
FADEC systems monitor engine parameters to make discrete adjustments to the control system and optimize engine performance.
As the digital world keeps pushing the electronics technology envelope, engine OEMs are seizing the opportunities to incorporate more capable full-authority digital engine control systems into their products, resulting in greater operational and maintenance efficiencies.
P.J. Titone, vice president of engine control systems at Collins Aerospace explains that full-authority digital engine control (FADEC) systems are essentially the “brains” of an engine, converting pilot inputs, such as throttle position, into the direction to control effectors such as the engine’s valves or actuators. “They in turn meter fuel or establish engine vane position,” he notes.
The FADEC, Titone points out, operates in a closed loop, which means that while providing direction to control effectors, it is monitoring other engine parameters, such as pressure and temperature, in order to make discrete adjustments to the control system and optimize engine performance. “FADEC also protects the engine from undesired events such as overspeed and overtemperature, and takes actions to mitigate them,” he says, adding that as engine control systems continue to become more complex, they will directly contribute to improved engine performance and fuel efficiency.
“This also requires additional advanced signal processing coupled with operation in increasingly challenging environments,” Titone says. “Collins has made significant investments and improvements to its FADEC portfolio that include increased use of microelectronics, advanced manufacturing techniques and sophisticated packaging solutions that accommodate demanding thermal and vibratory environments.”
A typical FADEC system is comprised of a single, line-replaceable unit (LRU), explains Brent Ostermann, vice president of engineering at StandardAero. However, he says many inputs to the FADEC come directly from multiple LRUs, such as the main fuel control, starter control valve, operability bleed valves, ignitor boxes, ignition leads, exhaust gas temperature harnesses and thermocouples, pressure valves, the fuel flow meter and speed alternators.
Ostermann says these types of LRUs provide important information to the FADEC that the engine requires for thrust management, including compressor discharge pressure, exhaust gas temperature and ambient pressure. Other inputs include fuel flow, variable guide vane positioning, fan speed, core speed, high-pressure turbine cooling temperature and low-pressure turbine cooling temperature.
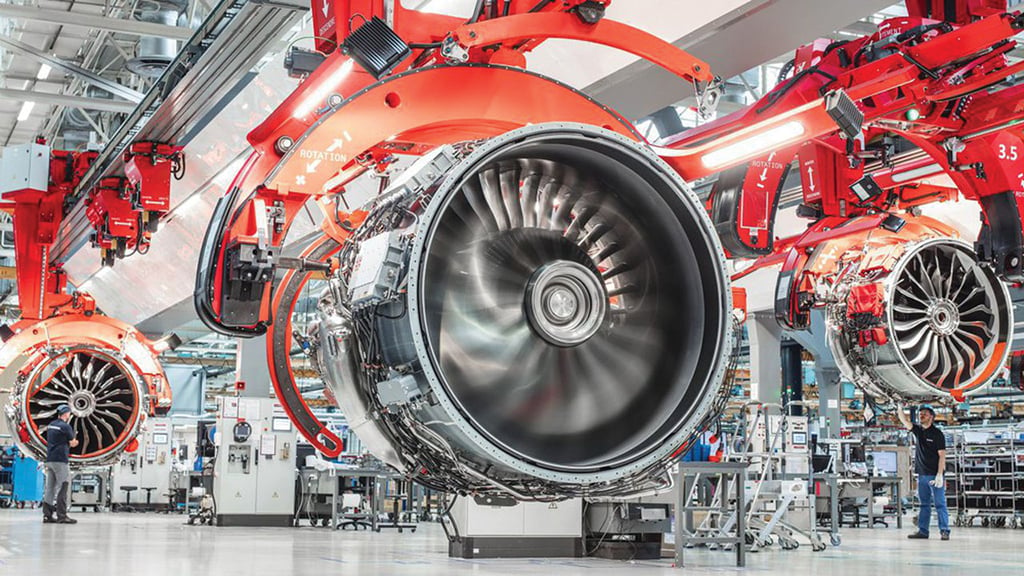
generation FADEC 3 systems. Credit: Safran
He adds that as engine technology has evolved, more inputs are coming into the FADEC, which means an increase in parts count. “For example, an engine with newer technology, such as the CFM Leap 1A and Leap 1B [powering the Airbus A320neo and Boeing 737 MAX, respectively], have incorporated a second FADEC to measure and record additional parameters for engine management,” he explains. “There are many more inputs from LRUs and engine monitoring equipment used on these engines today.”
That is the direction in which FADEC is going. “With advancements in electronics in general, we’ve been able to build much higher computing capability into our FADECs,” says Dave Milne, senior director of engine controls at Honeywell Aerospace. “This enables ultrafast and precise control, which equates to higher engine performance and improved thrust-specific fuel consumption (TSFC), diagnostics/prognostics and high-speed data communication with other aircraft systems—all with robust cybersecurity protection.”
Milne adds that improvements in FADEC engineering have focused on hardware as well as software. “The improved computing hardware allows us to run more sophisticated software,” he says. “With multicore processing, we’re able to partition across different functions or design-assurance levels. There have also been dramatic improvements in tools and processes.”
To achieve that, Milne says, Honeywell has employed advanced model-based development and simulation environments that enable the OEM to rapidly optimize the engine control. “Integrated tools automatically generate software code, test cases and procedures and documentation—taking humans out of the loop to reduce development time, cost and errors,” he says.
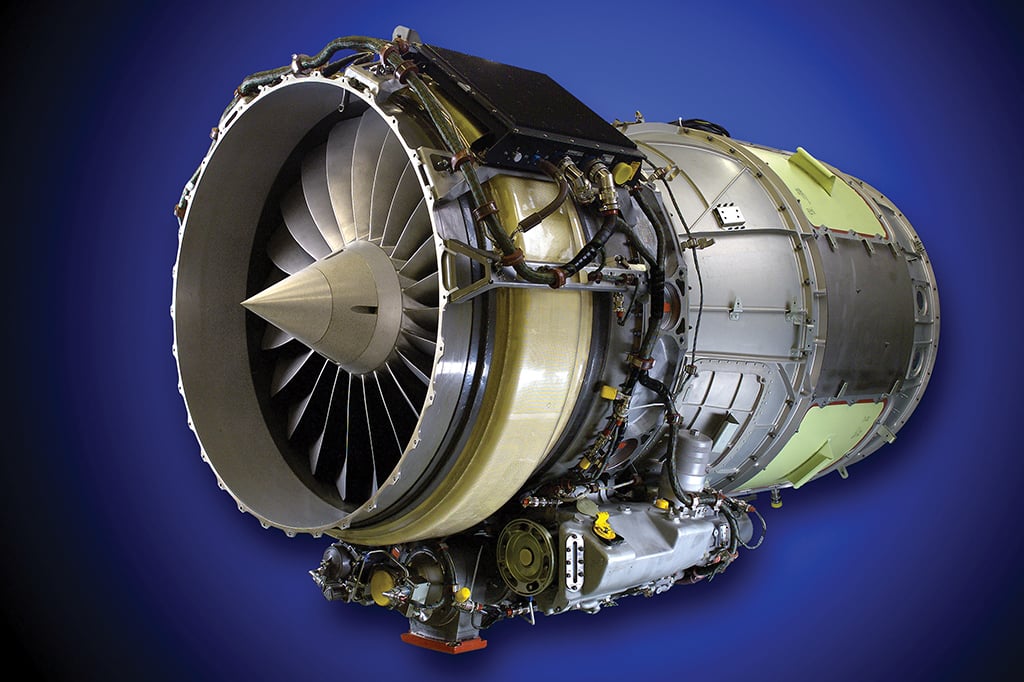
Milne says Honeywell began incorporating engine condition trend monitoring to support diagnostics/prognostics in its digital electronic engine controller (DEEC) and FADEC products in the early 1990s. DEEC, he explains, was a limited-authority, single-channel system that preceded FADECs.
“Since then, the focus has been on capturing more data and incorporating more advanced analytics to reduce maintenance cost and downtime,” Milne says. “We have implemented real-time data logging and are now capable of implementing ‘digital twins’ in the FADEC.”
The digital twin is a high-fidelity, real-time model of the specific engine the FADEC is bolted onto. It degrades as the engine does, affording deep understanding of the engine’s condition, and has the ability to accurately forecast needed maintenance actions, providing an effective arbiter if redundant input signals do not agree.
“This continued advancement in diagnostic/prognostic capability is one of the reasons our HTF7000-series engines achieve 99.996% dispatch reliability,” Milne says. The HTF7000 family powers the Challenger 350, Learjet 40, 45, 70 and 75, as well as the Gulfstream G280.
Milne predicts that as engine manufacturers develop new-generation turbine engines and continue to push the limits of higher TSFC, lower weight and better reliability, the control system—and hence the FADEC—will become more complex. “[That] means more variable geometry, sophisticated surge/bleed control, active tip clearance and complex thermal management,” he says.
“Managing FADEC size, weight, reliability and affordability will continue to be a challenge,” Milne cautions. “We are also entering an era where FADECs share volumes of data with a variety of aircraft and ground systems. This presents a substantial cybersecurity challenge.”
Claire-Marie Letourneur, FADEC programs director within the avionics division of Safran Electronics & Defense, says the capacity needs of FADECs are continuing to accelerate. Safran’s FADEC family, she says, includes multiple products designed to work with an engine thrust range of 30,000 lb. for CFM56-powered single-aisle aircraft up to 115,000 lb. for the GE 90-115B on the Boeing 777 family.
Safran’s latest-generation family member, FADEC 4, is a product of FADEC Alliance, a joint venture of GE Aviation and FADEC International—itself a joint venture of BAE Systems and Sagem/Safran Electronics. As Letourneur explains, FADEC 4 works with the Leap engines powering the Airbus A320neo, 737 MAX and Comac C919, as well as with the GE Passport engine used on the Bombardier Global 7000, 7500 and 8000. The FADEC Alliance is also developing the GE9X FADEC, which will be used on the Boeing 777X.
According to information published by Safran, FADEC 4 has 10 times the computing power of the previous generation, FADEC 3. “The next generation of engine, [Revolutionary Innovation for Sustainable Engines (RISE)], will require five times more computing power than FADEC 4,” Letourneur says.
She says FADEC 4 also contributes to engine performance by decreasing fuel consumption by 15%. “Safran Electronics & Defense has delivered more than 12,000 FADEC 4 units since 2016,” she says. “This is the fastest commercial engine control production ramp-up in our history, and now we are facing a second ramp-up following the COVID crisis.”
Letourneur adds that diagnostic/prognostic features for the FADEC and the engine “have significantly increased” on the Leap engines—both qualitatively and quantitatively.
The retrieval of the data, she explains, is mainly performed on the ground, either wired or wirelessly. “Data transmitted during flight through the [Aircraft Communication Addressing and Reporting System (ACARS)] system are usually limited to those parts needing maintenance action at the next stop,” she says.
Letourneur says one of the biggest engineering challenges for FADEC development has been the integration into a single box of 50% more functions with various criticality levels, such as engine control and engine protection functions, as well as engine health monitoring. “This increased functional scope had to be achieved while maintaining the box size and reliability to the same level as for the previous generation,” she says. “This led to the introduction of several new technologies, including multicore processors, distributed architecture, active thermal control and advanced vibration processing.”
To address the technical challenges of the new engines, a technical engineering team has been established within FADEC Alliance to work on the definition and design of future FADEC systems and FAR 33-associated electronics to reduce fuel consumption and emissions. Letourneur says the team’s main goals include: enabling new engine architecture such as open rotor and hybridization; minimizing the system’s weight and footprint; ensuring compatibility with product cybersecurity constraints; managing new engine interfaces; better distribution so that electronics can be placed closer to their function and are easier to integrate, and providing innovative architecture for obsolescence management.
The team also hopes to achieve 100% compliance with the European Union’s registration, evaluation, authorization and restriction of chemicals (REACH) regulation to improve protection of human health and the environment from the risks that can be posed by chemicals.
“In order to mature these technologies and get a good readiness level for a production program, Safran Electronics & Defense will integrate these new functions on the RISE demo program,” Letourneur says. RISE is an open-rotor engine program of CFM International.