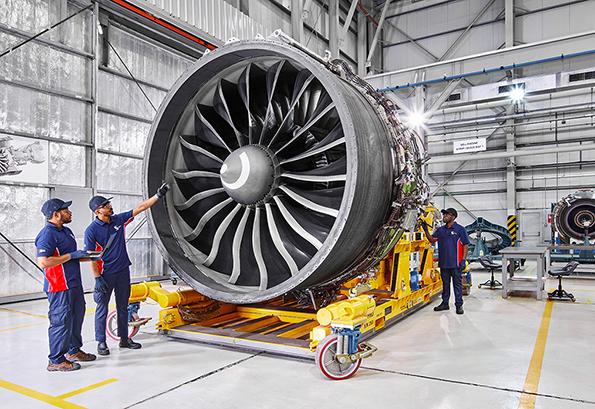
The end of 2019 saw a commercial aviation aftermarket buoyed by record MRO spending but one still skeptical that its well-documented capacity constraints will be alleviated in the near- to mid-term. The engine segment, which accounts for 42% of the market according to Aviation Week’s Fleet & MRO Forecast 2020 data, is evidence of this. While overall commercial MRO spending reached $24.3 billion for last year and is expected to jump to $34.7 billion in 2020, the surge in shop visits has left many providers running close to capacity for 12 months a year at shops worldwide.
The narrowbody engine segment, mainly the CFM56 and V2500, which account for more than half of the market combined, is particularly lucrative at present. Demand for these engine types is strong, with shop visits for their newer engine variants—the V2500-A5, CFM56-5B and CFM56-7—are all expected to peak by the mid-2020s. However, their successor engines, the CFM Leap and Pratt & Whitney’s PW1000G, have seen technical issues over the past few years, meaning the expected influx leading to the phase-out of older engines hasn’t materialized very quickly. As it stands, many in the industry believe the CFM56 and V2500 will be operating well into the 2030s.
Other mature engine programs have also shown longevity, which has had some detrimental effects on capacity. “Demand for services for older legacy engines, such as the CF6-80C2, has continued longer than expected—thanks to low fuel prices and air transport demand, where demand for aircraft and engines is faster than delivery rates,” says Martin Friis-Petersen, senior vice president for MRO programs at MTU Aero Engines. “Also, new-generation engines are entering the shops earlier than originally anticipated and will ramp up in the next decades. All this has led to our shops and many others being fully loaded worldwide.”
On top of these issues, a more recent development has been the technical woes that dogged the Boeing 737 MAX program last year. With the aircraft yet to return to service, the expectation is that this situation will continue well into the year, likely increasing demand for older aircraft and their engines. While retirements could provide relief for the used serviceable material shortages that are prevalent, any potential return to service of the 737 MAX could be key to driving that trend, says Mike Stengel, senior associate at consultancy AeroDynamic Advisory.
“Fleet demographics certainly suggest that a wave of retirements is coming. However, if the teething problems on the new-engine models continue, then older aircraft may remain in service longer than expected. The return to service of the MAX will also influence retirement rates in the coming years to replace the last generation of narrowbodies,” he says.
Stengel believes that the current environment has pushed MROs into adding capacity out of necessity. “MROs are somewhat backed into a corner in this regard, and one of their most effective options is to expand capacity,” he says, pointing to several suppliers announcing expansion plans, both for engine shop visits and component repairs. For airlines with in-house engine shops, he cites the decisions of American Airlines and United Airlines to insource some engine work, with the former bringing CFM56-5B in-house in late 2018 while the latter brought some V2500 engine services in-house. “This allows them to control their own destiny to a degree rather than relying on third-party capacity,” Stengel says.
Holger Lipowsky, principal at consultancy Roland Berger, believes that while the current climate is challenging, it presents a good opportunity for well-resourced companies to grow capacity. “It’s the perfect time for investments and especially for large OEMs with the financial power to build capacity and are expected to use this opportunity to strengthen their position for the coming years,” he says.

A recent example of an OEM doing this is Rolls-Royce, which in November 2019 confirmed several changes to its global aftermarket network as it looks to prepare for the growing number of its engines undergoing shop visits over the next decade. Its Rolls-Royce Deutschland site in Dahlewitz, Germany, is to transition into a services hub with capability for widebody engine overhauls from early this year.
Meanwhile, its Rolls-Royce Canada facility in Montreal will also introduce widebody engine overhaul services later this year, with a start date projected for the fourth quarter. As well as acknowledging capacity as being a driver behind the moves, Rolls-Royce says it also made the changes as a way of reducing the impact on customers handling in-service issues with the Trent 1000. This followed adjustments to its maintenance center (AMC) network of shops. U.S.-based MRO Standard Aero joined as an AMC for RB211 repairs at the beginning of 2018, followed by Delta Tech Ops becoming an AMC for the Trent 1000 and Trent XWB, which power the Boeing 787 and Airbus A350 respectively.
MTU Maintenance has also invested heavily in ramping up capacity. Expansions have occurred at shops in Hannover, Germany, and in Zhuhai, where it overhauls CFM56 and V2500 engines, along with its Berlin facility where demand for mature engines such as the CF6 remains high. Its Vancouver facility, which has specialized in the V2500, is also due for relocation.
The company factored in Leap and GTF engines into these expansions, with scheduled shop visits expected to begin between 2021 and 2022, to be followed by restoration shop visits. A new Poland-based joint venture with Lufthansa Technik, operating as EME Aero, was scheduled to induct its first GTF engine in late 2019 and will eventually build up to a capacity of 450 engines per year. MTU also plans to open a site in Serbia focusing on parts-repair services.
In the Middle East, the main capacity challenges have been workforce--related. This has been a focus for Sanad Aerotech, which was renamed from Turbine Services & Solutions last year, in a move combining its engine, finance and energy divisions.
The year 2019 saw the Mubadala-owned company sign several large-scale engine repair deals with OEMs, in moves set to add capacity demands at its Abu Dhabi-based facility. Starting in January, it will begin overhauls on the GEnx, with more than 300 engines expected over a 15-year period. It will also handle the Leap-1A and -1B, with the engines representing a new product platform in its portfolio. This will start in 2021, as a 10-year agreement, and will see more than 200 engines inducted over that time frame. With these new agreements in place, building a workforce to add capacity is one priority.
“With these new agreements, we’ve had to look at increasing our manpower and capacity in terms of production space,” says Sanad Aerotech’s CEO Mansoor Janahi. “In terms of numbers, we are looking to add around 400 employees across the aerospace business, taking us to between 550-600 employees over the next two years to deliver this” additional production capability.
While larger companies boasting greater resources have sought several solutions to address capacity concerns, smaller MROs have had to be more agile and creative to adjust. Nevertheless, the roles of these smaller, boutique-style independent engine repair providers could also expand in the next two to five years. GT Engine Services, which offers specialist repair services from its facility close to London Stansted Airport in the UK, is one company that sees itself as an alternative option to operators sending their engine into an overhaul shop.
Greg Macleod, the managing director, says the company was previously a seasonal business but changed strategy a few years ago in order to spread its workload year-round while adding further repair capabilities. Given its work for airlines and lessors, this means the shop is routinely full, while the allocation of manpower and resources is a constant challenge, Macleod says. “This year we have just increased our workshop space by a third,” he says. “We also have a constant recruitment drive and a growing apprentice program.” Specifically, he identifies materials for the Rolls-Royce RB211 engine as being tricky to acquire.
Like many repair providers, Macleod foresees further alignment with OEMs, as companies like GT Engine Services position themselves to take on the overflow of maintenance work from capacity-squeezed counterparts. “There is a lot of scope to strengthen our relationships with the OEMs, which will benefit all involved,” he says. “This is nothing new, we are filling a void where the OEMs and overhaul shops struggle to fill.”
Across the pond in the U.S., Global Engine Maintenance (GEM), another independent MRO, provides repair services for CFM56-3, CFM56-7B and starting this year, CFM56-5B engines. Like GT Engine Services, it is running either close to or at full capacity all year round, mostly working from a single bay configuration. When necessary, GEM changes the workspace to a double-bay configuration to add capacity.
At the facility, it sees a strong wave of inductions in the winter and spring months as aircraft operators gear up for the summer travel season. “In terms of engine repair volume, we are repairing almost as many -7B as we are -3C engines,” says Jamie Devin, the company’s director of business development says of the company’s output. “Components and life-limited parts (LLP) for the -3C engines are plentiful, with only a few exceptions. However, these parts and LLPs for -7Bs are slightly harder to procure generally because the operators want performance restorations built up to 10,000 cycles remaining.”
Devin says it has looked at other methods of adding capacity at its Miami, Florida, hangar and has identified one area where it can improve its output. “One way to increase capacity is to improve your throughput time—we’ve added a number of in-house capabilities that would otherwise be sent to outside vendors, thus saving time,” he says.
GEM, has also turned to technology to help its throughput time. “Our 3D scanner and high-speed grinder allow us to match grind high-pressure compressor (HPC) and high-pressure turbine (HPT) rotors in days rather than in weeks,” explains Devin. “The 3D scanner also aids in detail inspection. What would have taken hours to inspect using traditional methods can now be done in minutes,” he adds.
Another independent taking on extra capacity is Aero Norway, a CFM56 specialist focusing on engine overhaul service. Its shop in Stavanger also routinely runs close to full capacity annually, says Rune Veenstra, its chief business officer. It has increased capacity by bringing in more resources, including necessary tooling to grow volumes. Once the CFM56 engine family hits its expected shop visit peak between 2023-24, the cargo market will look to move over to these engine types, Veenstra tells Inside MRO.
Comments