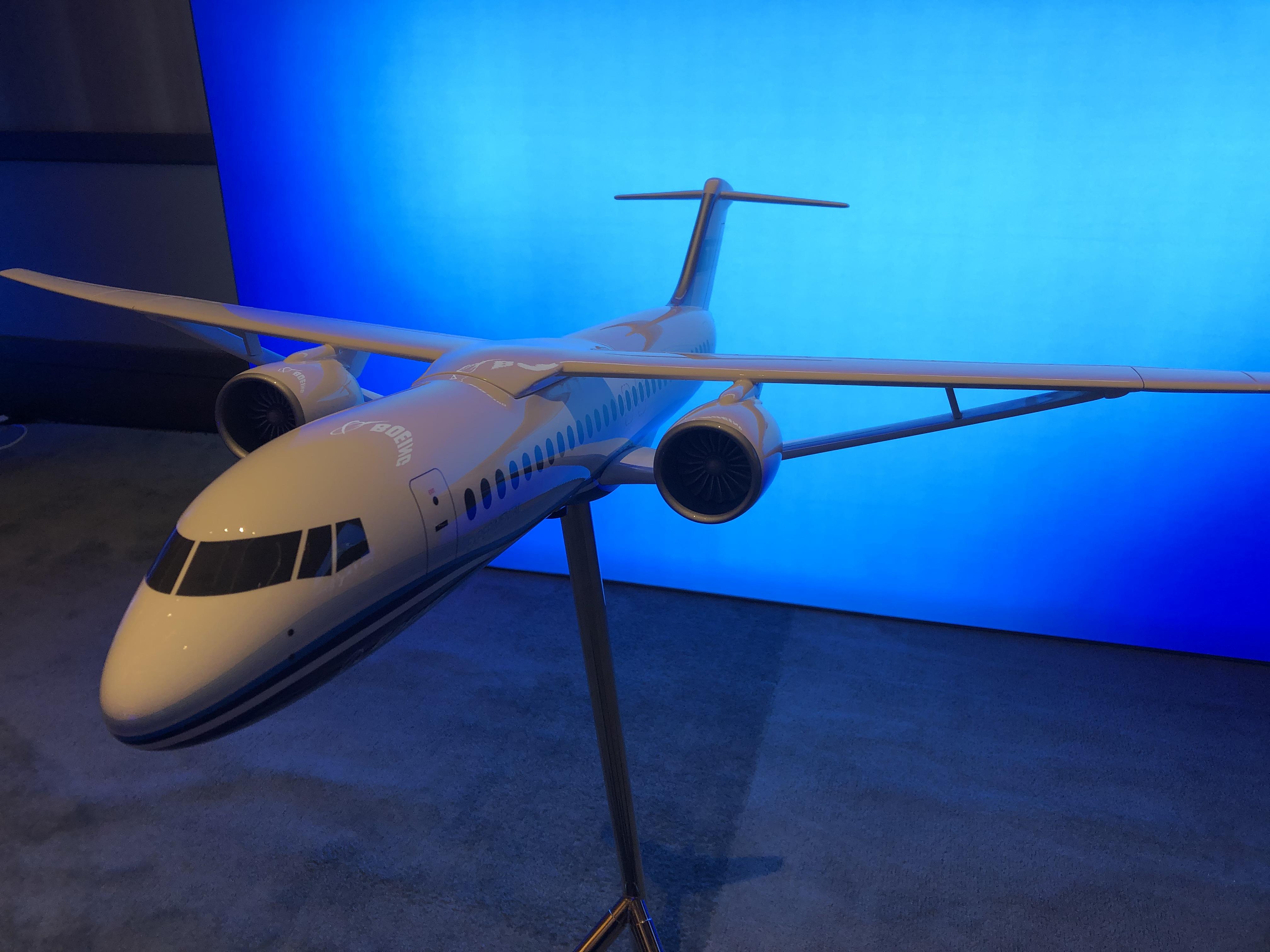
Boeing will study the certification challenges of its Transonic Truss-Braced Wing (TTBW) ultra-efficient airliner concept as part of a new phase of work following wind tunnel tests that prove the basic viability of the 737-class aircraft design for typical airliner cruise speeds of Mach 0.8.
Evaluation of the slender, low-drag wing concept continues as Boeing considers technologies for a potential next-generation single aisle design to succeed the 737 MAX towards the end of the decade. With a 170-ft.-span wing, the TTBW was originally developed in 2010 under the Boeing and NASA Subsonic Ultra Green Aircraft Research (SUGAR) program to study new configurations for ultra-efficient airliners that could enter service in the 2030-2035 timeframe.
Under the fourth and most recent phase of the program Boeing developed and tested a high-lift system for the vehicle’s long, thin wing which is braced by trusses to minimize the weight penalty of the 170-ft. span. The company estimates that, thanks to the reduced induced cruise drag of the high-aspect-ratio wing, the TTBW will have a 9% fuel-burn advantage over a conventional tube-and-wing airliner on ranges up to 3,500 nm.
The latest phase, which is due to wrap up in March, also included analysis of the aeroelastic behavior of the configuration—which incorporated changes to the wing sweep angle as well as the position, shape and make-up of the main and jury struts. Wing sweep was increased to enable cruise speed to rise from Mach 0.745 to Mach 0.8. To rebalance the resulting change in the aircraft’s center of gravity, the wing root was moved forward and the inboard strut was moved aft and no longer positioned directly beneath the wing.
The new strut has increased chord at the fuselage, forward sweep and tapers toward the junction with the wing. Together with the “unstacking” of the wing and strut, the changes reduced aerodynamic interference and, during wind tunnel tests, were found to have several other benefits. These include reduced compressibility drag from an improved cross-sectional area distribution, protection of the flow around the inboard strut during high-lift operations and a higher strength wing-strut structural arrangement.
“The big carrot here is a dramatic increase in vehicle wing aspect ratio which gives us a significant decrease in induced drag,” Boeing TTBW program manager Neal Harrison said. “We get efficiency from the strut-braced configuration itself, including a significant decrease in wing bending moment which in turns leads to the potential for simplified structural attachments such as hinge joints for wing attachments.”
Updating progress on the TTBW at the American Institute of Aeronautics and Astronautics SciTech conference in Orlando, Harrison said that while the concept shows “potential for significant performance improvements, there is no free lunch. A lot of technology has to be demonstrated and matured, including the wing-strut join. This is dimensionally a small wing box and when you add the aerodynamics and structure together you get these non-linear aeroelastic characteristics. There are also other challenges such as certification for icing, ditching and crash-worthiness and so on.”
The tests also showed that the design revisions improved high speed efficiency. “By unstacking we wanted to know if we could make the strut a positive contributor to lift rather than being a parasitic structural element that just creates drag—what could you get out of it? In the end we got significantly more lift off the strut,” Harrison said.
“Total vehicle performance was improved by moving the jury strut outboard,” he adds. “That portion was thinned down where it meets the wing, so you get improved transonic performance in that region. However, the structural requirements went up inboard and we increased the planform of the structure to take the increased load. Fortunately, that also ended up being beneficial aerodynamically.”
High speed testing and validation took place in NASA Ames’ 11-ft. Unitary Plan Wind Tunnel starting in July 2019, while the low-speed design was tested in the NASA Langley 14-by 22-ft. subsonic tunnel beginning in September 2019. The transonic tests, which used a 4.5% scale model, assessed vehicle lift-drag performance, longitudinal and lateral stability characteristics and included a preliminary assessment of flight controls effectiveness. “The measurements were within a couple of drag counts, so we are pretty pleased with that,” Harrison said. “It gives us confidence the vehicle is performing as we expected to transonically.”
The low speed tests, which ran through November 2019, used a 14-ft. span 8% scale model and evaluated several high-lift designs. “We looked at various fixed and variable camber Krueger leading edges as well as a conventional slat, drooped leading edges and morphing leading edges,” Harrison said. Ultimately a trailing edge single segment flap and variable camber Krueger arrangement was chosen.
“On the inboard wing we did a pretty good job, but on the outboard wing we ended up with differential rigging on the Krueger which deflects as you go further outboard to keep that surface [flow] attached,” he added. “That was a major finding.” Boeing said that “there remains significant potential for high-lift system performance improvement with additional study.”
Overall results show “we have beneficial changes from going to a higher sweep angle and we showed that the design is well suited to efficient operations, Harrison said. “The low speed performance is in line with expectations and on the structures side the results of our aeroelastic analysis indicate we need to go to a higher fidelity tool. But overall the results suggest it is feasible.”
Future work, which will be covered under a fifth phase expected to be agreed with NASA in the 2020 second quarter, will focus on further maturing the concept and reducing risk. Key study areas will include investigations of high-speed buffet; alternate high-lift systems development; transonic wind tunnel tests at higher Reynolds numbers; detailed aeroelastic analysis and development of roadmaps for demonstrating structural concepts and key acoustic technologies.
Certification challenges to be investigated include damage tolerance to bird-strike and crashworthiness, ditching characteristics and icing effects such as accretion, aerodynamic effects and protection.
Comments
As with the introduction of the A380, airfields and terminals will need to adapt. But (assuming this becomes the future narrowbody workhorse configuration regardless of manufacturer) the change will involve far more aircraft delivered and transiting far more airfields.
Whether the lifetime fuel burn improvement would cover the cost of the needed ground-side changes is an interesting question. But given that different entities will save or pay that money, I predict an epic battle.
Thu, 01/16/2020 - 12:17
Efficiency is a total package of airframe, propulsion and crew. This design has been around for a while and reflects none of the new possible hybrid power systems. If Boeing is not also designing its NNB to be "co-pilot optional", they are missing the boat - again.”
While I agree with utilizing possible hybrid power systems, I don’t agree with the “co-pilot optional” system. Many recent accidents in single pilot jets show that workload and decision making were the contributing factors. A rapid or explosive decompression at high altitudes where most airliners or business jets operate require mere seconds of reaction time. The odds of surviving dramatically increase when you have 2 crew members in the cockpit. And in today litigious society, single pilot operations in the airline industry will simply not work........
“ GWROBLE
Thu, 01/16/2020 - 12:17
Efficiency is a total package of airframe, propulsion and crew. This design has been around for a while and reflects none of the new possible hybrid power systems. If Boeing is not also designing its NNB to be "co-pilot optional", they are missing the boat - again.”
While I agree with utilizing possible hybrid power systems, I don’t agree with the “co-pilot optional” system. Many recent accidents in single pilot jets show that workload and decision making were the contributing factors. A rapid or explosive decompression at high altitudes where most airliners or business jets operate require mere seconds of reaction time. The odds of surviving dramatically increase when you have 2 crew members in the cockpit. And in today litigious society, single pilot operations in the airline industry will simply not work........
The New 717 to face off with the Bombardier designed and made A220.
Plus
1. New engine
2. Folding wings
3. Laminar air flow on more areas
4. Binary Human and Electronic pilots
5. More robotic production system
6. AI powered MRO support
7. Wider seats single aisle
Rene G. Abad
AirPino PH
Lupas