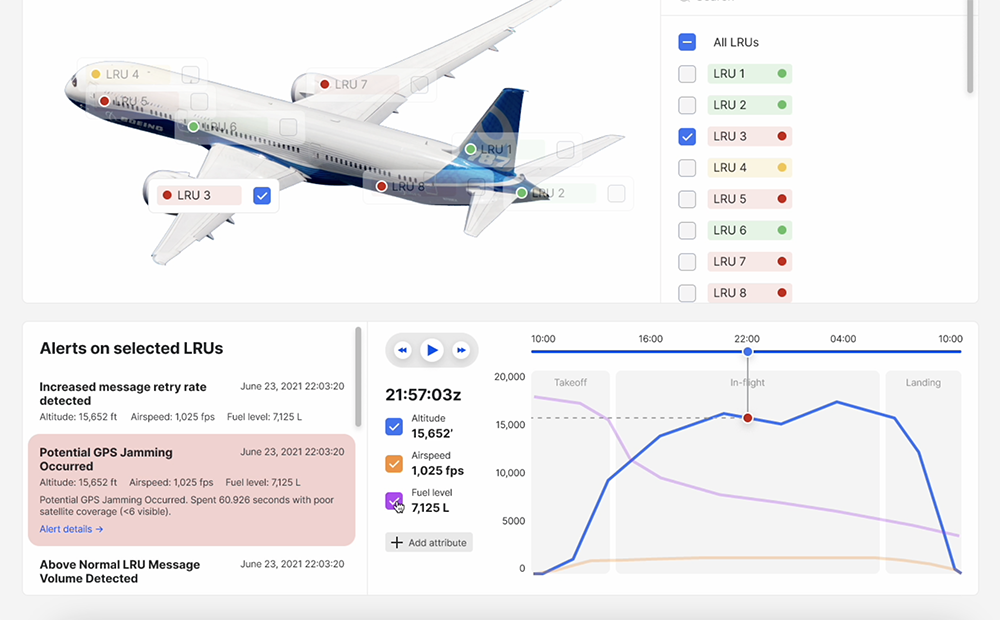
Shift5, which already supplies airlines with compliance data from aircraft and has a contract to support condition-based maintenance for the U.S. Air Force, will soon offer airlines a predictive maintenance module with some distinctive capabilities.
The company calls its basic product an observability platform for onboard operations. The platform works with any onboard hardware, data bus or protocol and passively performs full-take data capture from any onboard source. The new predictive module transforms raw data into readable, context-rich, actionable insights, enabling MRO teams to detect, identify, alert and take actions on anomalies in operations. The module can also integrate with airlines’ existing systems, tools and storage.
“The Shift5 Platform deploys onboard a commercial aircraft using a standard ARINC 600 enclosure optimized for size, weight and power,” explains Chief Technology Officer Egon Rinderer. During data capture, Shift5 also detects anomalies and analyzes data from multiple onboard sources, adding context to assist predictive maintenance.
If an aircraft already has an onboard general-purpose computer with access to all data buses, Shift5 can work without additional hardware.
Rinderer stresses that Shift5 can run on any commercial aircraft. “Shift5 tailors the technology stack to meet the requirements of the aircraft, rather than forcing the aircraft owner to accept technical limitations.” After normalizing data and detecting anomalies, Shift5 adds variables such as airspeed, geolocation, temperature, altitude, pressure and other thresholds to help interpret anomalies.
Shift5 uses both deterministic and non-deterministic algorithms to pinpoint anomalous behavior. It can develop its own algorithms or use those of airlines and third parties.
Shift5’s own deterministic rules come largely from documents such as protocol specifications and component documents. Shift5’s non-deterministic algorithms are trained using a software/system integration lab—basically a set of avionics boxes without an aircraft—and are then refined by on-aircraft training. “This establishes a baseline which can be monitored for deviation,” Rinderer explains.
Data analysis is performed by hardware onboard the aircraft as well as in the cloud, enabling the new predictive module to function at scale across an operator’s entire fleet.
Rinderer says Shift 5 is the only hardware-, bus- and protocol-agnostic platform that can do passive, full-take serial data capture and analysis from any source onboard an aircraft at the airframe level. This could enable Shift5 to support predictive maintenance tools developed by OEMs, airlines or MROs with a rich data set and deep analysis of all onboard components.
In this case, Shift5 results can be integrated into existing tools and workflows, making familiar tools work better. Shift5 data can be provided either in real-time or batches. For example, airlines can stream critical alerts off aircraft during flight while total data is downloaded at gates.
Shift5 is pursuing a supplemental type certificate (STC) from FAA to deploy its platform’s full capabilities on commercial aircraft. Rinderer expects the first STC in early 2024.