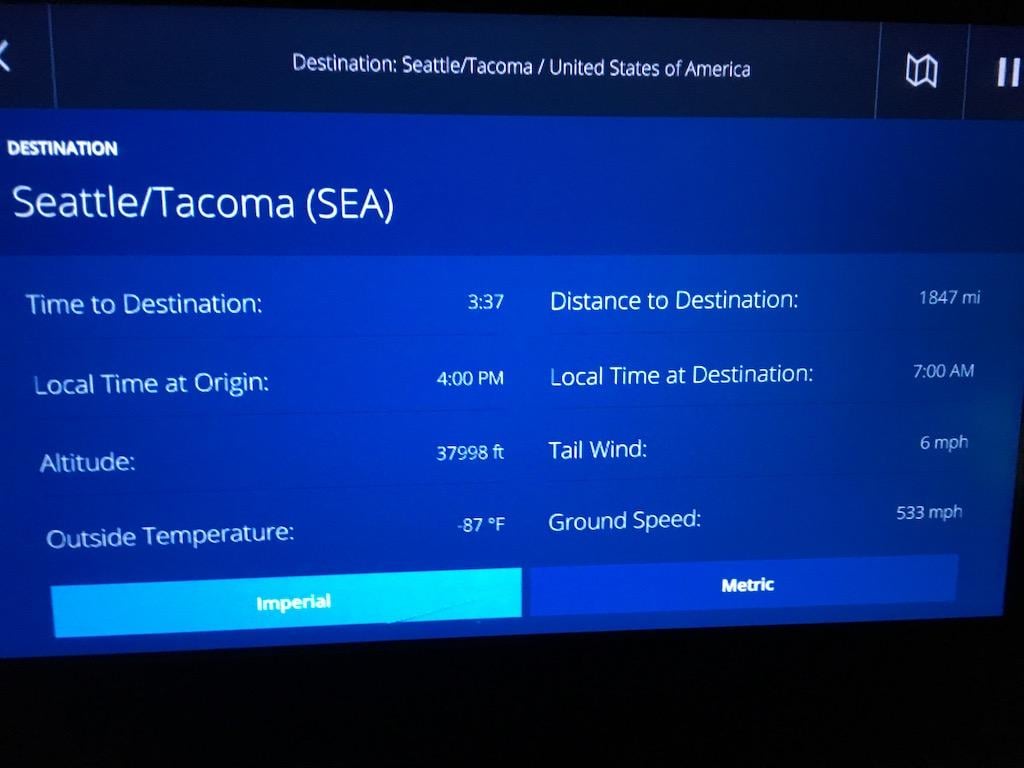
A key factor in fuel temperature is the outside air temperature, which tends to be most problematic in polar regions. During this trans-Atlantic flight from Amsterdam to Seattle, the OAT was -87 deg. F (-66 deg. C). Cold fuel is generally a risk if the OAT is colder than -60 deg. C.
Fuel that is exposed to extremely cold temperatures for long hours can chill enough to restrict the flow of fuel to the engine.
The temperature of the fuel in your wings is affected by a number of variables. The first important parameter is the initial fuel temperature at your refueling location. Obviously, the fuel uploaded at Palm Springs on a summer day will be much warmer than fuel uploaded in Fairbanks, Alaska, in winter.
The amount of fuel in a tank will influence the rate at which the fuel cools down. Fuller tanks will retain their temperature for a longer period of time than partially filled tanks. Even the solar heating during the day will provide a modest amount of assistance.
The size and shape of a fuel tank significantly affects the cool down of fuel. A tank with a high surface-to-volume ratio transfers heat faster. For example, the outboard tanks of the Boeing 747-400 are longer and narrower than the inboard tanks. These tanks will cool down faster and are more prone to low-temperature alerts.
The wing design of long-range business aircraft increases the risk of fuel cooling. The fuel contained in the long slender wing tanks of most business jets would be cooled down at a faster rate than the larger and deeper fuel tanks in long-range commercial transports.
The fuel temperature will vary between tanks due to internal components that utilize fuel tanks as sources of cooling for other systems. The Boeing 777’s left wing tank contains a single heat exchanger to cool hydraulic system fluid, whereas the right wing tank contains two heat exchangers for the hydraulic system. Thus, the left wing’s fuel tends to be slightly colder. The Airbus A318, A319, A320, A321 series utilize fuel for Integrated Drive Generator oil cooling. The warmed fuel from the engine is returned to the outer wing tank, thereby providing a modest amount of warming to counter-balance the cooling effects from the outside air temperatures.
What is your aircraft’s lowest temperature?
The lowest temperature threshold for YOUR aircraft depends on the fuel’s freezing point, the engine margin and the temperature accuracy error. The maximum freezing point for jet fuel depends on the geographical region of the fuel supply.
The average freezing point of delivered Jet A fuel at U.S. airports is between -43 deg C and -50 deg C. Refueling your aircraft at different locations creates a blend of fuels in the tanks, thus creating its own unique freezing point. Boeing recommends against automatically assuming that the freezing point of the uplifted fuel is the actual freezing point of the fuel on board. The manufacturer recommends using the highest freezing point of the fuel used on the last three fuel uplifts.
Different engine designs will have different temperature margins over the fuel freezing point. For instance, the GE engines on the Airbus 330 require a 3-deg. margin. If the Jet A freezing point in the fuel tanks is 40 deg. C, then the alert threshold is -37 deg. C for the inner fuel tank.
Operational Guidelines
With the increased number of ultra-long-range flights that often utilize polar routes, aircraft operators must have the proper pre-flight and in-flight procedures to ensure that the temperature of fuel in the fuel tanks remains at sufficiently above the freezing temperature of the fuel to ensure its flowability.
Obviously, the key factor is the outside air temperature (OAT), and this tends to be most problematic in polar regions. As a general rule, cold fuel is a risk if the OAT is colder than -60 deg. C. From an operational standpoint, the observed fuel temperature must remain at least 3 deg. C above the specified freezing point. If this condition is reached, the flight crew must take action to increase the Total Air Temperature (TAT) to avoid further fuel cooling.
Given the aforementioned differences in aircraft design, it is important for pilots to follow the specific procedures for their aircraft. One of the recommendations is to transfer fuel between tanks to mix warmer fuel with colder fuel. The easy-to-remember memory aid is “stir it up.”
A second recommended corrective action is to change altitude to where warmer air can be expected, if practical. In a “standard atmosphere” that would require descending. Descending 7000 ft. can result in approximately a 7-deg. C increase in the TAT. With that said, airmasses over the polar regions may be warmer at higher altitudes.
As previously mentioned, aerodynamic heating can be increased by speeding up. An increase of 0.01 Mach warms the fuel by 0.5 to 0.7 deg. C. An important note is that the latter two options will increase fuel consumption.
Don’t expect to see a rapid change in the fuel temperature after making one or more of these recommended procedures. Since liquids don’t change temperature readily, it can take from 15 minutes to an hour for a change in TAT to affect the fuel temperature.
Manufacturers provide software tools to help operators perform pre-flight analysis to minimize the threat from fuel freezing. Airbus provides a performance programs package called “WinPEP” that takes into account the actual weather and predicts the fuel temperature in each tank. This can be used proactively to determine the necessity of airspeed, altitude and/or route changes.
Fuel freezing is just one of the unique parameters that must be considered when planning flights in polar regions. Remote terrain, extreme temperatures, magnetic unreliability, availability of ETOPS alternates, and space weather affecting both navigation and communication signals all require extensive preparation and planning.
Factors That Lead To Fuel Freezing, Part 1: https://aviationweek.com/business-aviation/factors-lead-fuel-freezing-p…