Improving Aviation Sustainability Through Robotic Ultrasonic Inspections
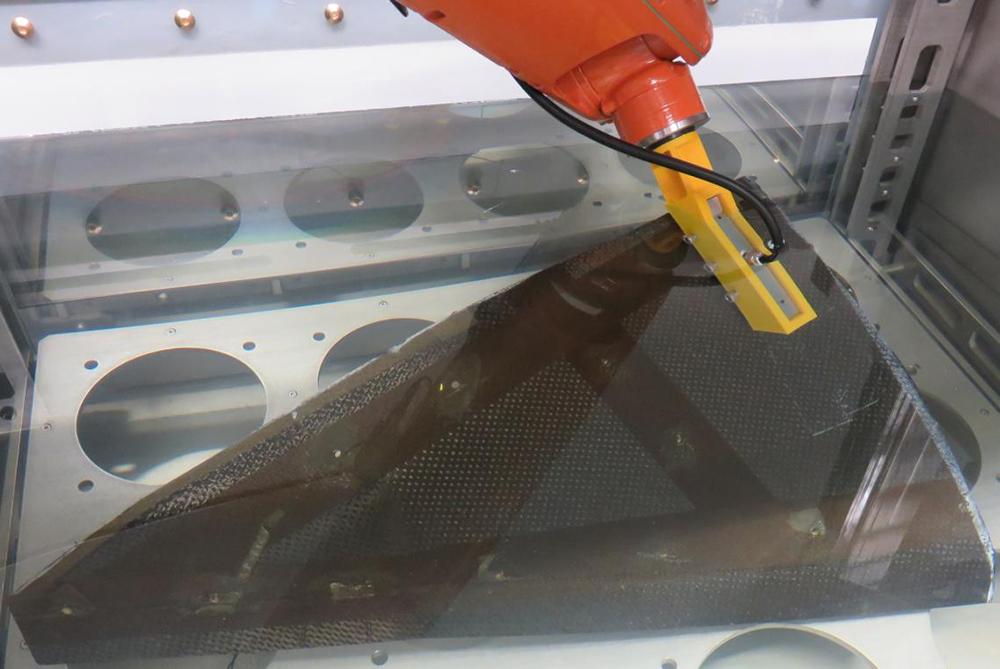
Europe’s Clean Aviation program, which is bringing public and private partners together to develop sustainable aviation technologies, has turned its focus toward an innovation that could have applications within MRO.
GKN Aerospace subsidiary Fokker Technologies initiated a research project called SonicScan under the Clean Aviation program in April 2019. SonicScan aimed to automate ultrasonic non-destructive testing (NDT) of more complex parts on aircraft—such as ones made from carbon fiber, which can improve aircraft efficiency and subsequently reduce CO2 emissions.
According to Clean Aviation, ultrasonic testing is commonly used to perform quality control inspections for structural composite parts in manufacturing, but the technology has mainly been used for thin, shell-like parts. Within aviation, structural composite parts frequently have higher levels of thickness and more complex shapes, such as tapered sections, high curvature and varying cross-sections.
Through the project, Fokker worked with Austrian applied research company Profactor and German ultrasonic testing equipment provider ACS-Solutions to automate ultrasonic NDT of larger structural components with complex shapes. The partners created a robotic work cell for ultrasonic testing capable of inspecting composite parts of up to 1.2 m (nearly 4 ft.) in length. The system can fully inspect parts using phased array technology in approximately two to three minutes.

During its development of the technology, the SonicScan project focused on testing a landing gear component. According to Clean Sky, manufacturing this component with composite materials could reduce its weight by up to 40%.
Now that the research is complete, the partners are looking into how the technology could be applied elsewhere within aviation and other industries, including within MRO.
“A particular feature of the developments is the automated planning of the robotic inspection process, which enables its quick adaptation to parts with different shapes,” says Christian Eitzinger, project coordinator, Profactor. “In MRO activities where ‘lot size one’ inspection is often the case, the SonicScan developments will enable a higher degree of automation through robotic inspection systems that quickly adapt to a particular part.”
In addition to exploring use cases in other markets, the project partners are working on final development steps to increase the maturity of SonicScan’s software and hardware setup so it can be used for industrial implementation in series production. Eitzinger says the partners are working to address customer feedback and hope to implement the technology by the end of 2022.