OEMs Target Cleaner, Greener Cabin Air Conditioning

Collins Aerospace’s environmental control system for the Boeing 787 draws fresh air directly into the cabin, eliminating engine bleed air.
A new generation of cabin air conditioning systems is emerging, prompted by a focus on reliability, air quality and sustainability.
In the commercial jet world, air-cycle air conditioning systems are the standard. They depend on engine bleed air that is pumped into the cabin, once it has circulated through a highly complex system of components. The exception is the system on the Boeing 787, in which outside air is routed directly to cabin air compressors for pressurization, eliminating the use of engine bleed air.
Generally, the lowest-reliability components within air conditioning systems have a complex set of moving parts such as air-cycle machines, valves and actuators. At the same time, engine bleed air pre-coolers often have low reliability due to the extremely harsh conditions under which they function, explains David Yokota, senior director for air management systems at Honeywell Aerospace. He cites environmental contamination, wear and vibration as the primary causes of these component failures.
“Many mitigation strategies are employed to maximize on-wing reliability with zero maintenance, including filtration of contamination, material selections that minimize wear and specialty coatings to protect surfaces,” Yokota says. One example he cites is Honeywell’s proprietary fifth-generation air bearings used within the OEM’s latest air-cycle machines (ACM). “They provide unmatched wear-protection capability to extend ACM life while achieving high-temperature capability and high bearing load capacity,” he notes.
Engine pre-coolers also are failure-prone due to the high temperature of the unconditioned engine bleed air and the vibration levels in the engine pylon, Yokota says. “As engine designs continue to evolve to higher pressure ratios, these interface conditions continue to increase,” he says.
In fact, Yokota says Honeywell sees bleed-air-driven air conditioning systems diminishing over time. As engine bypass ratios increase, he says, so will the energy penalty. “Eliminating the bleed air system will not only save energy, but will also simplify the engine nacelle and wing designs by eliminating bleed ducting and overheat-detection systems,” he says. “This also opens the door to alternate forms of cooling such as vapor-cycle systems (VCS), which offer a significant power savings over bleed-driven air conditioning systems but require robust designs to prevent refrigerant leakage.”
Honeywell is “investing to expand its VCS product line” to include products that cover the 50-80-kW cooling range, Yokota says, using the latest oil-free centrifugal compressors, environmentally friendly refrigerants and advanced electric power technologies.
He says Honeywell is leading a work package with industry partners under the EU’s Clean Aviation Joint Undertaking as well, focusing on thermal management technologies to enable highly efficient commercial aircraft designs. “One particular area of interest will be on more electric architectures, which will greatly reduce or eliminate engine bleed air consumption,” Yokota explains.
Paul D’Orlando, director of business development for environmental and airframe control systems at Collins Aerospace, confirms that cabin air conditioning will be increasingly electric. Collins is the supplier of the 787’s environmental control system (ECS), which D’Orlando stresses is still the only 100% fresh air ECS for a large commercial aircraft application.
“By replacing the traditional pneumatic engine-bleed-air control system with electric motor-driven compressors, the advantages for fuel efficiency are significant,” he explains. “The ECS is the largest energy user on the aircraft besides propulsion. More than 3% of fuel burn on any given flight is used for air conditioning and cabin pressurization alone, so any reduction in bleed air consumption for the ECS can have a meaningful impact on fuel usage and, in turn, carbon emissions.”
D’Orlando says Collins also continues working to reduce weight, complexity and parts counts. For example, he says the OEM has systems in service that incorporate composite parts. “Also, various assemblies have been integrated to reduce parts count,” he says. “In addition, we are actively developing additively manufactured parts for future systems, which will open a range of benefits including reduced weight, parts count and improved thermal performance.”
He notes that the company continues to develop new power and thermal management solutions for future aircraft as well for upgrades to the current fleet. “By designing air management systems that are more efficient and use less engine bleed air, we can help improve engine performance and optimize fuel burn,” D’Orlando says.
Typical design changes to cabin air conditioning systems focus on the positioning of control valves for temperature and flow control on the air-cycle machines, according to Holger Bammann, senior expert for air systems architecture at Airbus.
“Additional design enhancement targets fuel-saving potential, which is realized by smart control logics to minimize ram air drag for ECS heat exchangers and an optimized air supply just tailored for the amount of passengers actually in the cabin,” he says. “More disruptive technologies and designs are actually the subject of research and technology programs. However, these technologies are not yet available on Airbus aircraft.”
Asked about weight-reduction efforts, Bammann says they can be achieved by applying new materials and often by structural optimization—meaning better material distribution to where they are needed from a strength point of view. “Additionally lightweight materials (glass-fiber, carbon-fiber) are applied to minimize duct weight. For example, the A330neo uses thermoplastic ducts and particle-foam air outlets,” he explains.
While the OEMs continue to advance the engineering of cabin air conditioning, its system failure was high on the list of factors causing flight delays and cancellations at one airline, reports Patrick Quinn, product line manager for data acquisition products at Curtiss-Wright. To remedy that, the OEM installed its KAM-500 on more than 200 Boeing 737NGs flown by what he identified as “a major U.S. carrier.” He says this represented the first time the KAM-500 had an aircraft air conditioning system application.
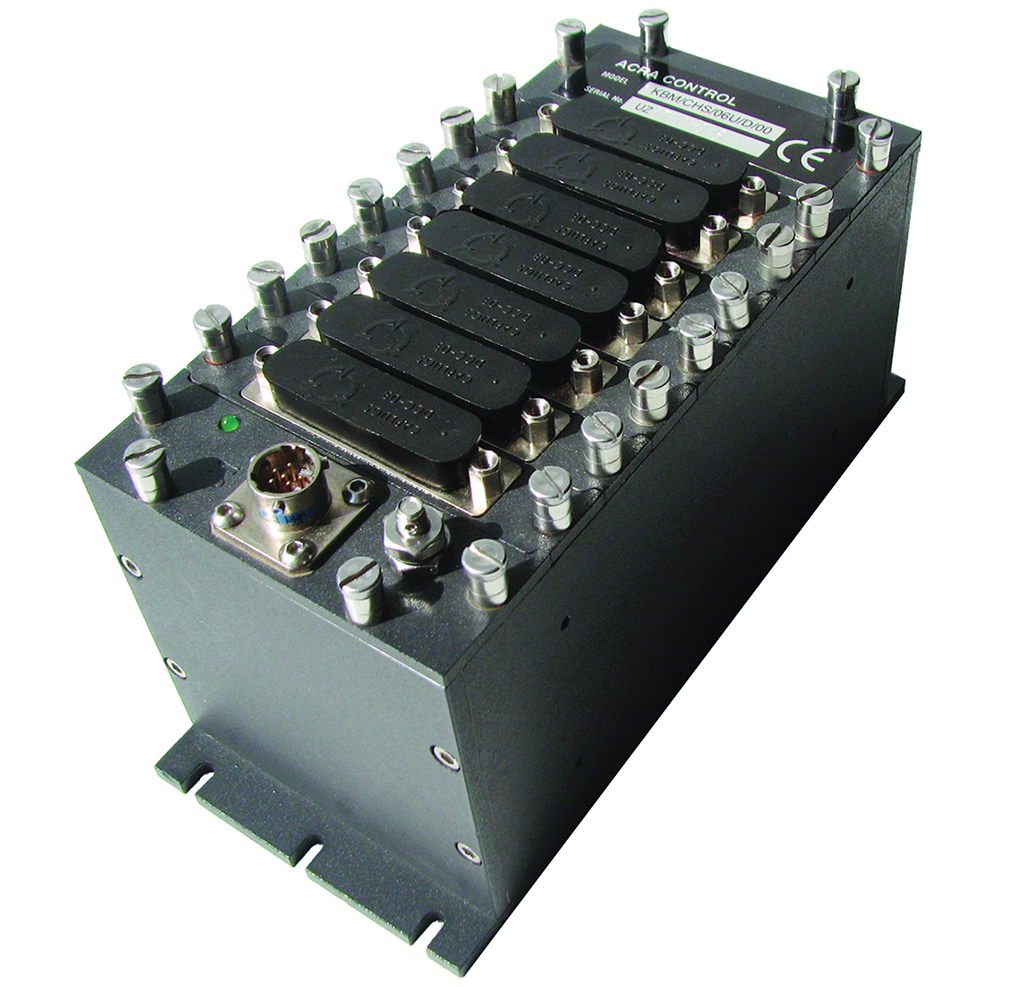
Credit: Curtiss-Wright
The KAM-500 is a hardware product developed for flight-test data acquisition by ACRA Control, owned by Curtiss-Wright since 2011. The KAM-500 works in tandem with Das Studio, software proprietary to Curtiss-Wright. Specifically, the data acquisition comes from a mix of pressure and temperature sensors strategically located throughout the aircraft that gather and interpret data regarding the air conditioning system maintenance status. Data is transmitted in real time over ARINC-429, using the Aircraft Communications, Addressing and Reporting System system resident on the aircraft.
“It was an off-shelf, predictive maintenance quick solution to what this airline wanted,” Quinn notes. “With KAM-500, the airline was receiving data they had not gotten before. As a result, air conditioning failures became one of the least problematic areas.”
With growing concerns about cabin air quality—recently due to the COVID-19 pandemic—airlines are showing more interest in assuring a pathogen-free cabin environment. For instance, Aviation Clean Air’s (ACA) airborne air purification system is being adopted on a commercial airliner, according to Jonathan Saltman, a partner in the California-based company.
The ACA system incorporates a bipolar ionization component, which generates positive and negative ions using the aircraft’s existing air, Saltman explains. The ions will be transferred via the airflow generated by the aircraft air distribution system to the cabin to neutralize and decontaminate cabin air and interior surfaces continuously.
Saltman says the ACA system is now offered by all business jet OEMs as either a standard installation or an option. Installation is accomplished under a supplemental type certificate (STC)—of which there are now more than 60—available from ACA, aircraft OEMs and some MROs. In addition, installations or a retrofit of an entire aircraft family are permitted under an Approved Model List, which can be included in the body of an STC or as a separate document.
Last year, ACA added an STC for the Leonardo AW139—the first for a helicopter application. Saltman says an STC for the Sikorsky S-76 is expected this year. A ground-based version is also available.
“ACA is currently working with several airlines for fleet-wide installation of our airborne air purification system,” Saltman says, adding that “an announcement is forthcoming.”
In 2022, ACA rolled out what Saltman terms “lower-profile” equipment for the air purification product to enable easier installation on air conditioning systems with smaller ducting and reduced clearance, typically found on light jets and turboprops.
“Ongoing laboratory testing has continued to show the effectiveness of the system for all pathogens beyond COVID, including bacteria and viruses, as well as volatile organic compounds and mold spores,” Saltman says.
Mathieu St-Cyr, manager of sales engineering at Bombardier, reports that the OEM introduced Pur Air, a sophisticated air purification and circulation system, on its Global business jets to provide a clean cabin environment while optimizing engine bleed air extraction. He says Bombardier recently enhanced the Pur Air system on the Global 7500 and upcoming Global 8000 to filter out volatile organic compounds.
Honeywell’s Yokota notes that the company is developing sensing technology to detect and isolate the sources of bleed air contamination. “Once the technology is mature and can be deployed, these sensor readings, combined with other air conditioning and aircraft parameters, can effectively identify the presence of bleed contamination and direct maintainers to potential sources of the contaminants,” he says.