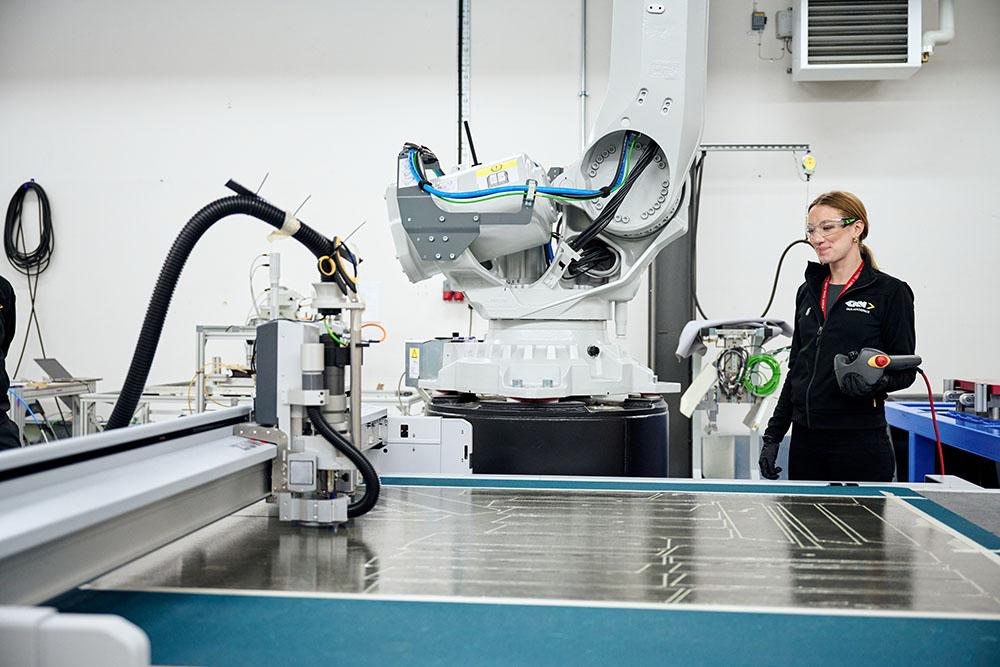
GKN Aerospace hopes new digital factory processes will improve its aero-engine manufacturing capabilities at its facility in Sweden.
In September, GKN announced plans to increase the capacity and efficiency of the facility in Trollhattan, Sweden. The facility covers a wide range of engine components, from the design and manufacturing of intermediate cases and compressor exhaust cases for civil and military aircraft engines to turbines and nozzles for the most advanced space rockets.
“Our Trollhattan facility is also a center of excellence for engine parts repair and a leader in laser-wire deposition additive fabrication technology,” Joakim Andersson, president of GKN Aerospace’s engines business, tells Aviation Week Network.
The new digitized processes include GKN’s proprietary Copilot (Connected, Optimized, Predictive, Integrated Lifecycle Operations Technology) system, which it currently uses to monitor and maximize machine uptime with plans for further development. The application in aero-engine manufacturing refers to an advanced approach that combines digital tools, data analytics and intelligent systems to improve the design, production and maintenance of aerospace engines.
According to Andersson, digitized processes also include a suite of other enterprise resource planning and product lifecycle management systems to ensure the process is operating at optimal efficiency.
Once fully operational in 2026, a new production area under development in Trollhattan will utilize the latest digital processes to support the ongoing global aerospace ramp-up.
GKN estimates suggest the backlog for aero-engines is up to nine years and the planned expansion will support the increasing demands for powerplants such as the General Electric GEnx, Pratt & Whitney Geared Turbofan and Rolls-Royce Trent XWB.
“We are a risk- and revenue-sharing-partner in 19 engine families, all at different stages of maturity,” says Andersson. “This gives us outstanding balance and strong relationships with all major engine OEMs.”
Andersson continues: “As a full partner in these programs, we provide core design and technology for improved engine capabilities throughout the life span of each of these engines.”
In the current climate, any expansion must tie in with sustainable responsibility. Specific to its engine business, GKN announced a £50 million ($63 million) investment in new additive fabrication capabilities in Trollhattan earlier this year.
Additive fabrication—which involves creating parts and components layer-by-layer, typically using 3D printing technologies—is spurring significant advances in aerospace manufacturing. Unlike traditional methods, additive fabrication accumulates material only where it is required, which creates efficiencies in producing aerospace components.
GKN’s usage of additive technology utilizes metal wire or powder fused together with lasers, which it says minimizes raw material waste, energy usage and shipping, significantly cutting emissions, costs and lead time.
Increasingly, additive fabrication is regarded as a potential solution to meet the industry’s challenges related to quality assurance and scale. For instance, GE Aerospace uses additive manufacturing for jet engine fuel nozzles and Airbus uses it to produce cabin components, brackets and structural parts.