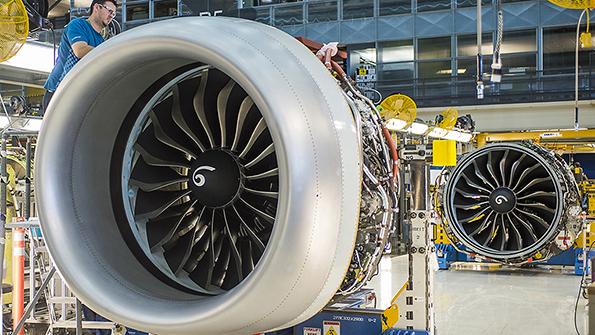
A year ago, despite signs of a sluggish widebody market, it was largely business as usual among the world’s commercial engine makers. They were preoccupied with the challenges of expanding capacity to handle swollen order backlogs and a bulging aftermarket business. But now, because of COVID-19 and the 2020 collapse of air travel, engine makers have thrown all these preparations into reverse thrust to match the grim new market realities.
In many ways, the engine industry has also taken a heavier pounding from the pandemic than other sectors. Hit by massive airliner production and delivery cutbacks, the demand for new engine production has slowed to levels not seen for 20 years. Simultaneously, large chunks of the priceless aftermarket on which it has become so dependent have evaporated as entire fleets of older aircraft have been grounded, most never to fly again.
Aside from pushing engine makers into survival mode, the pandemic has also prompted a series of profound institutional changes that will likely reshape the industry in the decades to come. These include the kick-starting or acceleration of studies of new engine concepts and more electric technology, as well as more urgent research into alternative fuels, including hydrogen.
All are focused on sustainable aviation goals that, in most cases, are underwritten by government support packages. Other longer-term changes include plans to reduce dependence on aftermarket revenue models and follow the airframe makers in a renewed focus on cash generation from initial equipment sales.
Riding high just before the crisis with 2,127 engine shipments in 2019, General Electric-Safran joint venture CFM International has faced one of the most challenging drawdowns. Although buffered to some extent by the production flexibility of its parent companies, CFM has had to carefully match the uncertain production outlook at Airbus and even more so at Boeing with the 737 MAX, for which it is the exclusive engine supplier, while protecting its LEAP-1 supply base.
“We have plans in place with both airframers that enable us to continue producing LEAP engines at a reduced rate while protecting our ability to accelerate production as needed in the future,” CFM president and CEO Gael Méheust says.
While Airbus plans to step up production next year from 40 A320-family aircraft per month to 47 in response to an expected market bounce back, Boeing isn’t expected to increase production of LEAP-1-powered 737 to 31 per month until the start of 2022.
GE Aviation, meanwhile, is cutting its workforce by 25% in response to the pandemic, having previously announced a temporary 10% reduction in March. The company, which is trying to save $1 billion in costs, has also warned that additional cuts may be needed. Although military engine production remains largely unaffected, the impact of COVID-19 has had repercussions on GE’s commercial engine business beyond reduced deliveries of CFM engines for single-aisles, to include fewer GE90 and GEnx-1s for twin-aisles.
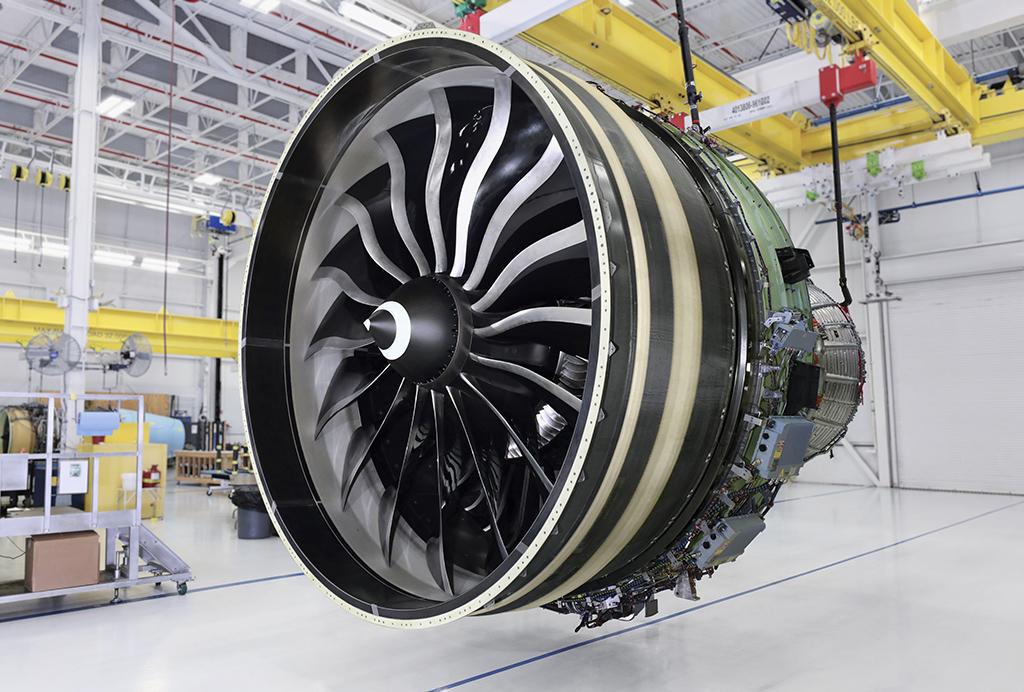
Amid the gloom a recent bright spot for GE was FAA certification of the GE9X turbofan for Boeing’s 777X in October. GE Aviation aims to complete testing for Extended Operations approval by year end and is preparing another engine for validation tests of an innovative flow inducer device designed to reduce the impact of dust and debris on durability. The GE9X, which is the largest turbofan ever developed, is scheduled to enter service on the 777-9 in 2022.
Despite the resilience of its strong military engine manufacturing side, Pratt & Whitney has also been forced to make significant cutbacks in production of the PW1000G geared turbofan family to maintain parity with slower demand from Airbus for the PW1500G-powered A220 and PW1100G-powered A320neo. In October the engine maker revealed it was also axing up to 450 jobs in the Connecticut area as part of a broader workforce reduction of 15,000 announced the previous month by parent company Raytheon.
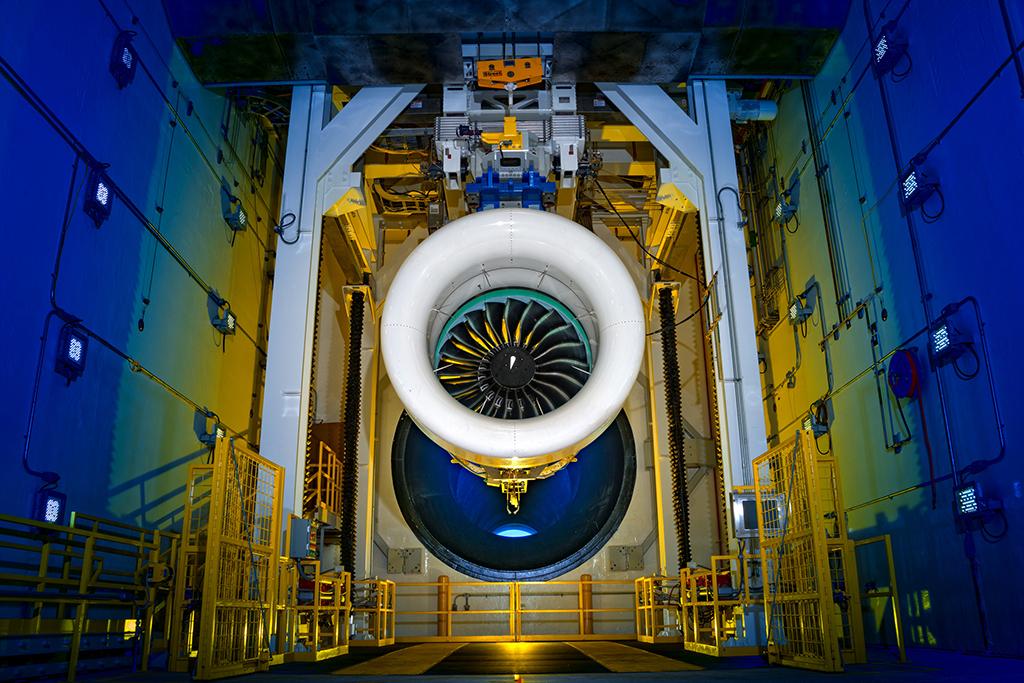
In the longer term, however, Pratt continues to plan for a significant market recovery, part of which will be catered for under newly revealed plans to invest at least $650 million through 2027 in a new turbine airfoil production facility in Asheville, North Carolina. The 1,000,000-square-foot facility will eventually support the addition of up to 800 jobs over the next seven years.
With its high dependence on the badly hit widebody market, Rolls-Royce has suffered the most of the “big three” engine makers from the pandemic. Already embattled at the start of 2020 by costly fixes to long-running issues on the Trent 1000 for the Boeing 787, the UK engine maker is making urgent cost cuts to see out the storm. This includes reducing its workforce by 9,000, of which 5,000 jobs are planned to go by year-end.
Rolls announced a £2 billion ($2.6 billion) rights issue Oct. 1 to shore up its balance sheet. The move formed part of a larger initiative to raise a total of £5 billion and provide increased financial resilience until the expected return of significant cash generation in 2022. Part of the investment will support continued development of the UltraFan, a geared engine design on which Rolls is pinning its longer-term hopes to provide the basis for a new generation of fuel-efficient engines for both future single- and twin-aisle designs.