Aviation Platforms Benefit from More Electric Architectures

A Collins Aerospace engineer from Solihull, England inspects an electrical distribution panel used to increase DC voltages on aircraft.
"I don't believe it's a question of if, but where on the aircraft and to what extent," notes Todd Spierling, Principal Technical Fellow of Electrification at Collins Aerospace, an RTX Business, in discussions on the future of More Electric Aircraft architectures.
More Electric Aircraft encompasses the underlying systems that pressurize the aircraft, heat and cool the aircraft, or move control surfaces, which are powered with electricity instead of traditional hydraulic and pneumatic options.
Current aircraft architectures still rely heavily on pneumatic and hydraulic sources for many of the secondary systems. These systems function efficiently across a narrower range of operating conditions, such as temperatures and pressures, than their electric counterparts. Additionally, a focus on eliminating centralized hydraulic systems results in easier aircraft build and reduced maintenance costs, as well as the removal of environmentally unfriendly hydraulic fluids.
"Today's aircraft are already flying electrified systems such as environmental control, wing ice protection systems, fuel tank inerting, thrust reversers, brakes and flight control actuation. These systems are applied to a limited extent. We anticipate that future aircraft will increase this degree of electrification, perhaps completely eliminating the centralized hydraulic and pneumatic systems from the aircraft," Spierling continues.
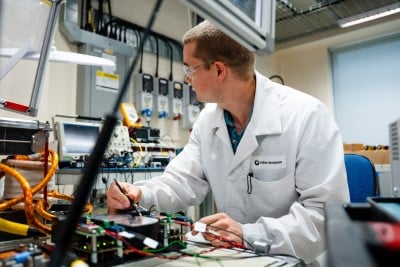
Electrification technologies allow for greater aircraft reliability, improved maintainability, and reduced fuel burn. And while electric and hybrid-electric propulsion show great promise in sustainable aviation, more electric systems have already proven themselves effective solutions on aircraft such as the Airbus A350 and Boeing 787. With more than 70 years working on electrical architectures, Collins Aerospace has unique experience in executing across not just components but complete electrical systems on many platforms.
The 787 utilizes more electric systems to a greater extent than any other aircraft flying today. The development and implementation of these systems led to a deeper understanding and expertise for both high-voltage safety and in-service reliability for these systems that remains unique to Collins.
Continued application of electrified technologies at scale will allow for greater platform efficiency. When considering an aircraft-wide approach to more electric systems, air framers gain efficient, data-rich systems that can also help reduce weight across the aircraft.
We know that weight reduction directly relates to less fuel burn and reduced carbon emissions. Considering a systems level approach and moving to voltage levels approaching the kilovolt level significantly reduces the weight of both the components themselves as well as the power distribution system that connects them together. This engineering has the ability to enable thin-wing designs and other space saving solutions to create lighter, more aerodynamic aircraft configurations.
More Electric Systems also support the evolution of less-bleed and bleed-less architectures throughout the aircraft. This takes power more efficiently from the engines, and in turn, reduces fuel burn. This has been proven in Collins' 787 environmental control systems and remains the only environmental system of its kind certified for flight.
All these benefits in both sustainability and platform functionality make More Electric Aircraft a needed inclusion on every platform, from regional and business jet to large commercial in the next generation of aircraft.