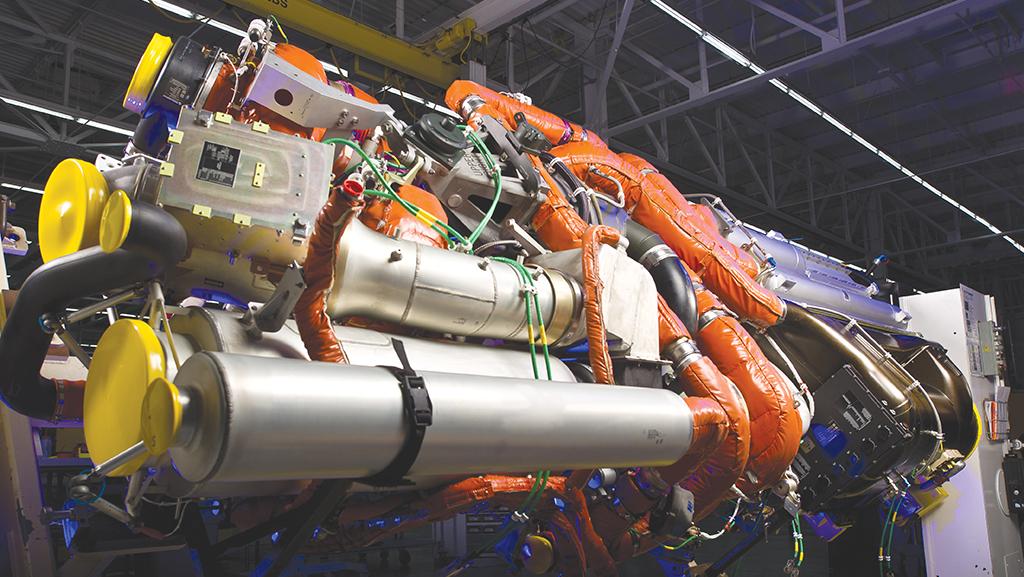
Aircraft cabins, long considered venues prone to the spread of airborne pathogens and volatile organic compounds (VOC), are attracting more scrutiny as the COVID-19 pandemic continues to depress travel globally. Fortunately, suppliers of aircraft environmental control system (ECS) components have developed promising cabin air purification technologies that can mitigate nearly 100% of airborne health risks for passengers.
Those technology developments are well advanced. Aero Biotek, a sister company of PWI Inc. in Wichita, commenced work on its Biotek Shield UVC cabin air treatment in the second quarter of 2020 in response to concerns about COVID-19 transmission through cabin air, explains Eric Dahlinger, PWI’s sales manager.
Biotek Shield uses UVC (ultraviolet C-spectrum) light to neutralize pathogens, including bacteria and viruses—-such as H1N1, SARS, West Nile, tuberculosis and COVID-19. The UVC spectrum, Dahlinger says, has been shown to be the most effective against all types of pathogens.
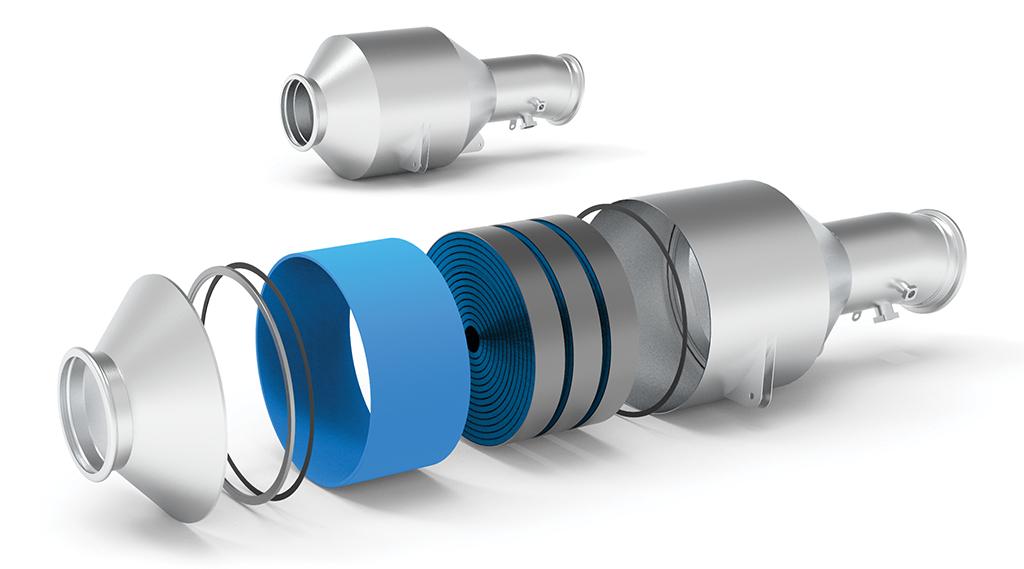
“Once installed, Biotek Shield will prevent rapid duplication of pathogens, including COVID-19,” he says, adding that Biotek Shield has been designed as a Log (logarithmical chart) 6 system, which is the highest degree of measurable effectiveness. “A Log 6 system will kill 99.9999% of pathogens. In contrast, a Log 1 solution kills 99% of live bacteria, but nothing as small as the coronavirus,” he notes.
Customized for compatibility with the aircraft’s airflow system architecture and cabin volume, the Biotek Shield component—a UVC light-emitting diode (LED)—can be installed within the existing duct work or in the mixing chamber, where outside air is mixed with recirculated air from the cabin. The number of Biotek Shield units installed ranges from one for a smaller aircraft up to four for a large widebody commercial jet. The unit weighs just several pounds.
Dahlinger adds that titanium oxide (TiO2) can be added to Biotek Shield to control odors as well as mold/spores and fungus.
The UVC light itself is generated by electrical power from the aircraft’s engines when in flight and from the auxiliary power unit (APU) when on the ground. “As long as air is moving through the ducts, it is being treated by the UVC light, and the pathogens are being stopped from replicating,” Dahlinger says. “When the aircraft is at the boarding gate and air is moving through the environmental control system, the air is being treated well before the aircraft takes off and will continue to be treated after the passengers depart. It should restore a tremendous amount of confidence in the quality and safety of the air on a passenger aircraft.”
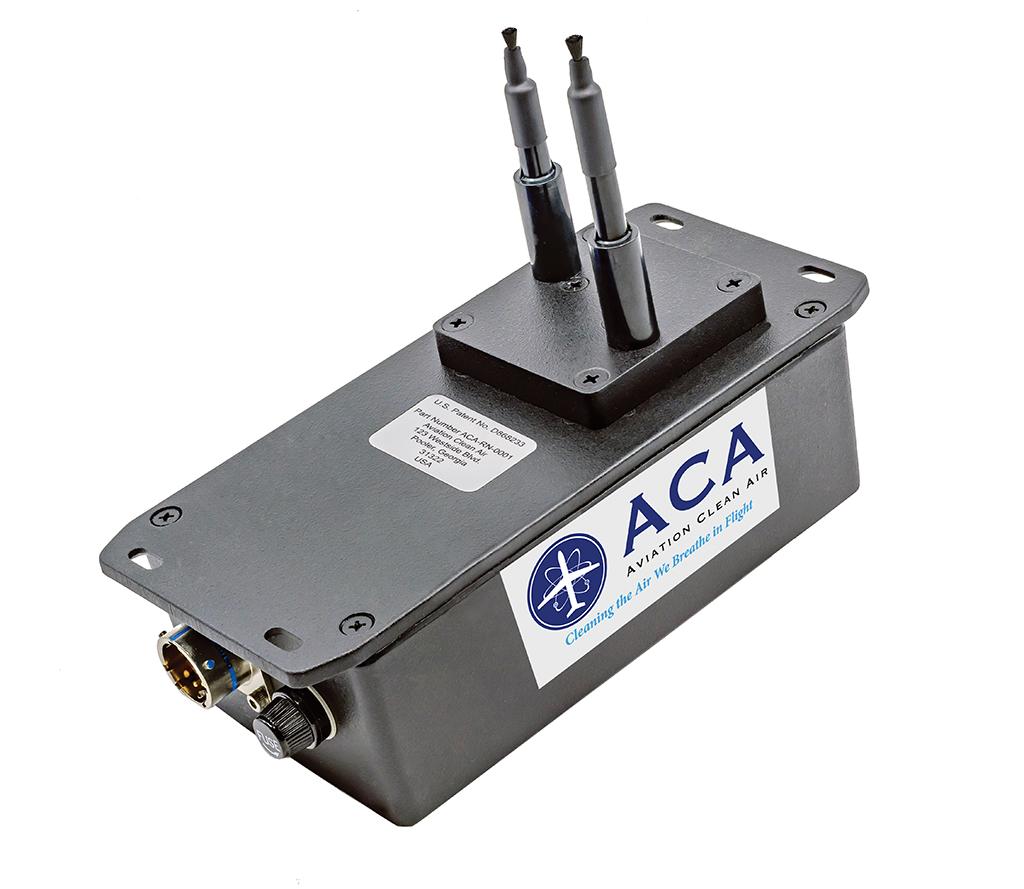
Currently, says Dahlinger, Biotek Shield is undergoing testing at multiple commercial laboratories throughout the U.S. FAA and European Union Aviation Safety Agency supplemental type certificate (STC) and parts manufacturer approval (PMA) certification is anticipated by mid-year. While the Boeing 737 family was conceived as Biotek Shield’s main market, Dahlinger reports that a business jet is the probable launch platform due to significant interest from private jet OEMs.
Aviation Clean Air (ACA) has addressed pathogen disinfection using an electronic—also referred to as a “plasma”—ionization process. With installations on both fixed-wing types and rotorcraft since 2014, the ACA cabin air purification system is available globally, for both line and retrofit, under STC and PMA agreements with all the major fixed-wing and helicopter OEMs as well as numerous MRO providers, according to Jonathan Saltman, a partner at ACA. The Savannah, Georgia-based company, he reports, continues to add more.
“There are over 50 STCs and [approved model lists (AML)]—either in the works or issued—that are held by ACA, OEMs and MROs all over the world for installations of our systems,” Saltman says. “Our system can also be installed on any aircraft for which we currently do not have an [amended type certificate] or AML, via an FAA Form 337.”
For all aircraft, he explains, the number of components installed is calculated to achieve a recommended level of ions in the cabin. “These calculations are based on the configuration of the ECS ducting, cabin volume and anticipated passenger loads,” Saltman notes.
The system is installed in the ECS, and activation begins when the ECS is switched on and air flows into the cabin and cockpit through the air ducts. The system is rated to Log 6.
“We have found that within 5 min. of deployment, there is an 86% reduction of COVID-19,” Saltman says. “That increases to a 99% reduction in 30 min., with the Log 6 reduction [99.9999%] taking place in 120 min.” ACA, he adds, expects reduction rates of other pathogens—over the same time frames—will be the same, although that is being determined by testing.
In addition to COVID-19, the system has been designed to eliminate infectious pathogens—existing or likely to evolve in the future. Along with viruses and bacteria, the ionization process neutralizes and removes VOCs as well as mold. “Mold can be a major contributing factor to corrosion, especially in damp areas such as galleys and lavatories,” Saltman points out.
Cabin odors, often due to VOCs and engine bleed-air contamination, have been responsible for delays and unscheduled maintenance. To address the problem, Honeywell announced development of new, fourth-generation Combined Hydrocarbon Ozone Catalyst (CHOC4) in December 2020.
CHOC4 is a recore/recoat upgrade for existing ozone converters for the elimination of ozone and reduction of odorous compounds from engine bleed air. Initially, Honeywell has targeted the upgrade to the many legacy ozone converters on the Airbus A320 family, says Tom Hart, vice president and general manager for air and thermal systems at Honeywell Aerospace.
As Hart explains, the A320 series has two existing ozone converters per aircraft, each feeding the ECS pack. These units are located approximately mid-ship, left and right, on the bottom of the aircraft, and ducted in the bleed- air system fed by either the APU or engines. The air passes through the ozone converters before reaching the pack.
Hart says the installation is straightforward. The existing converter core is replaced with Honeywell’s offset fin cores, which incorporate a specialized configuration providing higher removal efficiency of VOCs and oil compared to straight-channel core designs. The replacement is carried out using the aircraft maintenance manual instructions. The unit comes complete, with no additional work needed once reinstalled. “The part number remains the same, but the unit is identified with a metalized placard and chemically etched with the STC information and date of recore with Honeywell’s fourth-generation catalyst,” he says.
The STC covers nine of the legacy ozone converter part numbers commonly found on the A319/A320/A321 aircraft. “This upgrades the A320--family ozone converter to a combined hydrocarbon and ozone converter,” says Hart, who explains that an addendum to the original Honeywell-owned STC allows A320 converters to be upgraded with the Honeywell cores containing the new CHOC4 catalyst.
Hart says CHOC4 significantly reduces odor-causing VOCs in the cabin. He points out that most dual ozone and VOC removal converters commercially available today contain early-technology catalysts that can fail to remove 70% of the compounds, which can cause an undesirable odor in the air stream.
“CHOC4 is a breakthrough catalyst that removes 80% or more of many VOCs which cause odor,” he says, adding that CHOC4 was designed for high performance at lower bleed-air temperatures, such as during ground running, where odor removal is more challenging than at cruise.
“In controlled trials, the coating on Honeywell’s offset fin cores removed up to 77% of oil aerosol and vapor, providing additional protection against VOC contamination,” he notes. “CHOC4 will meet the maintenance interval requirements of the A320 family, depending on average fleet-hour flying time, which is about 3-4 years.” Honeywell will be providing additional solutions for other platforms throughout this year, Hart says.
With the advent of the Boeing 787, Collins Aerospace provided what is still the only 100% fresh air ECS for a large commercial aircraft application, according to Lee Annecchino, vice president of air management systems. As he explains, the system’s electric motor-driven compressors take in outside ambient air and provide pressurized air for the cabin, thus completely decoupling the engine bleed air from the cabin air.
“By replacing the traditional pneumatic engine bleed-air control system with electric motor-driven compressors, the more electric system also enables a significant engine fuel-burn improvement,” Annecchino says. “This architecture continues to be an area of focus for our future research and development.”
Collins Aerospace is not stopping there. “One of the future technologies we’re most excited about is the development of air-quality sensing and filtration solutions for our ECS,” Annecchino remarks. “We envision a future ECS that could detect these changes in cabin air quality and then take appropriate action to mitigate them. We anticipate that these sensing technologies could be applied and integrated into the ECS on the next new commercial airplane development program we are awarded.”
Annecchino confirms that Collins is actively engaged with its customers and the industry, including via initiatives such as Europe’s Clean Sky 2, in studying the best way to incorporate sensing and filtration technology into future ECS offerings.