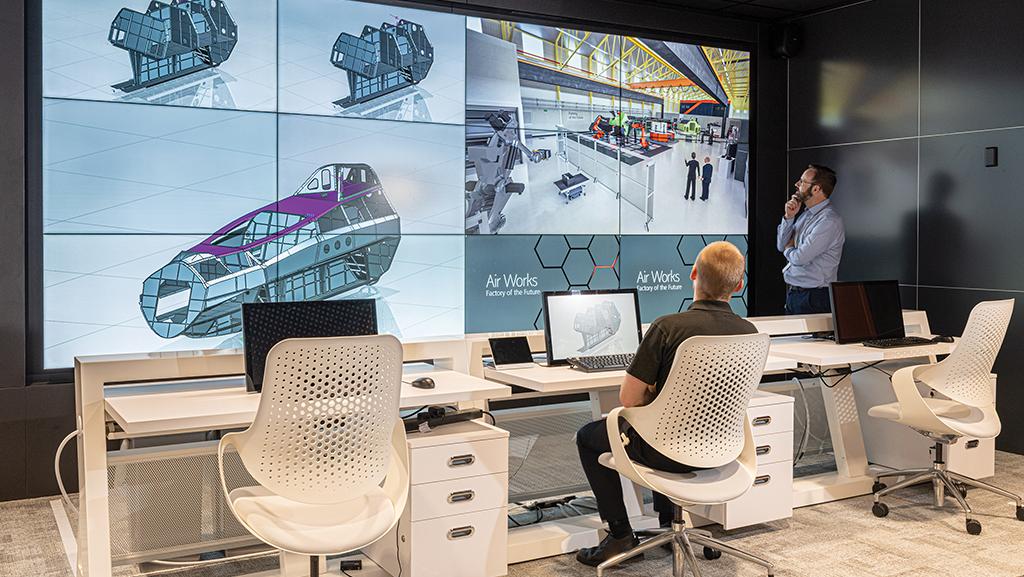
BAE Systems is making investments in new production and assembly technologies to reduce costs and halve the time associated with producing a complex future combat aircraft.
With the target of bringing the British-led Tempest future combat air system to the front line by the mid-2030s and ensuring it can capture a chunk of the export market before the competition is ready, BAE believes it needs to shake up its engineering processes and relations with suppliers as well as connect and digitize the entire through-life process.
- Tempest spin-offs already supporting Typhoon production
- Additive manufacturing to shake up supply base
The company has established a factory of the future at its site in Warton, England, where it has been experimenting with initiatives such as cobotics—whereby robots in reconfigurable cells assist human operators with complex tasks and additive manufacturing of ever larger parts. During the past 12 months, the company has been steadily introducing the technologies into its existing programs, including the Eurofighter Typhoon, as a steppingstone to future programs.
Currently, it can take about 36 months to produce and assemble a Typhoon. An extra 12 months can be added onto that timeline if the supply chain has to be primed in the event of a gap in production to allow for long-lead items such as the production of dies for forging and tools for moldings.
Those long lead times can be as much as 100 weeks using traditional manufacturing methods, says Dave Holmes, manufacturing director of BAE’s Air business. “We want to get that 100 weeks down to 100 days or less,” he notes.
BAE’s vision to pave the way for Tempest production calls for a “completely connected end-to-end environment from requirements, engineering, supply chains, production systems to support upgrades and enhancements,” Holmes says. Data and analytics would underpin the system, he adds. At its backbone would be open-architecture systems that could take advantage of new technologies as they emerge through the production life of the aircraft.
Holmes notes that the scaling up of capabilities such as additive manufacturing, which previously may have been restricted to producing components tens of centimeters in length, can now produce components that are several meters long.
“Additive will challenge the machining sector’s production of castings and forgings,” Holmes says. Subtractive manufacturing processes will still be needed for a future aircraft but will “become the exception rather than the rule,” he says, as additive takes on a greater role.
These technologies will “force a different relationship with suppliers,” Holmes says. “The connected world will make that relationship with suppliers more intimate, less transactional.”
The capabilities demonstrated at BAE’s facility are providing evidence for upcoming year-end submission of the business case to the British government to take the Tempest acquisition program from the current concept phase into the assessment phase in 2021. But in line with the UK Combat Air Strategy—which calls for the technology developed by Team Tempest through the Future Combat Air System Technology Initiative to spin off enhancements for platforms such as Typhoon—the factory of the future initiative is helping to streamline production of both the Typhoon and the Lockheed Martin F-35.
For the Typhoons being exported by Italy to Kuwait, BAE has supplied additive-manufactured ducting for the cooling of the active, electronically scanned array radars. Metallic 3D-printed parts are being used in the structure of the Typhoons supplied to Qatar. “This is helping us gather more evidence for the submission to our customer to show the potential of these technologies, approaches and processes with real data,” Holmes says.
In the coming months, the company will work on a full-scale fuselage section of the notional Tempest design. Holmes says the company had planned to do this earlier in the year, but the plans have been affected by the novel coronavirus pandemic. The structure is designed and component parts have been released for manufacture.
The first subassemblies are due to be completed in September using smart benches developed in conjunction with the University of Sheffield’s Advanced Manufacturing Research Centre. The benches deliver tailored cues and instructions to workers assembling parts and can be adapted for assembly of different components. BAE has also teamed up with aerospace automation firm Electroimpact to enhance the accuracy of off-the-shelf robots to deal with the precise tolerances required for military aircraft.
Although the company was the first in the Eurofighter consortium to boast the use of laser alignment in the assembly of the fighter, BAE is now experimenting with optical projection systems with real-time measurement feedback to assemble the Typhoon’s vertical stabilizer. The company is also in the process of rolling out technology for the F-35. Additionally, optical projection is being used on aircraft skins to provide information to workers on the size of a fastener for a particular section.
Comments