
Should a takeoff be continued or rejected after a suspected tire failure?
The chances of experiencing an actual engine malfunction during the takeoff roll is gratefully small thanks to the reliability of modern turbine engines. Simulator training every six months refreshes the quick decision-making and reaction times for an engine malfunction on takeoff. Essentially all of the industry training on the go/no-go decision focuses on an engine failure on takeoff.
The fatal accident involving a Learjet 60 during a rejected takeoff at South Carolina’s Columbia Metropolitan Airport (KCAE) on Sept. 19, 2008, reminds the industry that other malfunctions can occur during takeoff. The go/no-go decision during takeoff has precious margin for error, and the consequences of making the wrong decision can be unrecoverable.
Tragically, this accident illustrated that the split-second decision to go vs. no-go isn’t as easy to execute in the event of a high-speed tire failure.
It was close to midnight at KCAE when the flight crew of the Learjet 60 closed the main entry door and began their taxi from the FBO. The pre-takeoff briefing was similar to the same mantra uttered by the majority of flight crews before each takeoff. The CVR recorded the captain’s briefing as they taxied to the runway: “We’ve got plenty of runway, so we’ll abort for anything below 80 kts. after V1 and before V2 engine-failure fire malfunction loss of directional control all the big things after V2 we’ll go ahead and take it into the air treat it an inflight emergency.”
About 1.5 sec. after the first officer (FO) called V1, the CVR captured the beginning of a loud rumbling sound that corresponded with the first main landing gear tire fragmenting apart. Four-tenths of a second later, the FO stated “Go,” to which the captain said something unintelligible. At about this time the airplane’s groundspeed reached a peak of 144 kts. The FO stated, “No? ar…alright. Get ah what the [expletive] was that?” Seconds later, the captain stated, “I don’t know. We’re not goin’ though.” Two seconds later, the captain indicated that the thrust reversers were full out.
The two surviving passengers remember that the airplane was swaying back and forth all the way down the runway and that it felt “out of control.” The Learjet passed through the 1,000-ft. runway safety area, struck airport lighting and navigation antennas, and descended a steep slope, continuing to strike obstacles as it crossed a five-lane road, and erupted into a fireball. The captain, first officer, and two passengers were killed. The two other passengers were seriously injured.
During its investigation the NTSB found debris from all four main landing gear tires on the runway. Further inquiry revealed that the tires had experienced approximately 2% pressure loss per day in the three weeks since they had last been checked. At the time of the accident, the tire pressure was approximately 140 psi, dangerously below the recommended pressure of 219 psi.
The NTSB determined the probable cause of the accident was the operator’s inadequate maintenance of the airplane’s tires, which resulted in multiple tire failures during takeoff roll due to severe underinflation, and the captain’s execution of a rejected takeoff after V1, which was inconsistent with her training and standard operating procedures.
History Repeating Itself
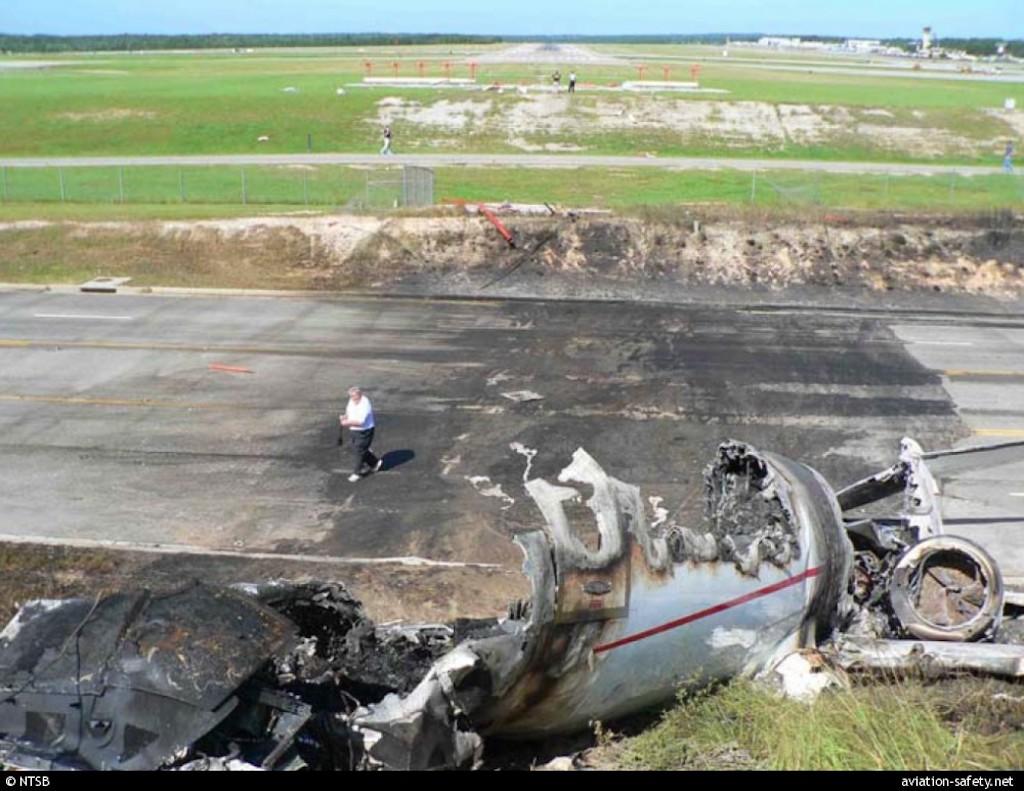
Credit: NTSB
This unfortunately was not the first accident involving a flight crew’s errant reaction to a high-speed tire failure. In 1990, the NTSB issued a special investigation report, “Runway Overruns Following High-Speed Rejected Takeoffs,” that examined high-speed RTOs involving commercial airliners. The Safety Board reviewed three studies, which included data from the NTSB, NASA and Boeing, related to the causes and outcomes of RTOs. The report found that tire failures led to more high-speed RTOs than did engine-related anomalies.
The original Boeing study on RTO-related events from 1959 to 1988 found that many of the RTOs were initiated after V1 and more than half of them were unwarranted. Boeing has since updated its study to include a total of 94 RTO-related accidents or incidents from 1959 to 1999. The Boeing review found that just as many events were attributed to tire or wheel failures as propulsion anomalies and that more than half of the RTOs were performed after V1.
This collection of special studies consistently found that many other pilots have misinterpreted tire anomalies and responded by initiating an unnecessary RTO after V1. These instances resulted in runway overrun accidents that might have been avoided had the takeoff been continued. Advisory Circular AC 120-62, “Takeoff Safety Training Aid,” cautions pilots about misinterpreting tire events. However, the NTSB investigation found its effectiveness is limited because it doesn’t prepare flight crews for the startling cues that include loud noises, airframe shaking and unusual vibrations.
Business Jets Are More Prone to High-Speed Tire Failures
As mentioned in our previous article on tire wear, the smaller tires on a business aircraft undergo more stress than an airliner’s tire while taxing to a runway. The smaller tire must rotate many more times to travel the same distance. As a result, smaller tires will heat up much more because of the deflection that occurs to the tire with each rotation. Smaller tires build up heat more rapidly than larger tires. Long taxi distances lead to heat buildup, which leads to weakening of the cord rubber interface and early failure of the tire, which is frequently catastrophic. Brake efficiency is also reduced as tire temperature increases.
Second, it is far easier for the airlines to conduct daily pressure checks than it is for operators of business or fractional aircraft, which often do not overnight at a location with an approved maintenance provider. The lack of a pressure check for three weeks in the Learjet accident at Columbia meant that the tires were woefully below their recommended pressure level.
Third, the centrifugal forces on smaller radius tires are considerably higher than on the tread of larger tires. Thus, this combination of factors raises the risk of high-speed tire failures for business aircraft.
How often have high-speed tire failures resulted in damage and/or injuries to business jets? This author examined official documentation for 251 accidents and 808 incidents involving business jets that occurred from January 1991 through December 2002. This effort also examined 3,190 NASA Aviation Safety Reporting System (ASRS) reports submitted by flight crews flying business jets.
The extensive data sample revealed that 17 of the 251 accidents resulted from RTOs. What were the causes? Eight accidents were caused by tire failures, four by improper takeoff performance calculations, two by engine failures, one by the parking brake being left on, one by flight control failure, and one due to a loss of directional control. In addition, 35 incidents resulted from RTOs, 19 of which were caused by tire failures.
These statistics led to an important conclusion. Takeoff incidents involving tire failures were four times more frequent than those involving engine failures. In fact, tire failures caused 47% of RTO accidents and incidents in the study. Contributing factors often included long taxi distances, hot day conditions, suspected low tire pressure, or a combination of these issues.
Likely to Depart the Runway
Nearly 75% of the tire failure incidents resulted in the aircraft departing the runway, adding further potential for injury and aircraft damage. Failed tires produce miniscule traction, which is needed to transmit the deceleration needed from the brakes to the pavement. The amount of runway necessary to decelerate an aircraft with failed tires is immense.
Even when a tire failure occurs below the takeoff decision speed, the ability of the aircraft to abort the takeoff within the remaining runway is not guaranteed since the accelerate-stop performance data is based upon an engine failure event as opposed to a tire failure event. An example of this principle occurred on May 23, 1995, at 0810 CDT, to a Learjet 35A that was substantially damaged during a runway overrun near Rogers, Arkansas.
The airline transport rated pilot, the commercial pilot acting as copilot and their five passengers were not injured. The airplane was on an IFR flight plan from Rogers Municipal Airport (KROG) to Toluca International Airport (MMTO) in Mexico.
According to the pilot's statement, "Around 10-15 kts. before V1 [136 kts.], I felt a large vibration along with a bang." The takeoff was aborted with maximum braking and full reverse. The Learjet overran the departure end of the 6,011-ft. Runway 19. The undercarriage collapsed as the airplane crossed a 1-ft.-deep drainage ditch approximately 200 ft. beyond the departure end of the runway. The airplane came to rest approximately 1,200 ft. from the departure end of the runway on a heading of 345 deg. Several fragments of the failed right outboard tire were found near the midfield point of the runway.
The pilot reported that the right main gear tire "blew out." The failed tire was retained for further examination and testing. No evidence of pre-impact mechanical failure, improper servicing or malfunction was found. [U.S. NTSB Accident Report No. FTW95LA216.]
In another incident, the NTSB interviewed an FAA flight test manager who was sitting in the right seat of a Learjet 55 during a takeoff at gross weight in Orlando when all four main landing gear tires came apart after the airplane was beyond V1. Both he and the other pilot heard the tires coming apart and he saw tire fragments passing forward of the cockpit. The takeoff was rejected due to concern that the tire fragments could be ingested by an engine. Even with the thrust reversers, it took nearly 9,300 ft. to stop the airplane on the 12,000-ft. runway.
In Part 2, we’ll discuss how tire failures can cause serious secondary damage and potentially lead to fire.