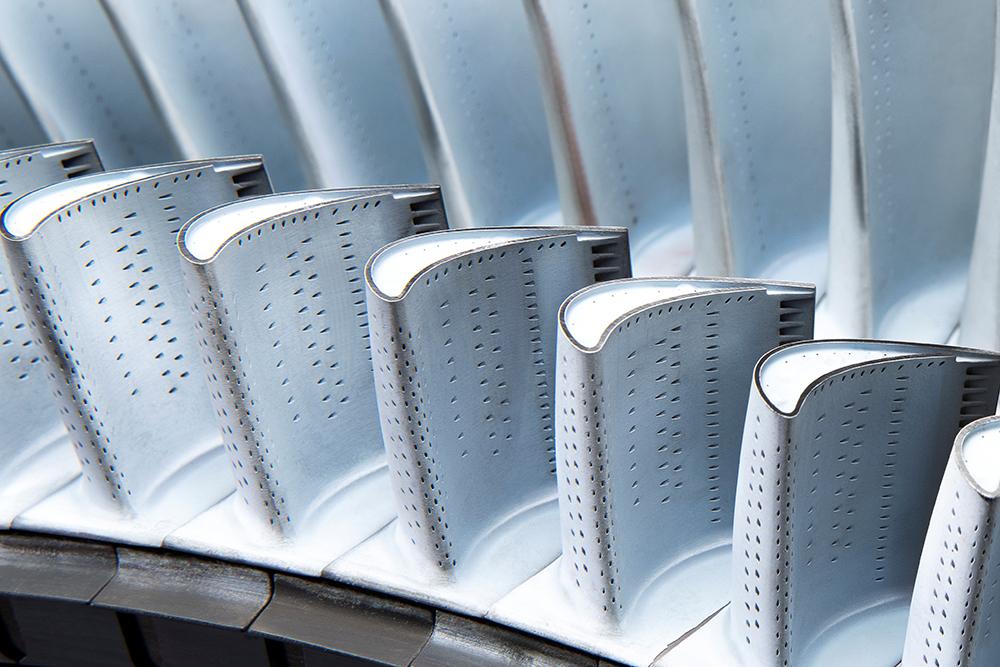
Each new generation of turbofan has offered improvements in fuel burn as well as technological advances in materials and design.
Yet while we may hear about higher bypass ratios, new gear systems and innovative composite parts, very little is said about the coatings that underpin the function of each.
This is an oversight, since without specialized coatings, modern turbofans couldn’t offer the same performance or reliability, while even the hardiest materials would degrade quickly under the huge temperatures and pressures within them.
The importance of these functions was demonstrated in late 2021 when Pratt & Whitney unveiled GTF Advantage, a new production standard for the PW1100G that will deliver greater power and 1% better fuel burn.
At the heart of technology improvements for the Airbus A320neo-family engine were new coatings and optimized blade tip clearances, Pratt said.
An improved protective coating was also a major part of Rolls-Royce improvements to the troubled early generations of Trent 1000 engines. As a result of pollutants reacting in the hot section, these engines had suffered from sulfidation of the intermediate-pressure turbine blade, a problem the OEM rectified with a new protective coating to improve durability.
“Coatings are considered a critical technology when optimizing the overall performance of today’s engines and they are becoming even more essential as advanced engine designs evolve,“ notes Leo Buchakjian, aviation business development manager at Praxair Surface Technologies.
The use and complexity of coatings have increased with each new generation of engine, explains Stefan Schneiderbanger, head of coatings at MTU Aero Engines.
“Increased pressure and temperature ratios designed to increase gas turbine efficiency and reduce environmental impact require higher-performance materials that, in turn, have higher coating requirements—both in terms of material and process.”
For an in-depth look at aero-engine coating technology, see the forthcoming Inside MRO.