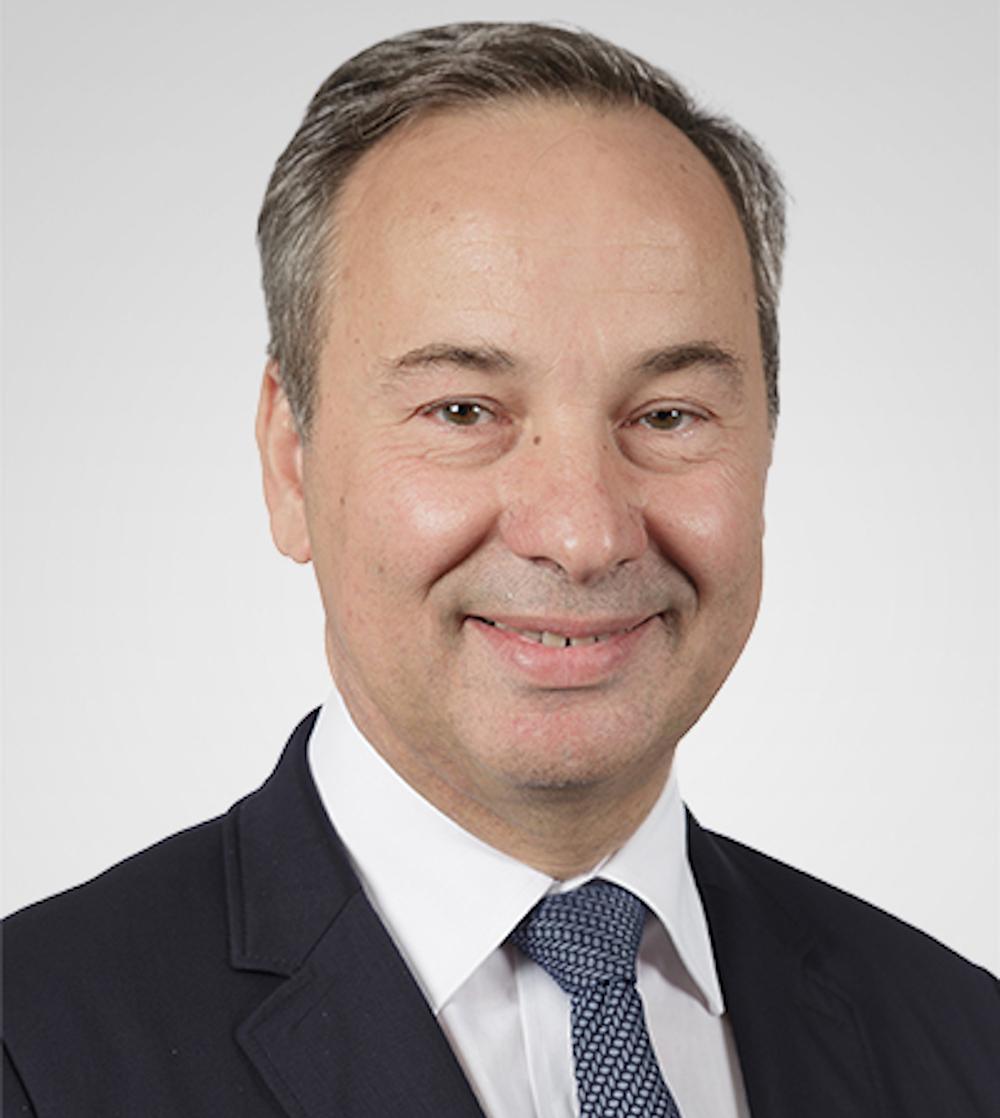
Sabena Technics opened its sixth maintenance hangar at its Bordeaux site this month. Philippe Rochet, the company’s CEO, speaks to James Pozzi about its plans for the facility.
What was the company’s thinking behind building a sixth hangar at the Bordeaux site?
We took over this company 14 years ago when it was EADS Sogerma, at a time when some said there was no future for this type of MRO business in France and on the European continent with labor costs high and the more affordable Asian market growing. Ever since, our challenge has been to demonstrate the opposite. When building this new hangar, we had to ensure confidence in our team in Bordeaux. We had to identify whether our team was at the right level in terms of competitiveness and performance to allow us to boost capacity – the answer to that was a resounding yes. The average weekly working time in France is 45 hours, but at this company, it was 39 hours per week. All our staff have accepted that they are going to work more to improve competitiveness in our specialist market focusing on airframes and improve efficiency across our workload, which is roughly 50% commercial and 50% defense.
Capacity is a challenge for many European MROs, with Sabena Technics no exception. Do you see this issue as your primary challenge?
I believe so. In Europe today, there are around 5,000 civil aircraft in-service. Airbus have forecast that by 2037, the European fleet will nearly double to 9,000 aircraft. The obvious question for maintenance providers is where is the airframe capacity to handle this growing fleet in the coming years? Our analysis shows existing airframe maintenance capacity won’t be enough to service the growing fleet. It’s not strictly our role as a company to bring the global answer to this, but we believe we can help bring some form of solution with the extra capacity we are developing across our sites. In the sixth hangar, we will service all Airbus and Boeing aircraft types except for the A380, which is catered for in another part of the Bordeaux site.
Financially, what is the investment in the sixth Bordeaux hangar?
It’s around €25 million ($21 million) of investment. This doesn’t only cover the hangar construction price, but also factors in all equipment including tooling and docking. We can’t decide to have this new capacity if we don’t invest in the best equipment possible for our people to use. Also, the total investment includes the digitization of processes.
Which processes is this digitization specifically being rolled out for?
Sabena Technics can perform a C check on all types of aircraft totally paperless. To date, we’ve performed one paperless C check on an Airbus A340. All our working parties are not yet operating on this digital model, but this will be ramped up. By the end of the year, we hope to have all our teams working on this paperless operating model. The first objective is not just to be paperless for the sake of it, but instead, to have all our staff and working parties connected to the aircraft technical documentation without moving from their location.
Sabena is bringing around 250 people into the company annually across France. What are some of the manpower targets for Bordeaux factoring in the additional facility?
Approximately half in Bordeaux, with the other half spread across the other French sites. We need more people, and while we are not alone in requiring them for aviation technical jobs, we must have a stronger involvement in supporting apprentice programs. Here in Bordeaux, we have close relationships with a local aerospace technical school and run several apprenticeship programs which allows us to increase staff annually. A minimum of 55% of our people working in Bordeaux have originated from apprenticeship programs.