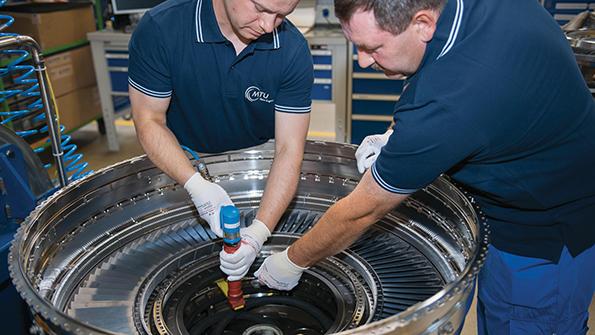
Engine maintenance has been the hardest-hit sector of the aftermarket during the COVID-19 pandemic. As the biggest-ticket maintenance items, engine overhauls immediately were in the firing line as airlines sought to slash costs and preserve cash. It also has been relatively easy for airlines to adopt this tactic—grounded aircraft and limited demand meant shop visits could be delayed, while remaining operations could be sustained by green-time engines and those with the longest remaining service intervals.
Major engine MRO providers saw revenues fall by roughly half in the first year of the pandemic. But after those dark days, there is significant optimism about a recovery as flights, especially of narrowbody aircraft, rebound in many key markets. But airlines must weigh pressures to rapidly scale up their operations to meet pent-up demand with the need to protect balance sheets weakened by almost two years of cash burn.
Short Change
One solution is to pursue alternatives to full engine overhauls, which are expensive and take engines out of service for long periods. Over the last two years, there has been evidence of this trend as airlines specified more limited workscopes for the shop visits they did perform, a tactic that is continuing this year.
“In the course of 2021, we [saw] a slight decrease of workscope in shop visits,” said Safran CEO Olivier Andries during a February 2022 earnings call. “The airlines have been basically, on average, pushing to the right [delaying] . . . the LP [low-pressure] side of the shop visit, the fan typically and sometimes the LP turbine.” Andries also said that while Safran expects airlines to catch up on such work eventually, this correction will not occur this year.
As well as lighter workscopes, airlines can take advantage of the modular nature of modern turbofans and swap out individual modules to achieve desired performance restoration of entire units. Such module changes are far cheaper than full overhauls and can be performed in a small fraction of the downtime required for an overhaul.
“This [module change] process takes 5-15 days maximum, can be accomplished at many more shops (as they need less capability) and exactly replicates the end result of the traditional overhaul in a shorter time and at much less cost,” says Sam Hammoud, head of The Module Factory business unit at FTAI Aviation.
Many airlines are taking advantage of such benefits as they seek to ramp up capacity quickly in response to the loosening of coronavirus-related travel restrictions.
“Demand [for module changes] has increased greatly since mid-2021 with the gearing-up back to capacity of the world fleet, and it will continue to be used as balance sheets are rebuilt,” comments Greg Macleod, CEO of London-based CFM56 repair shop GT Engine Services. He notes that of the three major CFM56 modules—the fan, core and low-pressure turbine (LPT)—demand is highest for LPT changes.
“The cost and time savings are huge: A simple module change could see an engine refitted to the aircraft within a week and at 5-10% of an overhaul cost,” he says.

When to Choose Module Change
The coronavirus pandemic caused many airlines to reassess their fleets and accelerate their transition to new-technology aircraft, often by retiring, returning or selling older models. Current geopolitical events may lead to an acceleration of that trend as fuel prices spike in response to sanctions on Russia.
This presents a dilemma for certain operators, as the cost of a full overhaul may be justified by the reduced time a current-generation engine, such as a CFM56 or an IAE V2500, is due to stay in service. Together, these two narrowbody engines will account for $14.2 billion in MRO demand and 3,200 shop visits this year, rising to a peak of 4,000 shop visits and $18.5 billion in 2025, according to the latest Aviation Week Network Commercial Aviation Fleet & MRO Forecast.
Traditional engine overhauls often occur when some of a module’s life-limited parts (LLP) are nearing or at the end of their designated service lives. The engine then goes to a major overhaul shop to remove the module and fully tear it down to replace its LLPs. The module then is rebuilt and reinstalled as part of a process with a turnaround time of 3-6 months. As this work proceeds, MROs typically pass significant cost risks to customers through exclusions.
“A traditional overhaul targets the entire engine to achieve a minimum build goal,” notes David Moreno, chief operating officer of FTAI Aviation. “As a result, this often forces overhaul on modules that still have useful life remaining but do not meet the target build. Typically, that remaining life is wasted.”
Macleod explains that module changes avoid such wastage. “There are many cases where a module change would be advantageous to a full overhaul—the most common reason would be to change certain LLPs and leave the rest of the engine undisturbed.”
Another potential downside of a full overhaul is the MRO provider may identify additional, unforeseen maintenance to perform on the engine, further widening the cost gap between an overhaul and a module change.
“Module exchanges are transacted at fixed pricing, which is lower than an overhaul and with zero exclusions—no maintenance is required aside from installation,” Hammoud says.
Moreno adds: “In addition to being faster and more cost-effective, module exchanges eliminate the risk of budget exceedances typical to overhauls that are caused by higher scrap rates or unexpected findings.”
An additional reason for a full overhaul might be performance restoration of the engine’s core. “This can occur at different times in an engine’s life depending on operating regime and environment,” Hammoud says.
For a performance restoration of an engine’s core module, overhaul customers typically select a target life for the next run, and any other module with useful life remaining below the target then undergoes a traditional overhaul, which, again, can be avoided via a module change.
In the Field
FTAI Aviation reports it has traded 65 engine modules—mostly fan and LPT sections—since April 2021. Of these, fan module changes were accomplished on wing in a couple of days, while the LPT can be swapped out “near-wing” in 10-15 days, according to Moreno.
“Most customers are largely accomplishing module exchanges in the field or hospital [light-duty MRO shop] environments. Others are performing exchanges during a shop visit where the core module of the engine is overhauled,” he adds.
One such customer is Lufthansa Technik, which in February subcontracted FTAI to provide module exchanges as part of a seven-year CFM56 engine maintenance program the German MRO provider has won from Canadian carrier WestJet.
“In subcontracting a third-party supplier like FTAI, we are confident that we will be able to provide a high-quality and reliable product at a competitive cost,” said Georgios Ouzounidis, vice president of corporate sales for the Americas at Lufthansa Technik. “One major pillar in our collaboration is that we will be able to, where appropriate, further optimize an engine’s life.”
The feedstock for FTAI’s module inventory is its portfolio of more than 300 CFM56 engines. “The replacement modules we offer were removed from engines with plenty of life remaining and inspected to certify that they are airworthy prior to sale,” Hammoud says.
Modules that FTAI removes are serviced and maintained by its MRO partner, Lockheed Martin Commercial Engine Solutions in Montreal. GT Engine Services, meanwhile, uses its own network to source modules.
“We have access to partners that we purchase modules from, some of which we hold on consignment, and have our own overhauled or repaired,” Macleod says.