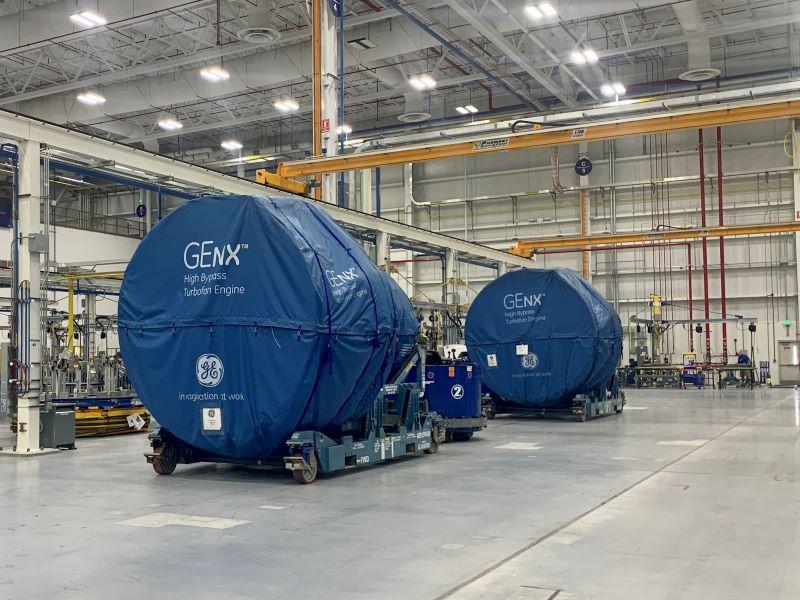
Credit: Sean Broderick / AWST
NORTH CHARLESTON, South Carolina—Boeing’s Charleston-area propulsion center, already growing as an aftermarket provider, is preparing to take on a larger role on 787 production by delivering ready-to-install engine “kits” to the final assembly line (FAL). Propulsion South Carolina (PSC) engineers...
Subscription Required
This content requires a subscription to one of the Aviation Week Intelligence Network (AWIN) bundles.
Schedule a demo today to find out how you can access this content and similar content related to your area of the global aviation industry.
Already an AWIN subscriber? Login
Did you know? Aviation Week has won top honors multiple times in the Jesse H. Neal National Business Journalism Awards, the business-to-business media equivalent of the Pulitzer Prizes.