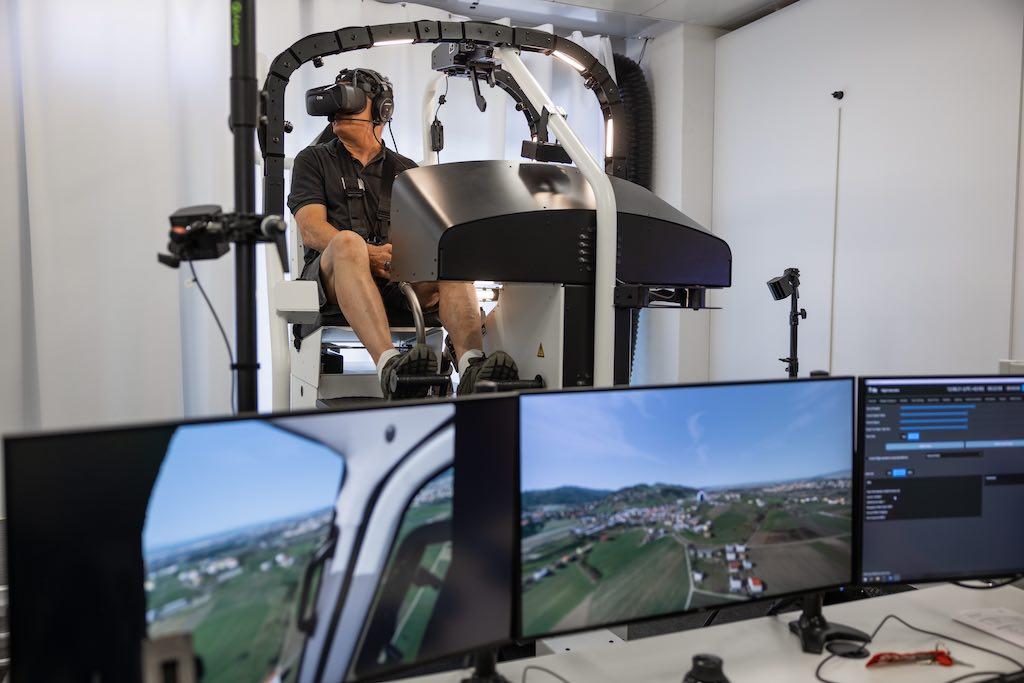
This is the first part of a three-part article series.
The ultimate question in a flight examiner’s mind during a check ride boils down to the simple concept, “Would I feel comfortable putting my family in an aircraft commanded by this individual?” This was the quandary facing a helicopter check airman while I sat in the back of the simulator observing an EMS pilot undergoing yearly training and evaluation. The trainee had been flying the Airbus H135 for the previous year and showed proficiency in the normal maneuvers. However, when mechanical malfunctions were introduced, it was obvious that the trainee wasn’t performing to acceptable standards. At the conclusion of the simulator session, I quietly excused myself because I knew it was going to be an unpleasant debriefing.
This observation directly leads to a vital question facing the industry. How do we prepare pilots for autorotations, mechanical malfunctions, external load operations, mountain operations and other high-risk operations without causing so many flight accidents?
Searching for Better Solutions
In recent years there have been a growing number of advertisements for “virtual reality” training devices. I’ve had an engineer’s skepticism, wanting to see hard data about the training effectiveness of these products. Quite frankly, some seemed to be hardly any different than the toys and games played by children.
However, upon watching Claude Vuichard’s demonstration of the virtual reality (VR) flight training device developed by VRM Switzerland, I immediately wondered if this could be an answer to the industry’s quandary. Vuichard’s evaluation of the great training effectiveness of this device with essentially zero risk convinced me to travel to VRM Switzerland’s headquarters in Zürich for a “hands-on” demonstration.
I was introduced to Nils Werder, VRM Switzerland account executive, and Simon von Niederhäusern, head of marketing, who would be my guides for the rest of the day. There was an excitement in their offices as the European Union Aviation Safety Agency (EASA) had just certified the VRM Switzerland and Airbus Helicopters H125 Virtual Reality Flight Training Device Level 3.
Then I met the CEO, Fabi Riesen. I expected to hear a salesman’s pitch about his great product. Instead, I felt as if I was sitting in a graduate engineering seminar as Riesen explained human factors aspects of the visual presentation system that are necessary to create such a high level of realism in flight simulation. This includes a high emphasis on accurate colors, transitions and shading, as well as preventing geometric distortion.
After these pleasantries it was time to get some hands-on experience. While getting ready for takeoff I turned my head far to the right and left to make certain that the tail rotor was far from any obstacles, then looked up to check for any overhead obstacles. The VR headset continuously recognizes its position and orientation with a tracking system. This gave me the feeling of being in a real environment and allowed me to look in a complete 360-deg. scan. Virtual reality offers a natural stereoscopic panoramic view. This opens a range of previously undoable training scenarios, especially for helicopter external sling load operations training.
As I leaned to the left and right, the entire visual scene replicated the change in perspective that would occur with a body’s shift. I leaned far to the right, as if to monitor picking up an external load, and again I was impressed with the realism of this system.
At this point Werder suggested that I wave my hand, and much to my astonishment, I saw its shadow across the instruments. This is another example of the immense research done by VRM’s team. They developed a precise Pose Tracking System utilizing several cameras mounted in the cockpit at specific positions and angles to ensure that all parts of the pilot’s body are visible. This allows the pilot to see his hand and body movements in the virtual world.
As I started to pull pitch, the vibrations in the seat replicated the vibrations of the rotorcraft. The vibration system is designed to reproduce the original vibration characteristics that occur in that specific make and model of rotorcraft as well as for the specific phase of flight. Additionally, important acoustic references are mapped in the sound system and contribute to a realistic experience.
It Flies Like a Real H125
VRM Switzerland’s flight control load system features force feedback in real time to enable the pilot to feel the helicopter realistically. Aerodynamic control pressures are accurately simulated. This becomes especially important during a hydraulic failure simulation with the reproduction of friction forces and feedback.
The engineers at VRM Switzerland, in cooperation with the Eastern Switzerland University of Applied Sciences, developed a completely new drive system. The flight simulation software features advanced flight dynamics thanks to realistic flight physics and real-time full multi-body simulation. The highly dynamic 6 deg. of freedom motion platform runs completely electrically (no hydraulic systems), providing high performance and a quick response time.
This system was carefully validated and calibrated during the development phase in collaboration with Airbus, which sent test pilots and instructors to Zürich to ensure the maximum fidelity to push the safety standards within the industry to new levels. As a result, the motion cueing gave me the perception that I was flying a “real” H125. In combination with the aural inputs, the high-resolution 3-D view, the accuracy of the flight control pressures, the feel provided by the vibrations and the body pose system replicating a pilot’s view with body twisting, it had the precise look and feel of being in an actual H125. This is the leading edge of simulation in terms of full immersion.
In Part 2, we’ll go “mountain flying.”