT) system that uses lasers to examine parts without causing damage. According to Aziz Tahiri, Hexagon’s vice president for global aerospace, the technology specifically focuses on external, dimensional inspections.
Tahiri says the Presto system is ideal for “high-volume, low mix” parts, such as fuselage panels, floor panels and doors, where multiples of the same part are required in large numbers for each aircraft.
External testing traditionally involves labor-intensive manual inspection, given the large size and volume of aerospace components. Hexagon estimates that teams of 3-4 people spend around 2-3 hr. on average visually inspecting parts for defects, often using handheld, mechanical tools.
“Nowadays, rising demands and increased production are driving the industry toward automation,” Tahiri says.
Hexagon believes the key advantage of the Presto system is automation and digitalization of the inspection process using 3D laser scanning, which it says eliminates the need for multiple teams to physically handle and inspect parts. The company says this also reduces risk of injury.
“It is digitally enabled, meaning it can produce a detailed 3D model of any part, which is a much faster and more precise method of identifying defects,” explains Tahiri. “The data can then be shared for post-treatment data analysis, and this provides stable and reliable results which are more objective than existing NDT methods.”
Tahiri believes the industry has little choice but to upgrade its manufacturing processes if it wants to keep up with demand. He says Presto enables near-line inspection that can be embedded into the shop floor, allowing for inspections to be conducted in parallel without the need to pause production lines.
“It also removes the need to perform measurements under the specialized controlled conditions of metrology labs,” he says. The automated inspection cells can also be directly integrated into existing manufacturing IT infrastructure for automatic reporting, offline simulation and remote configuration. Tahiri adds: “The system supports inbound and outbound inspection, providing quality control for supplier parts and in-house components and assessing structure tolerances before they are transported.”
Beyond manufacturing, Tahiri thinks MROs can also benefit from the technology, particularly in terms of time savings. “Regular inspection of components can be very time-consuming, with engine inspections accounting for approximately 50% of the total workload,” he says.
Tahiri says the growing labor shortage is driving the need for automation in inspection processes, which can replace routine MRO tasks, such as inspecting engine housings and blades for defects. Hexagon estimates that regular engine maintenance can currently take up to a month, with inspections taking up 10-20% of that time. Tahiri says Presto could shorten inspection time by up to 50%.