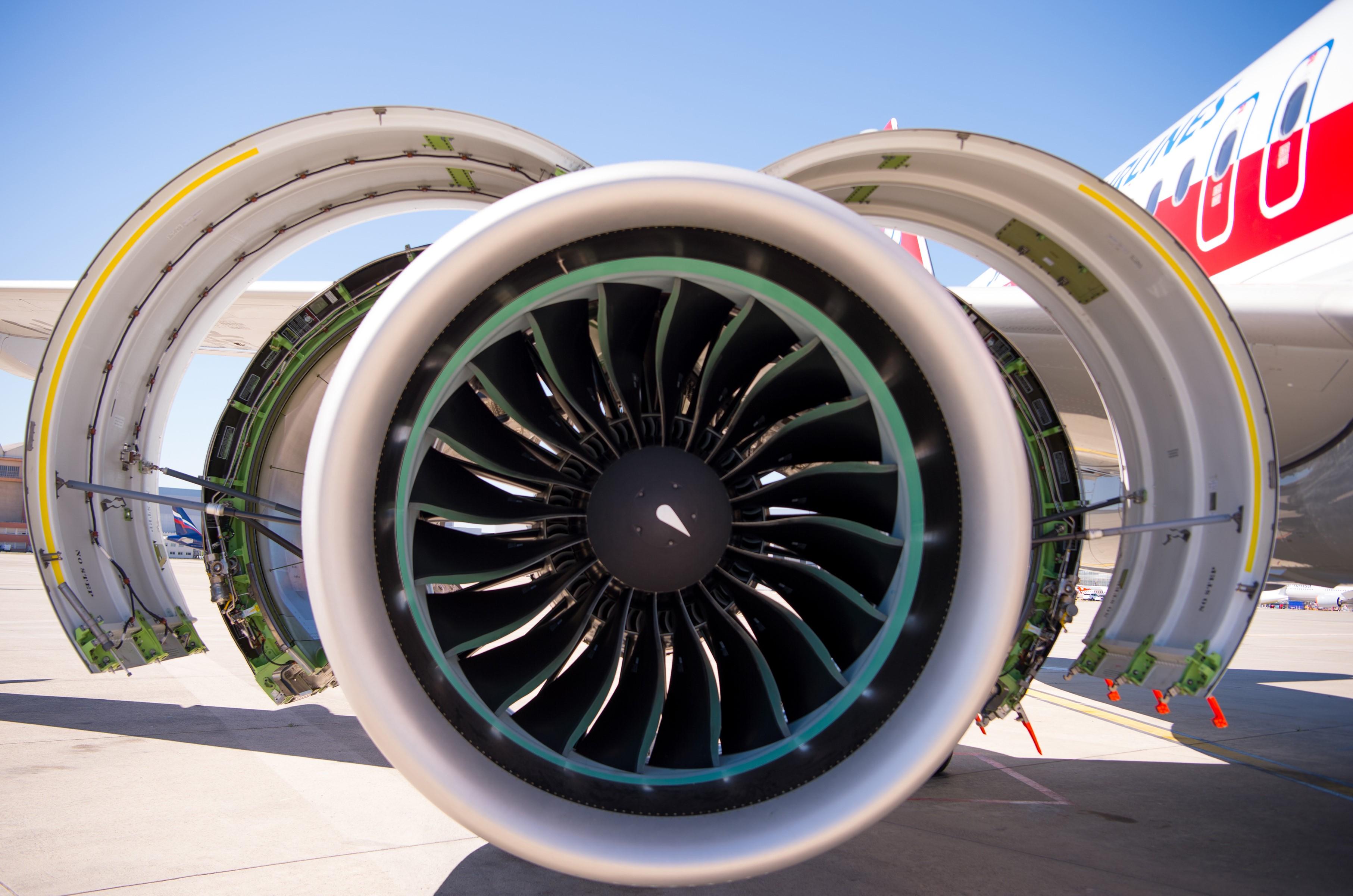
Credit: Airbus
Some Pratt & Whitney PW1100G engines undergoing required checks for cracking in certain parts are getting new, full-life components installed during the visits, and the company is on track to swap out more of the defective parts as checks progress. Chris Calio, president of Pratt parent RTX, said...
Subscription Required
This content requires a subscription to one of the Aviation Week Intelligence Network (AWIN) bundles.
Schedule a demo today to find out how you can access this content and similar content related to your area of the global aviation industry.
Already an AWIN subscriber? Login
Did you know? Aviation Week has won top honors multiple times in the Jesse H. Neal National Business Journalism Awards, the business-to-business media equivalent of the Pulitzer Prizes.