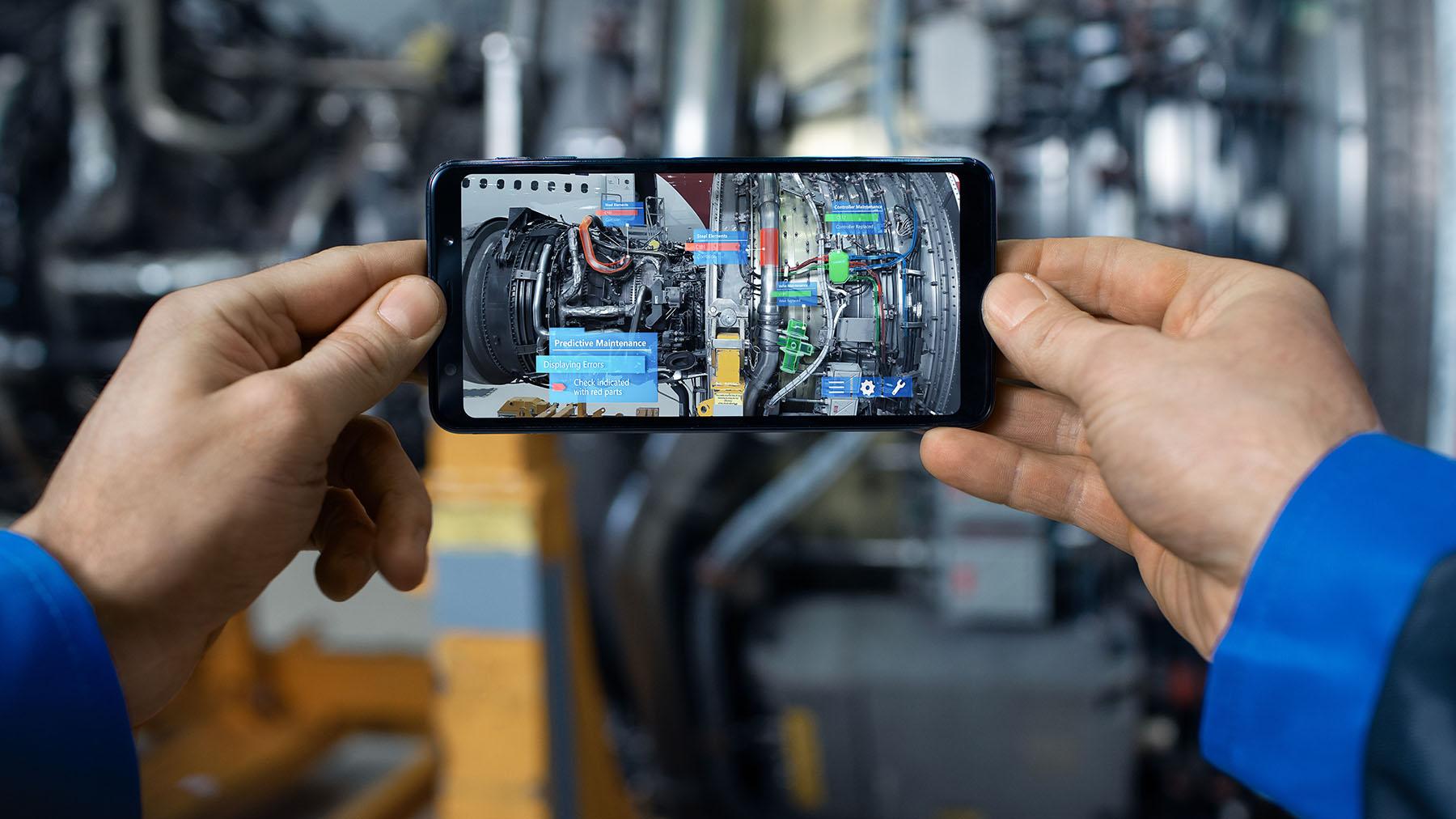
Industrial software specialist PTC is seeing the acceleration of digital trends such as augmented reality (AR) and remote collaboration within aerospace as the world adapts to life during the novel coronavirus crisis. During PTC’s LiveWorx virtual event, the company highlighted ways in which its digital products are being used by aerospace manufacturers and MROs to streamline operations and cope with COVID-19 related challenges.
“I think the COVID-19 world has emphasized where some of this market was already going and it’s been kind of a forcing function,” says H. Brent Baker, VP federal aerospace and defense, PTC. Baker points out that the pandemic has put remote work into overdrive and “it’s also driving us to more remote collaboration—it’s become really paramount.”
A number of PTC’s cloud-based tools were used to help aerospace manufacturers pivot to the production of ventilators as part of the Ventilator Challenge UK initiative. In collaboration with Smiths Medical, PTC used its Windchill product lifecycle management software and its Onshape software—which combines computer aided design with data management and collaboration tools—to design ventilators. The manufacturing process was then captured using PTC’s Vuforia AR software so OEMs such as Airbus, GKN Aerospace and Rolls-Royce could be trained on how to recast production lines for ventilators.
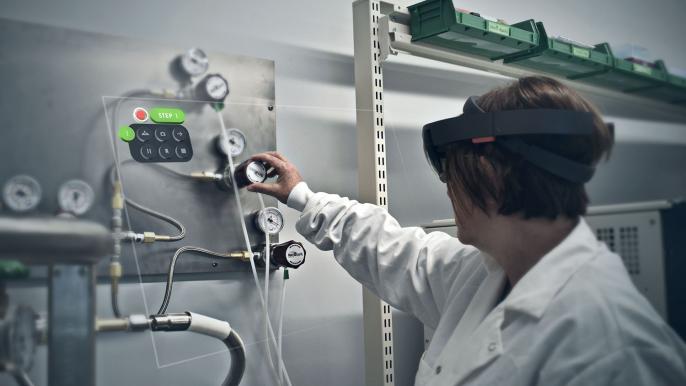
Meanwhile, manufacturers and MROs are using Vuforia to help with remote guidance and training of personnel. According to PTC, more than 500 of Rockwell Automation’s service engineers have used the software to conduct remote service visits with customers during COVID-19 travel restrictions. At Kirtland Air Force Base, the 58th Special Operations Group has used the AR software paired with the Microsoft HoloLens to capture heavy maintenance processes for CV-22 Osprey aircraft that can be used for training technical personnel.
“I think the greatest challenge is just getting folks to have the willingness to accept these new types of training processes and procedures. I think there’s some hesitancy because of fear of the unknown, but our experience tells us that it’s relatively easy to do,” says Baker, adding that younger workers who are more used to new technologies may even come into the work environment expecting these types of innovations.
According to a recent report by IBM and Deloitte, more than 120 million existing workers will need to be retrained and reskilled in the next 36 months. Baker points out that the rapidly aging workforce paired with new social distancing requirements will accelerate the need for new tools and techniques when it comes to training or reskilling technical staff. “Not only are we going to have to train new folks coming into the workforce, but now we’re going to have to train folks that are already there—that are maybe the experts—because they’re going to be working in new, socially distanced environments,” he says.
The pandemic has also created challenges within the supply chain and MRO industries that Baker says can be managed through the use of digital technologies. During a LiveWorx virtual session about extreme supply chain disruption during COVID-19, Ed Wodarski, a service supply chain expert and fellow at PTC, noted that customers have seen a 150% increase in lead time due to more sparsely staffed warehouses and resource shortages. Wodarski says PTC’s Servigistics software for service parts optimization can be used to better predict demand forecast and “position those chess pieces of inventory in the best fashion.”
“[COVID-19] has really illustrated how vulnerable the supply chain really is,” says Baker. “You really need an advanced spare parts planning capability so you can best understand what your demand requirements are, where those parts are coming from globally and how to best position those parts day-to-day in a crisis.”
Baker also believes Internet of Things (IoT) capability will play a key role in how MRO will function post-coronavirus. In addition to tracking inventory with tools such as Servigistics, an MRO could use an IoT platform such as PTC’s ThingWorx to remotely monitor smart assets such as tools, sensors and machines. MROs such as Lufthansa Technik are already using ThingWorx to create a connected shop floor for real-time asset health monitoring and predictive maintenance.
During an industry downturn where airlines and MROs are doing everything they can to save money, Baker says moving from a time phased-maintenance schedule to a condition-based maintenance schedule will be crucial. According to PTC’s LiveWorx session on digital transformation for maintenance, analyst firms Oniqua and ARC Advisory Group determined that 30% of maintenance activities are carried out too frequently. Additionally, the analysts determined that 40% of scheduled maintenance costs are spent on assets with negligible effect on uptime failure.
According to Baker, the ThingWorx IoT platform could be used to transition to condition-based predictive maintenance. “Once you’re able to do that, you’re going to be repairing and ordering the right parts, and you’re going to be able to cut down on excess ordering—which happens all the time today—and the savings are almost unlimited,” he says.