
When American Airlines formally accepted a new 787 from Boeing’s Charleston, South Carolina, production site on Aug. 10, the manufacturer officially marked the event as the beginning of the end for a painful and expensive 14-month suspension of deliveries due to production-quality issues.
But as Boeing’s latest quarterly earnings revealed in October, the company’s battle to recover from a rash of production problems that have plagued the program since 2019 will continue to be a burden for at least the next two years. Issues with surface-quality defects, shims, gaps and out-of-tolerance components twice brought deliveries to a standstill in late 2020 and again in 2021 and, despite fixes, remain a highly labor-intensive and expensive process to correct.
- Aft body rework-redesign is the focus
- Join verification required in 11 key areas
According to Brian West, Boeing chief financial officer and executive vice president, just nine 787s were delivered in the third quarter, and 115 remained in the undelivered inventory. “The pace of deliveries from inventory going forward will be based on finishing rework as well as customer fleet planning requirements,” he says. “We expect most of these airplanes to be delivered over the next two years.”
Boeing has already swallowed the bitter pill associated with the extensive rework costs and huge delays to deliveries, predicting overall losses of about $5.5 billion. As it stands, the company appears to be just over halfway through the worst of the financial effects of the quality issue. Commenting at the latest earnings call on Oct. 26, West said: “We recorded $303 million of 787 abnormal costs in the quarter, in line with expectations, and we still anticipate a total of about $2 billion—most being incurred by the end of 2023. These costs are driven by rework and production rates below five per month.”
Deliveries resumed after the FAA’s long-awaited July 29 approval of Boeing’s plan to correct the issues and inspect the undelivered aircraft. The plan, which addresses inspection and repair procedures, drives airframe-specific compliance processes that Boeing will use to show that each aircraft conforms with specifications. Boeing notes that as 787s come off the production line, they now do not require post-production join verification and rework.
But why is it taking Boeing so long to accelerate deliveries? Aviation Week has obtained documents outlining the huge scope of the issues facing the 787 program since 2019 and some of the complexities involved in inspecting and correcting them. These reports show that, starting in August and September 2019, the company began uncovering the first of a series of structural “quality escapes” that in the ensuing months would eventually include 15 structural noncompliances with airworthiness regulations and 57 nonconformances—or failures to meet specific requirements, standards or procedures.
Initial issues were spotted in the vertical fin, but as Boeing increased its scrutiny of the fuselage, nonconformances and noncompliances were found from the aft Section 48 all the way to the Section 41 nose subassembly (see graphic). Quality inspectors from the Boeing Salt Lake City site, where the fin is made, suspected that forces greater than the stipulated 5 lb. per foot had been used during fitting of shims—small elements that are added to eliminate gaps, maintain the structural performance and minimize pull-down forces required to bring the aircraft into nominal configuration.
Checks were made, and only three fins required rework, but the issue—contained by Line No. 898—triggered alarm bells, and an investigation was also launched to review shimming for the horizontal stabilizer assemblies. The assemblies had already been an issue early in the program, having led to a temporary grounding of the flight-test fleet in 2010 after the discovery of issues with improperly installed shims and the torque of associated fasteners.
As with the vertical fin, inspectors found that in some aircraft, incorrect clamping forces in excess of the 5 lb. per foot had been used to preload the joint, putting a pull-up strain on the stabilizer assembly. Although there was no immediate safety worry because of the young age of the fleet, there were concerns that the unplanned strain would reduce the aircraft’s static and fatigue safety margins.
Checks were made on all 787-8s from Line No. 821 to the latest aircraft on the line, while checks on all 787-9s and -10s were made from Line No. 126. The issue—which specifically affected parts of the stabilizer where it joins the fuselage at a point called the pivot strap and fitting as well as the tip assembly—was declared contained and incorporated in production by Line No. 1041.
In September 2019, the FAA issued an airworthiness directive (AD) requiring a one-time inspection of the 787 horizontal-stabilizer pivot pin assemblies for misalignment and incorrect gapping. This AD was prompted by a report of possible misalignment of the horizontal-stabilizer pivot pin lock ring, outer pivot pin and outboard spacer at final assembly. Boeing eventually reworked six items on aircraft at Everett, Washington, and in South Carolina.

More serious problems emerged in April 2020, when inspections revealed excessive gaps within the surface profile between the two aft tail Sections 47 and 48. Forming the junction between Section 47 at the aft of the cabin and the Korean Air-built tail cone Section 48, the issue was focused on where the parts joined at the aft pressure bulkhead around splice Station 1878. The gaps exceeded Boeing’s inner mold line (IML) requirement for each fuselage mating surface to maintain flatness to within 0.005 in., roughly the width of a human hair, over a given 5-in. span along the join surface.
While seemingly a variation of minute proportions, the gap did not conform to Boeing’s design, and the issue raised questions about effects on load transfer across the join and, potentially, structural margin. Load transfer considerations between the fuselage sections are important because composite structures are very stiff, unlike conventional aluminum airframes, which are flexible. Any issues that potentially interfere with the load transfer between sections—such as gaps, improperly installed shims or inner skin surfaces that are not smooth—can form a focus for stress buildup.
Boeing also identified a partially related issue with an automated laser-based system that scanned the mating surfaces of Sections 47 and 48 prior to joining. The predictive software in the system used the scans to automatically fabricate the shims, which smoothed out any potential gaps. It was discovered that in some cases, where thicker shims should have been produced, software mistakenly restricted the size of shims to a maximum thickness of 0.061 in.
Engineering analysis indicated that aircraft affected by both the shimming and skin surface smoothness issues might not be capable of meeting limit load, and as a result, eight aircraft operated by Air Canada, United Airlines and Singapore Airlines were grounded in August 2020. As the aircraft were repaired, corrected shim-manufacturing software was introduced in October 2020 and applied from Line No. 907 onward. A through-hole-in-place inspection process was added later that month from Line No. 915 onward.
Meanwhile, Boeing discovered more issues around the empennage, where improper shimming had again caused excessive clamping forces to be used while fitting the horizontal stabilizer. At the other end of the aircraft, window provider PPG discovered that a production variation in the bonding of the acrylic used in the No. 1 and No. 2 flight deck windows led to some arcing and cracking problems. Although the problem did not present an immediate fleet safety concern, it formed yet another supplier-driven delay to the program. PPG reviewed production processes and began staffing up to produce a planned 15 shipsets a month by mid-2022.
The gap issues prompted Boeing to expand its IML conformance inspection to include an audit of the joints between the sections made by suppliers. The audit examined interfaces between the forward fuselage Sections 41 and 43—made by Spirit AeroSystems and Kawasaki Heavy Industries (KHI)—and the interfaces between the midbody Sections 44 and 46 made by Leonardo and the Boeing Section 47. Notice of issues, or escapements, were subsequently found in all these joints.
In September 2020, as global air travel was decimated by the impact of the pandemic and with the decision to move all 787 production to South Carolina, the company opted to suspend deliveries as it conducted rework and more inspections. The audit, meanwhile, uncovered more problems within the nose Section 41, including shimming defects and gaps around the large cargo door, forward passenger entry doors and stringer plates beneath the cockpit. In January 2021, Boeing decided to expand the audit beyond circular joins to include all joins common to the surfaces requiring a smoothness criteria of 0.005 in. over a 5-in. span.
The supplier audit found 38 nonconformances and 12 noncompliances. Most affected were Sections 44 and 46, with nine nonconformances and one noncompliance; Section 43 from KHI, with 18 nonconformances; and Section 41, with eight nonconformances and nine noncompliances. Boeing’s own internal quality management system audit uncovered 19 nonconformances and five noncompliances. The most affected area in Boeing’s audit was the aft body assembly, which—excluding the two nonconformances uncovered on the vertical fin and horizontal stabilizer—contained 10 nonconformances and three noncompliances.
Deliveries briefly resumed in March 2021 with the handover of Line No. 1048 to United Airlines, followed by four additional aircraft to All Nippon Airways, Turkish Airlines and Uzbekistan Airways. However, with the true extent of production issues apparent and new problems continuing to emerge amid FAA concern over Boeing’s inspection methods, deliveries were again suspended late that summer.
Around mid-2021, during the FAA review of the Boeing processes used to check the fuselage joins, the company was asked to inspect the interface between the forward pressure bulkhead and the surrounding forward fuselage structure. The inspection found gaps that exceeded maximum tolerance and inevitably led Boeing to the decision that it would have to remove and replace the forward pressure bulkhead on every undelivered aircraft.
Boeing subsequently discovered that the bulkhead fatigue analysis had been based on incorrect thermal loads. The fix required updated analysis, new limits on inspection intervals and a redesign—most of which was released to engineering by late May 2022. The fixes were targeted at introduction by Line No. 1186, while an updated airworthiness limitation was calculated to reduce the inspection threshold at which the bulkhead should be inspected from the current 44,000 cycles to an as-yet-unspecified number.
During the remainder of 2021 and through early 2022, more “escapement” issues continued to disrupt the program. Spirit alerted Boeing of a shimming issue on the forward large cargo door, and Boeing discovered in September that areas around the Section 47 bulk cargo and passenger door surrounds were nonconforming. In a nearby area, an evaluation of the surface-quality problems in the join area between Sections 47 and 48 found that the stringer ends were delaminating.
Around the same time, ply wrinkles and voids were found in composite fixed leading-edge sections, or J-panels, made by Nikkiso under subcontract to Spirit. The issue affected all six panels on each wing leading edge. Boeing also discovered that parts of Section 46 might have been made using an incorrect titanium material; the time-consuming fix required X-ray fluorescence scanning and replacement as needed.
Parts of the keel structure in Section 48 also were found to have undergone improper nondestructive inspection, possibly leading to nonconformance, and required removal, inspection and replacement, too. In another instance in late 2021, a shim on the end of the same stringer was missing in Sections 41 and 46, requiring more measurement of gaps and shimming.
In November 2021, in the wake of the issues around the Section 47 doors, Boeing expanded the value-stream audit process to assess shimming practices with commonality to the passenger and cargo door surrounds in that area. The audit focused on fabrication of main, secondary and predictive shims as well as joins where hole locations could not be inspected.
In late 2021, the company also was tackling a nonstructural issue with connectors on the Raytheon Technologies (formerly Hamilton Sundstrand) integrated cooling system after discovering that some were built with insufficient potting compound.
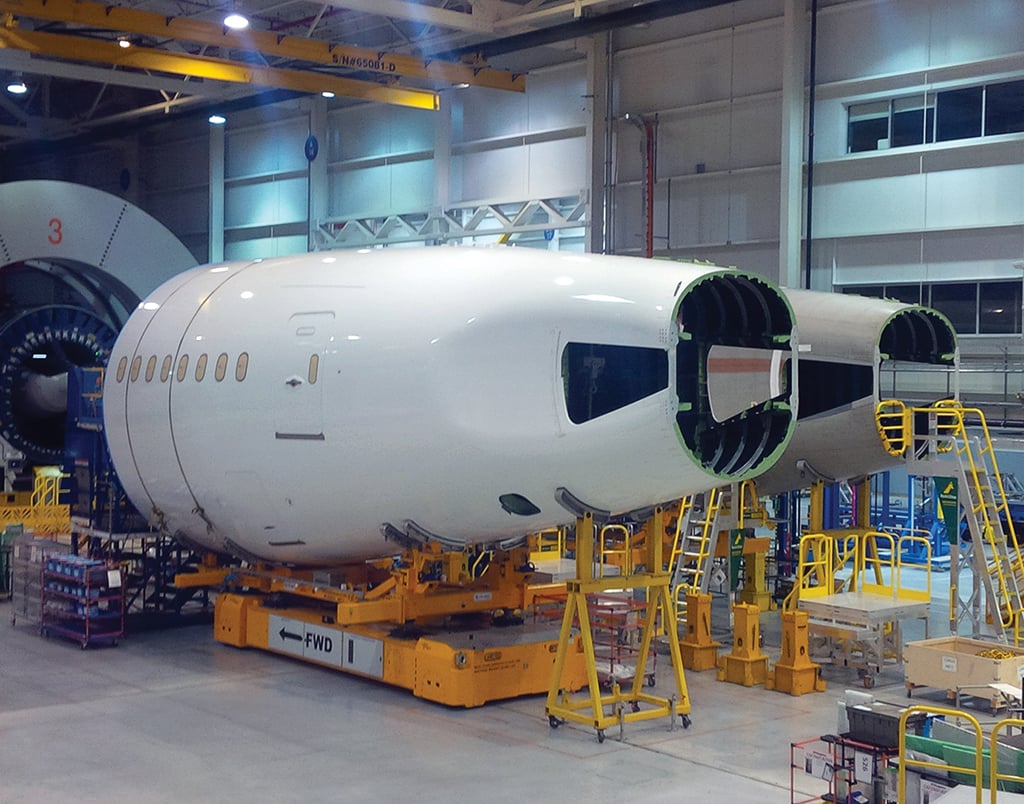
By early this year, as operator appetite for new deliveries started to grow, Boeing was dealing with another production-quality issue that was discovered with the assembly of longerons in the Section 48 horizontal stabilizer. The issue, although not deemed an immediate safety-of-flight concern, concerned a gap that had resulted from the use of excessive adhesive between four longerons (two upper and two lower) and the skin. The discovery prompted the company to launch a quality management system audit into the use of tacking agents to hold shims in place and the potential for excessive use of adhesive to cause gaps.
Around the same time, Boeing investigated a potential issue involving the use of threaded rods, or EK studs, which are designed to be used in tension during installation of the wing lower splice plate. Although again not deemed an immediate safety issue, an incorrect torque multiplier was used, potentially allowing the stud to rotate in the hole. Boeing believed it had managed to contain the issue, which occurred only in South Carolina and was contained by Line No. 1128.
Boeing’s internal studies of the EK stud situation also raised concerns that scratches on the holes and abrasions on some fasteners where the bolts are installed near fuel tanks could be a source of ignition. Although Boeing declines to comment on any specific links, in November it asked for FAA approval to add cap seals over some wing skin fastener nuts to prevent them becoming an ignition source in the fuel tank.
Because joint verification and rework dictated the schedule over which aircraft are cleared for delivery, the largest backlog tasks concern the Section 48 longeron and Section 47 doors, followed by the stringer rework on Sections 41 and 46. The rework of forward pressure bulkheads, stringer end fittings, Section 48 keels and Section 46 titanium fittings also remain a longer-term challenge.
Documents shown to Aviation Week, meanwhile, indicate that the entire process of join verification testing and rework can typically take about five months, from bringing an aircraft out of storage to final predelivery check flights. Following the restoration from storage—an activity that could last more than three weeks—the aircraft undergoes a two-week preparation period for the join verification work. The next month and a half, between 47 and 63 days, is dedicated to joint verification inspection and rework.
The third month begins with a period of up to eight days, during which the aircraft is refurbished prior to painting. The operator performs a customer inspection after both the restoration and painting. As the fourth month begins, the aircraft is reactivated and retested over a roughly 12-day period during which any out-of-sequence or traveled work also could be completed.
Finally, when all rework and traveled flow is complete, the aircraft enters the traditional period of production flight-test and predelivery checks. Sometimes taking up to six weeks, depending on any glitches discovered during the test period, the phase includes a customer acceptance flight prior to signoff for delivery.
Comments
Think it shows that Boeing is finally coming to grips with the real issues of making a technically demanding product assembled from a global supply chain. I think the lessons learned here will be invaluable when Boeing does its next aircraft.