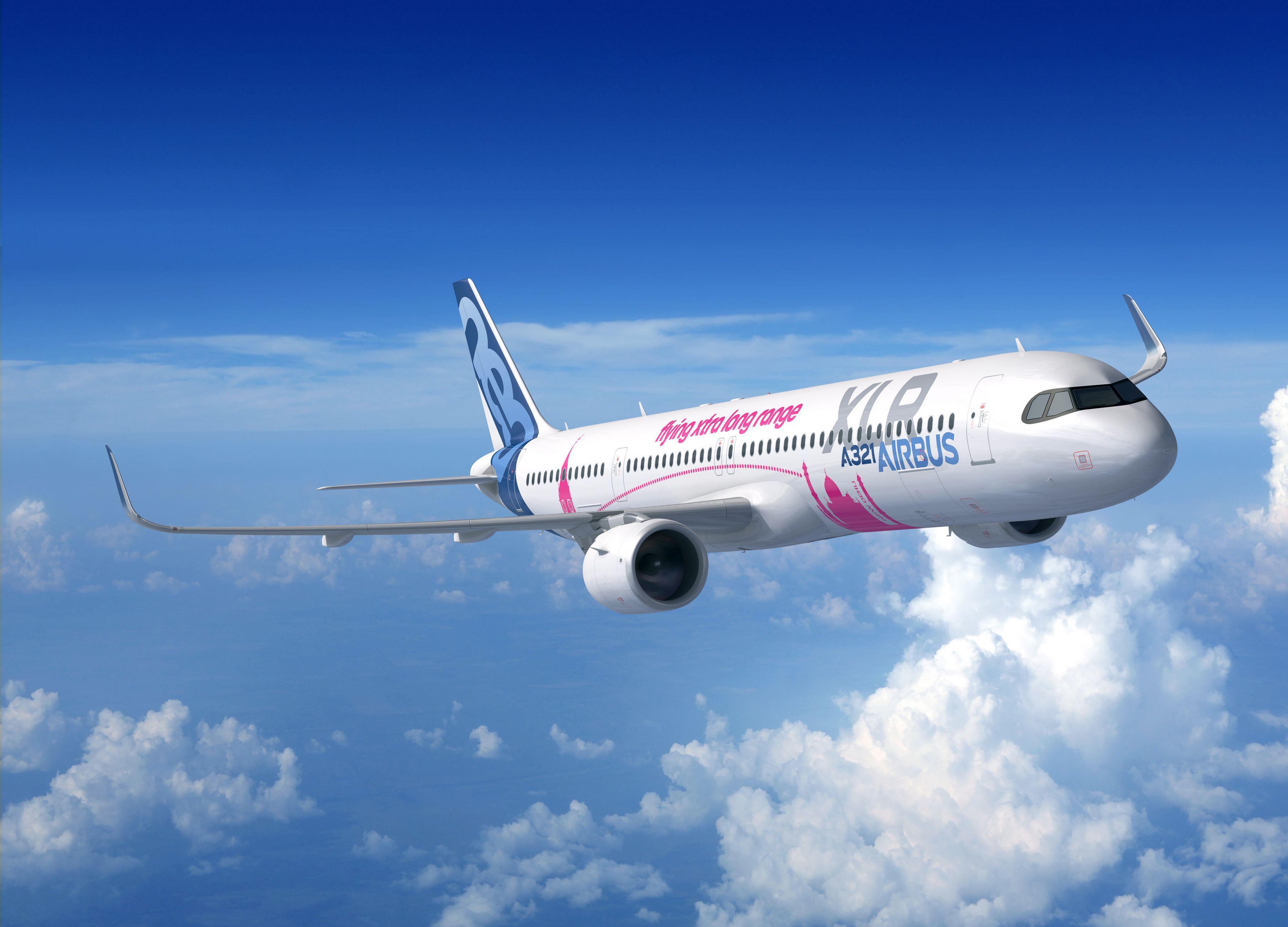
FRANKFURT—Airbus says it is working on solutions addressing concerns raised by EASA and Boeing about the fire safety of the Airbus A321XLR rear center tank (RCT), adding that the variant’s development and certification schedule remain on track.
As part of A321XLR certification process, Airbus applied for a major design change—the addition of an integral, thus structural, rear center tank behind the wheel bay and in space that would normally be part of the aft cargo compartment. The tank is key for increasing the XLR’s maximum range to around 4,700 nm from the around 4,000 nm reached by the current long-range version of the A321neo, the A321LR.
Airbus has secured more than 450 orders for the XLR, which it pitched for thin long-haul routes. The variant is winning a commanding market share in competition with Boeing’s 737-9 and -10.
There are several lingering design issues that have not yet been fully addressed. According to EASA, the RCT will create a “cold feet” effect for passengers seated above it. Therefore, the regulator proposed installing an insulation panel between the tank and the cabin floor, for comfort reasons. The panels would have to be compliant with burnthrough specifications.
However, Airbus studied and rejected EASA’s suggestion because there is not enough space for the panels between the tank and the floor. Also, burnthrough protection of the cabin floor would leave decompression panels on each side of the fuselage unprotected, Airbus argued. The fire, explosion and smoke risk assessment of the RCT concluded that a level of ventilation must always be ensured, but the ventilation would be impossible if burnthrough-compliant material was added in that area.
EASA, in a special-conditions document on the issue, also stated that an integral fuel tank behind the wheel bay “brings additional risks (explosion, penetration by fire, vapor migration etc.) if it is exposed to an external fire.” Enough time must be ensured “for the occupants to evacuate the aircraft in case of an external pool fire,” EASA wrote. With no adequate protection in place there may not be enough time for safe evacuation, the agency said.
EASA proposed a special condition for the lower half of the fuselage and in the area of the RCT to be “resistant to fire penetration.” According to the special condition, Airbus must demonstrate that its design is at least as safe as that of the basic aircraft either through the RCT design itself or additional features. Compliance has to be demonstrated in “tests, analysis supported by test evidence, or design similarity.”
Boeing weighed in during the public-comment process with several concerns.
“Fuel tanks integral to the airframe structure inherently provide less redundancy than structurally separate fuel tanks,” wrote Boeing Global Regulatory Strategy director Mildred Troegeler. “Such integral fuel tanks ... can foreseeably result in more hazardous outcomes when exposed to threats such as an external pool-led fire.”
The special condition should take into account internal volume heating leading to a threat of explosion or ignition of flammable vapors, Troegeler added.
“Heat transfer characteristics will be affected by the absence of a conventional configuration featuring insulation against the fuselage external skin and the potential presence of fuel in direct contact with the fuselage external skin,” she continued.
Troegeler also wrote that there are “additional concerns” beyond protection against external fuel fires, particularly “structural disruption due to an otherwise survivable off-runway or landing gear failure event.”
EASA said it agreed with the comments, adding they will be addressed in separate special conditions.
“Public consultation is part and parcel of an aircraft development,” Airbus said. “All subjects raised along the way will be dealt with hand in hand with the airworthiness authorities to fulfill all requirements for the type certification.”
Airbus began parts production for the first A321XLR earlier this year. Entry into service is planned for late 2023.