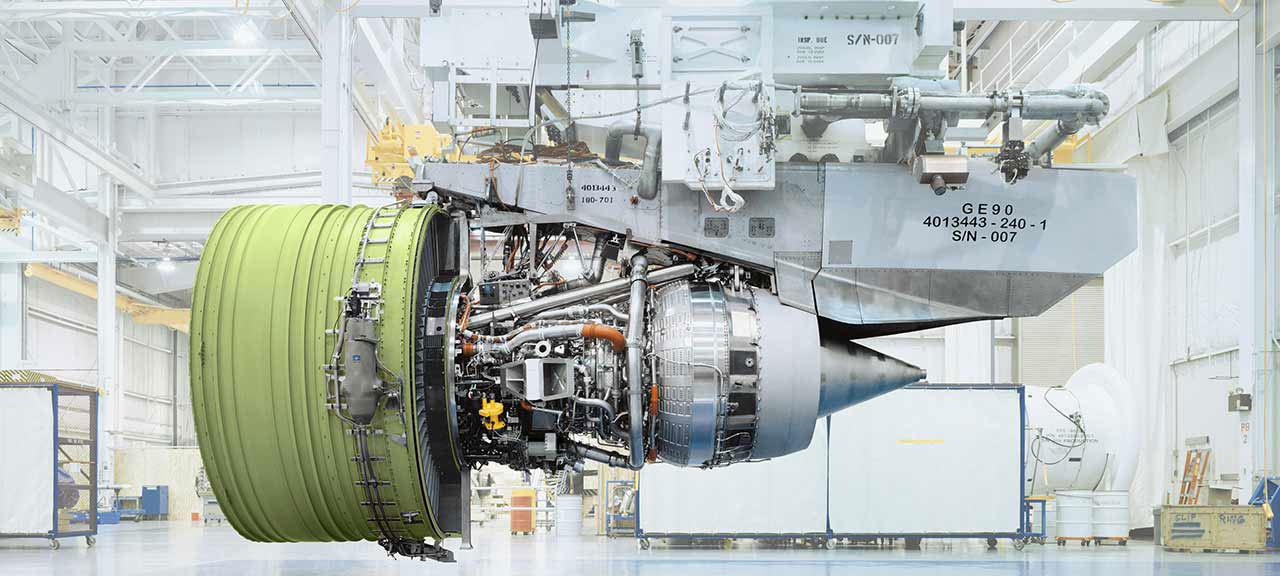
Leading MROs are pushing forward on printing polymer interior parts. But the much tougher additive manufacturing of safety-critical metal parts is a job for OEMs making new parts.
Roland Berger project manager Tim Femmer divides additive metal prospects here into two kinds: large, structural parts for airframes; and generally smaller parts for aircraft engines.
Airframe OEMs appear to be pausing their additive initiatives. “Boeing and Airbus have looked into the technologies, but are a little reluctant,” Femmer observes.
But engine OEMs are pushing ahead. Femmer predicts most additive engine parts will be static, not rotating, and believes GE is leading the charge.
That is certainly a view shared by Eric Gatlin, general manager of additive manufacturing for GE Aviation, and Chris Schuppe, general manager of engineering & technology for GE Additive.
They outline a very aggressive GE additive program and offer a peek into the long-term implications for the engine aftermarket.
The most immediate additive initiative is GE’s Catalyst turboprop engine, which will have 25-30% of its parts printed, according to Gatlin. These will include large structural parts.
Next is the T901 engine, a replacement for Apache and Blackhawk rotorcraft engines. Here too, additive will be used on both small and large parts.
The delay in Boeing 737MAX production created spare capacity at GE’s Auburn, Alabama, plant, which was printing fuel nozzles for LEAP engines. “This created capacity for other projects,” Gatlin explains. So in one year, GE developed four additive parts for its LM9000, a land and marine turbine derived from the GE90 turbojet.
The big commercial jet project will of course be the GE9X, soon to start production. GE is printing five different types of part for this powerplant for a total of 292 individual parts on each engine. A GE facility in Cameri, Italy, will print low-pressure turbine blades using Arcam electron beam (EBM) technology, while Auburn uses direct metal laser melting (DMLM) to print other parts.
The engine or engines to be developed under Safran and GE’s recently announced Revolutionary Innovation for Sustainable Engines (RISE) program are still in the concept stage, too early for evaluation of printing options.
Meanwhile, existing additive tools are being constantly improved. “Productivity is up a lot,” Schuppe stresses.
Efficiency is boosted in a number of ways, from how machines are fed data to post-processing of the printed part. Additive originally produced 9 LEAP fuel nozzles in 140 hours. Now it is doing 12 in 85 hours, and the goal is to produce 12 in 45 hours. After six years and production of 100,000 nozzles, the additive exec sees much more opportunity for improvement.
Schuppe acknowledges that GE prints largely static engine parts today. But he notes that EBM will be used to print rotating GE9X blades. Here the advantage of additive is not its ability to produce a complex part. Rather, it can print a large part made of titanium aluminide that is difficult to cast, yet weighs 50% less than the nickel alternative.
Still, Schuppe says GE will not be printing high-energy rotating disks or shafts for a long time.
So far GE has been using EBM and DMLM to print parts. A directed energy deposition system will be in production by the end of 2021. And GE is looking to add binder jet technology in aviation as well.
Gatlin says GE will be moving to a machine with four different lasers that will have to interact with each other to produce large parts. He acknowledges that certifying the multiple-laser machine will be a challenge for both GE and regulators.
Femmer says additive always faces two big hurdles: cost and certification. “Does it really work? Is it doable? Is it creep-resistant enough under temperature and force? How strong is the material? Will it start to creep, then crack, risking a break?”
Related to the cost challenge, GE Additive is moving more and more toward true industrial-scale, high-volume production. “We need to move to the next level of automatic control capabilities,”
Schuppe says. This is the goal of GE’s M Line, a modular machine architecture to enable economic production at industrial scale. Meanwhile, GE is already thinking about the aftermarket opportunities for additive.
Already GE has helped Cummins, which makes a variety of land engines, evaluate and develop binder jet technology for making replacement parts. Gatlin says traditional supply chains were disrupted during the COVID crisis, offering an opportunity to innovate new approaches to sustainment.
For the U.S. Air Force, GE is working on the Pacer Edge program to find replacement parts that are difficult to procure but can be printed. In just 15 months, GE developed a printable sump cover for F110 engines on U.S. fighter jets.
For commercial engines, GE is still looking for the right opportunities for additive production. Gatlin says two such parts have already been selected, but not yet announced.
Schuppe believes MROs may eventually print simple engine parts like brackets and supports. “But OEMs will still make the high-value assets for quite a while.”