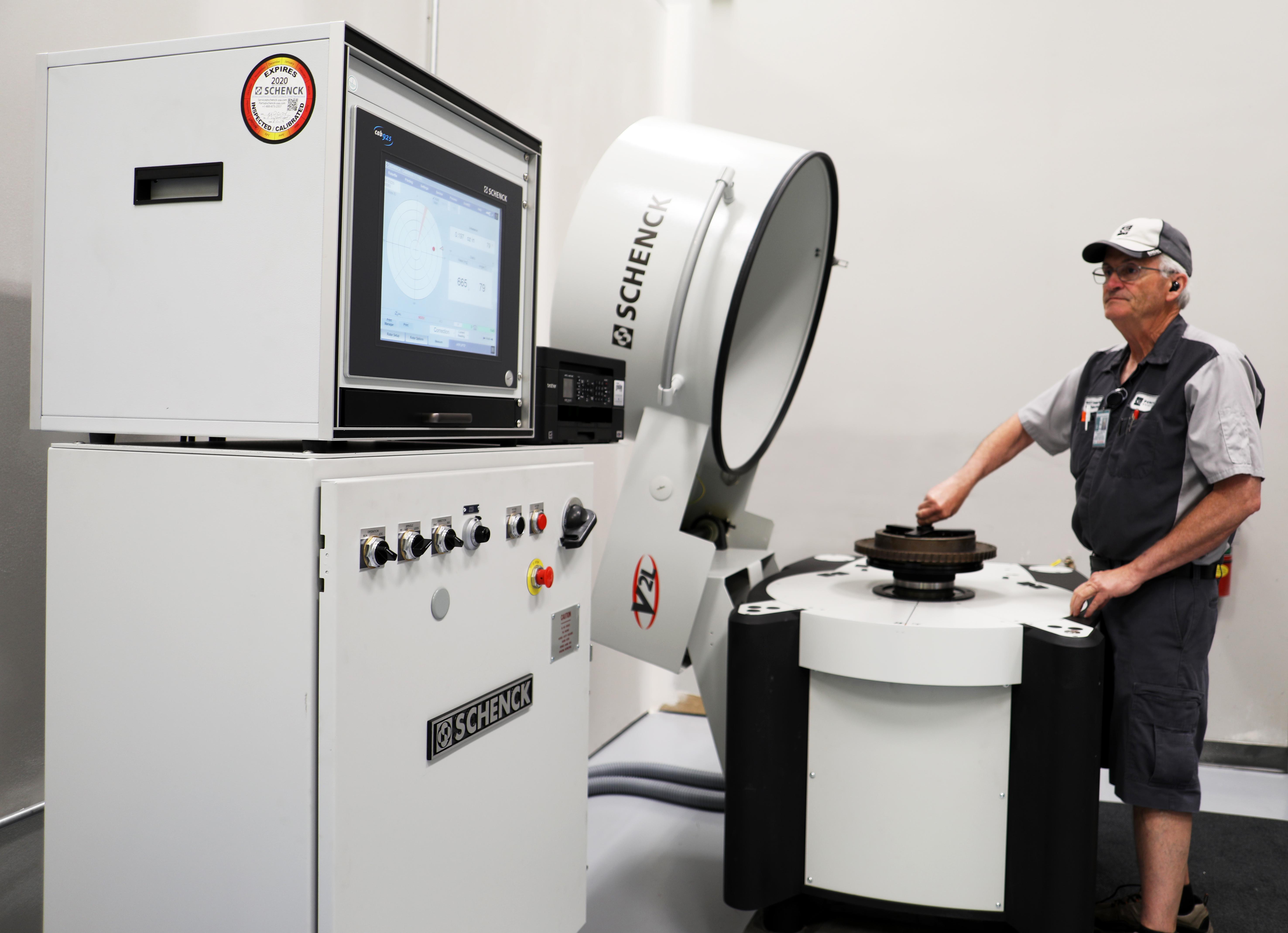
In the corporate aircraft world, engine MRO is evolving as OEMs focus on reducing maintenance costs through longer inspection intervals and more on-condition maintenance programs.
In fact, the increased application of on-condition maintenance “has forever changed the world of engine MRO,” says Ron Gillette, StandardAero Business Aviation’s director of new engine programs and products.
“For the MRO providers, the change means having a more robust supply chain to deal with the unpredictability of when or how deep a repair might be following an on-condition inspection, along with a stronger mobile support team capable of performing complex inspections and repairs away from the MRO facility,” notes Gillette. “These trends are effecting how MROs provide service and what services are being provided. While these changes help operators reduce maintenance costs, overall they also make those costs less predictable for retail customers—those who are not covered by a maintenance plan.”
Along this line, Gillette points out that even legacy engines, such as the Honeywell TFE731, are moving toward on-condition maintenance and extended inspection intervals. With more than 11,000 produced, the TFE731 continues to dominate the light and midsize jet engine market.
“When Honeywell extended the TFE731 major periodic inspection (MPI) from 3,500 to 4,000 hr., and the compressor zone inspection (CZI) from 7,000 to 8,000 hr., the need for inspections for some operators was reduced by several years,” he says. “OEMs are also providing some operators a path to move from fixed-time to on-condition repair, which can reduce or defer repair cost.”
In that regard, Gillette says that matching life-limited parts with expected aircraft hull life is a critical part of maintaining competitiveness in the legacy engine repair market. He adds that StandardAero has also seen increasing demand for used serviceable material (USM). “However, for OEM authorized MROs, the availability of approved USM is currently well below demand,” he says.