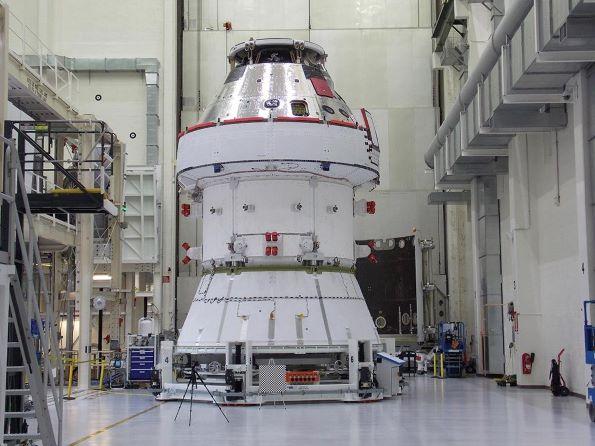
When Congress directed NASA to develop a new transportation system capable of flying astronauts into deep space, the hope was that recycling engines and other hardware from the space shuttle program would quicken the pace of development.
That proved to be wishful thinking. But after more than a decade of development, the first Space Launch System (SLS) rocket—a two-stage behemoth that rivals the lift capacity of the Apollo-era’s Saturn V—was rolled out to the Kennedy Space Center’s Launch Complex 39B and prepared for liftoff.
- Plans call for 42-day shakedown cruise
- Heat shield designed for Mach 32 reentry
“We’ve proved the propulsion system design is really good,” John Shannon, vice president and SLS program manager with prime contractor Boeing, tells Aviation Week. “What we haven’t done—and of course you can’t do this until you launch—is test in the combined-effects environment, such as going through the highest dynamic pressure and having the acoustic energy of the solid rocket boosters.
“You qualify your hardware on vibration tables and on other things so you can show that they can survive, but you don’t really know until you actually launch and go through the ascent environment,” he adds. “So this is very much a test flight.”
For its debut, the SLS will attempt to send a 53,000-lb. uncrewed Orion capsule on a trajectory that is intended to bring it close enough to be captured by the Moon’s gravity. Orion is aiming for what is known as a distant retrograde orbit, which is a highly stable, elliptical path 62-40,000 mi. from the lunar surface that requires little fuel to maintain. “You get this really nice long checkout period of all the spacecraft systems around the Moon without having to expend a lot of propellant to stay there,” says Debbie Korth, Orion program deputy manager at NASA’s Johnson Space Center.
The spacecraft will travel around the Moon in the opposite direction of how the Moon revolves around Earth. At its most distant point, Orion will travel some 30,000 mi. beyond where the Apollo 13 astronauts flew in 1970, the current record for the most distant human spacecraft.
The primary goal of the mission, known as Artemis I, is to test the ablative heat shield that will protect the Orion spacecraft during its Mach 32 reentry into Earth’s atmosphere. “We want to demonstrate [the shield] can withstand the high speed and high heat that Orion will encounter when it reenters the atmosphere,” says NASA’s Artemis I Mission Manager Michael Sarafin.
“No aerodynamic or aerothermal test facility can recreate the conditions that we will see from lunar return conditions,” he adds. “So validating the heat shield is our primary objective and a critical activity . . . before we fly crew on Orion on the very next mission.”
Orion’s heat shield is made of a material known as Avcoat, which is a reformulated version of material used on the Apollo capsule. The 16.5-ft.-dia. shield—the largest of its type—is designed to handle temperatures of nearly 5,000F, which is about half as hot as the Sun.
For Orion, blocks of ablative Avcoat, manufactured at NASA’s Michoud Assembly Facility near New Orleans, are shipped to the Kennedy Space Center and machined into 186 unique shapes, which are then applied to the heat shield’s titanium skeleton and carbon-fiber skin. Gaps are filled with an adhesive material. Following testing, the shield is coated with white epoxy paint, covered with aluminized tape to dissipate electrical surface charges and bolted to the crew module.
An earlier version of the heat shield was tested during the Dec. 5, 2014, Exploration Flight Test-1 (EFT-1) when an Orion capsule was carried into orbit aboard a United Launch Alliance Delta IV rocket to test reentry and landing systems. “We didn’t get quite the lunar return velocities that we were really looking for,” says Ronny Baccus, Orion spacecraft chief engineer at the Johnson Space Center.
Following EFT-1, the shield was redesigned from a single-piece system to blocks of Avcoat, significantly reducing manufacturing time. In the original design, a fiberglass-phenolic honeycomb structure was bonded to the shield. Each of the 320,000 tiny honeycomb cells were then individually filled—by hand—with Avcoat, inspected with X-rays, cured in a large oven and robotically machined to specific thickness requirements.
“It was very labor-intensive, very time-consuming,” Korth says. “Also, we found the process controls were really difficult to maintain.”
Another reason behind the change was to eliminate some minor cracking that was occurring in the monolithic design. “They were able to repair those, and they performed as expected,” Korth says. “But it wasn’t something we wanted to live with long term.”
Orion’s 24,500-mph return from lunar orbit, targeted for Oct. 10, will provide data that will be compared to analytical predictions ahead of a follow-on crewed Orion flight test, targeted for mid-2024.
“As your velocity goes up, the heating rate goes up even more, so it’s really important for us to get this data point,” Baccus says. “With all the ground-testing we’ve put the system through, plus our EFT-1 experience, we have confidence in the design. But there is that last bit that you only can get in a flight environment at these conditions to demonstrate the margins and the capability.”

Orion’s reentry profile also includes a dip into Earth’s upper atmosphere, which increases the range of reentry trajectories. The so-called “skip entry” is similar to aerobraking, a technique used to adjust a spacecraft’s orbit around Mars and other planets. “I’m not aware of any vehicles that have flown skip entries into Earth’s atmosphere, but there is a lot of heritage behind this,” Baccus says.
For the maneuver, Orion will dip into the atmosphere and use it, along with the lift of the capsule, to fly back out. The spacecraft will then reenter the atmosphere for the final descent under parachutes and a splashdown in the ocean off the coast of San Diego.
The skip entry creates more options for return trajectories, enabling Orion to splash down closer to recovery ships. Apollo spacecraft, which entered Earth’s atmosphere directly, could travel up to about 1,725 mi. before splashing down. The limited range required U.S. Navy ships to be stationed in multiple remote ocean locations.
With skip entry, Orion could fly up to about 5,524 mi. beyond the point of entry, allowing the spacecraft to touch down with more precision. Skip entries also reduce G forces on returning astronauts.
To reach the Moon, Orion was due to lift off as early as Aug. 29 aboard the SLS. Propelled by a pair of five-segment solid rocket boosters—derived from the space shuttle’s four-segment design—and four refurbished shuttle RS-25 main engines, the SLS will lift off with 8.8 million lb. of thrust. That is 15% more thrust than the Saturn V rocket used in 1967-73, the first—and so far only—booster to send people beyond low Earth orbit.
Like the space shuttle ascent profile, the SLS solid rocket boosters, which provide the majority of thrust during liftoff, will burn through their propellant and separate from the core stage 2 min. 12 sec. into the flight. The boosters will splash down into the Atlantic Ocean and will not be retrieved.
Unlike the shuttle, the SLS-Orion stack includes a launch-abort system (LAS) that could carry the Orion capsule away if the launch vehicle fails. When the SLS reaches an altitude of 287,500 ft. 3 min 30 sec. after liftoff, the LAS will be jettisoned. Meanwhile, the liquid-oxygen- and liquid-hydrogen-fueled Aerojet Rocketdyne RS-25 main engines will continue firing for another 4 min. 20 sec. Following engine shutdown, the 212-ft.-tall core stas, leaving the Orion spacecraft attached to the SLS upper stage.
During an orbit of Earth, Orion will deploy its solar arrays while the interim cryogenic propulsion stage (ICPS)—a modified version of the upper stage flying on ULA’s Delta IV rocket—ignites for the first time to raise the perigee of the spacecraft’s orbit.
The ICPS will fire for a second and final time 1 hr. 37 min. after liftoff to boost Orion’s speed to 22,670 mph from 16,840 mph, fast enough to escape Earth orbit.
If all goes as planned, 2 hr. 5 min. after liftoff the ICPS will separate and the Orion spacecraft will continue a solo journey to the Moon. The capsule will use its service module, provided by the European Space Agency, to tweak its trajectory and then put itself into a distant retrograde orbit around the Moon about 10 days after launch.
Meanwhile, the ICPS will undertake a secondary mission: deploying 10 cubesats, which are riding inside the Orion stage adapter, for a variety of science projects and technology demonstrations (see page 54). Eventually, the ICPS will end up in an orbit around the Sun.
In addition to testing Orion’s heat shield, the Artemis I mission will verify the SLS and Orion spacecraft’s communications, propulsion, navigation and other systems through all phases of the flight. “As a human-rated spacecraft, Orion will give us further confidence that it can tolerate the extreme thermal environment of deep space and that we can fly through the Van Allen radiation belts,” Sarafin says.
NASA hopes to retrieve the Orion crew module after splashdown to collect data that was not radioed back to Earth during flight and to practice recovery procedures ahead of crewed flights. Some components, such as the avionics, also are expected to be refurbished and reflown on future Orion spacecraft.
Additional Artemis I objectives include certifying Orion’s optical navigation system, operating onboard technology and biology payloads and collecting imagery throughout the mission.
In addition to a launch attempt scheduled between 8:33 a.m. and 10:33 a.m. EDT on Aug. 29, NASA has backup launch opportunities on Sept. 2 and Sept. 5. If the SLS has not launched by then, NASA will need to return the rocket to the Vehicle Assembly Building (VAB) to retest the battery-powered flight-termination system, as per its agreement with the U.S. Space Force Eastern Range, which provides tracking, safety and other support services for the SLS launch.
NASA received a waiver that extended the period of time between when the SLS flight-termination system is tested—which can only take place in the VAB—and launch. The previously approved 20-day period would have allowed launch attempts on Aug. 29 and Sept. 2 but not a third opportunity on Sept. 5. “Our team went to the range and showed them the qualification data for the batteries, which far exceeded the 25 days,” says Boeing’s Shannon. “They agreed that 25 days was acceptable for this launch period.”
The battery certification issue will be moot once NASA switches to an automated flight-termination system for the SLS, expected for the Artemis IV mission.
Comments