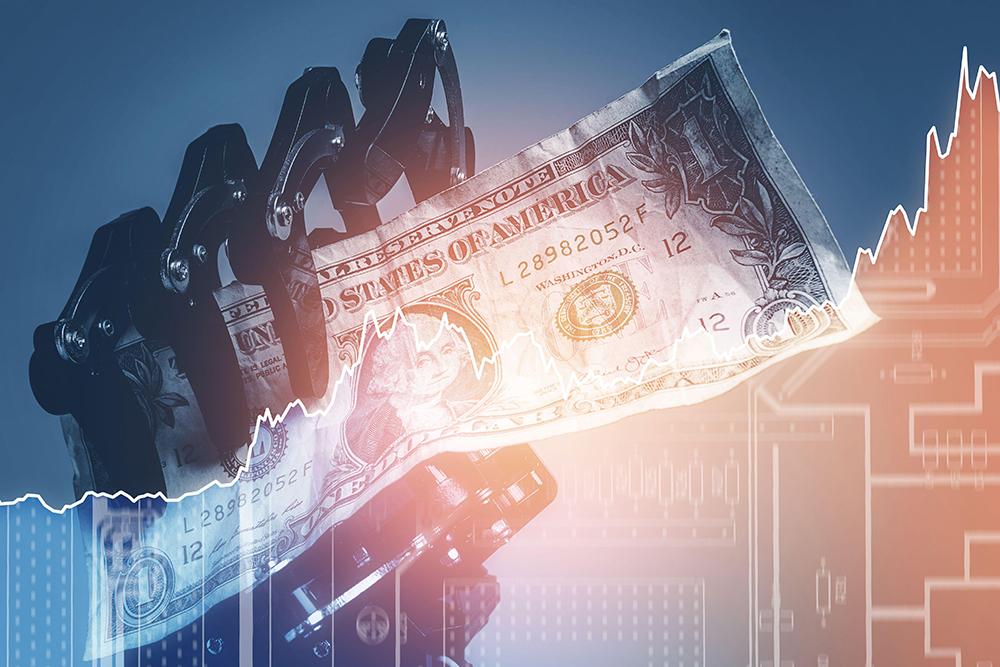
Experts suggest that model-based artificial intelligence technology is becoming increasingly useful in identifying cost savings for MROs and airlines, especially when it comes to the impact of unscheduled events or component fault detection. Running detailed “what-if” simulations for different areas of an organization could enable airlines to be more agile when dealing with unexpected events.
In addition to planning for small or large maintenance activities, model-based artificial intelligence (AI) can be used to plan for unexpected events—and the associated costs that will occur—to better understand the likelihood and severity of variables that could financially impact business.
“Companies can use the technology to examine these issues, identify which scenarios are most likely to occur and help make better business-critical decisions,” Simon Miles, head of AI at Aerogility, tells Aviation Week Network.
For instance, Miles says that if a forecast anticipates aircraft maintenance delays caused by the unavailability of specific spares, users can plan and simulate the best reaction to this scenario by modeling the impact of an increasing or decreasing spares pool to ensure that future operations run smoothly.
Miles says many often-overlooked financial aspects of an operator’s operation can be considered within a model, “For example, needing to negotiate new MRO contracts and being able to visualize multiple offerings to assess the impact on cost and ground time,” he notes.
He also sees companies increasingly leveraging digital and AI technologies to analyze financial uncertainty, contain costs and mitigate the risks in achieving business plans.
Mike Slack, simulation technologist at Ansys, believes simulation, AI and machine learning collectively can make new applications possible. Real data fused with simulation increases the fidelity of the design process and results in a more robust product, he says.
“The learning itself can identify the key design risks that are inherent in a system, allowing for early mitigation,” says Slack.
He also says digital twins of the system linked to functional safety models with causal trees can support fault diagnosis. By refining the understanding of part degradation, Slack says businesses can better plan maintenance and retrofits or redesign assets to extend their lives more cost-effectively.
Rob Mather, vice president of aerospace and defense industries at IFS, sees potential component failures from a predictive maintenance perspective. “You want to avoid a situation where your aircraft goes AOG because it’s flown to a location where you don’t have a replacement part available because this causes immediate issues,” he says.
Data from industry trade association Airlines for America shows that such delays cost an average of more than $100 per minute in the U.S. last year. “There are also costs associated with expedited purchases or shipments or expensive borrowed parts from other airlines, just to get back in the air,” Mather says. “Proactively determining when and where to take a failing component off wing can also help operators optimize maintenance to reduce costs.”