Winter Ops: Freezing Temps, Precip Can Have Serious Consequences
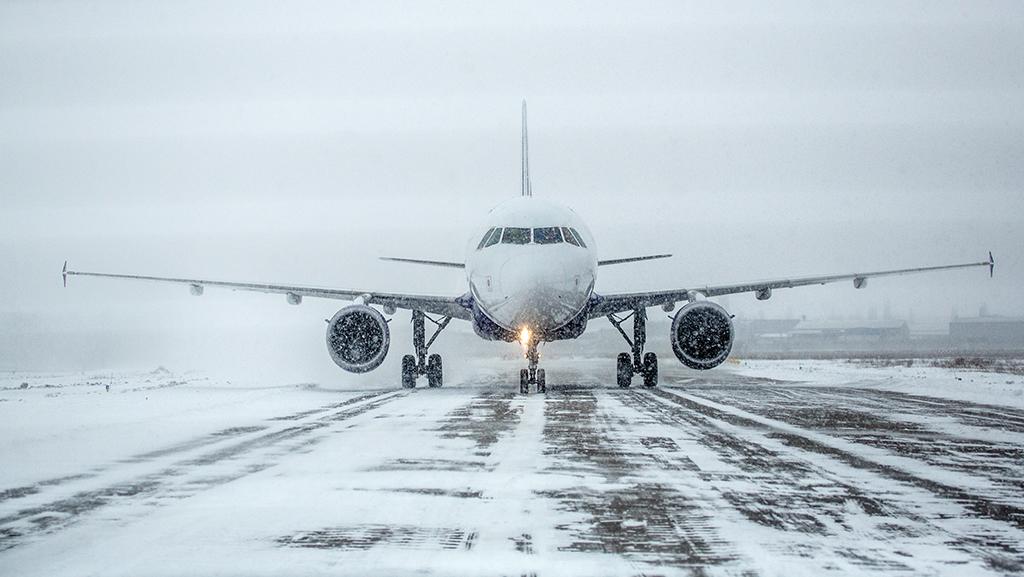
Ground operations in the winter create a large number of threats that can cause serious damage to an aircraft. Some of these are adequately addressed in operating manuals and recurrent training, but there are other conditions that are not covered which can lead to expensive damage.
For example, while the consequences of failing to properly deice an aircraft’s lifting surfaces that are contaminated by frozen precipitation are generally well understood, the susceptibility of jet engine components to contamination by ice during ground operations can catch a flight crew by surprise.
Consider the situation in which you are dropping your principal at Colorado’s Aspen-Pitkin County/Sardy Field (KASE) for a ski holiday and then you are asked to reposition to Grand Junction Regional Airport (KGJT). If the weather on the approach into Aspen required the use of engine anti-ice, then your engine inlets will be warm during the initial portion of your turnaround on the ramp. And if the weather included frozen precipitation, it is possible for snow to be blown into the engine inlet. Upon contact with the warm engine inlet surfaces that snow will melt and drip down to the bottom of the inlet. Depending on the outside air temperature and length of ramp time, those metal surfaces and the liquid can then freeze. It only takes a small amount of ice at the bottom of the inlet to prevent rotation of the engine fan blades.
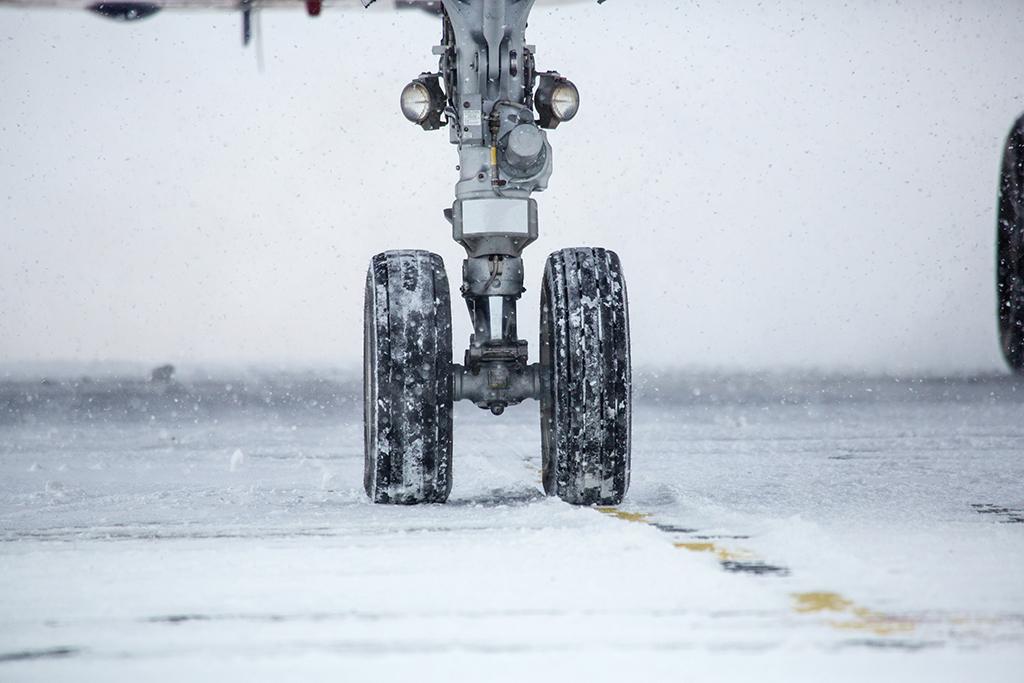
Unfortunately, a frozen fan can result in expensive engine damage if a start is attempted. During the start sequence, the N-2 (i.e., “high pressure”) shaft is free to turn, but the fan will not. If fuel is then introduced without sufficient airflow, temperatures in the combustion section will quickly soar, impacting the hot section and requiring serious maintenance action. The duration of the over-temp as well as the over-limit temperatures are important to note since those will dictate the post-incident inspections and the maintenance necessary.
As pilots we have been instructed to verify the engine cowl and inlet are clear of ice and snow, and the fan rotates freely during our walk-arounds. This is not easy on many business jets, particularly in the case of high-mounted engines. Attentively monitoring the engine-start process is equally important. “Catching” the lack of fan rotation early in the sequence before introducing fuel and aborting the start before engine temperatures begin to rise will minimize any problems.
Engine Icing During Ground Operations
Additionally, blowing snow, freezing precip or fog, slush, ground contaminants or even airport snow removal operations can cause contamination on many other turbofan engine components. Even after engine-start it is possible for snow and slush to accumulate within the intake ducting as well as on the rear surfaces of compressor/fan blades during ground operations when there is moderate to heavy freezing precipitation. That ice may affect the aerodynamic performance of the blades severely and cause compressor stall, engine surging and engine malfunctioning, and reduced thrust. (Reference: EASA Safety Information Notice No: 2008-29 [Issued April 4, 2008] “Ground De-/Anti-Icing of Aeroplanes; Intake/Fan-Blade Icing and Effects of Fluid Residues on Flight Controls”)
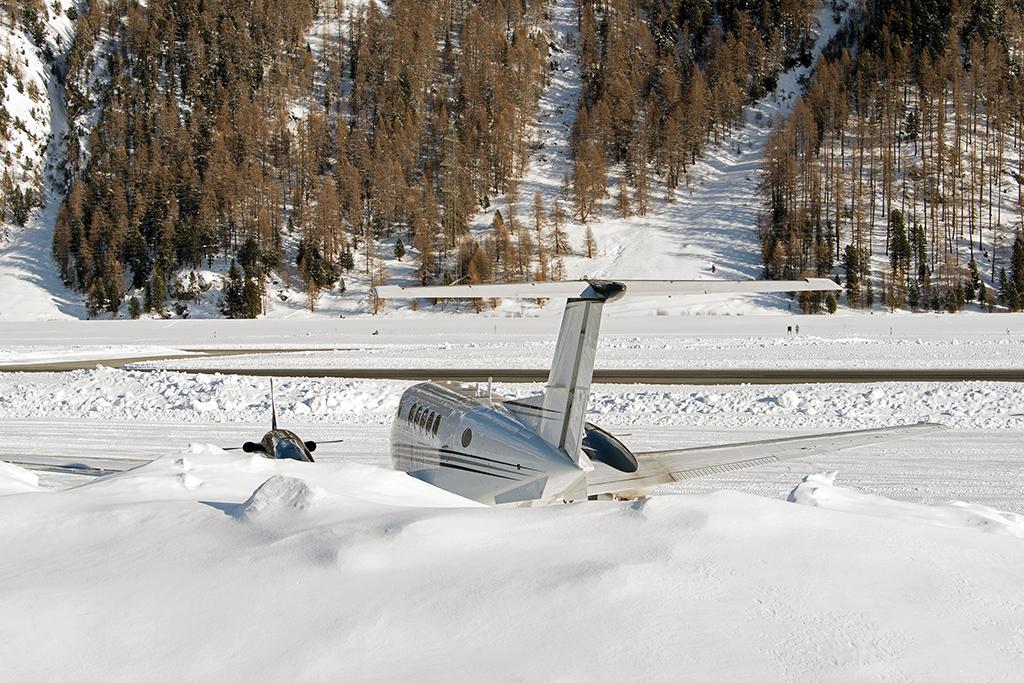
Intake icing occurs when snow or slush enters during low-power engine operations, such as taxiing after landing or prior to takeoff, and accumulates. Relatively long, curved intake ducts are particularly prone to this phenomenon. It is most likely to occur during heavy snow or rain at temperatures close to 0C before and after engine start. Also, in some cases, accumulation will not take place until after engine start. Then the consequences only become evident when applying power for takeoff.
These accumulations may be unaffected by the use of engine anti-icing, especially when turbofans are operated at or close to ground idle rpm. Intake duct deposits and engine blade deposits may detach and be ingested during the subsequent application of high power settings for takeoff, resulting in adverse effects on engine operation and possible flameout.
According to Andy Mihalchik, technical pilot and program manager at GE Aviation, if flight or maintenance personnel note ice or snow on an engine’s spinner with little or a thin layer of ice/snow visible on the fan blades, they should conduct a ground ice-shed procedure.
If the preflight inspection reveals ice or snow on the spinner and a heavy accumulation on the fan blades, confer with maintenance techs about the necessity to deice the engine prior to start. Not to be confused with engine anti-icing, engine deicing involves placing engine-specific coverings on the unit and then piping hot air in. If deicing is not an option, put the aircraft in a heated hangar. Spraying aircraft-deicing fluid into the engine is not approved because it reduces engine efficiency and corrodes the hardware. In addition, deicing fluids can cause contamination of the bleed air system.
Engine anti-ice must be selected ON immediately after both engines are started and must remain on during all ground operations when icing conditions exist or are anticipated. Most manufacturers recommend the use of engine anti-ice during ground operations when the OAT is 10C or less and visible moisture is present. When air is sucked into the engines there is a venturi effect that will decrease temperature. Thus, it is possible to get ice accumulation within the engine’s inlet at 10C. Boeing advises pilots not to rely on airframe visual icing cues before activating engine anti-ice. And since engine anti-ice extracts a performance penalty from the engine’s thrust, do not forget to apply the necessary corrections stipulated in the aircraft’s flight manual to takeoff and climb performance.
Engine anti-ice systems are designed primarily to deter the accumulation of ice on the nacelle intake, leaving the fan blades susceptible to ice accumulation in freezing fog or precipitation when the engine is at or near its ground idle speed. That ice must be removed by engine run-ups prior to takeoff.
Ground ice-shed procedures usually contain an acceleration of the engine rpm to a minimum thrust setting and then a dwell time at that setting. The acceleration increases centrifugal forces and slightly flexes the fan blades, resulting in mechanical shedding of ice. The dwell time contributes to the thermomechanical shedding process involving increased fan airflow temperatures and pressures. Asymmetric fan ice shedding may cause momentary increases in perceived and indicated engine vibration but it should return to normal levels as fan ice departs.
During severe icing conditions; freezing fog, rain or drizzle; or heavy snow, repeating the ice shed procedure at 10-min. intervals may reduce fan ice accumulation. Avoid doing the procedure in areas with loose ice and snow to minimize the FOD potential or in a location where the jet blast could damage other aircraft or nearby structures. Also, don’t forget that ice contamination of engine probes can cause erroneous instrument readings.
Carbon Brakes in Slush
Slush on ramps and taxiways can also affect aircraft tires and brake assemblies.
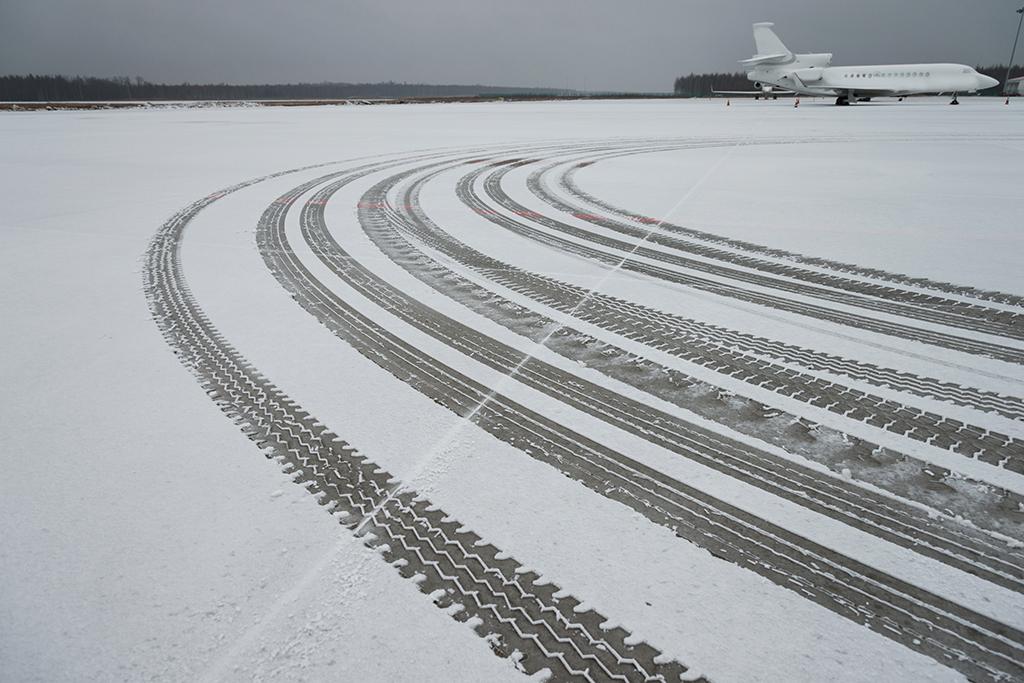
Conditions at Spain’s Pamplona Airport (PNA) were “messy” when the Bombardier CRJ1000 crew arrived for their scheduled flight to Madrid on Feb. 1, 2015. The airport was initially closed for snow removal. But even after it was reopened, the snow continued moderately. When the snowfall finally ceased temporarily, the flight crew used Type 1 deicing fluid and then slowly taxied the short distance to the runway threshold. There was enough slush present on the runway that snow-clearing vehicles had left tracks, but the pilots were able to see through the build-up of slush.
The subsequent flight to Madrid was uneventful—until touchdown. With wheels on pavement, the aircraft began vibrating so hard, the pilots believed a tire had ruptured. Accordingly, they minimized use of the brakes and reported no problems with directional control during the rest of the landing roll or subsequent taxi. An airport marshaller noticed that the outboard left tire had burst. Once the aircraft was parked, inspection revealed that the right outboard tire had a flat spot and chunks of white ice were stuck to the brake assemblies. The trailing edge of the inboard left flap and flap fairs were damaged, and a gear bay door had broken from its fittings. The airport authority conducted an inspection of the runway and found tire debris and part of the gear door.
FDR data determined that the two outboard tires did not turn. Unlike the CRJ900s in the Air Nostrum fleet, which are equipped with steel brakes, those on the CRJ1000 series are carbon. At the post-incident interview, both pilots admitted that they were more concerned about the possibility of ice on the wings and had not conducted the prescribed braking activations during the taxi because the distance was so short.
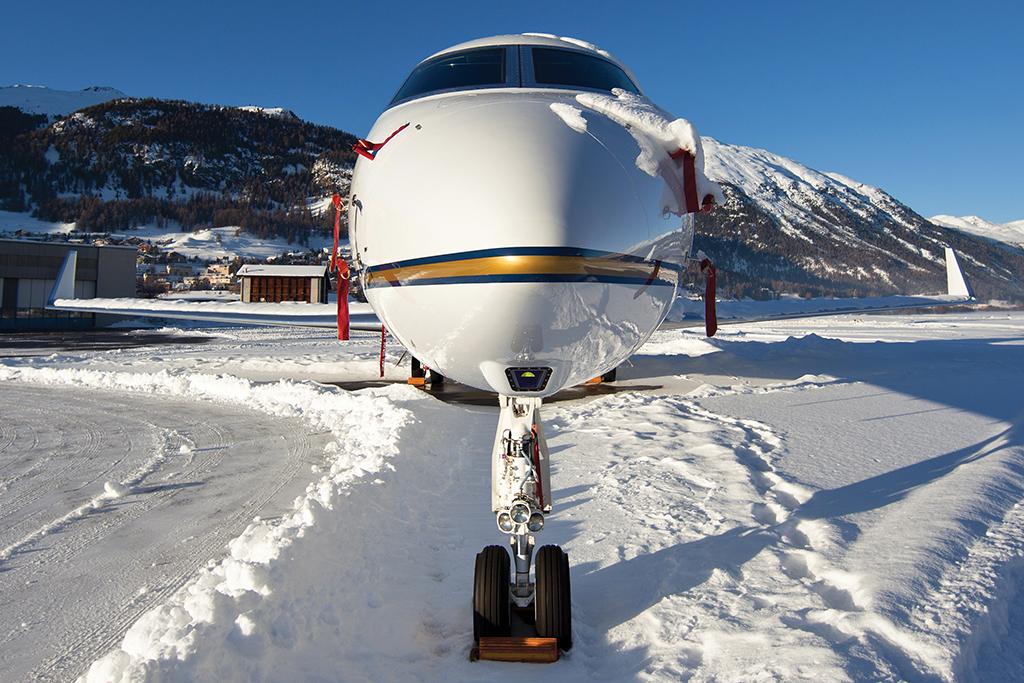
Furthermore, the pilots were unaware of the porosity of carbon brakes and the implications of this characteristic. Such brakes absorb moisture more readily when cold, which means the brake units are more susceptible to freezing after taxiing/takeoff/landing with frozen deposits on the surface. When the wheel assemblies are retracted after takeoff and they are exposed to the cold temperatures and reduced air pressure at higher altitudes, the contaminating liquid is spread even farther into the space between the rotors and stators, and can lock the brakes.
The Comisión de Investigación de Accidentes e Incidentes de Aviación Civil determined the primary cause for the incident as follows: “Part of the slush encountered while taxiing and during the subsequent takeoff run is thought to have made its way into the landing gear bays, adhering to the components there. When the gear was retracted, wheels No. 1 and No. 4 [the outboard wheels] were in a lower position and thus more exposed to low temperatures during the flight. As a result, the slush deposited on the gear could have fallen due to gravity to the brake assemblies before freezing in place.”
The flight crew operating manual contained a number of precautions for winter operations. When using wet, snow- or slush-covered runways or taxiways, or following overnight parking in known icing conditions, use light braking techniques to warm brakes while taxiing to takeoff and monitor the brake temperature while doing so. Then delay gear retraction following takeoff from slush- or snow-covered runways. And when touching down, carry out a positive landing to ensure initial wheel spin-up and brake-out of frozen brakes. During the landing roll and subsequent taxi, use the brakes to prevent progressive build-up of ice on the wheels and brakes. Following takeoff or landing on wet, snow- or slush-covered runways and taxiways, tires should be inspected for flat spotting prior to the next flight.
Carbon Brake Maintenance
Now that carbon brakes are standard on many types of aircraft, the airframe and brake manufacturers have learned that various chemicals used to deice ramps and runways can cause oxidation of those brakes in addition to corroding electrical connectors and hydraulic system components.
Ever since the 1990s, runway deicing materials containing potassium and sodium have been used as an alternative to those with urea and glycol. It was necessary to find alternatives to those chemicals due to the damage they create in nearby water systems and the toxic threat they pose to aquatic life. Following the introduction of the new runway deicers, aircraft operators began experiencing catalytic oxidation of the carbon-brake heat-sink disks. As a result, the FAA issued Special Airworthiness Information Bulletin NM-08-27 and EASA published Safety Information Notice 2008-19R1 recommending the main gear wheel removal/installation sections of applicable aircraft maintenance manuals be revised to include inspection of the carbon brake assembly for signs of catalytic oxidation damage whenever a wheel and tire assembly is removed.
Beware of Frozen Liquids
If an aircraft is to remain overnight with air temperatures dropping well below freezing, it is important to remove any liquids that could freeze, burst their containers and then, upon thawing, flow into unprotected areas and parts. This especially pertains to the water lines in the lav. If the pipes break, the water will seep into the aircraft’s underbelly, and that’s a concern.
On May 9, 2007, a Dassault Falcon 20 was descending toward London after a flight from Gander, Newfoundland, when a lateral flight-control restriction became apparent. The problem first appeared about 2 hr. into the flight when the pilots noticed a flickering aileron TRIM notice on the PFD. The captain applied corrective trim, but the warning indication reappeared. During descent the flight-control problem worsened. While in a left turn, the bank angle continued to increase and when it reached 45 deg., the captain disconnected the autopilot with the intention of flying manually.
However, upon doing so he found roll control was very stiff when rolling to the right. He used rudder to bring the aircraft to a wings-level attitude. Both pilots then applied full force to both control wheels in an attempt to recover lateral control, but no movement was possible. The captain was only able to make turns through the gentle use of rudder. Accordingly, he restricted the bank angle to a maximum of 10 deg. The pilots notified ATC they had a jammed flight control and were unable to do turns to the right and were only able to make shallow left turns. Turbulent crosswind conditions were a concern, but due to some apparently extraordinary airmanship, the pilots landed their compromised jet safely at London Stansted Airport (STN) and all seven aircraft occupants exited without injury.
During the following investigation, a significant volume of water (at least 20 liters) was discovered below the floor panels in the forward fuselage; the water had frozen in flight and caused a restriction to the movement of the aileron trim actuator.
The UK AAIB Bulletin 2/2008 said the water in aircraft bilges could have come from a variety of sources: Leaking plumbing, condensation and leaking seals are the most common. It seems likely that the water in the Falcon must have built up in the fuselage over a period of time.
However, Dassault believed a more likely source of the water in question was leakage in the area of the icebox drain over an extended period. The manufacturer had received notification of three previous events similar in nature to that experienced by this Falcon 20 crew. To prevent this problem from recurring, operators were reminded that drains must be checked during daily aircraft inspection, as well as checking both manual and automatic drains.
Ramp and Taxi Precautions
Wintertime aprons and ramps can be slick and the equipment and personnel operating thereupon can lack sufficient traction to start, stop or even remain in place when encountering jet blast from surrounding airplanes.
Pilots of parked or holding airplanes might use increased engine thrust to get moving or taxi over surface irregularities like frozen ruts formed by tire tracks. In so doing, excessive engine blast may damage other airplanes, equipment or even harm personnel.
The fact is wet snow cannot be blown off the pavement; rather it will readily compact and bond to the surface when run over by airplane wheels. Consequently, the airport operator needs to implement different clearing or preventive measures for wet snow than those used for dealing with dry snow. Wet snow and temperatures close to freezing can result in slush. Large chunks of ice, from refrozen snow or slush, or deposits from aircraft gear created during landings, can cause severe damage to tires, engines and airframes.
According to FAA Advisory Circular 150/5200-30D, “Airport Field Condition Assessments and Winter Operations Safety,” dated March 8, 2017, there are situations where complete removal is difficult or impossible to achieve within a certain timespan. It may require an hour or more for the dry chemical to go into solution and melt the ice.
The obscuration of normally visible surface markings or obliterated signs could make maneuvering on aprons difficult. It also increases the chances of taxiway or runway incursions. And snow piles that aren’t located far enough from the taxiway can create additional wingtip hazards.
Accordingly, allowing greater than normal distances between airplanes while taxiing will aid in stopping and turning in slippery conditions. Doing so also will reduce the potential for snow and slush being blown and adhering onto the airplane or engine inlets.
Taxi at a reduced speed since proceeding at excessive speed or with strong crosswinds may cause the airplane to skid. Use smaller nosewheel steering and rudder inputs.
Limit thrust to the minimum required. Use of differential engine thrust assists in maintaining airplane momentum through a turn. When nearing turn completion, placing both engines at idle thrust reduces the potential for nosewheel skidding. Differential braking may be more effective than nosewheel steering on slippery or contaminated surfaces. Nosewheel steering should be exercised in both directions during taxi. This circulates warm hydraulic fluid through the steering cylinders and minimizes the steering lag caused by low temperatures.
During taxi-out, avoid using reverse thrust on snow- or slush-covered runways, taxiways or ramps unless absolutely necessary since doing so can cause slush, water and runway deicers to become airborne and adhere to wing surfaces.
Before brake release, check for stable engine operation. After setting takeoff engine pressure ratio (EPR), or N1, confirm that engine indications are normal, in agreement and in the expected range. Check that other flight deck indications are also normal.
By no means does this article address all of the threats to an aircraft during winter ground operations. Following the recommendations within your aircraft operating manuals is always prudent, but as you can see from these examples, there are a number of threats that have been discovered only through incident reports.
Winter ground conditions create additional workload requiring time and attention to properly identify and manage these threats. So, stay warm and be careful out there.