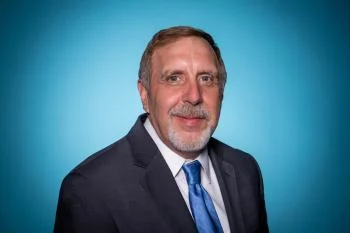
American Airlines operates four base maintenance locations—in Tulsa, Oklahoma; Dallas, Texas; Pittsburgh, Pennsylvania; and Charlotte, North Carolina. Some maintenance work at three of them is shifting. Greg Emerson, American Airlines’ vice president of base maintenance and facilities, describes the changes.
Please describe the base maintenance shifts at American Airlines’ facilities in Tulsa, Oklahoma.
Last year, we added 300 people to our Tulsa, Oklahoma, facility, primarily to grow our CFM56 engine maintenance capacity. This week’s announcement is not about adding capacity: we’re already doing [Boeing] 737 and widebody heavy maintenance in Tulsa. But the maintenance cycles change over the years—some years you might have higher demand for Boeing 737s and others for 787s. So, we move the mix of airplanes between bases or external vendors depending on the airline’s needs. But in this case, we’re actually adding one additional 737 overhaul line in Tulsa in 2025, as well as bringing a 787 heavy maintenance check line back to Tulsa. Tulsa had done 787s before, but then we loaded up Tulsa with more 737s to maximize our capacity there. We’re now seeing the volumes start to shift again. That’s one reason we’re adding 227 aircraft maintenance technicians, who will be working on those aircraft. The other 100-plus new hires will support the aircraft’s backshops—such as seats, galleys, lavs and composite repair—as well as engineering, supply chain, planning and management.
What maintenance work is changing in Charlotte and in Pittsburgh, where American is adding 133 and 44 maintenance positions, respectively.
It’s more like chess moves in Pittsburgh and Charlotte. Over the last three years, we’ve grown Charlotte. We’ve added headcount there the last two years, really to reset its mission to do Airbus A320 C11 checks, which are mid-checks between line maintenance and full overhauls. They take about 10 days to accomplish.
Pittsburgh was well suited to do those, so its hangars are full running three C11 lines right now. What we’re doing is bringing an A320 heavy check line from a vendor to Pittsburgh, which displaces a C11 line, which will shift to Charlotte. That will require us to add 100 people to Charlotte.
Which vendor lost the work?
We still have the same vendor network—and the same volume—we’re just shifting some things around to better support the volume of maintenance activity that we have. It’s really about making sure we maximize our internal capacity and leverage the resources that we have because we do have an advantage of reducing the overall span times of those checks internally, versus some of our vendors. We’re able to turn the airplanes faster with higher reliability. In my role, I need to ensure we have the right work and the right location, but also make sure we’re focused on the operational demands of the airline for the future—and managing it as efficiently as we can.
What percentage of base maintenance does American perform internally?
We do 60% on average in our peak base maintenance season. In the summer or over the holidays we don’t do much because we want every asset flying. So there are about nine months of the year that we’re running heavy and lighter checks.
The labor market is tight. How difficult is it going to be to hire those 500 people?
We don’t have a problem. Honestly, we really don’t. We’ve hired in Pittsburgh the last three years and we had no problem getting the resources that we needed. We hired 300 in Tulsa last year and we had no problem meeting the timeline of onboarding employees. We feel confident that we’ll have every one of those employees hired, and hopefully all of them will be onboarded by the end of the calendar year.