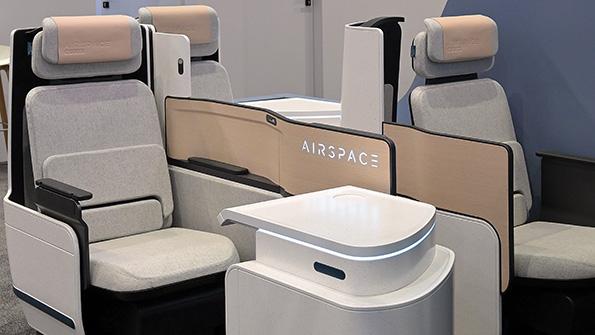
Airbus’ C Suite business-class concept addresses the need to reduce CO2 emission density by optimizing the use of space and applying new technologies for the A320 and A350.
Original equipment manufacturers (OEMs) are increasingly looking at every stage of the product life cycle through a lens of sustainability—from onboard catering and waste reduction to using cabin products that can be repaired, reused and recycled to minimize their environmental impact.
At the Aircraft Interiors Expo (AIX) Passenger Experience Conference in Hamburg in June, Airbus described a number of sustainability initiatives in its Cabin Vision 2035+ program. The manufacturer says around 10%-20% of an aircraft’s lifecycle eco-impact comes from the cabin, and around 10%-15% of this is weight driven.
“Sustainability in the cabin is really about a paradigm shift in cabin design philosophy and how we calculate and optimize our products in the cabin,” Airbus VP-cabin marketing Ingo Wuggetzer said.
This includes looking at cabin design from three points of view: transparency, decarbonization and circularity. “All of these require collaboration,” he said, adding the company has worked with 10 airlines and eight cross-industry partners from high-tech companies, as well as other startups toward a more sustainable cabin.
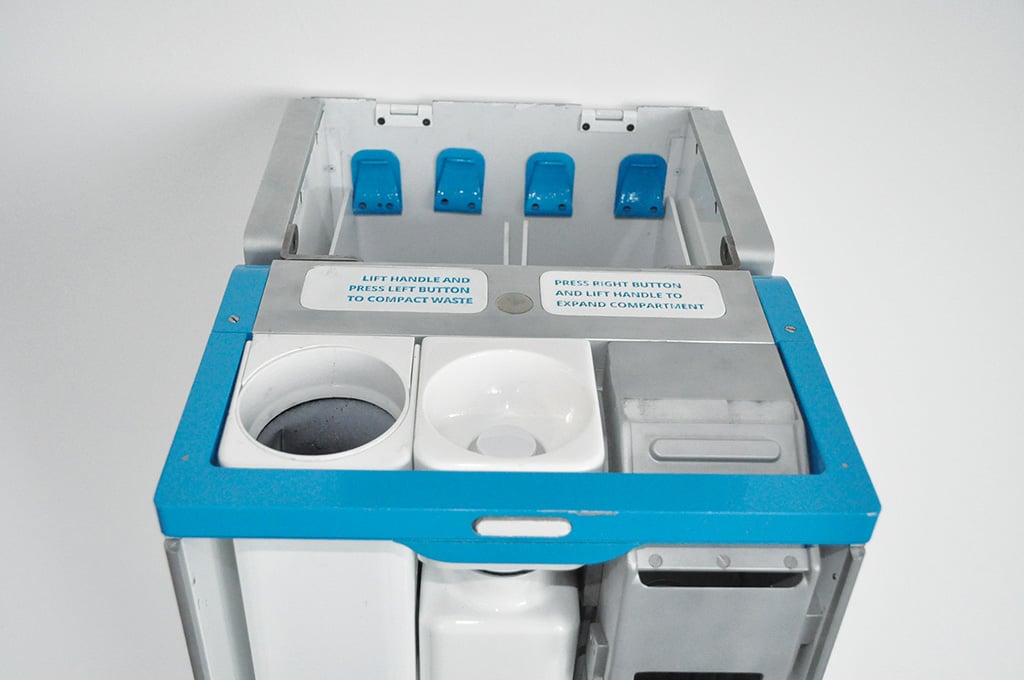
Transparency
In the short-term, through 2025, the focus is on full transparency on the environmental impact of cabin parts and operations, Airbus SVP-cabin & cargo engineering Marc Fischer said, “and the need to quantify the improvements the different design and engineering solutions bring to the cabin.”
It is also about making sustainability initiatives visible to passengers, which he said “starts at home with a mobile travel companion app” that provides a transparent end-to-end travel experience where passengers can choose options, products, meals, seating and carbon offsets that reflect their individual environmental footprint.
“Because in the cabin our value and supply chains are very complex and fragmented, it’s not all that straightforward to actually measure and capture all the relevant information,” Fischer said, adding that Airbus is developing the Airspace Eco Calculator tool, which gives a lifecycle assessment of the environmental impact along all product life phases. “This tool helps us with design choices and the optimization behind it, of all the different cabin solutions, which in turn helps airlines make the right choices when it comes to customizing their cabins,” he said.
Decarbonization
Approaching 2030, Airbus plans to introduce new cabin interior solutions and materials with a low CO2 impact and optimal lightweight design for reduced fuel consumption, to significantly reduce waste from cabin products during production and in the landfill, as well as establish new end-of-life management approaches.
One example of this is the bionic partition, which is the result of a collaboration with Autodesk and APWorks. The bionic partition, which is inspired by biomimicry—the design and production of materials modeled on biological entities and processes—is estimated to give a weight savings of up to 40% in the cabin.
“Its milled aluminum alloy is based on bionic principles and has the potential to also be used for other cabinet monuments and components,” Fischer explained. He said that this year static tests—a 16G test—will be performed and there will be a first flight with the A320. “Further examples of this technology include galleys and lavatories,” he said.
Also, the Airbus food scanner, which is an artificial intelligence-enabled device that tracks and controls inflight catering, enables a more personalized service, offers more efficiency, and reduces weight and waste reduction by up to 15%.
“That’s in combination with digitally enabled preflight ordering,” Fischer said, “which gives us much more flexibility in terms of choice and drives ancillary revenue.”
A second trolley, called the Retrolley, for recycling and segregating onboard waste, has been developed in collaboration with Iacobucci HF Aerospace, and can lead to a 20%-40% waste volume reduction. Fischer said certification is underway with a launch customer.
Circularity
Circularity requires rethinking, repairing, recycling and reusing products and materials.
“When it comes to material, engineering and design choices, we need to make the right choices that already consider what happens after cabin products come out of use and how they can have a second life,” Fischer said.
“We want to be the first major OEM to offer a fully circular cabin, maximize recyclability, and reuse of cabin components and materials,” Fischer said, pointing to the C Suite business class concept, which was on display at AIX, showing the different facets of sustainability, from cabin layout efficiency and weight reduction to new materials and processes, as well as a circular design approach.
The C Suite concept, which is the result of a collaboration with Stelia Aerospace, addresses the need to reduce CO2 emission density by optimizing the use of space and applying new technologies for the A320 and A350. The result is a 10% seat gain compared to benchmarked seat layouts, an overall weight savings of 30%, and 100% circular seats, Fischer said, adding that the concept showcases an “improved environmental footprint without any compromise to comfort. And that’s crucial.”
Another circularity example is the BioMat sidewall panel, which is a collaboration between Airbus and Mitsubishi Chemical Group, and uses a new bio-based resin, which is made from sugarcane waste that replaces the petroleum-based resin that is being used today.
It comes in two versions, Fischer explained, either combined with reinforced glass fiber or in combination with reused carbon fibers, which are typically taken out of carbon fiber production waste that can be reused instead of thrown away. This gives a weight reduction of up to 18 kg, for example, for the A350 per aircraft; up to 99% reused carbon fibers have been taken from production elsewhere; and 80% of the resin is from renewable sources. He said this project will soon be flying onboard the A350 Airspace Explorer flight test platform.
Another concept is a thermoplastic sidewall panel, which is planned to achieve a 100% recyclability of thermoplastic materials. Fischer said this is an opportunity to reduce the number of materials onboard the aircraft to just one—thermoplastics.
Carpets are also being studied for circularity, with a collaboration between Airbus, Anker and Lantal, which includes three different ways to install and remove carpets: the Hook & Loop, which uses 4X lighter fixation and 3X less tape; Lantal Deep Dyed, which reduces water use by 60%, with a 40% CO2 reduction, producing 80% less waste; and the Anker Monoone, which uses only one material—polyester. These offer much cleaner, leaner solutions that allow easier installation and removal of carpeting that doesn’t involve a glue that must be ripped off and cannot be recycled.
“Across the board, people love to fly,” Wuggetzer said, “but it is also about understanding that we can do it smarter in the future, as well as maintain superior comfort in the cabin. Definitely, all of this is driving the future passenger experience.”