How 5G Connectivity Could Make Aircraft Composite Repairs More Efficient
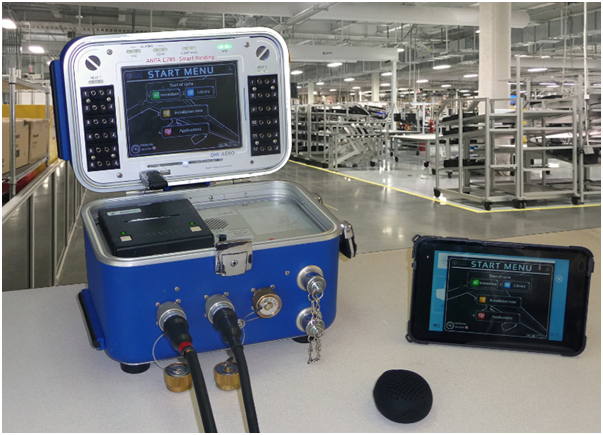
Composite repair specialist GMI Aero has been tapped by a European innovation project to test the use of 5G technology for improving efficiencies within aircraft repair processes. Through the EVOLVED-5G project, GMI Aero will perform research and development by connecting its hot bonder equipment to what it calls the “Industry 4.0 ecosystem” through 5G infrastructures, enabling digitalization of the composite repair process.
According to George Kanterakis, research and innovation director at GMI Aero, sharing of data for quality assurance between airlines, MROs, OEMs and regulatory authorities is necessary to ensure that a composite repair has accurately followed parameters for curing temperature and time to achieve the correct mechanical properties. Currently, says Kanterakis, the process is fairly inefficient.
“Today you do your curing, you send your data to a printer and then you submit at the various levels,” he says. “This takes time, this does not give any room for any intervention online and if the repair is bad you just need to restart.”
In addition to speeding up the process, Kanterakis says the project could help certify composite repairs occurring anywhere in the world—and with different environmental parameters—through the creation of a digital or physical twin.
“Suppose you have an aircraft from a major U.S. airline that landed in Mexico City with damage at the critical part. You need to do a repair, but you have a lot of challenges,” he says, noting that it would be difficult for a composite repair specialist to achieve a good vacuum due to Mexico City’s high altitude and potential humidity. Using 5G technology, the airline could work virtually with an OEM elsewhere in the world to create a physical or digital twin with exactly the same parameters to certify the degree of curing achieved through the composite repair.
The technology will work by connecting GMI Aero’s Anita hot bonders to an application through either 5G or Wi-Fi to provide engineering departments with a real-time picture of equipment and repair processes. Kanterakis says an MRO performing multiple hot bonder repairs at once could keep track of all the relevant parameters and intervene as necessary. “You could have better reporting to prove what you have done by including photos, videos, design data, non-destructive testing data—all that in one report that will go to the quality assurance,” he adds.
Kanterakis also notes that connectivity will enable equipment such as hot bonders to become portable, enabling composite repairs to take place on the apron, which he says has previously been a challenge due to environmental conditions. GMI Aero eventually foresees the connected hot bonder as one piece in an ecosystem of similarly connected equipment to comprise a “factory of the future.”
The EVOLVED-5G project is scheduled to finish by 2023 and Kanterakis says GMI Aero is running several projects in parallel to take advantage of new technology capabilities. One project, called AdaptHEAT, is developing a solution using zonal control to create several independent heating zones tailored to the thermal signature of a part to create a homogenous field, even in complex repairs. Kanterakis says the technology is applicable for components such as Boeing 777 nacelles or Airbus A380 trans-cowls. GMI Aero also plans to have a new version of its Anita hot bonder product available by the end of 2021 that will incorporate new features in light of the EVOLVED-5G research.