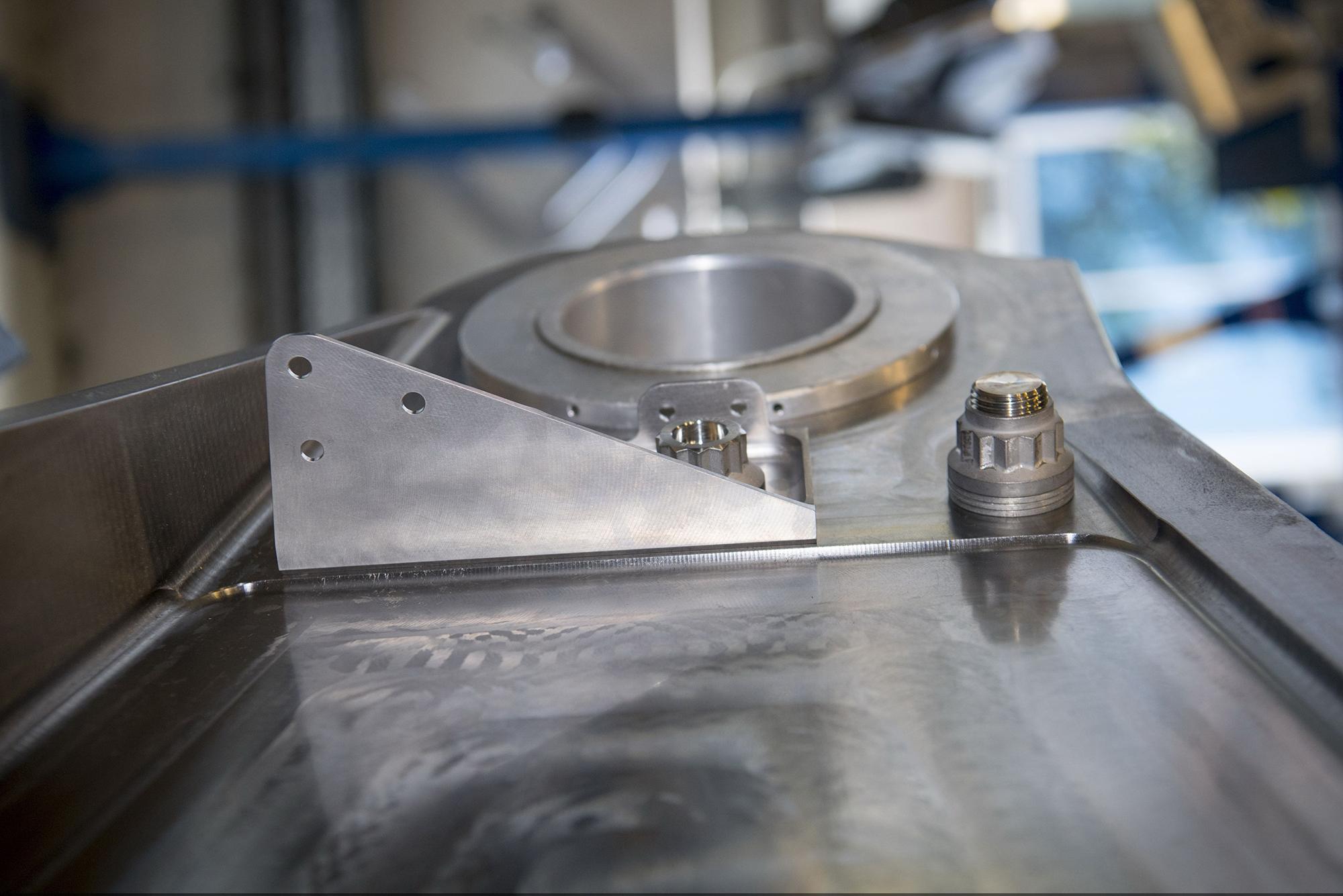
Airbus will expand its use of 3D printed polymer cabin interior components through a contract extension with additive manufacturing specialist Stratasys. The contract extension will increase the range of aircraft types supported by 3D printed parts and move into the use of additive for MRO applications.
The initial contract between Airbus and Stratasys, dating back to pre-2015, focused on 3D printing of production parts for the A350 as an alternative to traditional manufactured parts to increase supply chain flexibility. The OEM has since printed more than 1,000 flight parts for use on the A350 XWB using Stratasys FDM (fused deposition modeling) 3D Production Systems. According to Stratasys, Airbus progressed from 3D printing alternate parts to using the technology for serial production of parts.
Through the new contract extension, Airbus will now 3D print parts for additional aircraft types, such as the A300, A320, A330 and A340. While Airbus is not commenting on specific parts it plans to print, Stratasys notes that the expansion will likely include low criticality parts similar to those printed for the A350.
The contract extension will also include replacement and spare parts for MRO through Airbus subsidiary Satair. Although Satair is not commenting on specific replacement and spare parts it plans to print, the aftermarket specialist has been exploring the additive manufacturing segment for approximately five years now and has certified hundreds of 3D printed parts and tools.
The companies are not disclosing specific details about the contract’s value or length, but Stratasys’ aerospace lead, Scott Sevcik, says the contract will essentially double its time with Airbus.
“I think what’s exciting now, many years after we’ve started this, is additive FDM in particular is no longer special. It’s not a technology that’s being driven as an experiment anymore. We interact with procurement just as any other supplier would,” says Sevcik. “Five years ago, it was big news when there was one part going on an aircraft or one small activity that was taking a step forward. In 2021 it’s becoming regular business.”
In addition to its contract extension with Airbus, Stratasys recently introduced a new carbon fiber filled ABS (acrylonitrile butadiene styrene) material for its F123 Series printers, which Sevcik says are available at a much lower entry price point, making them ideal for offices and shop floors. Stratasys says the new material is 15% stronger and more than 50% stiffer than standard ABS while being lighter weight than metal, making it a compelling alternative to metal parts.
“With having the carbon fiber ABS on a more accessible platform, we expect our aerospace customers in particular to be using it much more extensively within the jigs and fixtures space in particular,” he says. “We use a ton of ABS today within aerospace for those applications—the shop floor tooling applications—and being able to bring a material that has that level of stiffness into those applications is a really exciting next step.”